Diaphragm compressors are a particular type of reciprocating compressor. Unlike conventional piston compressors, it does not directly use the reciprocating motion of the piston to pressurize the gas. Still, it uses the diaphragm’s deformation to change the cylinder’s volume. Its cylinder does not require lubrication, and the compression medium does not need to come into contact with any lubricant, so there is no contamination. Its compression purity can reach 99.999%. Diaphragm compressors are often used to compress precious gases or all types of gases that are corrosive, radioactive, toxic, or explosive. It is a famous gas compressor in the high-end industrial sector.
What does “diaphragm” mean?
Diaphragm group – the critical component in a diaphragm compressor. It consists of two external barrier diaphragms with an intermediate diaphragm. The diaphragm group is fixed inside the cylinder by a seal, which divides the cylinder into two completely isolated parts – the working chamber and the hydraulic chamber. The diaphragm has good deformation ability and high fatigue life. It can vibrate to change the process chamber’s volume, thus pressuring the gas. Diaphragms are usually made of rubber, plastic, or metal. Most diaphragm compressors have diaphragms made of metallic materials.
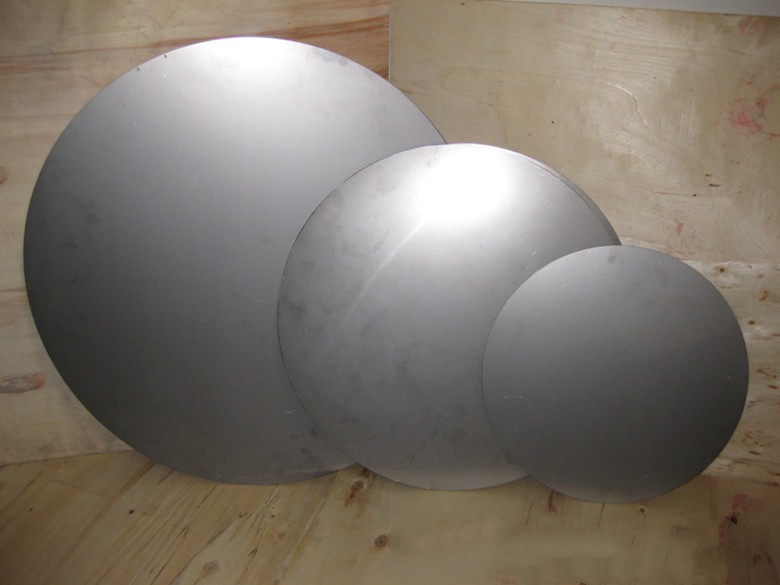
Principle of diaphragm compressor
The most important working part of the diaphragm compressor consists of two systems. They are the hydraulic oil system and the gas compression system. A metal diaphragm completely separates the two systems. The upper gas compression system is the working chamber of the diaphragm compressor. After the active gas enters the room through the inlet valve, it is compressed through the change in volume of the chamber and then discharged through the exhaust valve.
An electric motor usually powers the hydraulic oil system. The motor drives the piston in a reciprocating motion through the drive train. The piston is sealed by a piston ring and moves back and forth in the hydraulic cylinder. During operation, the piston moves upwards, driving the hydraulic fluid, which drives the diaphragm to deform it, thus changing the volume of the working chamber and thus compressing and transporting the gas.
During each compressor cycle, the hydraulic oil pushes the diaphragm against the air disc. If the leaking oil is not replenished promptly, the volume of oil will drop, and the diaphragm will not be able to press against the air disc fully. It will increase the residual volume and affect the performance of the compressor. Therefore, proper compensation of the oil circuit system is vital to ensuring the compressor’s performance.
It is important to note that hydraulic fluid is not just used to transfer kinetic energy. It also lubricates moving parts and cools the entire system with a water-cooled cooler.
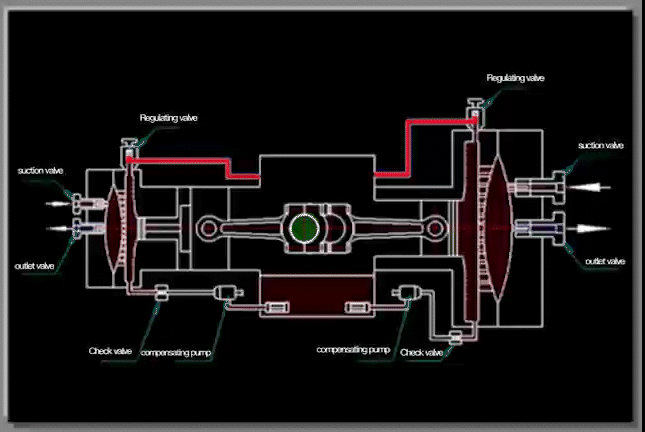
Why use diaphragm compressors?
Unlike conventional reciprocating compressors, diaphragm compressors have a piston that moves in a hydraulic cylinder. Each piston movement generates a fixed volume of hydraulic oil, which drives the diaphragm in a reciprocating motion. The hydraulic oil acts on the diaphragm, so it is the diaphragm that compresses the gas. According to its operating principle, it has many advantages.
1. The diaphragm can effectively separate the hydraulic oil from the working medium, realizing the complete isolation of the compressed medium from the pollution source caused by the traditional reciprocating compressor. Food, pharmaceutical, and other industries with more stringent control of raw material pollution can use it confidently.
2. The working temperature is easier to control. Since the hydraulic oil for driving the diaphragm is stored in the crankcase, we can use a cooling system to cool it. It will make it easier to ensure that the compressor’s working efficiency will not drop due to high temperature.
3. The piston head of a traditional piston compressor is a rigid part. It can’t fit entirely with the top of the cylinder. The diaphragm, on the other hand, can change its shape according to the shape of the air chamber, thus minimizing the remaining clearance volume. That makes the compressor work more efficiently.
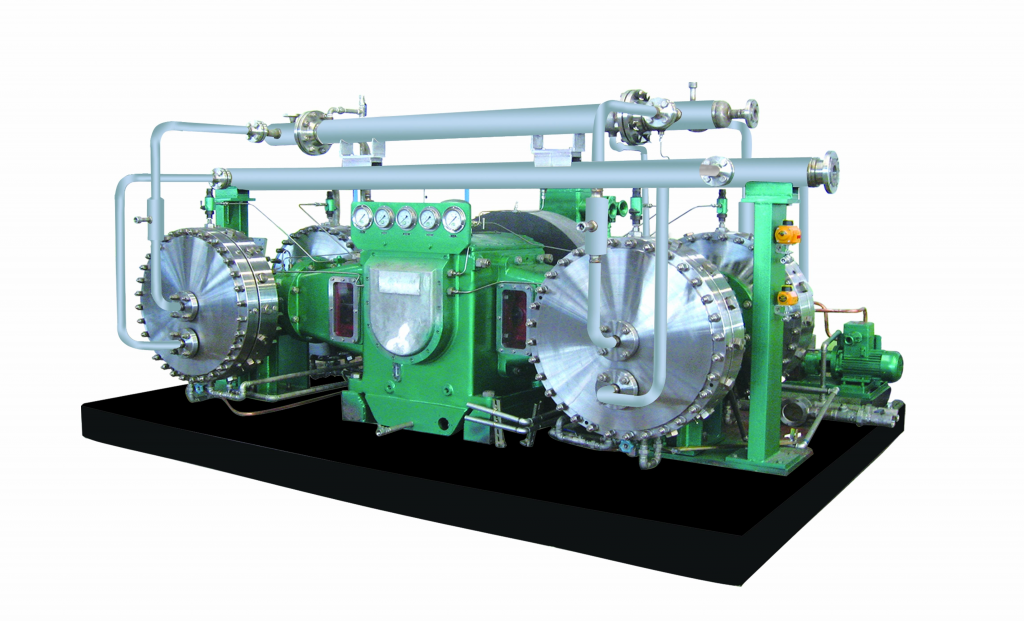
Application Areas
Diaphragm compressor has good cylinder heat dissipation, close to isothermal compression, and can adopt a high compression ratio. Therefore, it can provide a wide pressure range of up to 200 MPa. It is mainly used in the particular gas market, such as industrial gases, food, petrochemical, nuclear power, aerospace, military equipment, scientific research experiments, and other fields. It is suitable for conveying gases with high compression pressure, high purity, flammable and explosive, corrosive solid, and requiring no leakage, such as H2, He, Ar, C2H4, F, HS, CL, SiH4, and NF.
Major Components
As a reciprocating displacement compressor, the structural components of a diaphragm compressor can be divided into three parts: the working chamber, the drive, and the body. The increase in gas pressure is achieved by single or multi-stage compression to meet the customer’s requirements for process parameters such as pressure, flow, and temperature. The whole system mainly has these components.
- Main body
It generally consists of the body, the motor, and the crankcase. During operation, the main body must withstand the pneumatic and inertial forces of the piston and the moving parts. The main body also transfers all or a portion of the weight of the compressor to the base.
- Cylinder
The cylinder is an integral part of the compressed gas in a compressor. Due to its high air pressure, variable heat exchange direction, and complex structure, it has high technical requirements.
- Piston assembly
The piston assembly of a diaphragm compressor consists of a piston, piston ring, piston rod (or piston pin), and other parts. The piston and cylinder form the compression space. The reciprocating motion of the piston assembly is transmitted through the hydraulic oil in the cylinder to the diaphragm group’s reciprocating motion to complete the gas cylinder compression cycle.
- Diaphragm group
The diaphragm compressor diaphragm system is a three-layer structure: two external diaphragms for the barrier layer, the middle diaphragm through the fixed 0-shaped seal to provide a release path. The cylinder is also divided into a hydraulic oil chamber and a working gas chamber. The diaphragm is usually made of rubber, plastic, or metal. Most diaphragm compressors diaphragm made of metal material.
- Valves
The Diaphragm compressor valve is used to control the intake and discharge cylinder components. It is automatically opened and closed under the pressure difference and spring force, the so-called automatic action valve. The air valve usually consists of the valve body, flap, and spring. The air valve on the compressor directly affects the operation of one of the essential components, divided into the intake (air intake) valve and exhaust (exhaust) valve.
- Connecting rod
Diaphragm compressor connecting rods, according to the structure of its large head, can be divided into two kinds: split connecting rods and integral connecting rods.
- Crankshaft
The crankshaft structure uses a split connecting rod, and the large head and crank pin are fixed by connecting rod bolts when assembled. The integral connecting rod is used for eccentric crankshaft structures because the stroke of the strange crankshaft structure is twice the eccentric distance. Thus limiting the necessary connecting rod can be used for small refrigeration compressors. One-piece connecting rod construction is simple and easy to install. The split connecting rod is matched to the crank pin of the crankshaft so that it can be used for long-stroke refrigeration compressors. The large end of the connecting rod is inlaid with thin-walled bearing bushings. That improves its wear resistance.
Of course, in addition to the above components, a diaphragm compressor must also be equipped with a lubrication system, cooling system, electronic control system, etc.