Air compressors are essential equipment in modern industry, widely used across various sectors such as petrochemicals, metallurgy, and machinery manufacturing. However, after prolonged operation, air compressors often develop oil leaks, leading to reduced efficiency, energy waste, and even environmental pollution. Timely detection and repair of air compressor oil leaks are crucial to ensuring smooth operation. This article provides an in-depth guide on how to efficiently locate oil leaks in air compressors and offers solutions to help resolve this common industrial issue.
Oil leakage from air compressors is a common equipment problem. Timely discovery and repair of the source of oil leakage is essential to ensure stable operation of the equipment. By regularly checking key components such as seals, oil pipes, and oil filters, using leak detection tools, and combining effective repair measures and preventive measures, oil leakage can be effectively reduced, the working efficiency and service life of the air compressor can be improved, maintenance costs can be reduced, and smooth production can be ensured.
Common Causes of Air Compressor Oil Leaks
Air compressor oil leaks can occur for several reasons. Understanding these causes will help diagnose the issue quickly. Here are the main causes of oil leaks in air compressors:
Aging or Damaged Seals
Seals (such as O-rings and oil seals) are key components in preventing oil leaks. The high-temperature and high-pressure environment of air compressors can cause seals to age, crack, or wear out over time. Once seals fail, oil can leak through gaps or joints.
Loose or Damaged Piping Connections
The oil and gas pipelines inside the compressor are responsible for transporting oil. If the connections become loose or the pipes crack, oil and gas will leak. Factors like vibration and temperature fluctuations can cause these connections to loosen or break, leading to leaks.
Faulty Oil Filters or Oil Separators
Oil filters and oil separators play a vital role in the oil and gas system of the compressor. If these components fail, the separation process may be incomplete, causing oil to overflow and leak.
Excessive Oil Level
An overfilled oil level is a common cause of oil leaks. When the oil level is too high, it can cause oil to spill out through exhaust vents or seals because the oil cannot circulate properly.
Cracked or Worn Oil Lines
Oil lines are subject to pressure and friction over time, which may cause them to crack, wear out, or age. Once an oil line breaks, oil and gas will leak through the cracks.
High Temperature or Overload Operation
Operating an air compressor at high temperatures or under overload conditions can increase internal pressure and weaken sealing performance, making oil leaks more likely. Therefore, it’s critical to ensure that equipment operates within the proper load and temperature range.
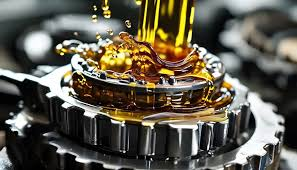
How to Locate Oil Leaks in an Air Compressor
Once an oil leak is detected, the next step is to pinpoint its exact location. Below are some common and effective methods for leak detection:
Visual Inspection
Visual inspection is the simplest and most commonly used method for detecting oil leaks. While the compressor is running, check for oil stains or smudges, especially around seals, pipe connections, and the oil tank. The distribution of the stains can help you identify the potential leak source.
- Pipe Connections: Check oil pipe joints, bolts, and valves for oil stains.
- Seals: Inspect O-rings and oil seals for signs of damage or aging.
- Oil Tank and Oil Filter: Check the connection points between the oil tank and oil filter for stains or leaks.
Using Leak Detection Fluid
Leak detection fluid is a chemical liquid specifically designed to detect oil and gas leaks. Apply it to suspected leak points. If there is a leak, the fluid will form bubbles, pinpointing the leak location. This method is especially useful for detecting small leaks.
Ultraviolet (UV) Detection
Some oils contain fluorescent additives that can be seen under ultraviolet (UV) light. By shining UV light on oil stains, the fluorescent agents become visible, allowing for precise leak detection. This method is effective for small, hard-to-detect leaks, especially inside oil lines.
Sound Detection
In some cases, oil and gas leaks produce specific sounds, such as airflow or gas leak sounds. Using a stethoscope or listening to the operating sounds of the equipment can help you determine the area of the leak.
Oil Level Monitoring
If the oil level drops quickly but no visible oil leak is evident, you can monitor changes in the oil level to determine if a leak is present. Regularly record the oil level, especially after prolonged compressor operation, to spot signs of leakage.
Temperature and Pressure Monitoring
Monitoring the oil temperature and pressure inside the compressor is another effective method for diagnosing leaks. Leaking oil typically results in a drop in oil pressure and temperature fluctuations. Monitoring these parameters can help identify potential leak issues.
How to Repair Air Compressor Oil Leaks
After identifying the leak, prompt repairs are key to resolving the issue. Below are recommended repair measures based on different causes of oil leaks:
Replace Damaged Seals
If the leak is caused by aging or damaged seals, the first step is to shut down the compressor and relieve system pressure. Then, replace the faulty seals, ensuring that the new seals are properly installed to prevent future leaks.
Tighten Loose Pipe Joints
Regularly check all pipe joints to ensure they are securely fastened. If any connections are loose, tighten them promptly. Loose joints are a common cause of oil leaks, so maintenance should not be overlooked.
Replace Faulty Oil Filters or Oil Separators
If the leak is due to a malfunctioning oil filter or oil separator, these components should be replaced immediately. Ensure that high-quality filters and separators are used to ensure proper separation and prevent future leaks.
Adjust Oil Levels
An excessive oil level is one of the most common causes of leaks. Ensure that the oil level is maintained within the recommended range. Regularly check and adjust oil levels as needed to prevent overflow.
Replace Damaged Oil Lines
If oil lines are found to be cracked or worn out, replace them with new ones. Check that the oil lines are properly installed and capable of withstanding the operating pressure of the compressor.
How to Prevent Air Compressor Oil Leaks
To reduce the occurrence of oil leaks, regular maintenance and management are essential. Below are some effective preventive measures:
Regularly Inspect Seals and Oil Lines
Inspect seals, oil lines, and pipe connections regularly to ensure they are in good working condition.
Keep Oil Clean
Regularly replace the oil to avoid contamination, ensuring the oil and gas system remains clean.
Maintain Oil Filters and Oil Separators
Check and replace oil filters and oil separators regularly to ensure effective separation of oil and gas.
Avoid Overload Operation
Avoid operating the compressor beyond its rated capacity or at high temperatures, as this can increase the risk of equipment failure due to overheating or overload.
Monitor Oil Levels and Temperature
Maintain proper oil levels and temperatures to ensure stable operation of the equipment.
Conclusion
Oil leaks in air compressors not only affect equipment performance but can also cause environmental pollution and pose safety risks. Therefore, timely detection and repair of leaks are crucial to maintaining stable operation. Regular inspections, advanced detection tools, and proper maintenance and operation effectively prevent oil leaks, improving the efficiency and longevity of air compressors.
For more information about MINNUO air compressors, stay tuned for updates.