In the field of industrial compressed air, screw air compressors have become the mainstream choice due to their high efficiency and stable performance. However, the design of their drive systems—especially the performance differences between direct drive (gear drive) and belt drive—has long been a focal point of attention. This article provides an in-depth analysis of the advantages and disadvantages of these two drive methods from the perspectives of technical principles, energy consumption, maintenance costs, application scenarios, and more, offering users a scientific basis for decision-making.
There is no absolute superiority between direct drive and belt drive in screw air compressors. The key lies in matching operating conditions and evaluating total lifecycle cost. Direct drive offers a compact structure, suitable for heavy-duty and continuous operations, but it faces disadvantages in unloaded energy consumption, maintenance complexity, and noise control. In contrast, modern belt drives, backed by technological innovation, have demonstrated clear advantages in efficiency, flexibility, ease of maintenance, and TCO (Total Cost of Ownership).
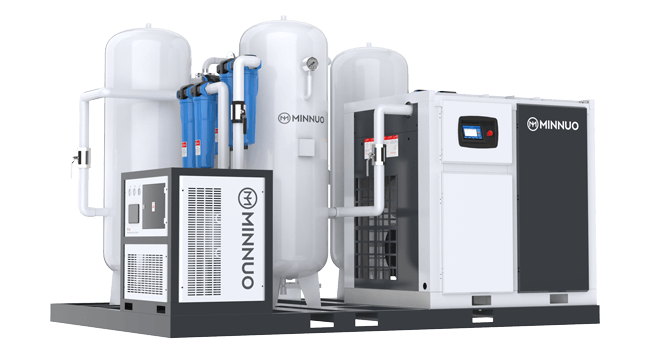
I. Technical Principles and Common Misconceptions of Direct vs. Belt Drive
1.Definition of Direct Drive and Common Misunderstandings
Technical Definition:
Direct drive typically refers to the motor shaft driving the rotor through a coupling or gearbox. However, a widespread industry misunderstanding is that “direct drive” means the motor and rotor are completely coaxial and operate at the same speed. In reality, this idealized form of direct drive is extremely rare in industrial applications.
Truth About Energy Loss:
Some manufacturers claim that “direct drive has no energy loss,” but mechanical friction in the gearbox and couplings inevitably leads to efficiency loss (typically 1%-2%). Therefore, truly lossless transmission does not exist.
2.Technological Advancements and Advantages of Belt Drive
Modern belt drive systems are no longer traditional in design but have achieved high precision and stability through innovation:
- Dynamic tension optimization: Automatic adjustment systems ensure optimal belt tension under varying conditions, extending service life.
- Low starting load: Avoids bearing wear caused by overly tight traditional belt systems, reducing motor load.
- Maintenance-free design: Some high-end models adopt lubrication-free synchronous belts, further reducing maintenance requirements.
II. Direct Drive vs. Belt Drive: 8 Core Performance Comparisons
1.Transmission Efficiency: Similar in Theory, Differentiated by Details
- Gear drive efficiency: High-quality gearboxes can reach 98%-99% efficiency, but wear over time may reduce it.
- Belt drive efficiency: Modern synchronous belt technologies (e.g., polyurethane belts) can also achieve 99% efficiency under ideal conditions.
Key Conclusion: Efficiency differences are more dependent on the precision of manufacturer design and material quality than the transmission method itself.
2.Unloaded Energy Consumption: Belt Drive Performs Significantly Better
- Gear drive drawback: To maintain gearbox lubrication, a minimum pressure of ≥2.5 bar is needed during no-load operation, with some models requiring up to 4 bar.
- Belt drive energy-saving advantage: No-load pressure can be reduced to 0.5 bar, and the rotor’s self-lubricating features reduce extra energy consumption.
Economic Example: A 160kW gear-driven compressor operating 1200 hours annually under no-load (15% load rate) consumes 28,800kWh more electricity than a belt-driven counterpart.
3.Maintenance Cost: Belt Drive Wins Decisively
Hidden costs of gear drive:
- Bearing replacement requires simultaneous gearbox overhaul—time-consuming and expensive.
- Shaft seal maintenance necessitates disassembling the motor and coupling, increasing labor costs.
Convenience of belt drive:
- Pulley replacement only requires simple tools, no alignment needed.
- Modular design allows rotor and motor maintenance independently.
4.Pressure Adaptability: Belt Drive Offers Greater Flexibility
- User customization: If a standard model’s pressure doesn’t meet requirements (e.g., needing to reduce from 13 bar to 11 bar), a belt drive only needs pulley replacement to achieve constant flow with optimized power.
- Gear drive limitation: Pressure adjustments require replacing gear sets or gearboxes—costly and time-consuming.
5.Failure Risk and Safety
- Gear drive chain reaction risk: Oil loss or bearing failure may cause gearbox breakdowns, sharply increasing maintenance costs.
- Isolated design of belt drive: No rigid connection between motor and rotor limits fault range, making the system safer.
6.Noise and Vibration Control
- Gear drive structural drawback: Rigid connection between motor and rotor transmits vibration, resulting in noise levels 3-5dB(A) higher.
- Belt drive shock absorption: The flexible belt absorbs some vibration, making it especially suitable for noise-sensitive environments such as hospitals and laboratories.
7.Service Life and Reliability
- Wear issues of gear drive: Gears running under long-term high loads may suffer from pitting and tooth breakage. The average overhaul cycle is 3-5 years.
- Breakthrough in belt drive lifespan: With carbon fiber-reinforced belts and automatic tensioning systems, service life can exceed 20,000 hours.
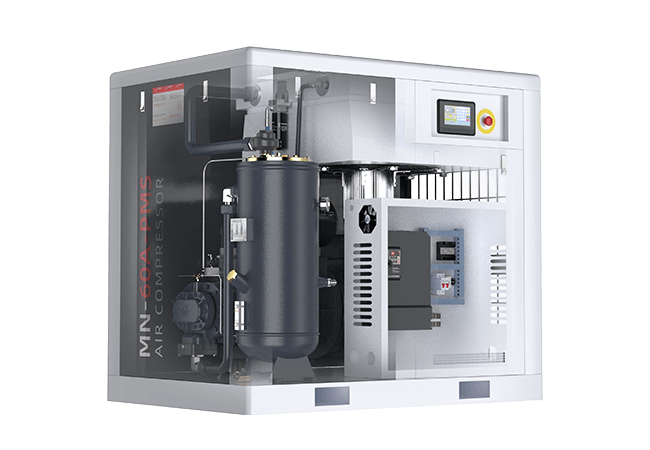
8.Initial Investment and TCO (Total Cost of Ownership)
- Gear drive: Lower initial purchase cost but higher long-term energy and maintenance expenses.
- Belt drive: Slightly higher upfront investment, but combined TCO (energy + maintenance) can be reduced by 15%-25%.
III. Recommended Application Scenarios by Industry
1.When to Prioritize Gear Drive
- Ultra-high power demand (>500kW) and stable continuous loads in heavy industries (e.g., steel smelting).
- Remote areas with space constraints and limited maintenance access (maintenance costs must be considered).
2.Ideal Fields for Belt Drive
- Food and pharmaceutical industries: Require clean environments with low noise and no oil contamination.
- Small to medium-sized enterprises: Emphasize overall energy efficiency and flexible pressure adjustments.
- Multi-shift production: Requires continuous equipment operation and minimal downtime.
IV. MINNUO’s Technological Innovations: Redefining Belt Drive Performance
As a technology leader in the industry, MINNUO has achieved three major breakthroughs in belt drive systems:
- Smart tension control system: Monitors belt status in real-time with sensors, dynamically adjusting tension.
- Nano-composite belt materials: Wear resistance improved by 40%, maintaining elasticity even under extreme temperatures.
- Quick-change module: Patented buckle design reduces belt replacement time to under 10 minutes.
V. User Decision Guide: 4 Steps to Choose the Optimal Solution
- Evaluate load characteristics: Choose gear drive for continuous high loads, belt drive for intermittent operation.
- Calculate lifecycle cost: Include electricity, maintenance, and production loss in hidden costs.
- Define pressure requirements: Will pressure need to be adjusted or capacity expanded in the future?
- Assess supplier’s technical strength: Belt drive performance heavily relies on manufacturer design capabilities.
VI. Conclusion
The competition between direct and belt drive fundamentally reflects a divergence in industrial design philosophy: the former pursues structural simplicity, while the latter emphasizes system flexibility. MINNUO recommends selecting a solution based on actual operating conditions. We provide customized consultation and free energy efficiency assessments to help enterprises maximize the value of their compressed air systems.