Introduction
Diaphragm compressors are a type of displacement compressor that uses a diaphragm to compress the gas. Unlike other types of compressors, diaphragm compressors do not require lubrication or oil, which makes them ideal for applications where lubricant contamination is a concern. Diaphragm compressors can provide high compression ratios and can operate at high pressures.
Diaphragm compressors are commonly used in industries requiring high purity gases, such as pharmaceuticals, semiconductors and food processing. They are also used in the oil and gas industry to compress natural gas for transportation or storage. In this article, we will discuss the faults that can occur in the operation of diaphragm compressors and give solutions for each of them.
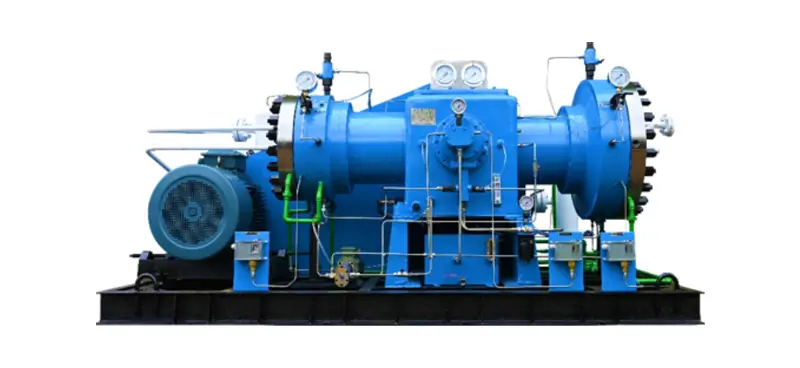
Lubricating oil pressure drops suddenly, less than 0.2MPa
The lubrication system of the compressor is essential to ensure the normal and reliable operation of the compressor. The lubricating oil pressure at the outlet of the oil pump must be kept within an appropriate range. When the oil pressure is too low, the oil supply is insufficient; there is no oil film on each friction surface, or the thickness of the oil film is not enough, and the pad holding accident occurs.
Main causes | Exclusion method |
Insufficient lubricating oil in the crankcase. | Refuel immediately. |
Blockage of the filter, and filtering compontents. | Cleaning. |
Oil pressure gauge malfunction. | Replace the oil pressure gauge. |
The oil pipeline is blocked or broken. | Overhaul oil pipeline. |
Oil supply system malfunction. | Check the oil supply system. |
The viscosity of the oil decreases. | Replace lubricating oil as required. |
The connection parts of the oil pipe are not tight. | Tighten the nut or add gasket. |
The bearing bush and cooper sleeve of the moving mechanism are seriously worn. | Overhaul bearing bush and cooper sleeve. |
The gear pump is damaged. | Replace the gear pump. |
Sealing parts wear out. | Replace the sealing part. |
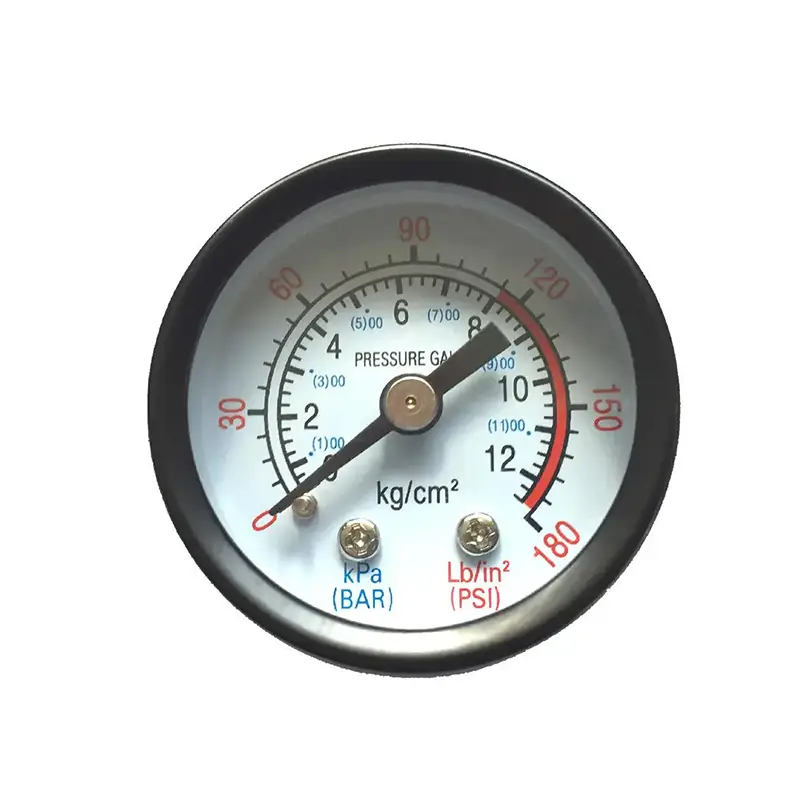
The charge pump is not oiled
The compensation oil pump is the heart of the entire oil circuit system of the membrane compressor. Its function continuously delivers the hydraulic oil required to form the oil pressure. If it breaks down, the entire oil circuit system will be paralyzed.
Main causes | Exclusion method |
Oil inlet and outlet valve ports are not tight. | Replace |
The inlet and outlet valves are not closed tightly. | Disassemble and wash inlet and outlet valves. |
Gear pump oil pressure lower than 0.3MPa. | Check oil pressure cause. |
Wrong position and direction of inlet and outlet valves. | Check carefully and install again. |

Excessive high temperature of lube oil
If the lubricating oil temperature of the diaphragm compressor is too high, the viscosity will decrease. And the oil film formation conditions cannot be reached between the moving parts, which directly affects the service life of the friction parts. So the oil cannot achieve better cooling, lubrication, and noise reduction.
Main causes | Exclusion method |
Insufficient supply of lubricating oil. | Check the oil circuit leakage and add lube oil. |
Low quality lube oil with bad heat radiation. | Replace qualified lube oil. |
Dirty lube oil that increase mechanical wear. | Clean the oil pool and replace the lube oil. |
Movement parts failure. | Check and repair failure parts. |
Poor cooling. | Increasing cooling water. |
Cooling water system leakage or other failures
The failure of the cooling water system of the diaphragm compressor is generally poor cooling, water leakage, etc. If it is not treated in time, it will cause water accumulation at the bottom of the compressor and corrode the casing of the unit. All these cause potential safety hazards to the machine.
Main causes | Exclusion method |
Piping water leakage. | Repair and replace |
Excessive water scale and high gas exhaust temperature. | Get rid of the water scale. |
Safety valve failures
The safety valve is a protective device. When the system pressure exceeds the allowable value, it will automatically open, discharge excess compressed air, and reduce the pressure to normal. The function of the safety valve is to ensure that the system will not cause accidents due to excessive pressure.
Main causes | Exclusion method |
Fail to start up on time. | Readjust. |
Fail to start up to the biggest power. | Readjust. |
Fail to close tightly. | Clean the valve and repair. |
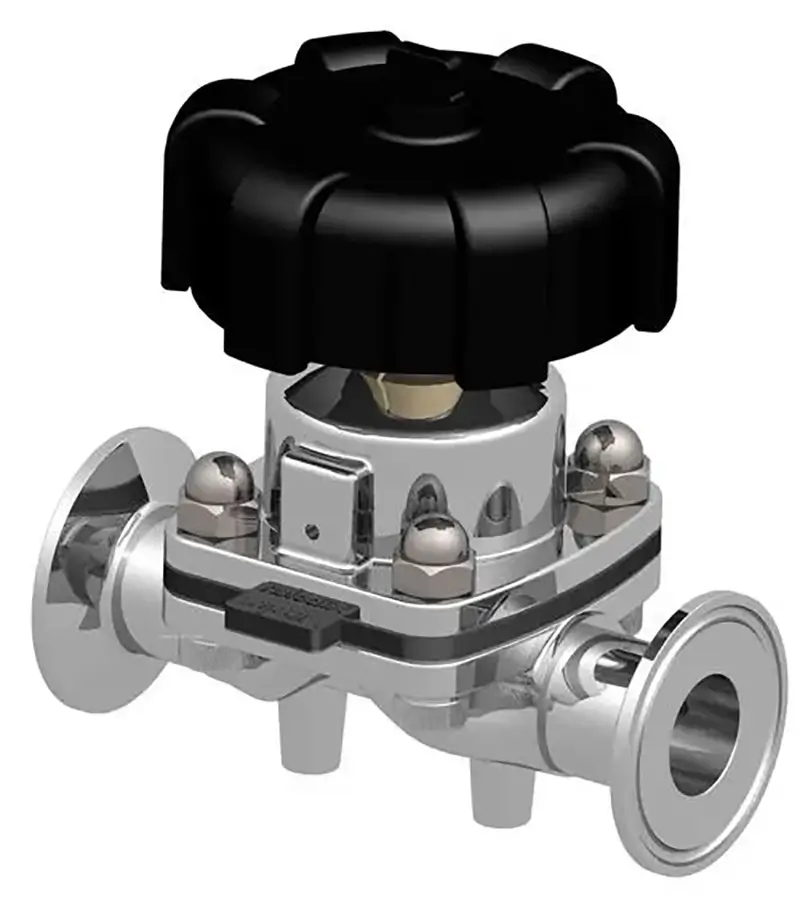
Overheated main bearing bush
Bearing wear is a very common problem, and avoiding it in diaphragm compressors is difficult. One of the main reasons for this failure is that an effective lubricating oil film cannot be formed between the crankshaft shaft diameter and the bearing bush, which directly produces friction.
Main causes | Exclusion method |
Poor contact between shaft radius and shaft bush. | Check and repair. |
Too small clearance of radial fitting. | Check and repair. |
Poor oil supply. | Overhaul the lubrication system. |
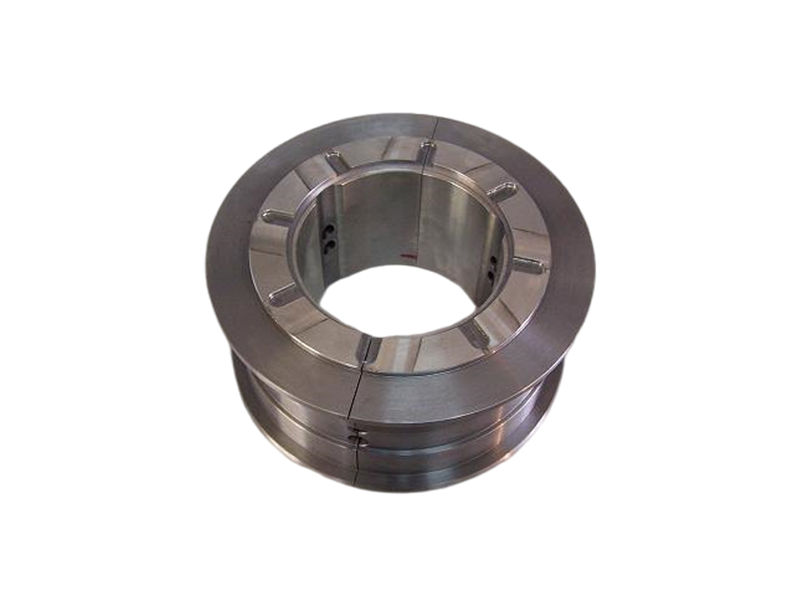
Pressure regulating valve malfunction
The pressure regulating valve is installed between the compressor and the air receiver. Its function is to limit the maximum pressure of the braking system and improve the economy and safety of the system, guaranteeing to ensure the system’s reliable operation. The common ones are pressure-regulating valves and combined pressure-regulating valves with other functions added.
Main causes | Exclusion method |
The valve seat and the valve port are not tight. | Replace. |
Spring loses elasticity. | Replace the spring. |
Gasket below pressure regulator failed. | Replace gasket or increase gasket thickness. |
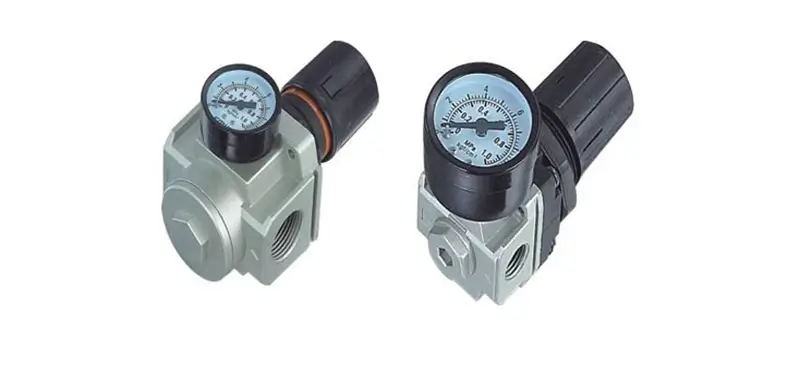
Slave valve malfunction
Unlike the pressure regulating valve, the follow-up valve uses the area difference between the air and oil pressure to form a pressure difference between the air and oil pressure. The oil pressure is a follow-up, which greatly reduces the oil pressure difference of the cylinder diaphragm, reduces the diaphragm pressure, and effectively improves the life of the diaphragm.
Main causes | Exclusion method |
Diaphragm rupture or the sealing loosens. | Replace. |
Oil pipe blockage. | Clean and clear the oil circuit. |
Valve seat and port damaged. | Repair or replace. |
Abnormal sound
The diaphragm compressor does not make much noise during normal operation, but it produces abnormal sounds when a fault occurs. There are many reasons for this phenomenon, and the solutions are different.
Main causes | Exclusion method |
Slapping the cylinder. | The oil cylinder is short of oil, check the oil pressure of the oil cylinder. |
Connecting rod and crankshaft counterweight clashes each other. | Adjust the gap and remove the excess. |
Improper fitting ellipticity of the belt wheel and crankshaft, or the belt wheel loosens. | Change belt wheel to make the conical contact above 70% then tighten the belt wheel. |
Gas valve loosen. | Tighten the valve nuts. |
The size of the bearing rollers is not suitable or worn. | Replace |
Connecting rod nuts loosen. | Tighten and lock. |
Connection of crosshead and piston rod loosen. | Tighten back cap and lock. |
Over big ellipticity of the crankshaft main shaft neck, crank neck or crossheand pin. | Check clearance and ellipticity, repair or replace |
Crosshead guide damaged. | Repair or replace. |
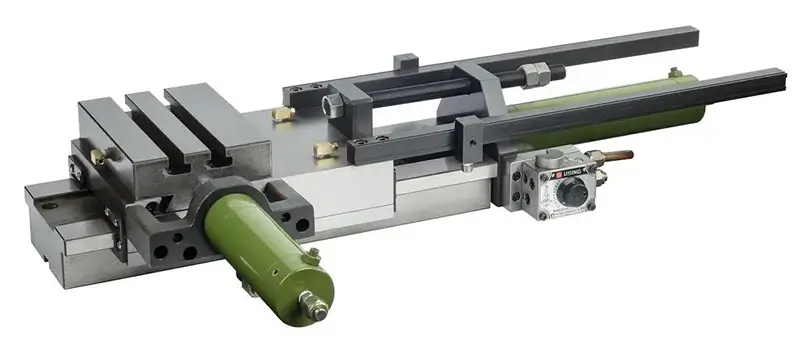
Not enough discharge capacity
The insufficient displacement of the diaphragm compressor has a great impact on the entire machine. If it is not repaired in time, it may lead to broken connecting rods, piston rods, cylinders, and cylinder heads. The insufficient displacement is a problem with the air conditioning of the compressor.
Main causes | Exclusion method |
Intake and exhaust valve port loosen or block. | Repair or replace. |
Excessive inlet and exhaust clearance. | Reduce the clearance. |
Abnormal oil pressure. | Repair. |
Local abnormal air leakage. | Take sealing measures according to the leak location. |
Diaphragm clamp force unevenly distributed or force on the diaphragm. | Tighten cylinder bolts evenly. |
No oil pressure after starting
The insufficient displacement of the diaphragm compressor has a great impact on the entire machine. If not repaired in time, it may lead to broken connecting rods, piston rods, cylinders, and cylinder heads. Insufficient displacement is a problem with the air conditioning of the compressor.
Main causes | Exclusion method |
Insufficient oil in the oil tank | Check and supply crankcase oil. |
Compensating oil pump malfunction. | Overhaul. |
The pressure regulating valve (slave valve) malfunction. | Overhaul. |
Pressure gauge relief valve is open. | Close the valve. |
Oil cylinder pressure abnormal
Abnormal cylinder pressure refers to the deviation of the normal working pressure of the hydraulic cylinder. Hydraulic cylinders are used in various types of machinery and equipment to generate linear force and motion through the use of pressurized hydraulic fluid. The pressure inside the cylinder plays a vital role in determining the efficiency and effectiveness of a machine.
Main causes | Exclusion method |
Pressure regulating valve malfunction. | Check or replace. |
Compensating oil pump malfunction. | Check or replace. |
Diaphragm rupture. | Replace. |
Cylinder sealing surface is not tight. | Overhaul. |
Check valve and damper under the oil pressure gauge malfunction, and the hand violently swings. | Replace or clean. |
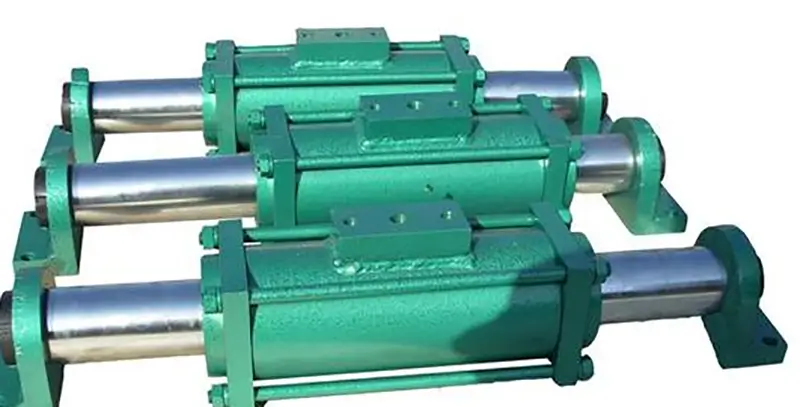
Oil and gas leakage on the sealing surface of the cylinder
The faults that occur on the sealing surface of the diaphragm compressor cylinder are air leakage and oil leakage. This is mainly due to the fact that the pre-tightening force of the cylinder head bolts is too small or uneven, and the sealing surface is defective.
Main causes | Exclusion method |
Insufficient or unevenly tighten force on cylinder cover bolt. | Tighten the bolts. |
The sealing surface is defective. | Repair the sealing surface. |
Damaged O-ring. | Replace O-rings |
Pipe joints are not tightly sealed. | Repair or replace. |
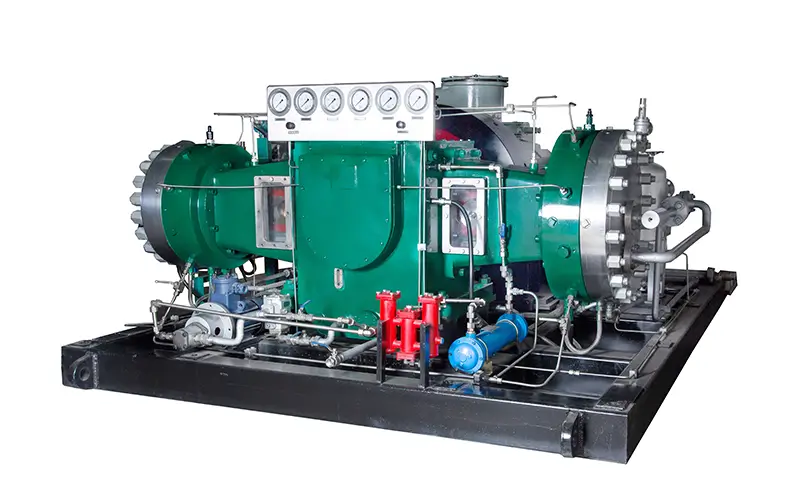
Conclusion
Diaphragm compressors are widely used in chemical companies. Their operating stability has become a key factor for profitability. Therefore, we have analyzed the common faults and causes in the operation of diaphragm compressors, and given solutions. Besides, the users must continuously improve the maintenance technology of the equipment, check the operation of the machine in time, and achieve timely detection and early warning.