Air compressors are indispensable gas supply equipment in industrial production, and their performance, reliability, and energy efficiency directly impact production efficiency and costs. With the advancement of energy-saving policies and the rapid development of industrial automation, inverter technology has become an essential tool for optimizing air compressor performance. MINNUO focuses on developing high-performance air compressors, using Inovance inverters—high-end core components—offering comprehensive gas system solutions.
Selecting efficient, high-performance inverters is key to improving energy savings and stability in the air compressor industry. First, the inverter should have high dynamic response capability to precisely control motor speed in line with load changes. Additionally, advanced control algorithms like sensorless vector control and closed-loop PID control ensure high precision and system stability. Inverters must also have high protection ratings and wide temperature adaptability to withstand complex industrial environments. Leading brands like Inovance stand out for their control performance, reliability, and adaptability, making them the ideal choice for achieving efficient air compressor operation and energy optimization.
Energy-Saving Challenges in the Air Compressor Industry
Air compressors are major energy consumers in the industrial sector, with electricity consumption accounting for about 15% of total industrial power usage. Traditional air compressors often rely on constant frequency control, leading to the following issues:
- Energy Waste: The motor still consumes significant energy during no-load operation, resulting in low efficiency.
- Pressure Fluctuations: Constant frequency control struggles to maintain stable pressure output, affecting process stability.
- High Equipment Wear: Frequent starts and stops cause shocks to the motor and mechanical parts, reducing equipment lifespan.
- High Maintenance Costs: Prolonged high-load operation accelerates equipment wear, increasing repair frequency and maintenance costs.
With the push for energy-saving and environmentally-friendly policies, businesses now seek more than just compressed air; they aim to improve overall performance, including:
- Energy Savings: Upgrading technology to reduce energy consumption and lower operational costs.
- Stable Pressure: Ensuring consistent air supply pressure to avoid production disruptions.
- Intelligent Control: Precisely matching air supply needs, reducing manual intervention, and enhancing automation.
- Equipment Reliability: Extending the service life of equipment and reducing downtime.
The introduction of inverters has become the optimal solution to address these challenges. As core equipment that adjusts motor speed to dynamically match load, inverters offer excellent energy savings and intelligent control, meeting the multi-faceted needs of air compressor users for stable and economical operation.
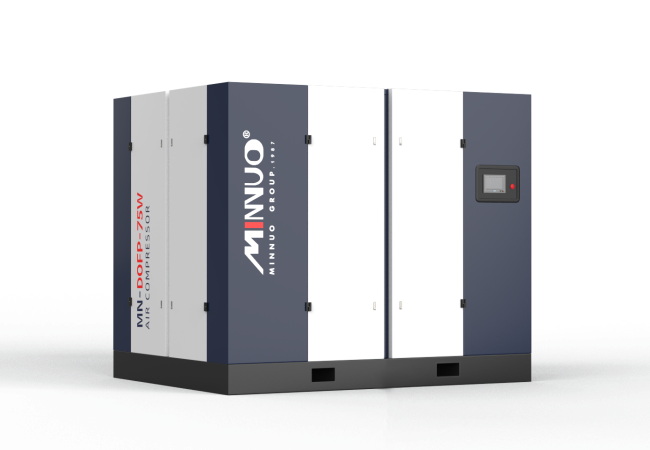
The Principles and Key Considerations for Choosing an Inverter
Inverter Control Principles
Inverters adjust the motor’s frequency and voltage to dynamically match air demand, optimizing air compressor operation and overcoming many of the drawbacks of traditional constant frequency models. The main functions include:
- Dynamic Adjustment Capability: Inverters can adjust motor speed in real time according to air demand, precisely controlling exhaust volume. By adjusting motor frequency in real-time, they also ensure constant pressure output.
- Reduced Energy Consumption: By adjusting motor power according to actual load, inverter control avoids no-load waste, significantly improving energy efficiency.
- Reduced Shock: Inverters feature soft start functionality, ensuring a smooth startup process and reducing shocks to motors and mechanical parts.
- Extended Service Life: Reducing mechanical part wear and improving equipment reliability.
How to Choose the Right Inverter
Not all inverters meet the complex operational needs of air compressors. When selecting, focus on the following four key factors:
Matching the Operating Characteristics of Air Compressors
Air compressors experience frequent load fluctuations and quick start/stop cycles. The inverter should have:
- High Dynamic Response: Able to respond quickly to pressure changes and adjust motor speed precisely.
- Wide Frequency Range: Capable of handling air compressors’ operations from low-speed no-load to high-speed full-load conditions.
Advanced Control Algorithms
High-quality inverters should feature the following technologies:
- Sensorless Vector Control (SVC): Achieves precise speed and torque control without the need for encoders.
- Closed-loop PID Control: Real-time pressure signal acquisition and comparison with set values to maintain stable pressure.
Environmental Adaptability
Inverters must be able to withstand the complexities of industrial environments, with:
- High Protection Rating (IP54 or higher): Strong dust and water resistance.
- Wide Temperature Range: Reliable operation in environments ranging from -10°C to 50°C.
Stability and Lifespan
Inverter stability directly affects the air compressor’s operational reliability. High-quality inverters not only reduce failure rates but also extend the overall equipment lifespan.
High-End vs. Low-End Inverters: Current Status and Differences
There is a wide variety of inverter brands in the market, with notable differences in performance, stability, and adaptability. Inverters can generally be divided into high-end and low-end categories based on brand reputation and technology level. High-end inverters include globally recognized brands like ABB, Inovance, and Siemens, which offer advanced technologies, outstanding performance, and strong environmental adaptability. Low-end inverters, mostly from second- and third-tier brands, have a price advantage but are less suited for high-demand environments. Here’s a comparison:
Feature | High-End Inverter | Low-End Inverter |
---|---|---|
Technology | High-precision vector control, closed-loop algorithms | Basic V/F control, lower precision |
Response Speed | Response time <20ms, adapts to complex loads | Slower response, struggles with load fluctuations |
Operational Stability | Stable, handles high temperature and humidity environments | Poor stability, prone to faults in changing conditions |
Suitable Scenarios | Large and medium-sized compressors, harsh industrial environments | Small compressors, low-demand environments |
Initial Cost | Higher | Lower |
Long-Term Cost | Low failure rate, low maintenance, low total cost | Frequent failures, high maintenance, high total cost |
While high-end inverters have a higher initial cost, their superior performance and reliability significantly reduce long-term operating costs, making them ideal for complex industrial environments. Low-end inverters are better suited for small businesses with lower performance requirements but fall short in high-load applications. Therefore, choosing the right inverter, particularly a high-end product like Inovance, is critical to achieving energy optimization and long-term economic benefits in air compressors.
Why We Choose Inovance Inverters
Inovance inverters, as a top-tier international brand specializing in industrial automation control, align with MINNUO’s philosophy of manufacturing high-quality products. We chose Inovance for the following unique technical advantages:
Outstanding Control Performance
- Sensorless Vector Control (SVC): Achieves high-precision speed and torque control without encoders, reducing hardware costs.
- Encoder-based Vector Control (FVC): Dynamic response time <20ms, quickly adapts to changes in air supply demand.
- Adaptive Algorithm: Automatically adjusts output according to real-time load, ensuring optimal equipment efficiency.
High Reliability and Environmental Adaptability
- Electromagnetic Compatibility (EMC): Built-in filters effectively suppress electromagnetic interference.
- Wide Temperature Range: Reliable operation between -10°C and 50°C.
- High Protection Rating: IP65-rated housing, excellent dust and water resistance, suitable for harsh industrial environments.
Significant Energy-Saving Effects
Inovance inverters reduce energy consumption by dynamically adjusting motor speed, achieving energy savings of 30%-50% compared to traditional constant frequency control.
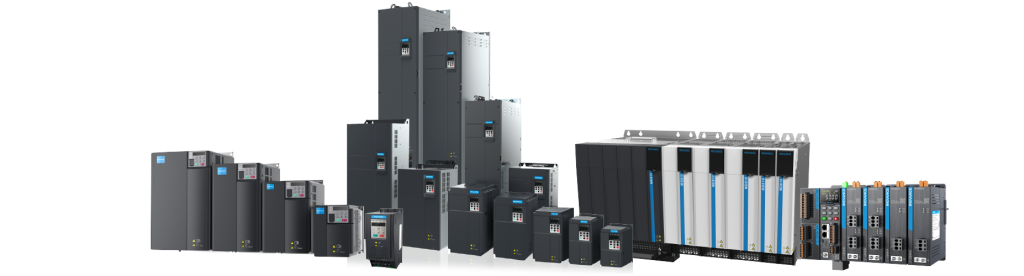
Core Advantages of Our Air Compressors in the Industry
By leveraging the technical advantages of Inovance inverters and combining them with our rich experience and expertise in air compressor manufacturing, we have created a series of high-performance products. Here are some of the technical highlights and core advantages of our air compressors compared to other products:
Precise Air Output Control
- Closed-Loop Control System: Pressure sensors and inverters work together in real time, keeping pressure fluctuations within ±0.5%.
- Fast Response: The inverter’s dynamic adjustment capabilities allow our air compressors to meet frequent fluctuations in air demand during production.
Energy-Saving Technology
- Minimal No-Load Loss: Traditional air compressors waste energy during no-load operation, whereas inverter control adjusts speed based on actual demand, significantly reducing no-load energy consumption.
- Optimized Efficiency: Our air compressors, combined with Inovance inverters and high-efficiency permanent magnet synchronous motors, maintain high energy efficiency under various loads, boosting energy savings by over 30%.
High Reliability and Long Service Life
- Protective Design: Corrosion-resistant coatings, independent air ducts, and fully enclosed structures enhance environmental adaptability.
- Self-Protection Features: The inverter integrates overload protection, overheat protection, and short-circuit protection, reducing the risk of equipment damage.
Professional Gas System Design
- Multi-Unit Control System: Coordinating multiple compressors for dynamic load distribution and energy optimization.
- Intelligent Monitoring Platform: Equipped with IoT remote monitoring, enabling real-time equipment status checks and predictive maintenance.
Comparison with Other Market Air Compressors
To better showcase our competitive edge, here’s a comparison of our air compressors with other products on the market:
Comparison Item | Our Air Compressor | Traditional Air Compressor | Standard Inverter Air Compressor |
---|---|---|---|
Control Precision | ±1% pressure fluctuation | > ±5% | ~ ±3% |
Energy Savings | >30% energy savings | No energy optimization | 15%-20% energy savings |
Stability | High protection rating, stable operation | Frequent load/unload, prone to damage | Poor interference resistance |
Environment | Suitable for high temperature, dust, and other harsh environments | Poor adaptability | Standard industrial environments |
Service Life | Long life, average lifespan >15 years | 8-10 years | Standard life, unstable |
Service Support | Full-process, customized service | Inadequate after-sales support | Limited service, slow response |
Conclusion
As a manufacturer of high-end air compressors and a leader in optimizing gas systems, MINNUO is committed to driving industry progress through technology. We offer efficient, energy-saving, and intelligent air compression systems, helping customers improve production efficiency while reducing operating costs.
Choosing MINNUO air compressors means selecting a combination of advanced technology and exceptional performance—a step toward a more sustainable and economical future for industrial production. Feel free to contact us for consultation!