Hydrogen compressors have broad applications in pressurizing, storing, transporting, and utilizing hydrogen. Choosing a high-performance and dependable hydrogen compressor is crucial for industrial and commercial purposes. Compressed hydrogen demands differ depending on the usage, and various hydrogen compressor types are designed to meet different standards and requirements at varying pressure or flow levels. This article will explore the hydrogen compressor types commonly used in the chemical and energy sectors.
Why do we need hydrogen?
Hydrogen is widely used in industry, with over half of production going towards ammonia, methanol, and refining processes. We can obtain it from fossil fuels or biomass or generate it using water electrolysis. Hydrogen is gaining traction in transportation and energy-related sectors as a potential alternative energy source. Although, these applications currently account for less than 10% of global hydrogen consumption.
Hydrogen has various industrial applications across diverse sectors, including:
- Agricultural/chemical industry: Hydrogen is used to produce ammonia for fertilizers.
- Petroleum refining industry: Hydrogen is used in hydrocracking to produce gasoline and diesel and to remove sulfur contaminants.
- Food: Hydrogen converts unsaturated fats to saturated oils and fats, including in margarine and buttercream.
- Metalworking: Hydrogen is used in various applications, including metal alloys and ironmaking.
- Electronics manufacturing: Hydrogen is used as a reducer and etchant in producing semiconductors, LEDs, displays, photovoltaic parts, and other electronics.
- Medical: Hydrogen is used to make hydrogen peroxide and has potential applications for treating various diseases.
Energy industry applications:
- Pan-storage: hydrogen storage for cross-region, large-scale, long-time energy storage.
- Transportation: Hydrogen fuel cell vehicles have high energy conversion efficiency and zero emissions.
- Aviation: hydrogen-powered aircraft for significant carbon emissions reduction.
- Shipping: Hydrogen fuel cell technology can be used to electrify inland and coastal shipping, and zero hydrocarbon ammonia can be used to decarbonize marine shipping.
- Hydrogen-powered trains: China’s trial runs of fuel cell systems instead of traditional internal combustion engines for less noise and significantly lower carbon emissions.
Hydrogen compression
Hydrogen, with its low density and large volume at room temperature, poses challenges for storage and transportation. Hydrogen compressors are employed to safely and efficiently compress it for storage and use.
In chemical production processes where hydrogen is utilized as the feed gas, piston compressors facilitate the chemical reaction by compressing hydrogen to high pressure. For instance, in the ammonia industry, hydrogen-nitrogen mixture is compressed through 6-7 stages to reach a final exhaust pressure of 31.4MPa, while in coal chemical synthesis gas to methanol process, the inlet pressure of hydrogen and carbon dioxide mixture is 2.5MPa, and the final exhaust pressure can reach 5-10MPa or 35MPa.
Hydrogen-powered vehicles are gaining popularity, and hydrogen compressors play a critical role in refueling. They compress the fuel for delivery to refueling stations or during the unloading and filling phases. The most economical method is to compress hydrogen at very high pressures, typically between 350 and 900 bar, before storage and use. For instance, transport fuel cell systems typically store hydrogen at 70 MPa or higher.
Types of hydrogen compressors
Compressors are machines designed to increase the pressure of air and other gases. The compression of air can be achieved through two primary mechanisms. The first is a volumetric compressor, which physically reduces the volume of the container holding the air, making the gas more compressed and dense. The second mechanism is a centrifugal compressor, which increases the velocity of the gas, leading to an increase in pressure and a decrease in volume. Hydrogen compressors are specifically designed for compressing hydrogen gas.
Given the unique properties of hydrogen and the expanding range of hydrogen applications, it is critical to use compressors that can safely handle and discharge the gas for optimal efficiency.
- Additional information:
When discussing compressors, the compression ratio is defined as the ratio between the outlet and inlet pressure. For instance, if a compressor takes in gas at a pressure of 20 bar and raises it to 200 bar at the outlet, the compression ratio would be 10 (calculated as 200 bar divided by 20 bar).
Compression for industrial field
In large-scale chemical processes that involve hydrogenation, there are two main types of compressors: those that transfer pressurized fresh hydrogen to the reaction system to replenish the hydrogen consumed by the reaction, known as supplemental or fresh hydrogen compressors. Due to the relatively significant pressure difference between the inlet and outlet of these compressors and the relatively low flow rate, reciprocating compressors are typically used.
Reciprocating compressor
Reciprocating compressors are volumetric compressors that use a linear drive motor to move a piston or diaphragm back and forth, thereby compressing hydrogen by reducing the volume occupied by the gas. These compressors are insensitive to the molecular weight of the gas. They can achieve high compression ratios through multiple compression stages, making them suitable for reducing fresh hydrogen.
Advantages:
- Wide pressure range, from low to high pressure
- High thermal efficiency
- High adaptability, with exhaust volume that can be adjusted over a wide range, and can be designed for low, medium, high, and ultra-high pressures (over 350 MPa).
Disadvantages:
- It has a low exhaust volume at low rpm, resulting in a bulky machine with a high exhaust volume.
- It has a complex structure, many wearing parts, and high daily maintenance requirements.
- Discontinuous exhaust volume with uneven airflow.
- Poor dynamic balance, resulting in vibration during operation and high noise.
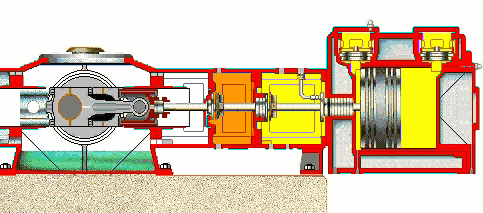
Centrifugal compressor
Another type of compressor used in hydrogenation plants is the circulating hydrogen compressor. Its role is to compress and cool the circulating gas and send it back to the reaction system to maintain the reactor’s hydrogen partial pressure. Due to the significant gas flow rate and slight pressure difference, centrifugal compressors are typically used for this purpose.
Centrifugal compressors rotate a turbine at high speed, throwing the gas into the diffuser behind the working wheel. The gas gains pressure from centrifugal action and can leave the working wheel at high speed. The diffuser reduces the gas speed and transforms kinetic energy into static pressure energy, increasing the pressure.
Advantages:
- It has a large output, simple structure, uniform and continuous gas conveying, slight vibration, and reliable operation.
- The compressed gas is not contaminated by lubricant, and the impeller can be driven by recovered energy, which is more economical.
Disadvantages:
- They can only operate under design conditions to achieve maximum efficiency, and efficiency drops in states higher or lower than the design conditions. When the flow decreases to a certain extent, the compressor produces violent vibration known as “wheezing.”
- Efficiency is generally low and only comparable to piston compressors at high flow rates (greater than 1000m3/min).
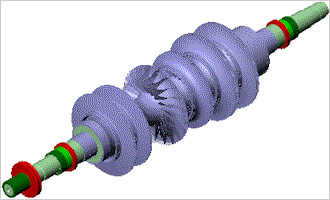
Compression for hydrogen refueling station
The hydrogen compressor is a crucial component pressuring hydrogen into the storage system. Due to the low density of hydrogen and the potential hazards of flammability and explosion, a hydrogen compressor’s most essential performance indicators are its output pressure and gas containment capabilities. Hydraulic piston compressors, diaphragm compressors, and ionic liquid compressors are commonly used in hydrogen refueling stations. Diaphragm and hydraulic piston compressors are primarily used in hydrogen refueling stations where the hydrogen storage pressure does not exceed 45MPa. In contrast, ionic liquid compressors are used in hydrogen refueling stations where the hydrogen storage pressure reaches 90MPa.
Diaphragm compressors
The diaphragm compressor is a device that compresses gas by reciprocating the motion of a piston driven by an electric motor. Unlike piston compressors, the diaphragm compressor adds liquid oil and a diaphragm between the piston and the gas. The diaphragm is fixed between the dome-shaped cover and the body, and when it deforms up and down, the volume of the diaphragm cavity changes, completing the compression and exhaust of gas. The diaphragm compressor has a hydraulic drive diaphragm, which provides good sealing, efficiency, and heat dissipation.
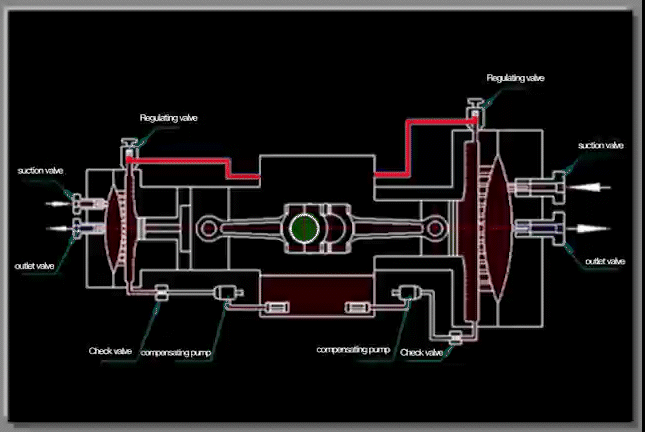
Advantages:
- The technology of diaphragm compressors is mature and widely used in process gas compression.
- They are suitable for situations that require high and very high pressures, with discharge pressures up to 100 MPa, flow rates of 200 Nm3/h to 700 Nm3/h, and efficiency up to 80% to 85%.
- Advanced diaphragm compressors have three-layer metal diaphragm structures, which can achieve output pressures above 85 MPa, and the highest discharge pressure of multi-stage compression can reach 400 MPa.
- Diaphragm compressors are almost pollution-free and have excellent sealing.
Disadvantages:
- Frequent starts and stops significantly reduce the life of the diaphragm, so it is only suitable for hydrogen refueling stations with a large average daily hydrogen refueling volume and requiring continuous operation.
- Additionally, the diaphragm has limited deformation capacity and can only handle a limited amount of gas.
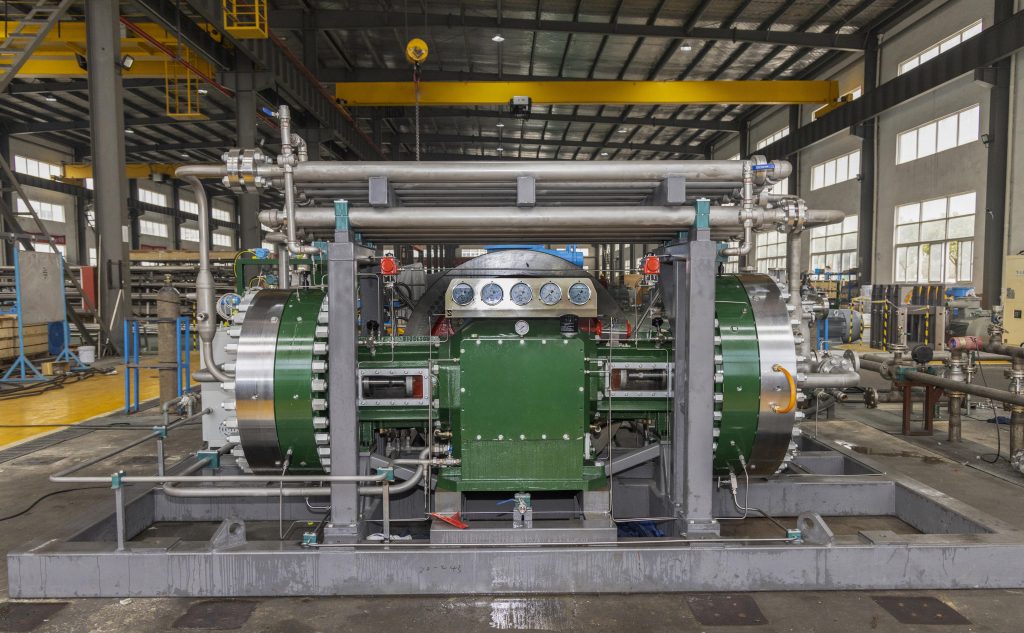
Hydraulically Driven Piston Compressors
Hydraulically driven piston compressors are positive displacement compressors that work on the same principle as ordinary piston compressors for compression components. However, instead of using a crank linkage mechanism, the piston is driven by a hydraulic system.
Advantages:
- Using liquid as a cushion results in less vibration and noise and also seals and cools the system.
- The compressor has a simple structure, fewer parts, and is easy to maintain.
- Due to the liquid’s limited expansion, it is safer.
- The unique structure allows frequent starting and stopping without damage, making it well-suited for gas-filling stations.
Disadvantages:
- The hydraulic-driven piston compressor was developed to solve the problem of low diaphragm compressor diaphragm life. However, its piston working frequency is limited to around a dozen times per minute, so the equipment supply capacity is relatively small.
- Both hydraulic-driven piston compressors and traditional cranked connecting rod piston compressors can contaminate the hydrogen being compressed with the lubricating (or hydraulic) medium during the compression process.
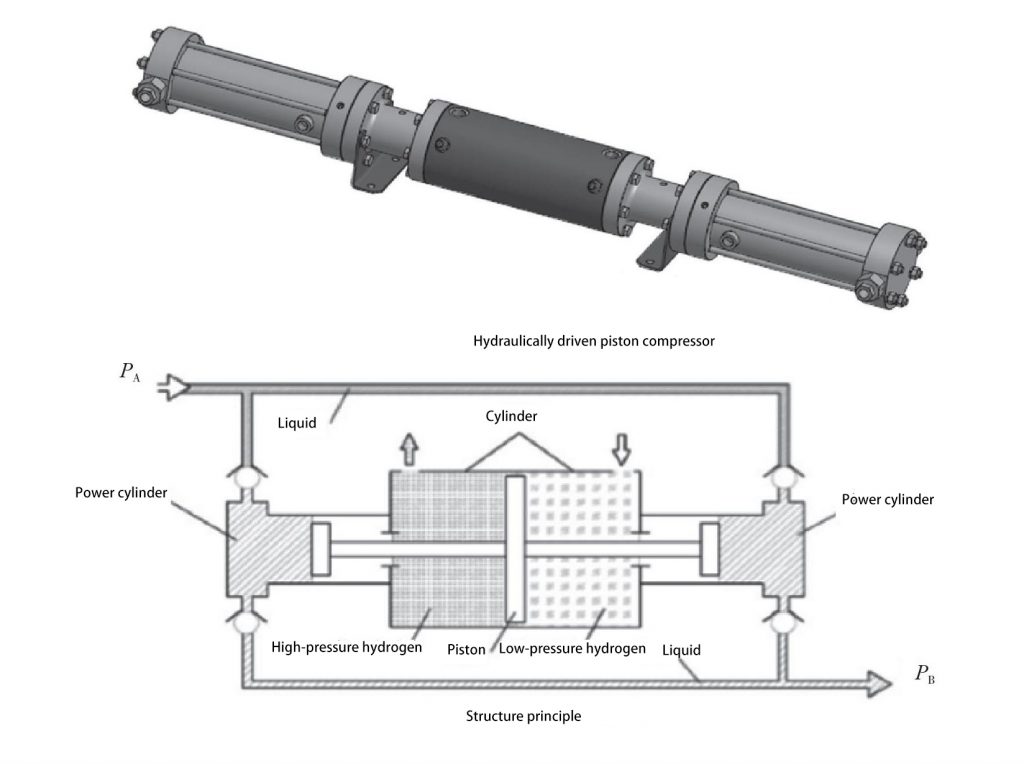
Ionic Liquid Compressors
Ionic liquids are salt molecules with unique chemical and physical properties that make them useful in various applications, such as aerospace, automation, electronics, and energy. In an ionic liquid compressor, a hydraulic piston drives an ionic fluid into a cylinder to compress the gas. A high-pressure liquid pump circulates the ionic fluid, and it has excellent lubrication and cooling properties while being virtually incompressible and not dissolving or contaminating hydrogen.
Advantages:
- The ionic fluid is stable, requiring less frequent maintenance and no frequent replacement of worn parts, which allows for reliable long-term operation.
- The use of ionic fluids ensures the purity of the compressed gas.
- The compressor can operate at high frequencies, achieving a large gas supply capacity.
Disadvantages:
- Ionic liquid compressors are currently expensive and have yet to be widely used.
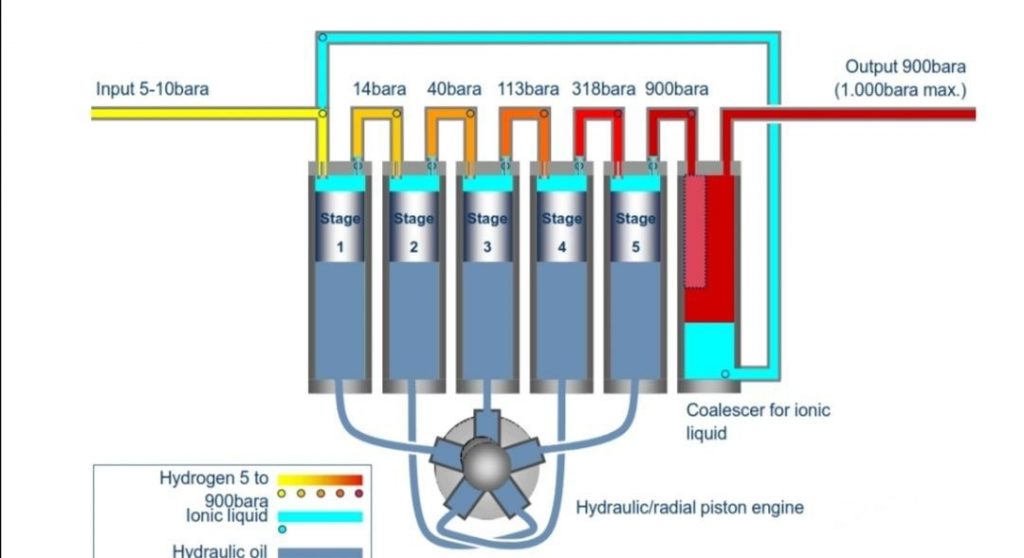
Conclusion
Types | Advantages | Disadvantages |
Diaphragm compressor | · Higher gas purity · Smaller residual volume · Good heat dissipation capability · Wide range of applications Higher single-stage compression ratio | · Relatively small exhaust volume · Higher cost · Concerns about frequent start/stop |
Hydraulically Driven Piston Compressor | · Larger exhaust volume · Longer service life · Easier repair and maintenance needs Adaptability to frequent starts and stops | · Unavoidable for gas pollution · Lower single-stage compression ratio |
Ionic Liquid Compressor | · Simpler construction, easier maintenance needs · Lower energy consumption | · Higher prices · Fewer application cases |
Classification by flow or pressure
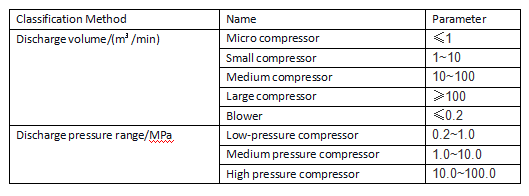
Classification by model
Hydrogen compressors can be categorized into horizontal, vertical, and angle compressors based on the relative position of the base ground plane and cylinder centerline. Vertical and horizontal compressors with cylinders on the crankshaft side are suitable for low air volume conditions. The symmetrical balance compressor is a commonly used medium to sizeable reciprocating compressor in the horizontal compressor category. This compressor has multiple cylinders distributed symmetrically on both sides of the crankshaft at a 180° angle to the cylinder centerline. The opposed compressor is suitable for compressing high-pressure gases, while the angle compressor is suitable for small to medium-sized compressors. The angle compressor can be further divided into different types, such as W-type (60° clamping angle), L-type (90° clamping angle), and fan-type (40° clamping angle), depending on the angle of clamping.
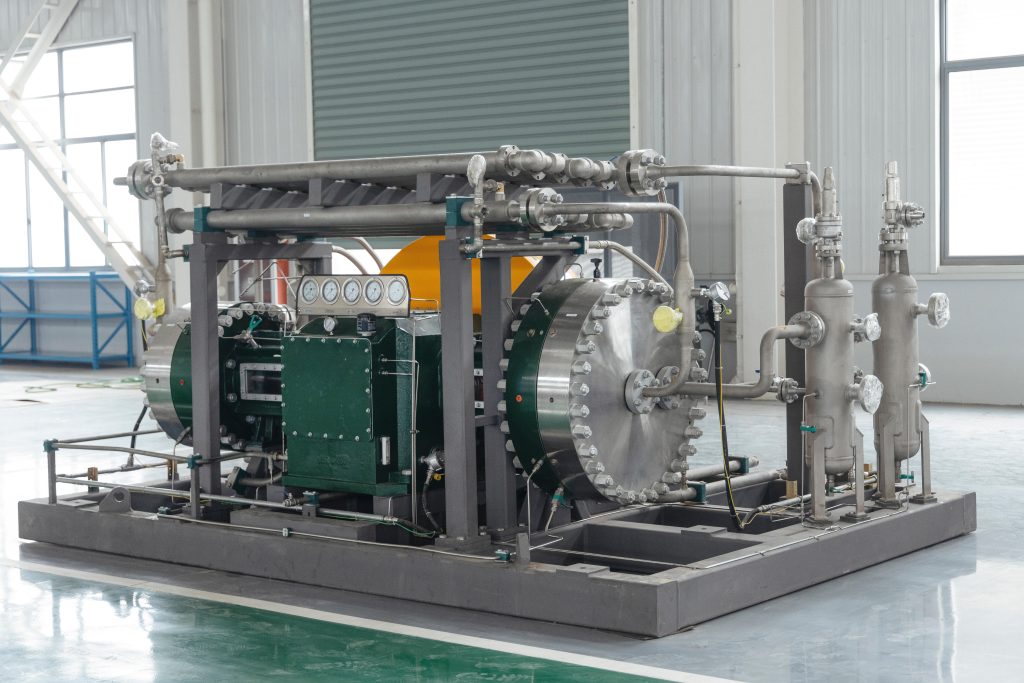
Choosing hydrogen compressors for your industry
Hydrogen compressors are crucial in various industrial processes, including petrochemical gasoline hydrogenation refining and methanol syngas transmission. A malfunctioning compressor can result in device failure, gas leakage, fires, explosions, and other serious accidents, resulting in significant financial losses. Moreover, compressors account for 30% of total costs as a core component of hydrogen refueling stations. Reducing their price by 30% to 50% translates to 15% to 20% of the total cost of a hydrogen refueling station. Thus, selecting a suitable hydrogen compressor is critical to minimize the construction cost of a hydrogen refueling station. At Jiangsu Minnuo, we specialize in creating high-performance and dependable hydrogen compressors for commercial and industrial use. Our technical experts will assess your operational processes and hydrogen requirements to provide superior hydrogen products that meet your long-term needs.