As the world moves to low-carbon energy, compressed natural gas (CNG) is becoming an important fuel for vehicles. CNG refueling stations connect gas sources to vehicles, and their design and operations affect energy efficiency. These factors impact the stability of energy systems, both locally and globally. Understanding how these stations work is key to promoting clean energy and improving energy networks.
The three types of CNG refueling stations: standard stations, parent stations, and sub stations.
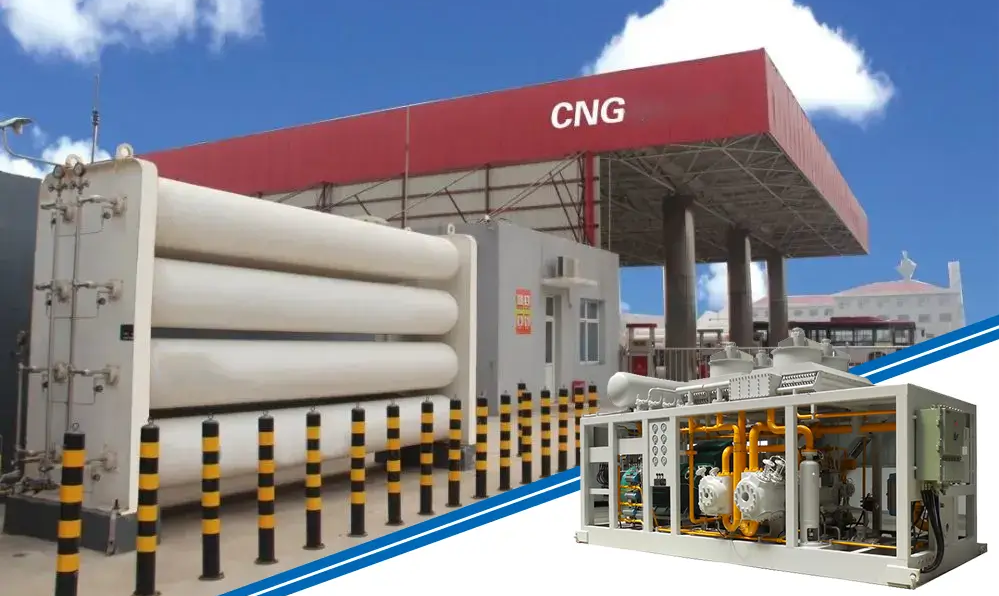
Strategic Value of CNG Refueling Stations
Environmental Perspective
Traditional gasoline vehicle exhaust contains sulfur oxides, nitrogen oxides, particulate matter, and other pollutants, which are major contributors to air pollution, severely harming urban air quality, ecosystems, and public health. CNG, primarily composed of methane, produces primarily carbon dioxide and water as combustion byproducts, resulting in a significant reduction in harmful emissions. Research indicates that global CNG vehicles emit about 90% less carbon monoxide, 70% fewer hydrocarbons, 40% less nitrogen oxides, and almost zero particulate matter compared to gasoline vehicles. This aligns with climate change mitigation efforts and green development goals, offering an effective pathway to improve urban microclimates.
Energy Perspective
Currently, the global energy supply heavily relies on oil imports, making it vulnerable to geopolitical risks that threaten energy stability. Natural gas, however, is abundant and widely distributed. When converted into CNG for transportation, it reduces dependence on oil and enhances energy autonomy. With advancements in natural gas extraction and storage technologies, the development of unconventional gas resources has further strengthened the foundation of the CNG industry. Refueling stations, as the terminal link in the natural gas supply chain, not only expand the market but also promote upstream innovation, improving the energy supply ecosystem and facilitating energy structure optimization.
Core Compression Technology in CNG Refueling Stations
Thermodynamic Principles of Multi-stage Compression
Natural gas is typically in a low-pressure gaseous state under normal conditions, with weak molecular interactions. To meet the high-pressure storage tank requirements of vehicles (typically 20-25 MPa, and higher for some high-performance applications), multi-stage compression technology is widely used in CNG refueling stations. According to the ideal gas law:

where P is pressure, V is volume, γ is the heat capacity ratio, and C is a constant.
As gas enters the compressor cylinder, the piston or impeller does work, drastically reducing the gas volume, causing a sharp increase in pressure and temperature. Each stage of compression is approximately adiabatic. However, real-world conditions are affected by factors such as gas viscosity, heat transfer, and leakage, which create significant deviations from ideal states. Advanced computer simulation technology is required to model these processes accurately, considering various factors and predicting parameter changes during compression to ensure stable and efficient operation of refueling stations under different climatic and geographical conditions.
Compression Heat Management
Uncontrolled temperature rise during compression can lead to a sharp decline in compressor efficiency, lubrication failure, component thermal fatigue, or even accidents. The cooling system is crucial, with air cooling and water cooling being the two main options. Air cooling is simple, easy to maintain, and suitable for small, low-load refueling stations, especially in dry, moderate climates, where natural air convection dissipates heat at a low cost. Water cooling provides stronger heat exchange and precise temperature control, making it suitable for large refueling stations operating under high temperatures and heavy loads. However, it requires more complex systems and high-quality water treatment facilities. Engineers design cooling solutions based on factors like station location, climate, costs, and environmental concerns to ensure that the gas exits the system at an appropriate temperature (usually ≤ 60°C).
Fine Control of Compression Ratio
The compression ratio, defined as the ratio of discharge to intake pressure, is a key performance indicator of compressors. While a higher compression ratio helps increase gas pressure, it imposes higher demands on mechanical structures and sealing performance, potentially leading to component wear, gas leakage, and even the decomposition of gases at high temperatures, affecting CNG quality. Gas source pressures vary globally, with pipeline gas at 0.2-0.4 MPa and long-distance pipeline gas at 2-4 MPa. Engineers, considering local gas sources, target filling pressures, and compressor types (positive displacement or centrifugal), use simulation optimization software to iteratively calculate the best balance between efficiency, lifespan, and gas quality. Positive displacement compressors are commonly used in small or standard stations where intake pressure is low and large pressure increases are needed, while centrifugal compressors dominate in large-scale operations, such as at parent stations.
Detailed Explanation of Three Types of CNG Refueling Stations
Standard Station
Process Flow
Natural gas from the urban pipeline network (0.2-0.4 MPa) enters the station, where it is stabilized by a high-precision pressure regulator to ensure stable compressor intake. It then passes through multiple filters to remove large particles, sub-micron impurities, liquid contaminants, and some sulfur compounds. The purified gas is compressed through 3-4 stages in a reciprocating compressor, cooled by a water-based temperature control system. The CNG is then stored in underground storage tanks or above-ground cylinder groups, and a refueling column is used for rapid fueling of taxis, private cars, etc.
Core Equipment
The pressure regulating unit includes intelligent pressure transmitters and electric valves for remote monitoring and precise adjustment. Reciprocating compressors use high-strength alloy pistons and wear-resistant seals for reliable long-term operation. Underground storage tanks are lined with anti-corrosion coatings and reinforced with high-strength steel wire to withstand pressures over 30 MPa, ensuring safe CNG storage. The refueling column integrates high-precision flow meters, IC card readers, and multiple safety features to ensure accurate fueling and operational safety.
Safety Measures
The standard station is equipped with a highly sensitive leak detection system, placing combustible gas detectors in critical areas. If leakage is detected, alarms are triggered, and gas supply is automatically cut off. Electrical equipment is selected and installed according to explosion-proof standards to prevent electrical sparks from causing explosions. Firefighting equipment and emergency escape routes are planned for efficient emergency response.
Suitable Scenarios
Standard stations rely on the urban pipeline network and are quick to build with relatively low investment. They are densely distributed in global urban areas with high population density and older neighborhoods, providing convenient refueling services for scattered, small vehicles, reducing vehicle idle energy consumption, optimizing urban traffic energy micro-cycles, and improving energy supply efficiency.
Parent Station
Process Flow
The station receives high-pressure gas (2-4 MPa) from long-distance pipelines. Multiple large centrifugal compressors drive the gas through high-speed rotating impellers, converting kinetic energy into pressure. Indirect water cooling, paired with brazed plate heat exchangers, precisely controls the temperature. Part of the produced CNG is stored in large spherical storage tanks, while the remainder is transported to nearby sub stations using high-strength seamless steel tube bundles.
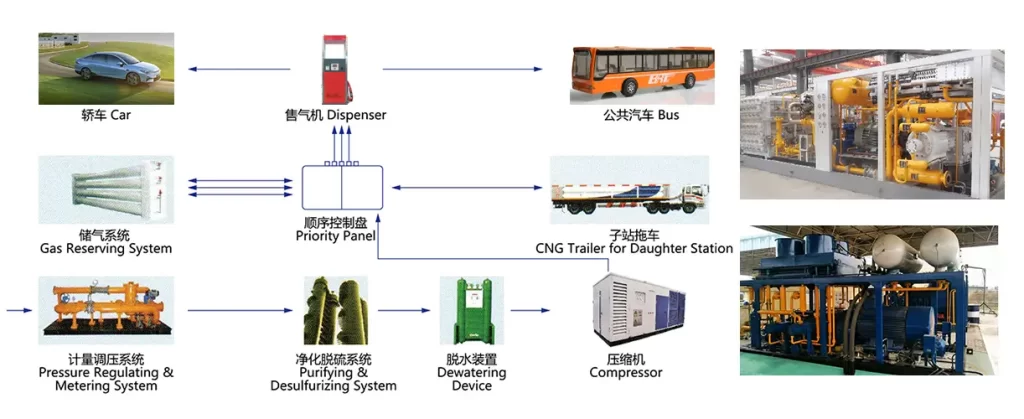
Core Equipment
Centrifugal compressors use high-strength titanium alloy impellers and magnetic bearings to reduce friction and increase efficiency. Spherical storage tanks are equipped with safety valves, liquid level gauges, and anti-corrosion coatings to ensure safety under extreme conditions. Refueling columns are optimized for high flow rates and equipped with automatic shut-off and emergency venting controls to ensure efficient and safe refueling of trailers. Transport trailers are fitted with air suspension and GPS systems for stable and secure transportation, with real-time positioning for precise location tracking.
Safety Measures
As a regional CNG hub, the parent station adheres to stringent safety standards. In addition to regular safety features, the spherical storage tanks have multiple safeguards, such as automatic overpressure relief and precise liquid level monitoring to prevent overfilling. The station is built to international seismic standards, considering geological conditions and using seismic-resistant materials and techniques to maintain facility stability during earthquakes. Rigorous security checks are conducted before trailers depart and return to ensure safe transportation throughout.
Suitable Scenarios
Parent stations leverage local gas sources and large production capacity to serve large vehicle fleets such as buses, sanitation vehicles, and logistics trucks in urban new districts, industrial parks, and transportation hubs. They support large-scale clean energy vehicle operations, driving the construction of sub stations and a regional CNG supply system that promotes the large-scale application of clean energy in the region, contributing to sustainable development.
Sub Station
Process Flow
CNG is unloaded from full-load gas cylinder trailers using a high-precision hydraulic pushing device, which precisely controls the unloading speed and ensures smooth transfer into storage tanks. The gas is heated using electric heaters or hot water heat exchangers to raise the temperature to an optimal range before fueling, preventing vehicle gas cylinders from becoming brittle due to the low temperature of the CNG. The gas is then precisely regulated for vehicle fueling by an intelligent refueling machine, which includes fault diagnosis, remote monitoring, and multiple safety protections.
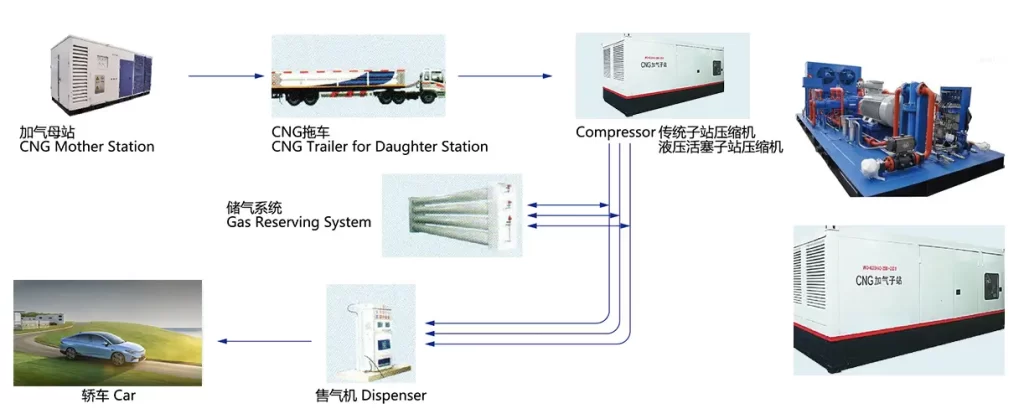
Core Equipment
The tube bundle containers are made from high-strength seamless steel tubes with specially forged joints and metal-wound sealing gaskets, capable of withstanding high-pressure, repeated refueling. The hydraulic pushing device uses servo control for precise force management. Small reciprocating compressors are made from aluminum alloy and feature low-friction pistons to reduce energy consumption and maintenance needs. The heater is equipped with intelligent temperature control and redundant heating elements to ensure stable gas output temperatures under extreme conditions. The refueling machine integrates IoT and mobile payment technologies to improve service quality and operational efficiency.
Safety Measures
Sub stations are equipped with intelligent gas leak monitoring, automatic alarm systems, and fire suppression systems based on air mist or carbon dioxide. Faults or gas leaks in unloading, storage, or refueling processes are immediately detected by sensors, and the system responds with necessary safeguards. Data transmission between components is encrypted to prevent unauthorized access and tampering, ensuring operational confidentiality and security.
Suitable Scenarios
Sub stations are deployed in areas where local demand is concentrated, such as near large transportation terminals or industrial parks. They provide convenient refueling for buses, taxis, and logistics vehicles, acting as important nodes in a larger CNG distribution network, while providing enhanced accessibility and reliable refueling services.
CNG Filling Station Selection Strategy
Geographical Location Factors
In global urban core areas, such as the financial district in London and the Champs-Élysées in Paris, land is scarce, and traffic congestion is high, with frequent, small-volume refueling. Standard stations rely on city gas networks and are located near transportation hubs and vehicle aggregation areas to reduce detours and queues, improve refueling efficiency, reduce empty running energy consumption, ensure timely energy supply, and integrate into urban traffic. In urban outskirts or suburban areas, such as the suburbs of Houston, USA, or outside Munich, Germany, land is ample, and gas networks are sparse, so main stations or sub stations are laid out according to demand. Main stations use their gas source advantage to supply sub stations, which are flexibly located to optimize the regional energy distribution, ensuring clean energy supply for vehicles in remote areas.
Gas Demand Characteristics
In different regions worldwide, large bus fleets and sanitation vehicle fleets, such as the Mumbai bus hub in India or the sanitation vehicle yard in São Paulo, Brazil, require stable, high-flow gas sources, which are supported by main stations or affiliated standard stations. In logistics parks and industrial zones where heavy trucks are concentrated, CNG and LNG refueling stations cater to the fuel needs of different vehicle types. In residential communities where private cars dominate, refueling stations are dispersed, with low traffic, but concentrated during morning and evening peaks. Standard stations or small sub stations use gas storage facilities to store gas during off-peak hours, with smart scheduling to balance peak demand and ensure convenient refueling for residents. In tourist areas, gas demand fluctuates seasonally, with small sub stations deployed in advance for peak seasons and scaled back during the off-season to avoid resource wastage.
Energy Policy Guidance
To promote clean energy, many countries have introduced policies supporting CNG filling stations. In some European countries, large subsidies are given for building new main stations, along with land approval and tax incentives to encourage the development of clean energy transport systems. In some U.S. states, operators receive long-term subsidies based on refueling volumes, helping to stabilize gas prices and make CNG vehicles more economical.
In Singapore, the gas station network is carefully planned based on land and energy needs, with standard stations in neighborhoods, main stations at energy hubs, and sub stations in emerging areas to ensure efficient energy distribution. In China, the “dual carbon” goals are driving the expansion of CNG stations in core regions like Beijing-Tianjin-Hebei, the Yangtze River Delta, and the Guangdong-Hong Kong-Macau Greater Bay Area, promoting collaboration between CNG networks, cities, and industries.
Globally, stricter environmental regulations are driving improvements. The European Union has set tough standards for CNG station emissions and gas quality, pushing for process optimization and equipment upgrades to support green development.
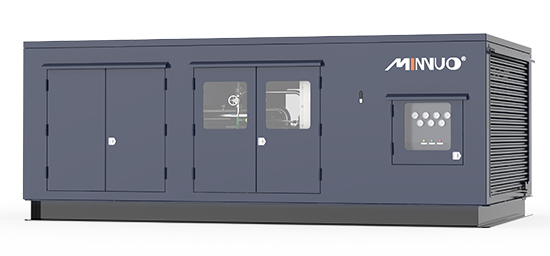
Future Outlook
Empowering with Cutting-Edge Technology
In the future, CNG filling station compressors will incorporate artificial intelligence adaptive control. By using big data from gas sources, environmental conditions, and refueling demands, machine learning algorithms will optimize compression strategies, potentially improving efficiency by 10%-15%. New storage materials, such as Metal-Organic Frameworks (MOFs) and nanoporous carbon, will gradually be commercialized, potentially increasing CNG storage density by 30%-50%, thus reducing construction costs. The Internet of Things (IoT) will enable intelligent monitoring throughout the entire refueling station process, precisely predicting peak and off-peak refueling times, automatically adjusting gas sources and equipment parameters, and realizing unattended self-service refueling. This is expected to reduce labor costs by 30%-40% and improve the user experience.
Cross-Industry Integration
Globally, CNG filling stations will be integrated into renewable energy ecosystems. In areas with abundant sunlight, solar power generation systems will be deployed at filling stations to supply power for internal use or gas production, reducing dependence on the power grid and lowering carbon emissions. In regions rich in wind resources, wind power – CNG synergy will be explored to create low-carbon or even zero-carbon refueling stations. At the same time, mixed refueling of CNG and hydrogen will become a trend, with small-scale hydrogen production and storage trials at existing filling stations, providing emergency hydrogen refueling for hydrogen fuel cell vehicles. As technology matures, the creation of integrated “oil, gas, and hydrogen” energy supply stations will be possible, meeting the diverse energy needs of transportation and contributing to the global energy transition.
Conclusion
In conclusion, CNG refueling stations are key to the global energy shift. They help the environment and improve energy use. With different types of stations for various needs, they are set up efficiently. In the future, new technologies will make them smarter and more efficient, supporting green energy and cleaner transportation.
As a professional manufacturer with over 30 years of experience in the gas compression industry, MINNUO is committed to providing efficient, safe, and cost-effective customized turnkey solutions for CNG gas stations.Welcome to consult!