The manufacture of steel and alloys in the metallurgical industry involves complex high-temperature and high-pressure production processes, and reliable and efficient power equipment is the key. As a key equipment for providing compressed air, air compressors play an irreplaceable role in metallurgical processes. From raw material smelting to product packaging, air compressors always provide stable and powerful power support for equipment. This article will comprehensively analyze the application of air compressors in the metallurgical industry, revealing how it empowers steel production through compressed air and provides powerful power for various process flows.
Air compressors play a key role in the metallurgical industry. From high-temperature smelting, steel rolling to cooling and packaging, the compressed air provided by air compressors is indispensable in every production link. With stable and efficient power and energy-saving and environmentally friendly characteristics, air compressors not only improve production efficiency, but also reduce labor and energy costs. With the introduction of intelligent and Internet of Things technologies, air compressors will achieve a higher level of automated management and environmental protection and energy saving in metallurgical processes in the future, injecting new momentum into the innovation and development of the entire industry.
Wide application of air compressors in the metallurgical industry
In the metallurgical industry, the application scenarios of air compressors extend from smelting and steel rolling to dust removal, cooling and product storage. The following are specific application scenarios of air compressors in metallurgical processes
High-temperature smelting and casting processes
High-temperature smelting and casting are key links in the metallurgical industry, and the role of air compressors is mainly reflected in the drive of pneumatic control systems. Through compressed air, air compressors provide stable power support for smelting furnaces and casting molds.
- Pressure regulation: During smelting and casting, air compressors adjust the output pressure of compressed air to ensure that the flow of molten metal stops and avoid the generation of bubbles and defects.
- During the cooling process, the equipment temperature is high, and the air compressor also provides auxiliary support for the cooling system to ensure that the temperature of the smelting furnace is timely regulated.
Precision control in steel rolling production
At the moment of steel rolling, the air compressor is responsible for driving the hydraulic system and pneumatic components to keep the steel rolling equipment running stably and ensure that the shape and thickness of the structure are uniform.
- Pneumatic support: The hydraulic cylinders and pneumatic valves in the rolling mill rely on the stable high-pressure air provided by the air compressor to ensure the smooth operation of the equipment in the rolling process.
- Dynamic feedback: The air compressor system connects to the pressure sensor, enabling real-time monitoring and adjustment of peak values and pressure to accommodate temperature fluctuations and pressure changes during the rolling process.
Gas pipeline and chemical reaction control
The chemical reactions in the metallurgical industry require extremely high oxygen, nitrogen, air pressure and other gases. The air compressor pipes these gases through the compressed air pipeline to ensure the stability of the reaction.
- Pipeline and nitrogen control: The air compressor pipes high-pressure oxygen and nitrogen through the precision pipeline system to ensure precise control of the chemical reaction process.
- Gas: The compressed mixed air output by the air compressor can adjust the gas mixing ratio, ensure the stability of the atmosphere in the reaction area, and effectively improve the safety and consistency of the production process.
Efficient purification: Create a clean production environment
The concentration is extremely high in the metallurgical process. The air compressor provides efficient dust removal function through compressed air, clean production environment and safe operation of equipment.
- Negative pressure suction: Through the negative pressure system, the air compressor will quickly suck into the adsorber, effectively cleaning the factory environment.
- Instant air flushing: The instant high-pressure air provided by the air compressor can quickly blow the surface of the equipment to ensure that there is no dust on the surface of the equipment and reduce equipment loss.
Temperature control of cooling system
The role of the air compressor in the metallurgical cooling system is crucial, providing safe and stable cooling steam for high-temperature equipment to avoid continuous equipment overheating and damage.
- Exhaust gas output: The air compressor controls the cooling exhaust gas control system to achieve precise joints of the equipment and ensure continuous and stable operation of the equipment.
- Real-time temperature control: The air compressor works in tandem with the temperature control system to adjust the intensity and direction of the cooling exhaust, ensuring that the temperature of the production equipment remains consistently within a safe range.
Finished product inspection and resource requirements
In the finished product inspection and storage operations, the pneumatic support provided by the air compressor makes the efficient sorting, loading and storage operations of the product more automated and standardized.
- Automatic support and sorting: Driven by the air compressor, the pneumatic device provides automatic support and sorting upon inspection completion, minimizing manual operations and enhancing efficiency.
- Packaging: The air compressor provides compressed air for the compression box system, and the compression operation achieved by the automatic boxing and sealing equipment improves the total efficiency of the production line.
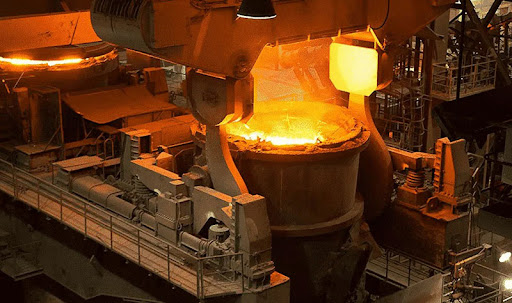
Analysis of the advantages of air compressors in the metallurgical industry
Air compressors are well-known for their efficient and stable power output in the metallurgical industry, providing unparalleled support for every stage of metallurgical production:
Efficient power output and precise control
The high pressure and stable power provided by the air compressor can meet the high temperature requirements of the metallurgical process, especially for processes such as steel rolling and smelting that require extremely high precision and strength.
Energy saving and environmental optimization
Modern air compressors have automatic energy saving and variable frequency speed regulation functions, which can reduce energy consumption and production costs while ensuring power output. In addition, the filtration system of the air compressor reduces the dust content of the factory’s emissions and realizes green and environmentally friendly production.
Improve the level of production automation
The air compressor combined with the intelligent control system can remotely control the pneumatic device to realize automated production, effectively improve the automation level of the metallurgical process, reduce dependence on manual operation, and improve the factory’s production efficiency.
Increase equipment consumption and production safety
The cooling system and dust removal function of the air compressor effectively extend the service life of the equipment and maintain the stability of the equipment. At the same time, through air cooling and filtration, the risk of fire and explosion in the production process is effectively reduced, and the safety of the factory is improved.
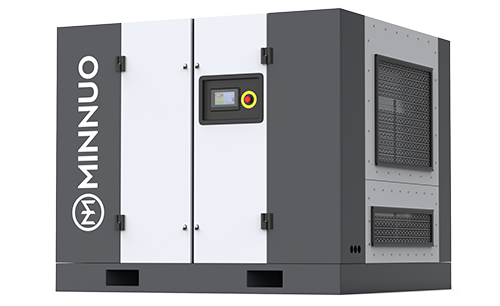
Future development trend of air compressors in the metallurgical industry
With the advancement of standardization and sustainable development concepts, the future application trend of air compressors in the metallurgical industry will be more convincing:
Standardized control and remote monitoring
In the future, manufacturers will combine air compressors with the Internet of Things (IoT) to enable real-time monitoring, automate management, reduce losses from equipment failures, and enhance factory production efficiency and safety.
High-efficiency energy saving and environmentally friendly design
In the future, air compressors will be equipped with more energy-saving technologies, gradually realize waste heat recovery and efficient energy, and further reduce the carbon footprint and energy consumption in metallurgical production.
Noise reduction and anti-seismic technology
In the future, the quietness and anti-seismic performance of air compressors will be improved, making the equipment quieter in high-noise and strong sleep environments. Quieter and more stable air compressors meet the requirements of modern metallurgical industry for equipment comfort and durability.
Conclusion
In the metallurgical industry, air compressors are not only equipment for providing compressed air, but also the core power to ensure the normal operation of the entire production process. Air compressors play an irreplaceable role in every key stage of metallurgical production. Many customers have reported that from high-temperature smelting, steel rolling, cooling, to finished product testing and energy saving, the efficient operation of MINNUO air compressors ensures the stable production and sustainable development of their factories. MINNUO will always adhere to the concept of technology first, continuously improve the standardization and energy conservation and environmental protection of air compressors, and bring new development possibilities to the metallurgical industry.