In industrial applications, compressed air is the power source for many devices and systems. Therefore, it is crucial to select the appropriate compressed air pipeline size to ensure the efficiency and reliability of the system. This article will explore in depth how to determine the size of compressed air pipelines, including the basic principles of pipeline selection, influencing factors, calculation methods, and common practical tips.
Determining the size of compressed air pipelines is a complex process that requires comprehensive consideration of flow requirements, pipeline length, system pressure, pipeline materials, and environmental factors. Through reasonable calculation and design, the efficient operation of the compressed air system can be ensured, energy consumption can be reduced, and production efficiency can be improved. In practical applications, it is advisable to combine professional design software and tools for more accurate calculations and simulations to achieve the best pipeline configuration. On this basis, regular maintenance and inspection are also the key to ensure the long-term and stable operation of the system.
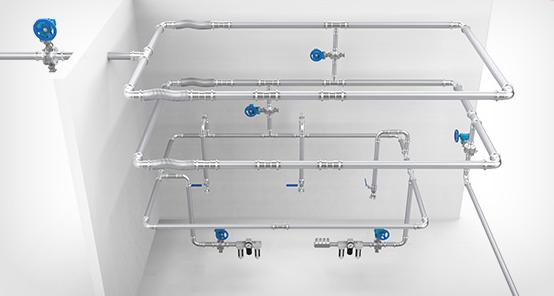
The importance of compressed air pipelines
The design and size of compressed air pipelines directly affect the flow efficiency, pressure drop, and energy consumption of the air. The appropriate pipeline size can not only ensure the normal operation of the equipment, but also reduce energy loss and improve the overall efficiency of the system.
Air flow and pressure loss
When air flows in a pipeline, it is affected by friction and factors such as pipe elbows and valves, resulting in pressure loss. A pipeline size that is too small will increase flow resistance, resulting in insufficient air supply to the equipment and affecting production efficiency; while an oversized pipeline may lead to cost waste.
Economic efficiency of pipeline design
When designing compressed air pipelines, in addition to functional requirements, economic efficiency is also an important consideration. Choosing the right pipe size can reduce material and installation costs while reducing energy consumption during operation.
Factors affecting pipeline size
When determining the size of a compressed air pipeline, multiple factors need to be considered, including:
Flow demand
The size of the pipeline needs to be determined based on the flow demand of the equipment. Flow is usually expressed in standard cubic meters per minute (SCFM) or liters per minute (LPM). Understanding the flow demand of each device and summarizing it into the total flow demand of the system is the first step.
Pipeline length
The length of the pipeline also affects the flow and pressure loss. Generally speaking, the longer the pipeline, the greater the pressure loss. Therefore, when designing the pipeline, it is necessary to consider the layout of the pipeline and minimize unnecessary length.
System pressure
The operating pressure of the system is another key factor. High-pressure systems may require a smaller pipe diameter to maintain the required flow rate and pressure; while low-pressure systems may require a larger pipe diameter.
Pipeline materials
Different pipe materials have different friction coefficients, which affect pressure loss. Commonly used pipe materials include steel, aluminum, plastic, etc. The characteristics of each material may affect the size selection of the pipe.
Environmental factors
Ambient temperature, humidity, etc. may also affect the characteristics of compressed air, thereby affecting the selection of pipe size. In high temperature or high humidity environments, the effects of gas expansion and moisture condensation on the pipeline may need to be considered.
Methods for calculating pipeline size
Determining the size of the compressed air pipeline usually requires calculations through the following steps:
Calculate the required flow
First, determine the total flow demand of the system. It can be calculated by the following formula:

Where Q is the total flow and Qi is the flow demand of each device.
Determine the pipe diameter
Based on the flow requirements, the required pipe diameter can be calculated using fluid mechanics formulas. The following is a commonly used formula:

Where:
- D is the pipe diameter (meters)
- Q is the flow rate (cubic meters per second)
- v is the flow velocity (meters per second)
Generally, the flow velocity should be kept between 7 and 15 meters per second in the compressed air system to avoid excessive pressure loss and noise.
Calculate pressure loss
The Darcy-Weisbach equation can be used to calculate the pressure loss in the pipe:
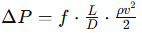
Where:
- ΔP is the pressure loss (Pa)
- f is the friction factor (dimensionless)
- L is the pipe length (meters)
- D is the pipe diameter (meters)
- ρ is the air density (kilograms per cubic meter)
- v is the flow velocity (meters per second)
By calculating the pressure loss, you can determine whether the selected pipe size is suitable for the system requirements.
Common practical tips
When selecting and designing compressed air pipelines, the following practical tips can help improve system efficiency:
Avoid excessively long pipelines
Try to minimize the length of the pipeline and avoid using too many elbows and valves to reduce flow resistance and pressure loss.
Regular inspection and maintenance
Regularly check the tightness and wear of the pipeline to ensure that the system remains in good working condition and reduce leakage and energy loss.
Consider future expansion
When designing the pipeline, consider possible future equipment expansion and flow increase, and reserve a certain amount of pipeline size margin.
Choose the right material
According to system requirements and environmental conditions, choose the right pipeline material to reduce friction loss and improve durability.
Use flow monitoring equipment
Install flow monitoring equipment to monitor the flow and pressure in the pipeline in real time, detect problems in time and make adjustments.
Conclusion
If you are designing a compressed air system, please contact our MINNUO sales engineer to help you design an ideal and optimized compressed air distribution system to reduce operating costs and improve productivity.
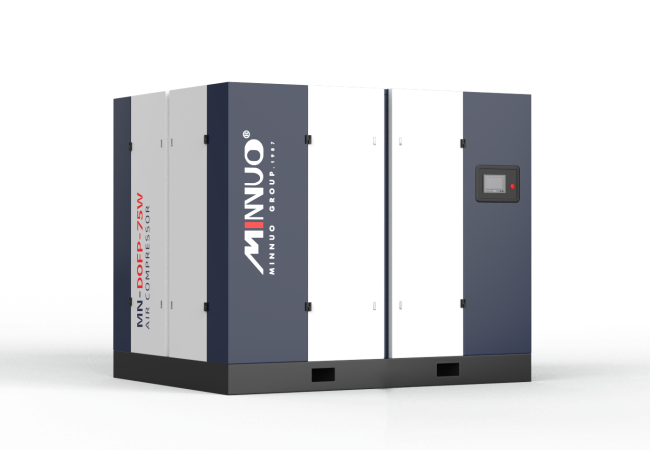