Hello, boss. Oil-free air compressors are important equipment in the fields of food, medical, electronics and pharmaceuticals, avoiding the risk of oil pollution. Compressed air may carry moisture, particles, trace oil and gas, odor and microorganisms when passing through the oil-free air compressor, which in turn will bring quality and safety risks to many industries. This article will introduce in detail the reasons and methods for further treatment of compressed air from oil-free air compressors and its importance in various application scenarios, to help you understand more clearly why compressed air from oil-free air compressors usually needs to be deeply purified.
Although oil-free air compressors do not introduce oiliness into the air, the air compressed by them often still needs further treatment to ensure that it meets the cleanliness standards of specific industries. Treatment measures include further moisture removal, particle filtration, oil and gas removal, temperature regulation and sterilization. The oil-free air compressor system can significantly improve the cleanliness of compressed air by equipping it with dryers, filters, coolers and sterilization equipment, providing protection for the safe production teams in various industries.
Basic principles of oil-free air compressors and air treatment requirements
The uniqueness of oil-free air compressors lies in their oil-free lubricated design structure. Compared with traditional oil-lubricated air compressors, the oil content of compressed air is almost the same, so the risk of secondary air pollution is reduced during use. The air compression method of oil air compressors is usually achieved through material self-lubrication, oil-free coating, etc. Such a design structure is suitable for scenarios with high air quality requirements.
However, compressed air may not only contain oil, but also moisture, particulate matter, oil vapor, odor, etc. These substances can significantly increase in concentration after being concentrated during the compression process, so even if the air is compressed with an oil-free air compressor, further purification may be required. According to different air treatment needs, we can divide purification measures into the following directions: moisture removal, particle removal, oil and gas removal, temperature control and microbial disinfection.
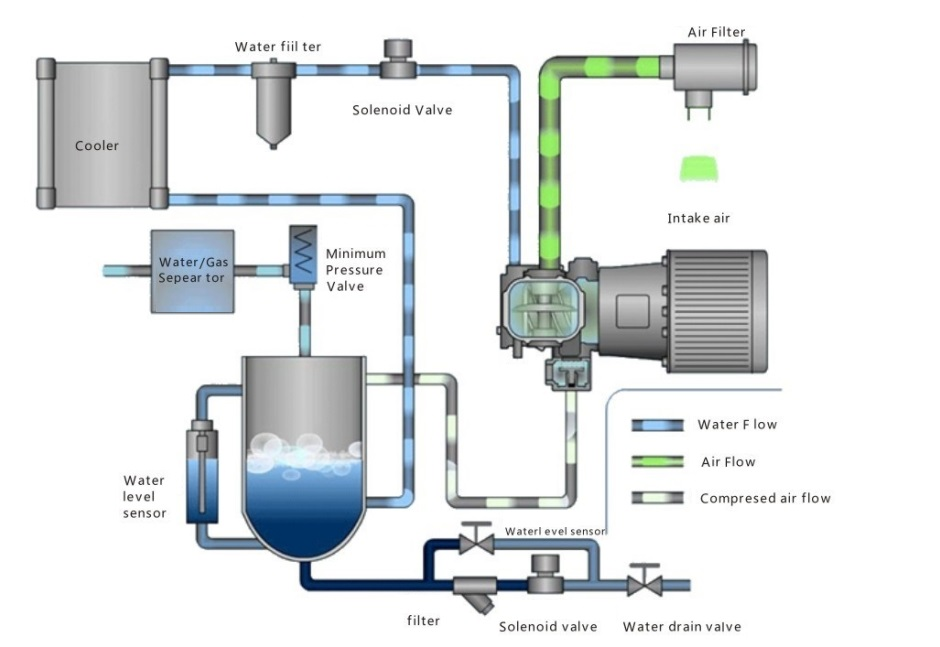
Necessity analysis of air purification
Moisture removal
Moisture sources and effects
Air accumulates in the compressed air system, which may cause internal corrosion of the equipment, pipe blockage, and even failure of pneumatic tools or automated production lines. For many industries, moisture is also a major factor causing product contamination and quality degradation. For example:
- In food processing, humid air can cause products to become damp, affecting the taste, appearance and shelf life of food.
- In the pharmaceutical industry, moisture may affect the stability of drugs, making them damp or even stable.
- In electronic manufacturing, moisture may cause circuit board corrosion and short circuits, affecting the service life of products.
Common methods for removing moisture
Oil-free air compressor systems usually need to be equipped with the following drying equipment to ensure the dryness of the air:
- Freeze dryer: Reduce the air temperature below the dew point, so that water vapor condenses into water droplets and then stirs. Freeze dryers are suitable for applications with medium humidity requirements, such as most industries and batch production.
- Adsorption dryer: Using adsorbents to absorb and adsorb moisture, compressed air can reach extremely low dew point temperatures. This method is suitable for occasions with extremely high requirements for air dryness, such as electronic manufacturing, semiconductors, medical equipment manufacturing, etc.
Typical application scenarios
Food processing, pharmaceuticals, electronic manufacturing and other industries have strict requirements on air humidity, ensuring that air drying can effectively improve product safety and equipment life.
Remove particle
Source and impact
Dust particles, fibers and other particles in the air are usually invisible to the naked eye, but they will accumulate in the compressed air system after entering the oil-free air compressor with air, which may have a serious impact on precision instruments and aviation equipment. Equipment will cause wear of precision parts such as valves and compressors, accelerate equipment aging, and even cause blockage or blockage.
Lifting filtration method
Oil-free air compressor particle machine system usually installs floor filters to lift particles:
- Coarse filter: Usually installed in the primary filtration stage of the air system, used to add new particles.
- Precision filter: Installed at the end of the system, used to remove micron-level particles to ensure that the particle concentration of pollutants in the air meets the clean air standard. Precision filters can effectively remove most of the tiny particles and meet the scenes with higher cleanliness requirements.
Application
In industries such as semiconductor manufacturing and medical equipment manufacturing, tiny objects have a great impact on product quality, so multi-layer filtration is required to ensure air cleanliness. In addition, in the pharmaceutical and food industries, particles in the air may also affect the purity and safety of the product.
Amazing trace oil, gas and odor
The source and impact of trace oil and gas
Although oil-free air compressors do not use lubricating oil, trace oil and gas may be carried in the ambient air, especially in industrial areas with poor air quality, where oil, gas and odor will be sucked into the equipment with the air. These trace amounts of oil and gas may have adverse effects in specific applications. For example, in food, pharmaceuticals and precision manufacturing, oil, gas and odor may contaminate products and even affect user experience.
Oil and gas removal method
Oil-free air compressors need to be equipped with the following purification equipment:
- Activated carbon adsorption device: Using the strong adsorption capacity of activated carbon for oil, gas and odor, oil, gas and odor in the air can be effectively removed.
- High-efficiency oil and gas filter: Further purify the air to ensure that the final air is oil-free and odor-free, meeting industry standards.
Applicable scenarios
In the production process of food, beverages and medicines, any flavor and trace oil and gas may directly affect the flavor, purity and safety of the product, so these industries have extremely high requirements for oil-free and odor-free air.
Air temperature control
Need to control the compressed air temperature?
Compressed air becomes very hot during the air compression process. If it is not cooled, direct use of high-temperature air may cause thermal damage, accelerate the aging of parts and equipment, and affect production stability. For example, in food and laboratory research, excessively high air temperature may cause product deterioration, deviation of experimental results, and other problems.
Common methods of air extraction
Aftercoolers or water cooling systems are often used in oil-free air compressor systems:
- Aftercoolers: can reduce the air temperature to close to the ambient temperature, suitable for most industries and applications.
- Water cooling system: suitable for large-scale industrial production, effectively reducing the air temperature through water cooling to meet the needs of scenarios with high temperature requirements.
Application
In typical application scenarios in food packaging and laboratory analysis, temperature control is critical to ensure that compressed air can meet the needs of specific environments and production processes.
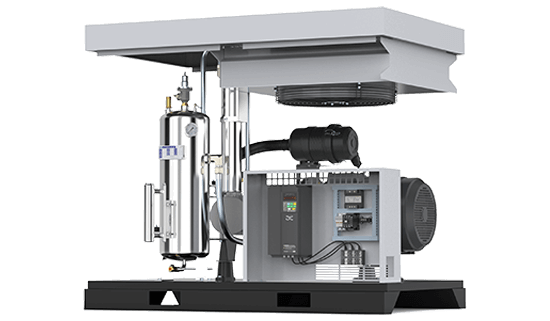
Microbial removal
The impact of air microorganisms
In sterile production environments, such as pharmaceuticals, medical and food fields, microorganisms such as bacteria and fungi in the air will directly affect the safety of products and even threaten the health of end users. Although oil-free air compressors avoid oil contamination, cross-contamination in the air also needs to be strictly controlled in specific applications.
Removal method
Oil-free air compressor systems usually use the following devices for disinfection:
- High-efficiency sterilization filter: Use microporous filtration system to achieve bacteria and other antibacterial in the air.
- Disinfection equipment: Disinfection can effectively kill bacteria and viruses in the air to ensure that the air meets the sterility requirements.
Applicable scenarios
In sterile environments such as hospital operating rooms, pharmaceutical factories, and food production lines, the stability of the air may bring product contamination risks and even affect the health of users. Therefore, sterilization treatment is crucial for these scenarios.
The overall advantages of oil-free air compressor air treatment
Oil-free air compressors not only greatly reduce the risks of oil pollution in use, but also the closed air purification system equipped can ensure the high cleanliness of compressed air and provide the industry with safe and reliable air sources. The system can usually be equipped with flexible purification configurations according to different needs to adapt to different air quality standards and special application scenarios.
The application effect of oil-free air compressors in compressed air purification is remarkable, which not only saves maintenance costs, but also effectively extends the service life of equipment, improves product quality, and makes the production environment cleaner and safer. Its air purification technology is widely used in the food, pharmaceutical, electronic and medical industries, and promotes high-quality production processes.
Conclusion
Equipping oil-free air compressors with devices according to industry standards can ensure that the air meets strict cleanliness standards, extend the service life of the equipment, and ensure product safety and the purification of the production environment. While MINNUO produces oil-free air compressors, it also designs various supporting devices to meet the needs of industries such as food, pharmaceuticals, medical and precision manufacturing. At the same time, we also provide personalized customization services to ensure that your purchase plan not only meets industry needs, but is also sufficiently favorable.