The global aluminum smelting industry is experiencing rapid growth, particularly driven by emerging markets such as the Middle East. As new smelting projects continue to grow, so does the demand for high-performance equipment to support aluminum production. Notably, a major aluminum smelter in the United Arab Emirates has completed 50% of its new project development, highlighting how ongoing investments are driving this expansion. As the industry continues to grow rapidly, the need for robust and reliable equipment is becoming increasingly urgent—especially for critical components like sliding vane compressors. However, due to the high costs of components from suppliers like Mattie, many companies are seeking cost-effective alternatives.
Sliding vane compressors, also known as rotary vane compressors, are a type of positive displacement compressor that uses rotating vanes within a rotor to compress air or gas. Its operating principle involves capturing and reducing the volume of gas between the blades and the housing to increase pressure, enabling it to consistently meet high-pressure demands while offering durability and reliability—key factors for operational success.
This article will explore how MINNUO sliding vane compressors meet these demands, highlighting their role as an economical alternative to Mattie’s traditional high-cost solutions, helping businesses maintain efficient production processes while minimizing downtime and maintenance costs.
1. Why is the sliding vane compressor a critical component of the aluminum electrolysis crane system?
1.1 The role of the sliding vane compressor in the aluminum electrolysis crane system
The aluminum electrolysis crane system requires a large and stable supply of air pressure to ensure efficient operation, and the sliding vane compressor plays a crucial role in this process. It primarily provides the crane with sufficient compressed air to ensure stable equipment operation, particularly during the aluminum electrolysis process, which demands high-pressure air.
Sliding vane compressors provide continuous and stable airflow, enabling smooth lifting and operation of the crane. By optimizing airflow output, sliding vane compressors maximize energy efficiency and extend equipment lifespan.
1.2 High-pressure stability advantages of sliding vane compressors
Sliding vane compressors are widely used in the industry, with some opting for screw-type air compressors. The following table compares their core advantages:
Comparison dimensions | Sliding vane compressor | Screw compressor |
High temperature resistance | ✅ Excellent (stable operation at 60°C ambient temperature) | Limited (usually requires ≤40°C) |
Lifespan | ✅ Long (design life of 200,000 hours+) | Medium to long (major overhaul required after 100,000-150,000 hours) |
Adaptability to harsh environments | ✅ Extremely strong (dustproof, corrosion-resistant, vibration-resistant) | General (requires additional protection) |
Structural complexity | ✅ Simple (few moving parts) | Complex (precise rotor meshing) |
Maintenance costs | ✅ Low maintenance (no need for regular bearing/seal replacement) | High (regular replacement of oil separators/bearings/seals) |
Energy efficiency | Medium-high (single-stage compression) | ✅ High (two-stage compressor models are preferable) |
Noise level | ✅ Low noise (≤70 dB(A)) | Medium-high (≥75 dB(A)) |
Aluminum electrolysis crane systems typically require a high-pressure air source to drive complex mechanical systems. Sliding vane compressors, due to their structural advantages, can operate continuously under high pressure, maintaining a stable air output, and are particularly suitable for large-scale equipment exceeding 90 kW.
In aluminum electrolysis processes, any instability in airflow or insufficient pressure can lead to production interruptions or equipment failures. Therefore, sliding vane compressors ensure that aluminum electrolysis crane systems can operate stably under high loads, significantly reducing the risk of equipment failures.
1.3 维护简便,降低运营成本
The low-failure-rate design and modular structure of sliding vane compressors result in significantly lower operational costs compared to screw compressors. Taking a 90kW air compressor commonly used in aluminum electrolysis workshops as an example:
Cost type | Sliding vane compressor (unit price $22,222) | Standard permanent magnet screw compressor (unit price $10,417) | Difference comparison |
Equipment depreciation cost | $22,222 ÷ 15 = $1,481/year | $10,417 ÷ 5 = $2,083/year | Screw machine height 40% |
(amortized over useful life) | ≤$417/year | ≥$1,111/year | Screw machine height 167% |
Typical annual maintenance cost | (Only oil change and basic inspection required) | (Replacement of oil separator, oil filter, air filter, and bearing maintenance) | Pure incremental cost |
► Data conclusions:
Annual comprehensive operating costs: Sliding vane compressor ≤$1,908 vs. Screw compressor ≥$4,874
Total costs over 15 years: Sliding vane compressor $22,222 + ($1,908 × 15) = $50,842 vs. Screw compressor $10,445 × 3 units + ($4,874 × 15) = $104,445
→ The total lifecycle cost of the sliding vane compressor is reduced by 46%, and it avoids the risk of production downtime due to three equipment replacements.
1.4 成本效益(效率和可靠性的双重优势)
The cost advantage of sliding vane compressors lies not only in “lower maintenance costs,” but also in continuously creating value through high-efficiency conversion and zero unexpected downtime:
Energy efficiency benefits:
Sliding vane compressors have a specific power consumption ≤6.0 kW/(m³/min), while screw compressors typically have ≥6.4 kW/(m³/min)
Calculated based on 8,000 operating hours per year and an electricity rate of $0.25/kWh:
Annual electricity cost difference = 90 kW × (6.4–6.0)/6.0 × 8,000 h × $0.25 = $12,000
→ 15 年内节省 180,000 美元电费
Production continuity assurance:
An aluminum electrolysis crane shuts down for 1 hour due to a gas supply interruption, resulting in losses exceeding $14,000. The sliding vane compressor’s bearing-free/gearless design eliminates sudden failure points, ensuring 24/7 continuous crane operation.
► Comprehensive economic benefits:
Cost items | Sliding vane compressor (15 years) | Standard Permanent Magnet Screw Compressor (15 years) |
Equipment purchase cost | $22,222 | $31,337 (3 units) |
Operating and maintenance cost | $28,621 | $73,119 |
Electricity cost | $601,671 | $701,949 |
Total cost | $652,576 | $806,406 |
→ Slide valve machine saves $153,830 (19% of the total cost of screw machine) |
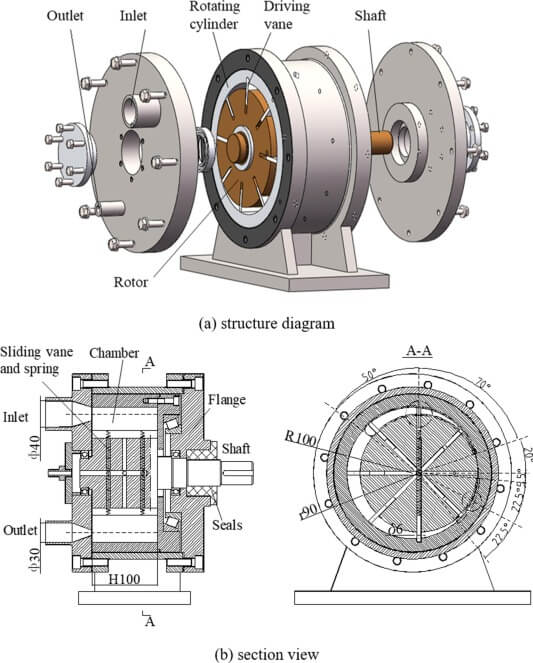
图1 滑片压缩机详细原理
2. Potential market size: Each project requires dozens of sliding vane compressors.
随着全球铝冶炼行业的持续增长,尤其是在中东、俄罗斯、印度等国家,需求日益增长。这些大型铝冶炼厂每年需要数十台甚至更多的滑片式压缩机,以确保高效稳定的产能。由于铝冶炼过程中对气压的要求很高,滑片式压缩机凭借其在提供稳定气流和维持高压方面的优势,已成为铝电动起重机系统中不可或缺的关键设备。
2.1 全球铝冶炼产能重点区域(2024年数据)
Country/Region | Annual production capacity (10,000 tons) | Core Expansion Projects | Sliding Plate Machine Demand Characteristics |
China | 4,300 | Xinjiang Zhonghe Electrolytic Aluminum Technical Renovation Project | Replacement of existing equipment, mainly models above 90kW |
India | 410 (↑35%) | Hindalco’s Mahan Aluminum Plant Phase II | Dense new projects, with single factory demand exceeding 50 units |
Middle East | 650 (↑20%) | Emirates Global Aluminium (EGA) | High-temperature environments, 100% selection of high-temperature-resistant sliding plate machines |
Russia | 390 | RUSAL Taishet Aluminum Plant | Extreme cold conditions, rigid demand for vibration-resistant models |
► Demand calculation: Taking the Hindalco project in India as an example (500,000 tons of additional production capacity), the supporting crane system requires 22 90kW sliding vane compressors (each serving 12 electrolytic cells), with a single project equipment investment of over 3 million yuan.
2.2 Global sliding vane compressor brand competition landscape
▌铝冶炼行业市场份额:
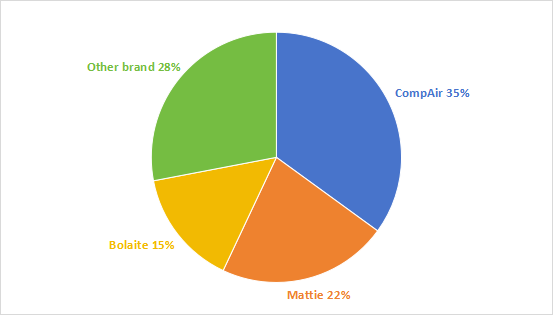
康普艾技术优势:获得专利的高温铸铁缸体
Mattie 核心客户:RUSAL(俄罗斯)、Ma’aden(沙特阿拉伯)
博莱特全国价格优势,主导新疆项目
Other brands, including Atlas Copco and Ingersoll Rand non-professional models
Note: CompAir and Mattie together dominate 57% of the high-temperature special sliding vane compressor market, with their market share concentrated in new large-scale smelting projects.
2.3 Market Growth Engines: Four Driving Factors
Capacity Expansion:
India plans to add 2.8 million tons of new capacity over the next five years → driving demand for over 600 units of 90kW+ sliding vane compressors
The Middle East’s EGA has launched a zero-carbon electrolysis project, with a equipment replacement wave involving the update of 120 compressors
Technological Replacement:
Iran’s South Aluminum and other older plants are phasing out piston compressors, with single-plant retrofit demand for 18-25 sliding vane compressors
Maintenance Cost Pressure:
Vietnam’s Novelis plant has measured that the annual maintenance cost of sliding vane compressors is $12,000 per unit lower than screw compressors → driving replacement of existing equipment
In practical applications, aluminum smelters typically configure multiple sliding vane compressors with power ratings of 90 kW or higher based on production scale. This is not only to meet the continuous demand for air pressure but also a necessary measure to ensure smooth smelting processes. Additionally, the long-term operational costs, maintenance requirements, and system stability of these devices are critical factors for project success.
2.4 Data Validation: Single-Project Economic Scale Calculation
Taking the Taishet Aluminum Plant in Russia (annual capacity of 428,000 tons) as an example:
Demand stage | Sliding Plate Machine Configuration Plan | Quantity | Total power |
Electrolytic cell shelling | 90kW Cold-Resistant Type (-45°C Operation) | 16 units | 1440kW |
Anode assembly and transportation | 75kW Dust-Proof Type (IP65 Protection) | 4 units | 300kW |
Flue gas purification system | 45kW Variable Frequency Control | 2 units | 90kW |
Total | → 22 units installed in a single project | Quantity | 1830kW |
► Market size extrapolation: Globally, an average of 5 similar projects are added annually → Annual demand for new projects alone: 110 high-end sliding vane compressors (approximately $25,074,000 market capacity).
According to industry trends, the number of sliding vane compressors required for each aluminum electrolysis crane project is typically correlated with the production capacity scale of the smelter. As projects progress, market demand for high-quality, highly stable compressor equipment will continue to grow.
3. Current Status and Bottlenecks of Mattie Sliding Vane Compressors
3.1 核心技术壁垒高
Sliding vane compressors appear structurally simple, but their core technologies are not easily mastered, particularly in the following areas, which present significant technical barriers:
3.1.1 Sliding Vane Materials and Wear-Resistant Technology
The sliding vane is one of the core components of the entire device, requiring excellent sealing performance and wear resistance during long-term high-speed operation.
High-quality sliding plate materials must possess high strength, high toughness, self-lubricating properties, and an extremely low thermal expansion coefficient. Mattie has pioneered solutions to these technical challenges by adopting special carbon materials or high-performance composite materials, ensuring stable operation even under extreme operating conditions.
3.1.2 Stator (Cylinder) and Rotor Processing Precision
The fit between the sliding plate and the rotor slots, as well as the inner walls of the cylinder, requires extremely high precision. Even minor machining errors can lead to reduced compression efficiency or unstable operation.
Mattie has mastered high-precision concentricity machining and coating technology, ensuring the longevity and stability of the equipment.
3.1.3 高性能涂层与散热设计
The continuous friction between the sliding plate and the cylinder walls causes significant heat generation. Conventional designs struggle with heat dissipation, exacerbating wear and thermal expansion, which can compromise sealing performance.
Mattie has developed a proprietary combination of heat dissipation and surface coating technologies from an early stage, effectively extending equipment operational lifespan.
3.2 Patents and Market Strategy
3.2.1 Core Patent Protection
Mattie has filed numerous patents in the sliding vane compressor field, covering structural design, lubrication systems, gas sealing, and optimized sliding vane shapes, making it difficult for competitors to imitate without infringing on patents.
3.2.2 高壁垒品牌定位
Mattie initially targeted the high-end markets in Europe and the Americas, establishing a strong reputation in industries such as petrochemicals, energy, rail transportation, and environmental protection, where equipment stability is critically important.
Its brand image of “reliability as the standard” makes it difficult for new entrants to penetrate the high-end market.
3.3 Market Supply Chain Advantage
Mattie has established long-term partnerships with global high-end component suppliers, such as imported bearings, seals, and lubrication systems, ensuring that its sliding vane compressors have an exceptionally long lifespan and low failure rate.
Additionally, Mattie leads the industry in after-sales service, data monitoring, and customized services, offering users an unparalleled experience.
3.4 High Barriers for Late Entrants
Even if late entrants can replicate the structural design of sliding vane compressors, they struggle to surpass Mattie in core performance, lifespan, and stability. The significant R&D investments and trial-and-error costs involved make it challenging for newcomers to break into the market, resulting in Mattie effectively monopolizing the industry for an extended period.
3.5 Technological Leadership, but High Costs
Mattie’s sliding vane compressors have long held a technological advantage in the European market, winning the favor of many large industrial clients with their advanced design and outstanding performance; however, this technological leadership comes with high production and operational costs, especially during large-scale production, where cost advantages gradually diminish.
3.6 High Costs, Long Lead Times, and Limited After-Sales Service
Despite Mattie’s technical advantages, its products remain priced at a premium level. The high costs and extended lead times often force customers to make significant budgetary sacrifices; additionally, Mattie’s after-sales service network is not sufficiently established globally, leading to slow response times and inadequate technical support for customers in many regions when equipment malfunctions or requires maintenance.
3.7 Challenges on the Re-evaluation List
As market competition intensifies, Mattie compressors are increasingly being placed on the re-evaluation lists of multiple procurement parties. Many companies are beginning to reassess the overall cost-effectiveness of their products, especially under the dual pressures of budget constraints and long-term operational costs. As global industrial sectors increasingly demand more economical, reliable, and low-maintenance solutions, Mattie faces new challenges in maintaining market share and achieving sustained growth.
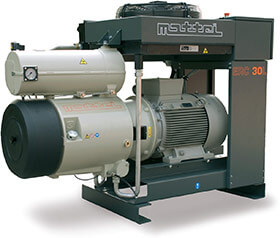
图2Mattie压缩机
4. MINNUO’s Market Breakthrough: Deepening Advantages and Overcoming Challenges
4.1 Unmatched Core Advantages
Advantages | Specific Features | Customer Value |
Deep customization capabilities | – Voltage-adaptive design (compatible with global power grids ranging from 220V to 1140V) | Break down barriers between equipment and application scenarios. |
Supply chain strength | – Motors customized for specific operating conditions (explosion-proof/high-altitude/high-temperature versions) | Avoid secondary procurement and adaptation costs, shortening the production cycle by 40%. |
Intelligent operation and maintenance ecosystem | – Flexible modification of critical valve components (pressure valve response accuracy ±0.1 bar) | Reduce total cost of ownership by 25%. |
Case study: An Indonesian aluminum smelter adopted MINNUO’s customized 160kW compressor (replacing outdated Mattie equipment) and saved $120,000 in transformer procurement costs through voltage adaptive upgrades. The remote diagnostic system provided a three-week advance warning of bearing wear, avoiding $500,000 in production losses.
4.2 Ways to Break Through Market Challenges
Current Disadvantages and Response Strategies:
Challenges | MINNUO Response Plan | Progress |
Market share needs to be increased | – Old Machine Replacement Program: Mattie equipment that is 8 years old can be traded in for a 30% discount on a MINNUO purchase. | Successfully replaced 32 old Mattie machines in 17 countries |
Brand awareness is insufficient | – Financial Support: 3-year interest-free installment plan available. | Industry search volume increased by 300% in Q1 2024 |
Double squeeze from competitors | – Industry White Paper Program: Release of the “Energy Efficiency Guide for Compression Systems in Aluminum Smelters.” | Won a lithium battery project in Africa (beating Compai’s bid) |
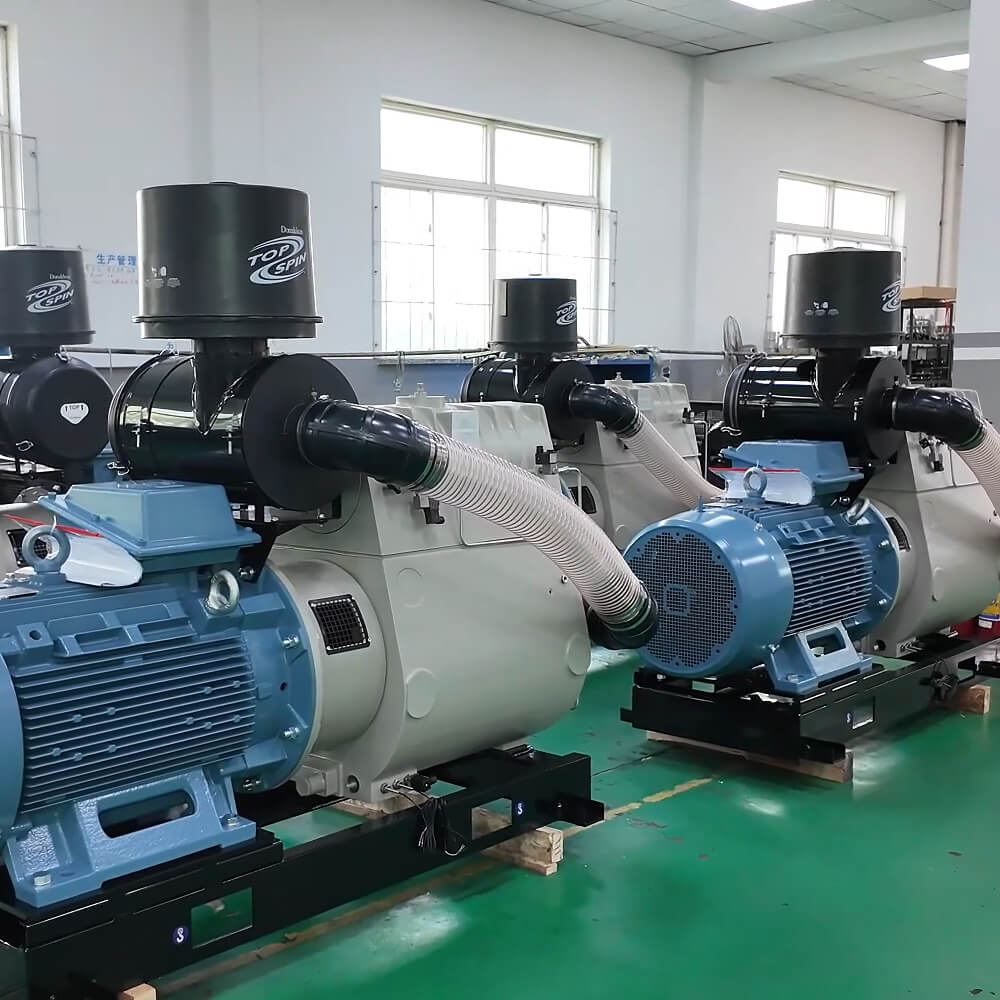
图3 MINNUO产品展示
5.深入的竞争对手比较
在铝电解等行业,对高性能、可靠的压缩机的需求至关重要,因为系统效率直接影响运营成本和可持续发展目标。Mattie 和 CompAir 长期以来一直是该市场的主导者,而 MINNUO 则将自己定位为经济高效的替代方案。以下比较重点突出了 MINNUO 滑片压缩机与 Mattie 和 CompAir 产品的区别和优势:
5.1 与欧洲领导人的终极摊牌
Key indicators | Mattie (Italy) | Compressor (France) | MINNUO (China) |
Procurement costs | €220,000 (160kW benchmark) | €180,000 | €149,000 (↓32%) |
Delivery cycle | 90-120 days | 60-75 days | 30-45 days |
Maintenance response | Third-party agent (72 hours+) | Authorized service center (48 hours) | Remote diagnosis + direct engineer dispatch (24 hours) |
Power adaptability | Fixed 380V | 380V/415V optional | Full voltage customization |
Total cost over 10 years | €480,000+ | €410,000 | €298,000 |
Cost calculation model: Based on a 10-year cycle for 160kW equipment, MINNUO cost savings = 1 Mattie new machine purchase price (including electricity costs/maintenance costs/production downtime losses)
价格优势:
Mattie 和 CompAir 压缩机价格相对较高,而 MINNUO 压缩机的设计旨在显著降低成本,同时又不牺牲质量。MINNUO 内部生产关键部件,从而降低了生产成本,使其成为大型项目更具成本效益的选择。
Technology and Performance:
这三个品牌均提供高性能滑片压缩机,但 MINNUO 的技术创新(尤其是在核心部件生产方面)确保其能够达到或超过 Mattie 和 CompAir 压缩机的性能水平,同时以更低的价格提供竞争优势。
交货时间:
MINNUO leverages its domestic parts and assembly supply chain to offer shorter delivery times, typically 30 to 45 days. This is significantly faster than the longer delivery times of Mattie and CompAir, whose extended lead times could cause delays in large-scale projects, especially in time-sensitive operations like aluminum electrolysis.
Maintenance and Serviceability:
MINNUO does not merely sell compressors but also provides comprehensive service packages. From remote monitoring systems to convenient access to spare parts, MINNUO’s customers benefit from lower total cost of ownership, thanks to minimized downtime and continuous maintenance. In contrast, Mattie and CompAir’s after-sales service is more limited, often requiring third-party maintenance, which increases the complexity of after-sales support.
Customization Flexibility:
Mattie offers generic solutions with fixed power ranges, while MINNUO provides more customization options, offering compressors with power ranges from 90 kW to 160 kW tailored to project requirements. This flexibility enables MINNUO to more effectively meet the needs of both small-scale operations and large-scale industrial applications.
5.2 Golden window of opportunity to replace old Mattie machines
技术替代可行性:
✅ 100% interface compatibility (flange size/control signal/mounting base)
✅自动风量补偿(MINNUO智能变频技术补偿管道损失)
Economic breakthrough point:
Mattie Old machine repair——-(rotor replacement $65,000) can be used for another 3-5 years.
Mattie complete replacement——– $220,000 used for 10 years
Replace MINNUO Trade-in of old machine + price of new machine———$120,000 for 12 years of use + remote maintenance
Conclusion: Replacing MINNUO extends the service life by 7 years compared to repairing old machines, with a 41% reduction in overall costs.
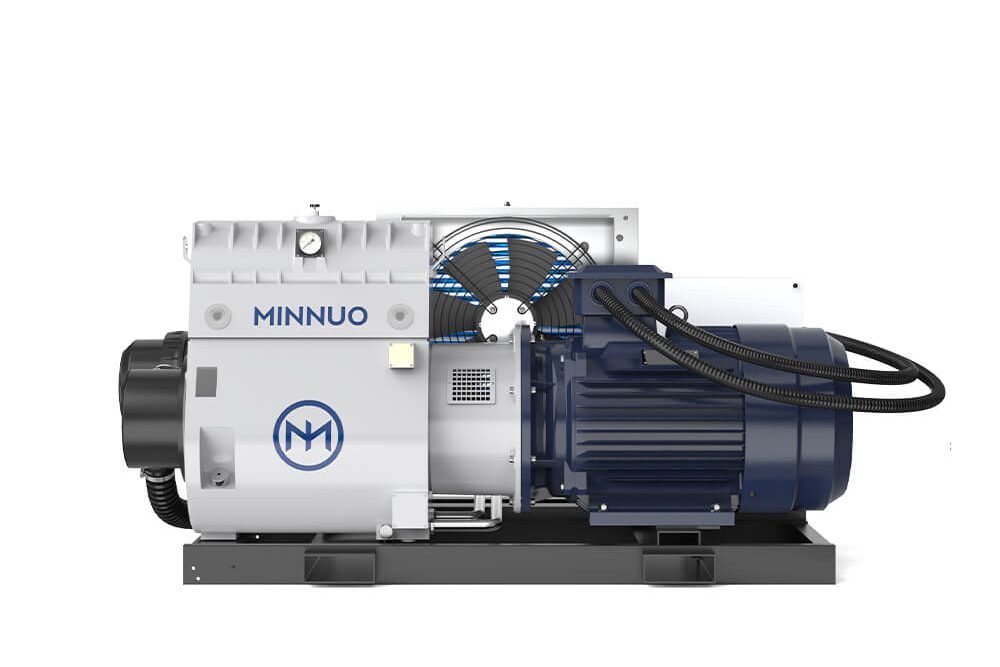
图4MINNUO滑片压缩机
6.项目应用场景及案例研究
6.1 A Middle Eastern Aluminum Smelter:
A large aluminum smelter in the Middle East recently upgraded its existing Mattie compressors to MINNUO’s 90kW sliding vane compressors. The factory’s old system had high operational and maintenance costs and frequent breakdowns. After upgrading to MINNUO compressors, the factory achieved the following results:
初期投资减少30%:与玛蒂相比,MINNUO压缩机性价比更高,为工厂节省大量压缩机采购成本。
Maintenance costs reduced by 25%: MINNUO compressors’ reliable and low-maintenance design significantly reduced downtime and repair expenses.
提高效率:工厂现在拥有更稳定的气压,从而促进铝生产流程更加顺畅并提高生产率。
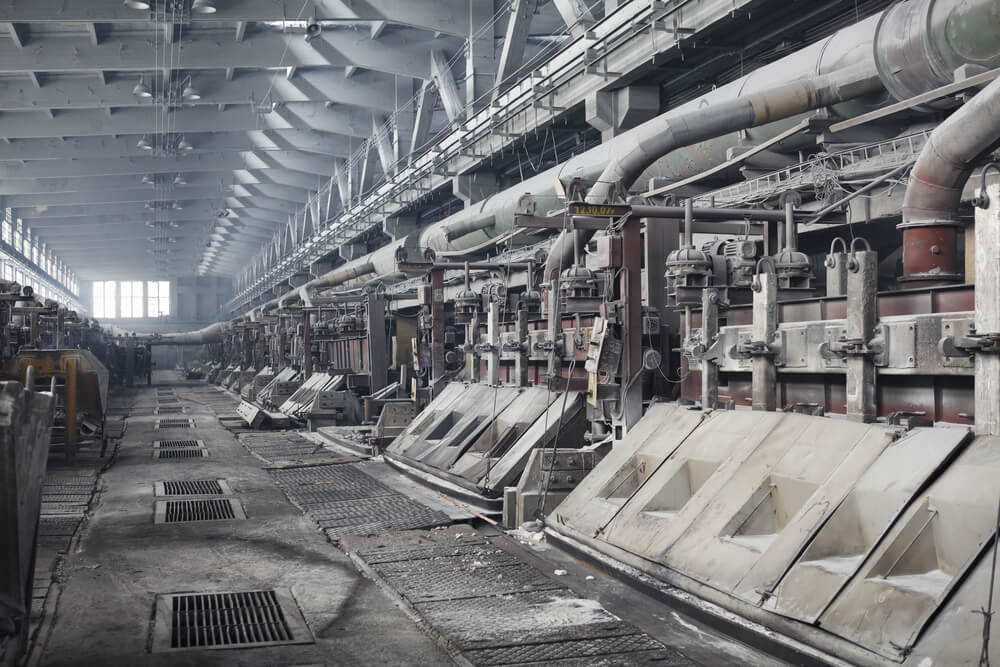
图4:中东一家铝冶炼厂
6.2 A large Russian petrochemical refinery:
俄罗斯一家大型石化炼油厂将其维护成本高昂的压缩机替换为MINNUO型号,以改善其炼油工艺的空气供应。选择MINNUO后,该炼油厂获得了以下优势:
Improved efficiency: By using MINNUO’s energy-efficient compressors, the refinery reduced energy consumption by 20%, thereby saving costs.
Enhanced reliability: The new compressors operate without frequent failures, thereby improving the overall reliability of the plant.
Faster delivery: The refinery also appreciated the shorter delivery time, ensuring minimal disruption during the upgrade.
Customer Feedback:
“Switching to MINNUO compressors not only reduced our operational costs but also improved our overall system efficiency. We noticed a significant increase in reliability and a reduction in maintenance downtime.” — Director of a Middle Eastern aluminum smelter.
“Switching to MINNUO was one of the best decisions our refinery made. These compressors are energy-efficient and high-performing, and the service we received was top-notch.” — —Operations Director of a Russian Petrochemical Refinery.
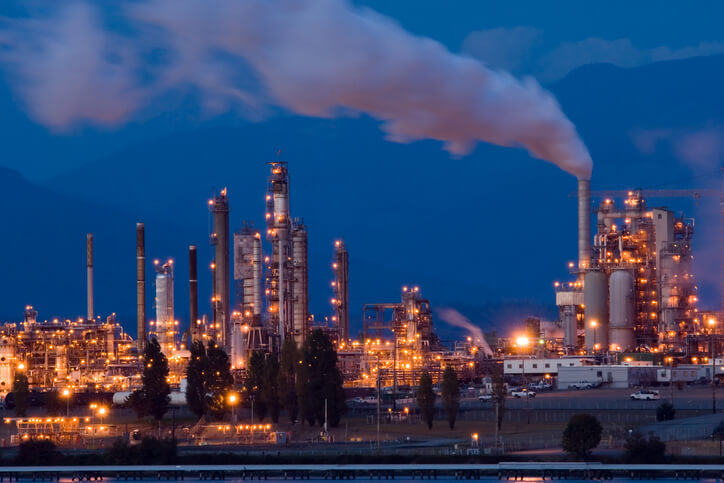
Figure 5: A large Russian refinery
Conclusion
随着全球制造业格局的演变,尤其是在铝工业领域,对经济、可靠、高效的设备的需求空前高涨。像Mattie这样的公司提供的传统压缩机解决方案长期以来占据着市场主导地位。然而,这些压缩机成本的上升和交付周期的延长,正促使铝厂重新考虑其选择。为了应对这些挑战,MINNUO的滑片式压缩机正逐渐成为一种极具竞争力且经济高效的替代方案。
MINNUO has successfully bridged this gap, offering powerful compressors that not only match the performance standards of high-end brands like Mattie but often surpass them, while significantly reducing operational and maintenance costs. With its exceptional local manufacturing capabilities and deep understanding of customer needs, MINNUO can deliver the required performance to global aluminum plants at extremely low costs.
As the industry continues to evolve, MINNUO remains committed to innovation and quality, ensuring it remains a trusted partner for global aluminum plants. The trend toward replacing high-cost brands with MINNUO compressors is growing, not only to save costs but also to ensure operational sustainability, improve efficiency, and contribute to the sustainable development of aluminum production.