The air compressor is important and indispensable equipment in modern industry. However, cracks in operation are often a headache, affecting production efficiency at the least and bringing safety risks at the worst. Understanding the causes of cracks in air compressors and the corresponding solutions can not only effectively prevent equipment failures, but also help companies save maintenance costs and increase the service life of equipment. This article will deeply analyze the common causes of cracks in air compressors and effective prevention and detection measures to provide you with practical reference.
Cracks in air compressors during operation can arise from various factors, including material defects, excessive operating pressure, temperature stress, frequent starting and stopping, inadequate maintenance, and external environmental influences. These factors will cause uneven force on equipment components or accelerate material aging, and eventually cracks. In order to effectively prevent crack formation, users should regularly maintain the lubrication system on the basis of reasonable control of working pressure and temperature, and keep the equipment ventilated and clean. At the same time, non-destructive testing methods such as ultrasonic, magnetic particle testing, and X-rays can be used to detect cracks in the equipment to detect potential problems in advance. Standardized operation, regular testing and proper maintenance are the key to ensuring the long-term and efficient operation of air compressors.
6 major reasons for cracks in air compressor operation
Material defects: potential hidden dangers of cracks
The main components of air compressors, such as cylinders, pistons, crankshafts, etc., are usually made of metal materials, but tiny internal cracks may occur during the manufacturing process due to material defects, smelting problems or improper processing. These seemingly harmless “hidden injuries” will gradually expand into obvious cracks as the operating time increases.
- Solution: In addition to choosing a reliable air compressor manufacturer, ensure that the raw materials of the equipment meet the standards. Non-destructive testing technologies such as X-rays or ultrasound can also be used to test key components to eliminate potential material defects in advance. Of course, the air compressors produced by our MINNUO have always been at the forefront of the industry. Customers deeply trust MINNUO for its excellent product quality and exceptional service attitude, and our products consistently stand up to rigorous testing. If you’re still uncertain about choosing a reliable air compressor manufacturer, consider giving MINNUO’s products a try.
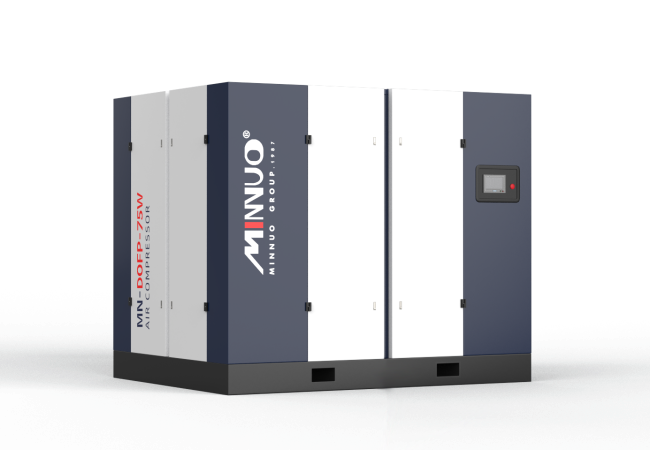
Excessive operating pressure: the “catalyst” of cracks
When the air compressor operates beyond the design pressure, it will cause excessive fatigue of the components and increase the risk of cracks. Long-term overpressure operation will not only impose excessive stress on the internal components of the equipment, but also accelerate the fatigue loss of metal materials, making them more prone to cracks.
- Solution: Operate within the design pressure range of the equipment to avoid overload operation. Install pressure monitoring equipment to monitor the equipment pressure in real time to prevent equipment damage caused by excessive operating pressure.
Temperature stress: the “invisible pusher” of crack formation
When the air compressor works in a high temperature environment or high-frequency operation state, the metal parts inside the equipment will expand and contract due to temperature differences. The constant change in temperature causes stress inside the metal material, which in turn forms cracks. Especially when the air compressor has poor heat dissipation effect, this temperature difference stress has a particularly significant impact on the components.
- Solution: Ensure air circulation around the equipment, and install cooling devices such as water cooling or air cooling systems when necessary to reduce temperature stress. Clean the heat dissipation device regularly to maintain its good heat dissipation function and avoid cracks caused by temperature problems.
Frequent start and stop: repeated “pressure fatigue”
When the air compressor starts and stops, its internal pressure and temperature will change instantaneously, and the mechanical stress will change with the pressure fluctuation. Frequent start-stop processes will cause repeated impacts on the metal structure inside the equipment, causing fatigue cracks, which will in turn affect the overall stability of the air compressor.
- Solution: Try to avoid frequent start-stop of the air compressor, arrange the work flow reasonably, and reduce the start-stop frequency. Use delayed start and automatic control functions to avoid cracks in the equipment due to frequent start-up and extend the service life of the equipment.
Improper maintenance or lack of maintenance: the “black hand” behind the generation of cracks
Lack of maintenance or improper maintenance is one of the important reasons for the frequent occurrence of crack problems. For example, failing to replace the lubricating oil on time increases friction between parts, and neglecting to repair worn seals leads to a higher internal pressure load. Lack of proper lubrication and cleaning will accelerate the wear of the equipment, thereby providing a breeding ground for the formation of cracks.
- Solution: Regularly maintain the air compressor, keep the lubrication system clean, and regularly add or replace the lubricating oil. Check and replace worn seals in time to ensure normal friction between equipment parts and reduce crack problems caused by improper maintenance.
External environmental influence: “Invisible corroder” of cracks
The working environment of the air compressor directly affects the durability of the equipment, especially in a humid or corrosive gas environment, metal parts are more susceptible to corrosion or oxidation. This external factor will accelerate material aging and make the air compressor more prone to cracks.
- Solution: Choose an environment with dry air and no corrosive gas to use the air compressor to avoid high humidity or corrosive gas erosion of the equipment. Install anti-corrosion coating or moisture-proof equipment when necessary to reduce the impact of the external environment on the air compressor and extend the life of the equipment.
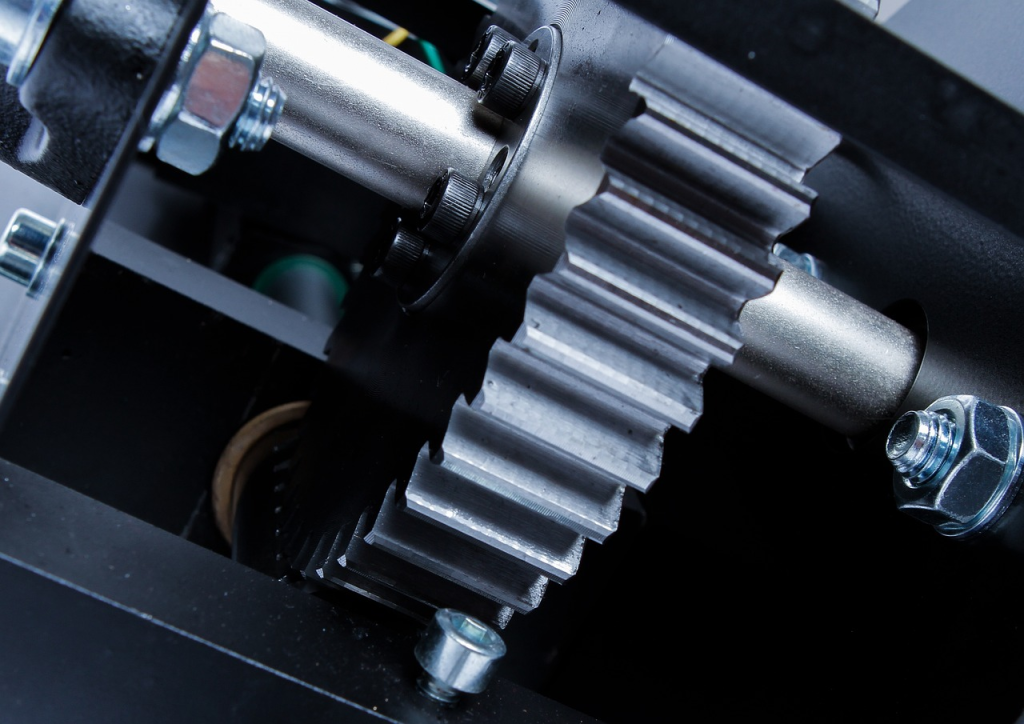
How to detect cracks in air compressors: accurately identify hidden dangers
Regularly checking the cracks of air compressors can timely detect potential risks and avoid sudden equipment damage. The following are several commonly used crack detection methods:
Ultrasonic detection
By emitting high-frequency sound waves to metal parts and detecting the reflected signal of the cracks to determine whether there are defects inside. This method can quickly and accurately detect cracks inside the material, especially for thicker metal parts.
Magnetic particle detection
The location of the crack is determined by applying a magnetic field to the surface of the air compressor parts and observing the aggregation of magnetic particles at the crack. This method is suitable for surface crack detection, but the effect on deep cracks is poor.
X-ray detection
Suitable for detecting thicker metal materials. X-rays can image the crack position after penetrating the material. Although the cost is high, the detection accuracy is high, which is suitable for crack detection of complex structures and heavy parts.
Dye penetration detection
Apply dye on the metal surface and judge the crack position by observing the penetration of the dye. This method is suitable for detecting surface cracks, easy to operate and low in cost. It is a commonly used crack detection method.
Crack prevention and daily maintenance suggestions
To ensure the normal operation of the air compressor, it is very important to prevent cracks. The following are several effective measures for preventing cracks in air compressors:
Reasonable operation to avoid overpressure
When operating the air compressor, keep the working pressure within the design range to avoid crack problems caused by overpressure. Install a pressure monitoring system to promptly warn of abnormal pressure and ensure that the air compressor always operates within a reasonable pressure range.
Control temperature and reduce temperature difference stress
The heat dissipation system of the air compressor should be kept unobstructed, and dust and oil stains on the heat sink should be cleaned in time. Install cooling devices when necessary to ensure that the equipment is at a suitable temperature to avoid cracks caused by temperature differences.
Regular maintenance and lubrication
It is very important to maintain the lubrication system of the air compressor to avoid excessive wear caused by insufficient lubrication. Establish a detailed maintenance plan, replace lubricants and seals on time, and avoid cracks caused by increased friction.
Optimize the installation environment and reduce the impact of corrosion
Choose an environment with non-corrosive gases and suitable humidity to avoid cracks in the equipment due to oxidation or corrosion. In a humid or highly corrosive environment, take anti-corrosion measures, such as coating anti-corrosion materials or installing dehumidification equipment to extend the service life of the equipment.
Conclusion
The problem of cracks in air compressors cannot be ignored. The causes of their occurrence are complex, involving multiple factors such as materials, temperature, pressure, operation, and maintenance. By ensuring proper operation, conducting regular inspections, and performing effective maintenance, you can significantly reduce the risk of cracks and ensure the air compressor operates efficiently. At the same time, regular crack detection of the equipment can timely discover potential hidden dangers and avoid sudden failures caused by crack expansion. Paying attention to the daily use and maintenance of the air compressor can better ensure the stable operation of the equipment and extend its service life.
Please remember, when you buy an air compressor, go to MINNUO; when you encounter a problem, go to MINNUO; when you need help, go to MINNUO. MINNUO is always with you, and we can provide you with personalized customization services and a comprehensive after-sales system at any time.