As a critical piece of industrial equipment, air compressors have a direct impact on production efficiency and energy consumption. The discharge capacity is one of the core technical parameters of air compressors, determining their gas output capabilities under different working conditions. This article will detail several simple and effective methods to calculate the discharge capacity of air compressors, providing useful references for users, vendors, and manufacturers.
The main methods for calculating the discharge capacity of air compressors include observational, measurement, calculation, and manufacturer data reference methods. The observational method involves estimating the discharge capacity by inspecting the size of the compressor head and its drive system; the measurement method directly measures the discharge capacity using a flow meter, providing precise data; the calculation method estimates the discharge capacity based on known drive power and discharge pressure, suitable for general engineering applications; and the manufacturer data reference method relies on technical data provided by the manufacturer to help users understand the actual discharge capacity of the air compressor.
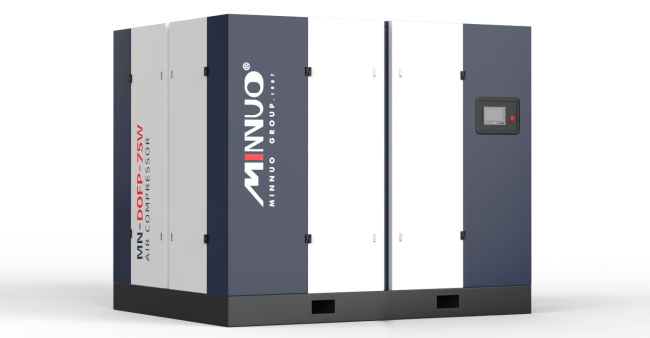
1.The Importance of Air Compressor Discharge Capacity
The discharge capacity of an air compressor refers to the volume of air it can discharge within a given period. It is one of the key indicators of compressor performance. The discharge capacity directly affects the overall efficiency of the air compression system, determining the air supply capability and operating costs. Therefore, accurately measuring and estimating the discharge capacity is crucial for users and vendors.
The discharge capacity, discharge pressure, and drive power of an air compressor are interrelated. For example, even in the simplest air compressors, the discharge pressure is directly displayed via a pressure gauge, and in modern screw compressors, the discharge pressure can also be clearly shown digitally on the PLC screen. The drive power is typically listed on the motor nameplate, though it is not the actual power applied to the compressor head rotor, it provides an initial reference for users. Additionally, the current value can indirectly reflect the shaft power.
However, the discharge capacity is often not directly indicated on the machine. Whether for customers, sales agents, or even some sales managers, lack of knowledge about the discharge capacity can lead to confusion. To assist these individuals in understanding and assessing the discharge capacity, the following simple and reliable methods for calculating the discharge capacity of air compressors will be introduced.
2.Key Factors Influencing Air Compressor Discharge Capacity
Before calculating the discharge capacity, it is important to understand the key factors that affect it. The discharge capacity of an air compressor is not only related to discharge pressure and drive power but also closely tied to the following factors:
2.1Discharge Pressure
Discharge pressure refers to the pressure value of compressed air when it is discharged from the air compressor. It directly determines the energy efficiency and performance of the air compression system. The higher the discharge pressure, the greater the drive power required by the air compressor. Different industrial applications require different discharge pressures, so the impact of discharge pressure must be considered when calculating the discharge capacity.
2.2Air Temperature
Air temperature also affects the discharge capacity. Under the same drive power, lower temperatures can increase the air compressor’s discharge capacity because cooler air increases its density, allowing the compressor to deliver more air within the same volume. In contrast, higher temperatures may reduce the discharge capacity.
2.3Air Humidity
The water vapor content in the air also affects the discharge capacity. In environments with higher humidity, the air’s density increases, leading to a larger mass of air per unit volume, which can cause fluctuations in the discharge capacity. In certain special applications, humidity control becomes a critical factor in accurately measuring the discharge capacity.
2.4Compressor Type and Design
The type and design of the air compressor also influence the discharge capacity. For example, screw compressors and piston compressors differ in structure and working principles, resulting in variations in their discharge capacity calculations and actual gas output. Screw compressors generally provide more stable and efficient discharge capacities, while piston compressors are more suitable for low-load operations.
3.Methods for Calculating Air Compressor Discharge Capacity
After understanding the factors influencing discharge capacity, we can explore several common methods for calculating the discharge capacity of air compressors. Different methods are suitable for different measurement scenarios. Below are some common methods:
3.1Observational Method
The observational method is the simplest and most direct approach. By inspecting the external structure of the air compressor, particularly the size of the compressor head, one can roughly estimate the discharge capacity. Based on the internal mechanisms of the compressor, we know that under the same drive power and discharge pressure conditions, larger compressor heads generally indicate higher discharge capacities and lower noise levels, whereas smaller compressor heads tend to have lower discharge capacities and higher noise levels.
Specifically, if the air compressor uses a 1:1 direct coupling drive (i.e., the head and motor are directly coupled) and has a large head, it usually indicates a higher discharge capacity and lower noise. Additionally, if the head lacks a gearbox, this can confirm it is a genuine large-head compressor. On the other hand, small discharge capacity compressors typically use belts, pulleys, or gearboxes for speed-up transmission, which produces more noise and lower discharge capacity.
This method is simple and effective for initial estimates of discharge capacity, especially for non-professional users, allowing them to quickly get an approximate range for the discharge capacity.
3.2Measurement Method
For more accurate discharge capacity data, the measurement method can be used. This method involves measuring the actual discharge capacity using a flow meter installed at the discharge port of the air compressor. The flow meter provides real-time readings of the discharge capacity in standard units, such as cubic meters per minute. Based on the actual measurements, users can gain a clearer understanding of the compressor’s discharge capabilities, enabling more informed decisions.
The advantage of using a flow meter is the ability to obtain precise discharge capacity data, which is indispensable for applications where discharge capacity needs to be strictly controlled, such as in medical or precision manufacturing fields.
3.3Calculation Method
In the absence of a flow meter, the discharge capacity can be estimated using the calculation method. This method primarily relies on the discharge pressure, drive power, and certain known conventional parameters. A simple calculation formula is provided:

When using this calculation method, it is important to note that different types of air compressors have different efficiency coefficients. For example, screw compressors are generally more efficient, while piston compressors are less efficient. The specific efficiency coefficient can be referenced from the compressor’s product manual or technical data provided by the manufacturer.
Using the calculation method, users can quickly estimate the discharge capacity based on known power and pressure data, even without a flow meter. This method is suitable for most standard industrial environments and provides a reasonable degree of accuracy in discharge capacity estimation.
3.4Manufacturer Data Reference Method
In addition to the above measurement and calculation methods, users can refer to the technical data provided by the air compressor manufacturer. Although the discharge capacity is often not directly indicated on many air compressors, manufacturers usually provide relevant discharge capacity data in product manuals, sales materials, and technical documentation. These data are typically measured under standard testing conditions and have been rigorously validated. For users unsure of the discharge capacity, they can communicate with the manufacturer to obtain technical support and gain a clearer understanding of the actual discharge capacity.
The advantage of the manufacturer data reference method is that the data is reliable and validated, offering users a relatively accurate estimate of the discharge capacity. This is a highly effective reference for users who cannot directly measure or calculate the discharge capacity.
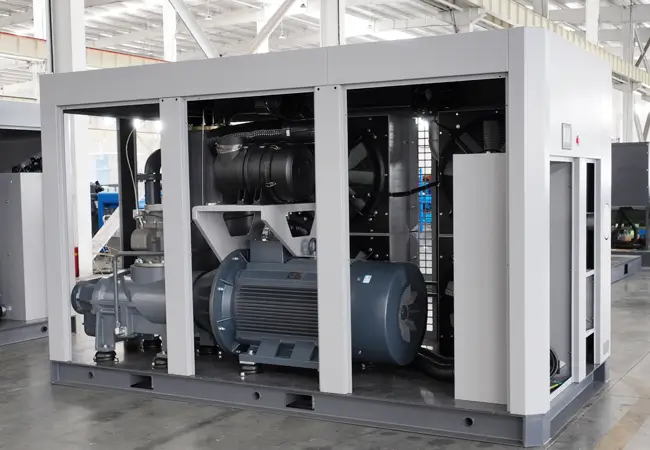
4.Choosing the Right Method for Measurement
In practical applications, selecting the appropriate method for calculating discharge capacity is very important. Different air compressors and usage scenarios may require different methods:
- Simple Initial Estimation: For general users or non-professionals, the observational method is the easiest and most direct way to estimate the discharge capacity range quickly by examining the compressor’s external structure and head size.
- Precise Measurement: For applications requiring precise discharge capacity data, flow meters and the measurement method are the best choice, particularly for high-precision applications in fields such as medical or research industries.
- Engineering Applications and Design: For industrial design or system engineering applications, the calculation method and manufacturer data reference method provide engineers with a theoretical basis and design support, ensuring the rationality and feasibility of system design.
5.Conclusion
The discharge capacity of an air compressor is a critical parameter in evaluating its performance, and accurately understanding it is essential for selecting the right air compressor. The methods outlined above are effective tools for different application scenarios, and users can choose the most suitable method based on their specific needs, providing strong support for selecting and using air compressors.
As a compressor manufacturer, MINNUO has been committed to providing high-quality, stable, and efficient compressor solutions to help customers improve production efficiency and reduce operational costs.