In compressed air systems, dryers are the core equipment determining the quality of the air source. Residual moisture can lead to issues such as pipe corrosion, valve jamming, and product contamination, directly threatening production safety. As a global leader in compressor brands, this article provides a comprehensive analysis of the technical differences, applicable scenarios, and selection strategies of the refrigerated dryer (cold dryer) and the desiccant dryer (adsorption dryer), helping you avoid selection pitfalls and achieve cost reduction and efficiency improvement.
The refrigerated dryer and the desiccant dryer serve different purposes. Refrigerated dryers cool compressed air to remove moisture with dew points above 3°C, making them ideal for general manufacturing. Desiccant dryers, using adsorbent materials, achieve ultra-low dew points as low as -70°C, suitable for precision electronics and extreme environments. While refrigerated dryers are energy-efficient and cost-effective, desiccant dryers excel in moisture removal but consume more energy and require periodic maintenance.
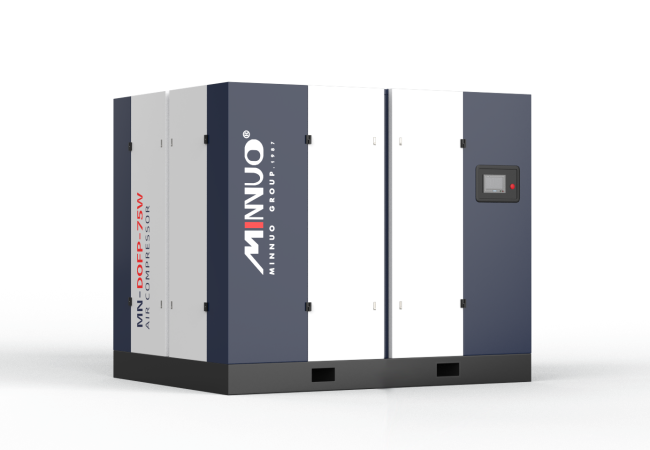
1. Core Principles and Technical Differences of Dryers
1.1 Refrigerated Dryer Working Principle: The Physical Law of Refrigeration and Dehumidification
The refrigerated dryer lowers the temperature of compressed air through a refrigeration cycle system, causing moisture to condense and separate. The core process includes:
- Pre-cooling Stage: High-temperature air (≤80℃) enters the pre-heat exchanger for initial cooling.
- Heat Exchange: The air passes through an air-to-air heat exchanger, exchanging heat with low-temperature dry air to further reduce the temperature.
- Deep Cooling: The air is cooled to 2–10℃ via the evaporator, reaching a saturated moisture state.
- Moisture Condensation: The moisture in the air condenses into water droplets.
- Gas-Liquid Separation: Liquid water is discharged through a cyclone separator and drain valve.
- Air Reheating: Dry air is reheated to ambient temperature ±5℃ to prevent condensation in the pipes.
Technical Features: Relies on the coordinated operation of compressors, condensers, expansion valves, and evaporators, with a dew point stable at 3℃ or higher.
1.2 Desiccant Dryer Working Principle: Molecular-Level Capture by Adsorbents
Desiccant dryers use adsorbents (such as activated alumina or molecular sieves) with porous structures to capture water molecules, typically using a dual-tower alternating operation:
- Adsorption Stage: Wet air enters tower A, where water molecules are locked by the adsorbent.
- Saturation Detection: When the adsorbent in tower A approaches saturation, the system automatically switches.
- Regeneration Stage: Tower B releases the adsorbed moisture through heating or pressure reduction, consuming 6%–15% of the compressed air.
- Recovery Cycle: The adsorbent is regenerated and cooled, ready for the next adsorption cycle.
- Cycle Switching: The two towers switch every 5–10 minutes to ensure continuous air supply.
Technical Features: Capable of achieving dew points as low as -70℃, but requires periodic regeneration with relatively high energy consumption.
2. Comprehensive Comparison of Refrigerated Dryers and Desiccant Dryers
2.1 Performance Parameters Comparison Table
Parameter | Refrigerated Dryer | Desiccant Dryer |
Pressure Dew Point | +3℃ to +10℃ | -20℃ to -70℃ |
Processed Air Flow | 1–500 m³/min | 0.5–200 m³/min |
Energy Consumption Type | Electricity (approx. 3%–5% of system power) | Air consumption (6%–15%) + Electricity |
Sensitivity to Ambient Temperature | High (requires pre-cooling above 35℃) | Low (adaptable to -40℃ to 50℃) |
Initial Investment Cost | Low ($1,400–$2,800) | High ($7,000–$14,000+) |
Annual Maintenance Cost | < $280 | ¥700–¥4,200 (adsorbent replacement) |
2.2 Eight Advantages and Three Limitations of Refrigerated Dryers
Advantages Detailed:
- Outstanding Energy Efficiency: Uses variable frequency refrigeration technology, saving 18% more energy than traditional models.
- Low Maintenance Costs: No need to replace adsorbents, only requiring quarterly cleaning of the drain filter.
- Suitable for General Applications: Ideal for most manufacturing, spraying, food, and pharmaceutical industries.
- Quiet and Eco-Friendly: Operating noise ≤55dB(A), meeting ISO 4871 standards.
Limitations and Solutions:
- Poor Adaptability to High-Temperature Environments? High-temperature models (HT series) can be selected, supporting high-temperature working conditions up to 45℃.
- Dew Point Not Low Enough? A combination of refrigerated dryer + post-filter can be used, which is more cost-effective than a desiccant dryer.
2.3 Five Advantages and Four Pain Points of Desiccant Dryers
Advantages In-Depth Analysis:
- Ultra-Low Dew Point: Can achieve dew points of -40℃ to -70℃, ideal for electronics, semiconductors, and other industries.
- Extreme Environment Stability: Suitable for harsh environments like extreme cold, high heat, and high humidity.
Pain Points and Solutions:
- High Air Consumption Issue: Zero-air-consumption desiccant dryers (ZLD series) use waste heat for regeneration, reducing air consumption to 0%.
- Complicated Adsorbent Replacement? A remote monitoring system provides adsorbent life warnings.
3. Industry Application Scenarios and Selection Formulas
3.1 Industries Best Suited for Refrigerated Dryers
- General Manufacturing: Dew point requirements ≥3℃, recommended refrigerated dryer + three-stage filter.
- High Temperature and Humid Areas: Requires pre-cooling devices.
3.2 Industries Necessitating Desiccant Dryers
- Precision Electronics and Semiconductors: Chip packaging requires a dew point of -40℃, recommended desiccant dryer + CO catalytic filter.
- Low-Temperature Extreme Environments: Arctic research stations and similar conditions.
3.3 Selection Calculation Formula
Actual processed air volume = Compressed air system rated air volume × (Ambient temperature coefficient + Pressure coefficient)
Example:
For a rated air volume of 50m³/min, ambient temperature of 40℃, and working pressure of 0.8MPa, the actual required air volume = 50 × (1.2 + 1.2) = 120m³/min.
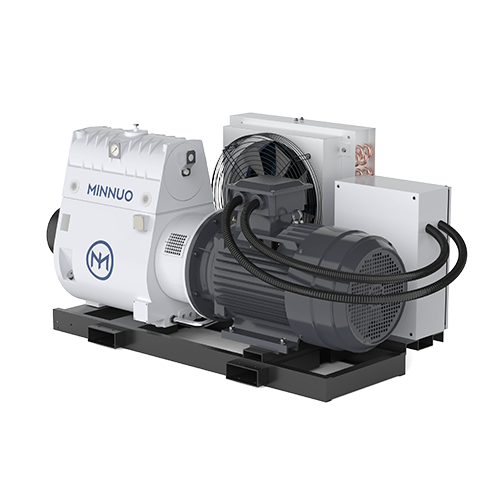
4. MINNUO Innovative Technology: Redefining Drying Efficiency
4.1 Refrigerated Dryer Technological Breakthroughs
- Two-Stage Refrigeration System: Lowers evaporator temperature from 5℃ to -15℃, achieving a dew point as low as -10℃.
- AI Energy-Saving Algorithm: Automatically adjusts refrigeration capacity, reducing energy consumption by an additional 12%.
4.2 Revolutionary Upgrades in Desiccant Dryers
- Composite Adsorbents (Alumina + Molecular Sieve): Extends the life to 8 years, reducing replacement costs by 50%.
- Silent Regeneration Technology: Reduces tower switching noise to 55dB(A).
5. FAQ
Q1: Why does the refrigerant dryer emit water droplets?
A: Possible reasons include insufficient refrigerant, evaporator icing, or clogged drain filter. It is recommended to use an intelligent diagnostic module.
Q2: How to handle desiccant adsorbent poisoning?
A: It is recommended to use a pre-activated carbon filter and choose a pollution-resistant adsorbent.
6. Professional Selection Advice from MINNUO
6.1 Limited Budget + General Requirements → Choose Refrigerated Dryer
Suitable for most manufacturing, spraying, and food industries. High cost-performance and low maintenance.
6.2 Ultra-Low Dew Point + Complex Working Conditions → Choose Desiccant Dryer
Ideal for electronics, semiconductors, extreme cold, or high humidity environments. While energy consumption is high, the dew point remains stable.
6.3 Mixed Requirements → Combination Solution
For applications requiring both low dew point and cost-effectiveness, a combination of refrigerated dryer + post-filter can reduce overall costs.
7. Conclusion
In conclusion, both refrigerated dryers and desiccant dryers have their pros and cons. The selection should be based on specific application scenarios, budget, and dew point requirements. If your needs are for general industrial applications and you are focused on cost-effectiveness, the refrigerated dryer is a more economical choice. For industries with stringent dew point requirements, such as precision sectors, a desiccant dryer will ensure stable air quality.
MINNUO boasts a professional engineering team, and choosing MINNUO means choosing professionalism!