Air compressor oil is essential for the normal operation of air compressors. High-quality air compressor oil can not only effectively lubricate components, but also extend the life of equipment, reduce maintenance frequency and energy consumption. However, there are many types of air compressor oil on the market. How to judge their quality? This article will introduce you to the 6 key factors that determine the quality of air compressor oil to help you make a more informed choice.
The key factors that determine the quality of air compressor oil include viscosity index, oxidation stability, anti-wear performance, anti-emulsification, anti-foaming and clean dispersibility. High-quality air compressor oil can extend the life of equipment, ensure stable operation at extreme temperatures, reduce equipment failure rate and reduce maintenance costs, and is an important guarantee for the efficient operation of air compressors.
Viscosity index
The viscosity index is a measure of the ability of oil to change viscosity at different temperatures. A high viscosity index means that the oil can maintain stable fluidity in high or low temperature environments. For air compressors, the viscosity index directly affects the lubrication effect and the degree of wear of the equipment. Therefore, it is particularly important to choose air compressor oil with a high viscosity index, especially for those equipment that need to operate at extreme temperatures.
The viscosity index is mainly related to the composition and additives of the oil. Mineral oils usually perform poorly in terms of viscosity changes, while synthetic oils, due to their special molecular structure, can better resist temperature changes and show a higher viscosity index. In addition, appropriate additives, such as polyisobutylene (PIB), can effectively increase the viscosity index of oils. Air compressor oils with high viscosity index can not only flow quickly at low temperatures to ensure startup lubrication, but also maintain viscosity at high temperatures to prevent direct contact between mechanical parts, thereby reducing wear and heat.
Imagine the cold winter in the north. When the air compressor needs to start at a low temperature of tens of degrees below zero, if the air compressor oil cannot maintain good fluidity, the lubrication cannot reach the key components at all, causing the equipment to start wearing out at startup. Similarly, in the hot summer or high temperature environment, oils with unstable viscosity index may become too thin, lose the lubrication protection they deserve, and increase the risk of mechanical wear. Therefore, the viscosity index is the “guardian” of the quality of air compressor oil, which can ensure the smooth operation of equipment at different temperatures.
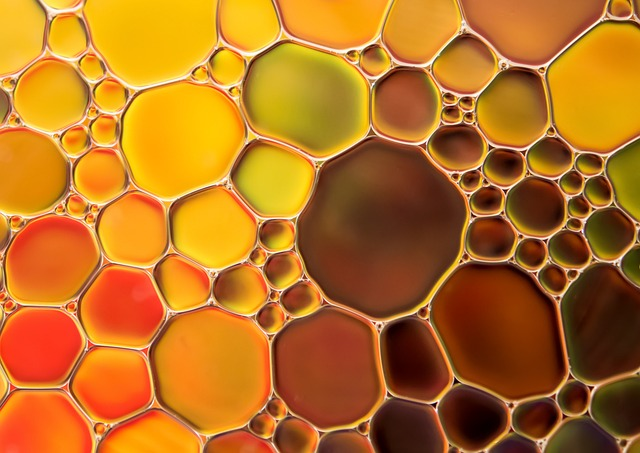
Oxidation stability
Oxidation stability refers to the ability of oil to resist oxidation at high temperatures. The air compressor will generate high temperature during operation, and inferior air compressor oil is easy to oxidize at high temperature, resulting in the generation of sediment and acidic substances, which will not only affect the lubrication effect of the air compressor, but also aggravate the internal corrosion. High-quality air compressor oil has good oxidation stability, which can reduce the generation of sludge and carbon deposits and keep the system clean.
Imagine that the air compressor runs continuously under high temperature conditions. If the oil has poor oxidation stability, the oxidation reaction is like an uncontrolled flame, which quickly erodes the oil and produces a large amount of harmful substances. Those generated sediments will not only block the oil circuit, but also corrode metal parts and cause system failure. Air compressor oil with good oxidation stability is like a “protective cover” for equipment, which can maintain lubrication at high temperatures and prevent these adverse reactions from occurring.
In order to improve the oxidation stability of oil products, manufacturers usually add antioxidants such as phenolic and amine additives to the oil. These additives are like “firefighters” that can effectively inhibit oxidation reactions and slow down the deterioration of oil products. Therefore, for air compressors that are in high-temperature environments for a long time, it is very important to choose synthetic oil with excellent oxidation stability. It is like equipping the equipment with a “firewall” to ensure long-term worry-free operation.
Anti-wear performance
The anti-wear performance of air compressor oil determines its ability to protect the key components of the air compressor, especially when it is running under heavy load. High-quality air compressor oil should contain anti-wear additives, which can form a protective film on the metal surface, reduce friction and wear between components, and thus extend the service life of the equipment. This is especially important for air compressors that need to run continuously for a long time.
During the operation of the air compressor, friction between mechanical parts is inevitable, just like two pieces of metal rubbing against each other, which will inevitably wear out severely over time. If the air compressor oil lacks anti-wear performance, the mechanical operation is equivalent to “running naked” without any protection, and the service life of the equipment is naturally greatly reduced. High-quality air compressor oil is like forming a layer of “invisible armor” on the metal surface, effectively preventing the occurrence of wear.
Especially under heavy load and high-speed operation, the strength and stability of the oil film are crucial. Once the oil film breaks, the metal will come into direct contact, resulting in increased wear. Anti-wear additives, such as zinc phosphate and molybdenum disulfide, are like guardians that form a protective layer on the friction surface, ensuring that mechanical parts remain safe under high pressure. For industrial air compressors that need to run for a long time and are frequently used, choosing oils with high anti-wear properties can greatly reduce downtime caused by wear and help factories produce more stably.
Demulsibility
During the operation of the air compressor, it is inevitable that the air compressor oil will come into contact with water, which requires the air compressor oil to have good demulsibility, that is, it can quickly separate from water to avoid oil emulsification. Emulsified air compressor oil will lose its lubricating effect, resulting in performance degradation or even damage to the air compressor. Choosing air compressor oil with excellent demulsification properties can effectively prevent the negative impact of water on the system.
Imagine working in a humid environment, the oil of the air compressor will inevitably come into contact with water. If the oil has poor demulsibility, water and oil mixed together, like oil drops in milk, not only can not effectively lubricate, but also may form a bad mixture, blocking the oil circuit and causing equipment damage. Oils with good anti-emulsification properties, like magicians, can quickly separate water from oil and drain water, so that the oil can continue to function normally.
Anti-emulsification properties are particularly important for air compressors working in coastal areas or humid environments. It is one of the keys to ensure that air compressors can still work efficiently in harsh environments. Therefore, choosing air compressor oil with excellent anti-emulsification properties can keep the equipment efficient in a humid environment and avoid downtime and failures caused by oil emulsification.
Anti-foaming properties
During the circulation process, oil products may produce foam due to high-speed movement. If the oil product has poor anti-foaming properties, the foam will occupy the volume of the oil tank, affect the transmission of the oil product, and then affect the normal lubrication and heat dissipation of the air compressor. High-quality air compressor oils usually add anti-foaming agents to ensure that the oil in the system can flow smoothly and reduce operating problems caused by foam.
During the operation of the air compressor, if the oil produces a lot of foam when it flows at high speed, it is like pouring beer into a full cup. The full foam will occupy the space of the oil tank, hindering the normal circulation and transmission of the oil product, resulting in poor lubrication and even equipment failure. Air compressor oil with excellent anti-foaming properties can effectively prevent the “big trouble” caused by these “small bubbles”, allowing the oil to flow freely in the system to ensure lubrication and heat dissipation.
Anti-foaming performance is particularly important in air compressors that need to be started and stopped frequently. Just like the coolant of a car engine, if there are too many bubbles, the cooling effect will be greatly reduced, the temperature of the equipment will rise rapidly, resulting in reduced efficiency or even failure. Choosing air compressor oil with good anti-foaming performance can effectively reduce the generation of foam and ensure that the equipment runs smoothly and smoothly.
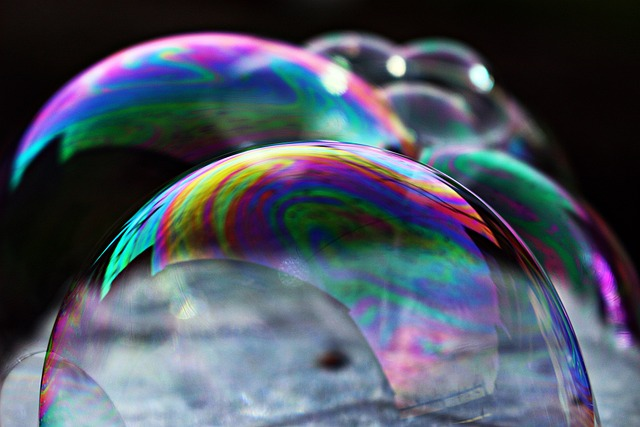
Cleanliness and dispersibility
Cleanliness and dispersibility refer to the ability of oil to keep the inside of the air compressor clean, and can effectively disperse the generated sludge, carbon particles and other impurities to prevent them from accumulating on the surface of the components. High-quality air compressor oil should have good cleanliness and dispersibility to avoid carbon deposits and sludge from wearing the air compressor, ensuring that the air compressor can operate efficiently for a long time.
In the daily operation of the air compressor, some sludge and impurities will inevitably be generated over time, just like the garbage we generate every day. If these impurities cannot be effectively dispersed, they will gradually settle inside the air compressor, block the oil circuit, and affect the operation of the equipment. High-quality air compressor oil is like a “scavenger”, which can disperse and suspend these pollutants in the oil, remove them through the filtration system, and keep the system clean.
Imagine an air compressor filled with “garbage”—its lubrication and heat dissipation effects will significantly diminish, making it challenging for the equipment to operate efficiently over long periods. By choosing an air compressor oil with excellent cleaning and dispersing properties, you can not only reduce maintenance frequency but also effectively extend the equipment’s lifespan. This helps keep the air compressor in optimal condition, ready to handle various working conditions with ease.
The significance of choosing high-quality air compressor oil
Choosing the right air compressor oil can not only extend the service life of the equipment, but also greatly improve the operating efficiency and reduce the failure rate. When judging the quality of air compressor oil, the six major factors of viscosity index, oxidation stability, anti-wear performance, anti-emulsification, anti-foaming and cleaning and dispersibility are crucial. By comprehensively considering these factors, you can choose the most suitable lubricant for your air compressor to ensure that it can maintain the best condition under various working conditions.
High-quality air compressor oil is a worthwhile investment. It can not only reduce maintenance costs, but also reduce unexpected downtime and improve the continuity and stability of production. Especially in some key industries, such as petrochemical, metallurgy and pharmaceutical, the reliability of air compressors is directly related to the stability and production efficiency of the entire production line. Therefore, choosing high-quality air compressor oil is particularly important for these industries.
When selecting air compressor oil for practical applications, consider specific working conditions and equipment types. For example, choose synthetic oils with high oxidation stability for air compressors that operate at high temperatures for extended periods. In humid working environments, select oils with excellent anti-emulsification properties.In addition, regular oil testing and maintenance are also important measures to ensure the performance of air compressor oil. By monitoring indicators such as oil viscosity, acid value and water content, oil deterioration can be detected in time to avoid equipment failures caused by oil problems.
Conclusion
Although the air compressors produced by MINNUO are of good quality and durable, the quality of air compressor oil directly affects the operating effect and life of the equipment. By understanding and mastering the six factors that determine the quality of air compressor oil, you can make more informed decisions when choosing oil and provide reliable protection for the efficient operation of the air compressor. I hope this article can help you better understand the importance of air compressor oil, so that your air compressor can always be in the best condition and easily cope with various challenges.