In modern power plant operations, start-up air compressors are essential and indispensable equipment. When selecting the right start-up air compressor, it is necessary to consider various factors, including the type of equipment, compressor performance, and air quality requirements. This article provides a detailed introduction to the working principles, functions, types, and selection considerations for start-up air compressors, and will help you understand how to choose the right start-up air compressor for your power plant.
Starting air compressor plays a key role in power plants. It provides the required starting air for equipment, ensuring smooth startup and stable operation of the equipment. Its main functions include providing starting air, accurately adjusting flow and pressure, reducing mechanical shock, and improving starting efficiency. The working principle of starting air compressor includes four stages: air intake, compression, storage and release. Common types of compressors are piston, screw and centrifugal, each type has its own scope of application and advantages and disadvantages.
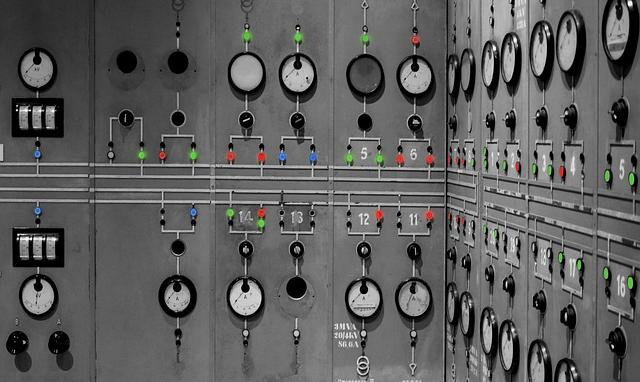
What is a Start-up Air Compressor?
A start-up air compressor is a device that supplies compressed air to critical equipment in a power plant, such as gas turbines, steam turbines, and water pumps, during the start-up process. During start-up, the equipment requires a large volume of high-pressure air to overcome the initial load and reach normal operating conditions. The role of the start-up air compressor is to provide a stable and efficient air supply to ensure that the equipment starts smoothly and quickly, and enters normal operation.
Main Functions of a Start-up Air Compressor
Start-up air compressors play a crucial role in power plants. They not only provide the necessary air for start-up but also optimize the start-up process in several ways:
Providing Start-up Air
The core function of a start-up air compressor is to provide sufficient start-up air for power plant equipment. Large equipment, such as gas turbines and steam turbines, require a significant amount of high-pressure air to drive the equipment and overcome the start-up load. The start-up air compressor ensures the equipment starts smoothly by delivering stable compressed air flow.
Controlling Start-up Speed and Load
The start-up air compressor must not only provide air flow but also regulate the flow and pressure to ensure that the equipment runs at a steady pace during start-up. Too much or too little air could cause start-up failure or equipment damage. By precisely adjusting air flow, the start-up air compressor ensures that the load during the start-up process increases smoothly.
Reducing Mechanical Shock and Extending Equipment Life
Equipment often faces significant mechanical shocks during start-up, particularly when there is a sudden change in rotational speed. The start-up air compressor helps mitigate these shocks by stabilizing air flow, reducing potential load impacts, and preventing excessive wear on internal components, thereby extending equipment life.
Improving Start-up Efficiency
In a power plant, the efficiency of equipment start-up directly affects overall production efficiency. Start-up air compressors reduce the start-up time by providing high-efficiency and stable air supply. This leads to improved overall power generation efficiency, reduced downtime, and ensures the power plant can resume operation quickly and maintain a stable electricity supply.
Working Principles of Start-up Air Compressors
While the working principles of start-up air compressors are relatively straightforward, their role in a power plant is vital. The basic process includes four stages: air intake, compression, storage, and release.
Air Intake
The start-up air compressor begins by drawing in air through the intake valve. This air typically comes from the atmosphere, and the quality of the air significantly impacts the start-up performance. To ensure high-quality air, compressors are often equipped with air filtration systems to prevent contaminants, such as moisture and dust, from entering.
Air Compression
After intake, the air is compressed by mechanical devices such as pistons, screws, or centrifugal mechanisms. The compressed air’s pressure increases, storing energy for use during start-up. This process raises both the pressure and temperature of the air.
Air Storage
The compressed air is stored in air storage tanks. These tanks not only store enough air for use but also help regulate air pressure, preventing fluctuations that could affect the equipment’s start-up.
Air Release and Start-up
When the equipment is ready to start, the stored high-pressure air is released through valves, driving the equipment to start. The start-up air compressor controls the valves to precisely adjust the air flow and pressure, ensuring the equipment starts smoothly and steadily.
Types of Start-up Air Compressors
Depending on the operating principle, application scenario, and equipment requirements, start-up air compressors can be categorized into several types. Each type has its advantages and suitable applications, and power plants must select the most appropriate type based on their specific needs.
Piston Compressors
Piston compressors are one of the most common types of start-up air compressors. They operate by using a piston’s reciprocating motion within a cylinder to compress the air. Piston compressors can provide high air pressure, making them ideal for applications that require high compressed air.
- Advantages: Simple structure, easy maintenance, and capable of providing high-pressure air.
- Disadvantages: High operational noise and potential for wear with frequent starts.
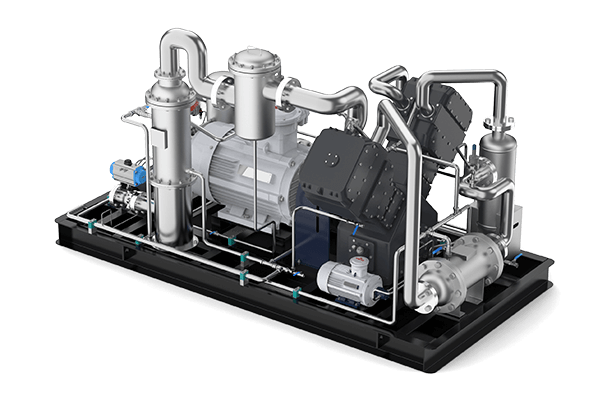
Screw Compressors
Screw compressors compress air using rotating screws, and they generally provide a stable and efficient air flow. Due to their smooth operation and low noise, screw compressors are well-suited for equipment requiring long-term stable operation, such as gas turbines in large power plants.
- Advantages: Smooth operation, high efficiency, and low noise.
- Disadvantages: Higher equipment cost and more demanding maintenance.
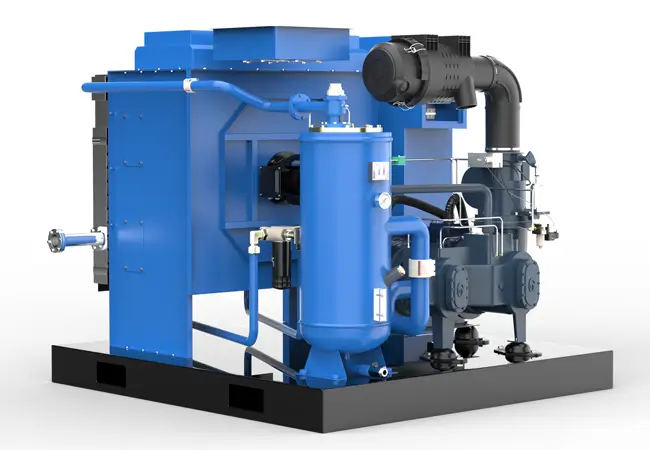
Centrifugal Compressors
Centrifugal compressors accelerate air using high-speed rotating impellers to achieve compression. They are typically used for applications requiring large volumes of air at low pressure, offering high efficiency for large-scale operations.
- Advantages: Suitable for large flow and low-pressure needs, high efficiency, and low energy consumption.
- Disadvantages: Longer start-up times and more complex structures.
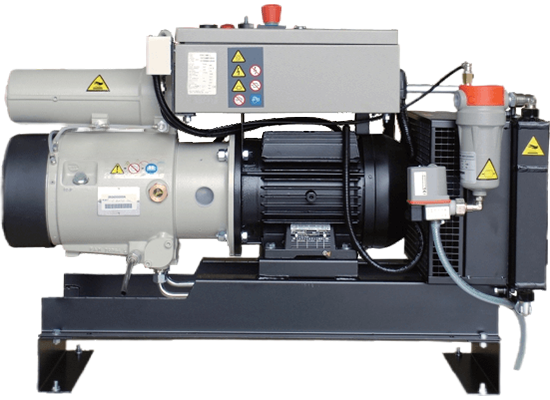
How to Choose the Right Start-up Air Compressor
When selecting a start-up air compressor, several factors need to be considered to ensure that the best equipment for the power plant’s needs is chosen. Here are the key selection factors:
Air Flow and Pressure Requirements
Different types of equipment require different amounts of air for start-up. Large equipment like gas turbines typically requires higher air pressure, while smaller equipment, such as fans, may only need larger air flow. The compressor must deliver the required air flow and pressure for equipment start-up.
Air Quality Requirements
The quality of the start-up air directly affects the equipment’s start-up performance and operational stability. To ensure that air quality is maintained, air treatment systems such as filters, coolers, and dryers should be used to guarantee clean, dry compressed air.
Energy Efficiency and Economic Viability
Energy efficiency is an important consideration when selecting a start-up air compressor. A high-efficiency compressor can reduce energy consumption and operational costs, ultimately lowering the power plant’s overall running costs. Choosing a compressor with good energy efficiency can help businesses save on energy expenses.
Maintenance and Serviceability
The ease of maintenance is a significant consideration in compressor selection. Piston compressors are typically easier to maintain due to their simpler structure, while screw and centrifugal compressors may require more specialized maintenance. It is essential to consider the maintenance costs and frequency of service.
Environmental Adaptability
Environmental conditions such as high temperature, humidity, or altitude can affect the operation of start-up air compressors. In regions with harsh conditions, compressors need to be equipped to handle these challenges. Selecting compressors with good environmental adaptability ensures they can operate normally in various conditions.
Future Development Trends of Start-up Air Compressors
With advancements in technology and stricter environmental regulations, start-up air compressors are continuously evolving. Smart, automated, and highly efficient compressors are becoming the future trend. Intelligent control systems will allow compressors to automatically adjust their operating conditions and optimize performance. Moreover, as environmental regulations tighten, compressors with low noise, low energy consumption, and low emissions will become a critical focus for industry development.
Conclusion
Start-up air compressors play an indispensable role in the operation of power plants, providing essential support for the smooth start-up of equipment. Proper selection and use of start-up air compressors not only improve start-up efficiency but also extend equipment lifespan and reduce maintenance costs. By choosing efficient and reliable start-up air compressors, power plants can ensure high, safe operational performance and provide stable energy supply.
As a professional air compressor manufacturer, MINNUO has a complete range of products. We can provide professional technicians to design the best purchase plan for you to ensure that any of your production needs are met.