Clean energy solutions, especially green hydrogen and carbon capture technologies, are increasingly taking center stage in the global transition toward sustainable energy. These technologies aim to reduce carbon emissions, promote energy storage, and support net-zero targets.
In both green hydrogen production and carbon capture, gas compressors play a critical role in facilitating energy-efficient and sustainable operations. From high-pressure gas storage to efficient transport and conversion, compressors are indispensable for the smooth functioning of these systems.
This blog will explore the innovative ways in which gas compressors support these groundbreaking clean energy projects, and why selecting the right compressor is crucial for maximizing system efficiency, minimizing operational costs, and achieving sustainability goals.
1.Green Hydrogen Production: How Gas Compressors Enable Efficiency and Safety
What Is Green Hydrogen?
Green hydrogen, a clean energy source produced through the electrolysis of water using renewable electricity, is gaining prominence as a sustainable fuel for decarbonizing hard-to-abate sectors. It is considered a cornerstone in clean energy systems due to its ability to store excess renewable energy and reduce carbon emissions in industries such as transportation, energy storage, and industrial applications.
The Role of Compressors in Green Hydrogen Projects
Compression of Hydrogen Gas:
One of the most critical tasks for compressors in hydrogen projects is raising the hydrogen gas pressure to facilitate safe storage and transportation. Since hydrogen gas has a very low density, compression is essential to increase its volume, making storage and transport more feasible.
Gas compressors designed for hydrogen applications must accommodate the high pressure required (often 700 bar or more) for efficient transportation and ensure the safe handling of this flammable gas.
Storage Solutions:
Hydrogen’s high volatility demands safe, high-pressure storage solutions. Compressors not only pressurize hydrogen for transport but are integral to the storage systems that safely contain this gas under pressure, making it ideal for large-scale, mobile applications like fuel cell vehicles or industrial hydrogen storage tanks.
Maintaining Purity:
Maintaining hydrogen purity is paramount in green hydrogen applications. Compressors in these systems must be oil-free to prevent contamination, ensuring the hydrogen maintains its purity and meets critical industry standards such as ISO 14687 for hydrogen quality. This is particularly important when hydrogen is used for fuel cells, where any contaminants can damage sensitive components and reduce system efficiency.
Innovative Compressor Features for Green Hydrogen:
Energy Efficiency:
With the high energy costs associated with hydrogen production, selecting energy-efficient compressors is vital. Compressors with integrated variable-speed drives (VSD) are ideal for this purpose as they can adjust output based on demand, reducing overall energy consumption and optimizing the overall cost of hydrogen production.
Hydrogen Compatibility:
Modern compressors used in green hydrogen applications are designed with specialized materials that can handle hydrogen, which has a tendency to embrittle metals over time. Compressors need to be equipped with hydrogen-compatible seals, corrosion-resistant materials, and bearings capable of handling the aggressive nature of hydrogen while maintaining operational integrity.
Durability and Low Maintenance:
Hydrogen compressors must not only be highly durable, but they also need to operate efficiently under challenging environmental conditions. To ensure long-term performance, compressors designed for green hydrogen applications are built with low-maintenance features that reduce downtime and repair costs. Seals and components resistant to hydrogen embrittlement and corrosion are a must for reliable operation.
Customer Tip:
When selecting a compressor for green hydrogen projects, it’s important to consider the specific needs of the hydrogen system. Ensure that the compressor you choose is tailored for handling hydrogen, with hydrogen-compatible seals, corrosion-resistant materials, and low-maintenance features. Selecting the right compressor ensures not only operational efficiency but also long-term savings and safety in hydrogen production systems.
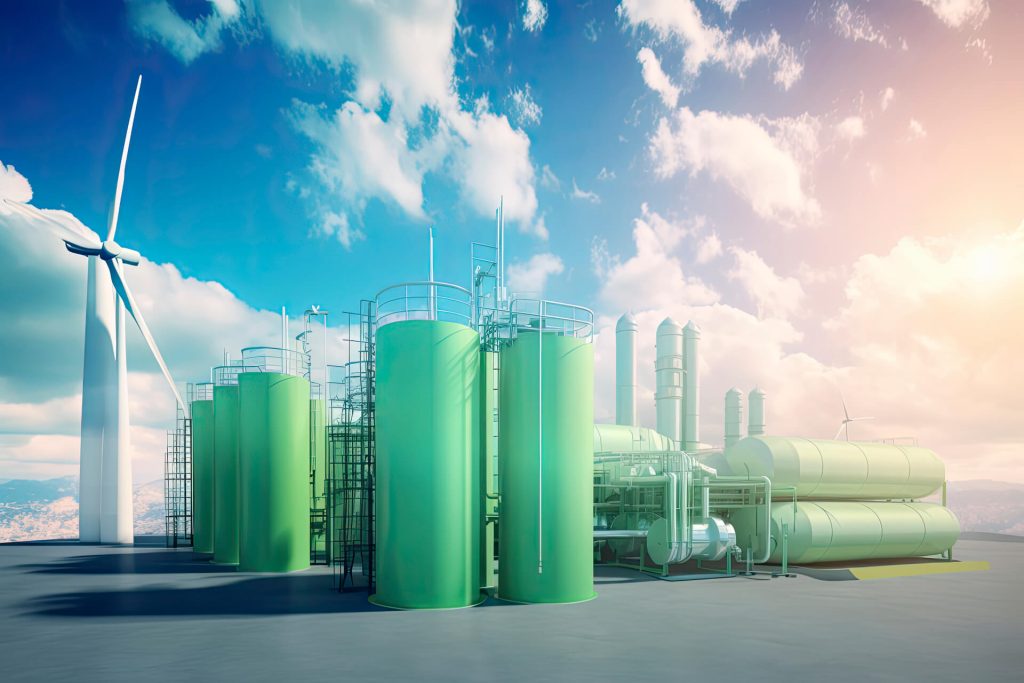
2. Carbon Capture and Storage (CCS): How Gas Compressors Facilitate Emission Reduction
What Is Carbon Capture?
Carbon capture is a crucial technology for mitigating climate change. It involves capturing carbon dioxide (CO₂) emissions from sources like power plants or industrial processes and safely storing or reusing it to prevent its release into the atmosphere. This process plays a key role in reducing the global carbon footprint.
Compressors in Carbon Capture
Compression of CO₂:
Role: Compressors are central to the process of capturing and compressing CO₂ from flue gases. They must be robust enough to handle high-pressure CO₂, which ensures that the gas can be effectively transported or stored.
Key Consideration: The compressor must be able to operate efficiently under high pressures while ensuring that the CO₂ is in a state suitable for storage or transportation.
Efficient Storage:
Importance of High-Pressure Storage: Compressors help store CO₂ in pipelines or underground reservoirs, providing an effective solution for long-term carbon storage. The storage of CO₂ under pressure in geological formations is an important part of reducing emissions.
Application Tip: Ensure that the compressors used for storage have high reliability and can handle the specific pressure requirements for CO₂ storage systems, such as in depleted oil fields or saline aquifers.
Preventing Leaks:
Sealing and Safety: Given that CO₂ is stored under high pressure, it’s crucial to prevent leaks. High-pressure compressors are needed to ensure that CO₂ is stored safely without leaks, maintaining the integrity of the entire CCS process.
Customer Tip: Choose compressors equipped with superior sealing mechanisms, which will help maintain the integrity of CO₂ storage systems and prevent any potential environmental risk associated with CO₂ leaks.
Innovative Features for CCS Projects
Durable and Corrosion-Resistant Compressors:
Corrosion Resistance: Specialized compressors for CCS applications are designed with corrosion-resistant materials to cope with the aggressive nature of CO₂. These compressors help ensure long-term reliability and minimize downtime associated with maintenance or failure due to corrosive elements.
Material Tip: Consider compressors made with stainless steel or coatings that protect against corrosion, ensuring durability and operational longevity even in harsh conditions like those encountered in CCS projects.
Energy-Saving Solutions:
Energy Efficiency: Compressing CO₂ is an energy-intensive process. To make the process more cost-effective, compressors integrated with Variable Speed Drive (VSD) technology can adjust their energy usage based on the demand, thereby significantly reducing overall energy costs.
Pro Tip: Look for compressors with VSD technology to reduce energy consumption during CO₂ compression, which is particularly important for large-scale carbon capture projects.
3. Key Challenges in Clean Energy Projects — and How the Right Compressor Solves Them
Clean energy initiatives like green hydrogen production and carbon capture are booming — but they also come with tough engineering challenges. For many customers entering these emerging fields, gas compression is not just a supporting role, but a core enabler. Here’s how choosing the right compressor can make or break your project’s success.
Green Hydrogen: Compression Isn’t Optional — It’s Critical
Challenge: Hydrogen Storage and Transport
Hydrogen must be compressed to extremely high pressures (often >350 bar) to be stored or delivered in practical volumes. The challenge? Hydrogen is the lightest and smallest molecule on earth — meaning leakage risks, energy consumption, and safety concerns are all magnified.
✅ Solution:
Investing in oil-free, high-pressure compressors with hydrogen-grade sealing systems significantly reduces leakage risks and improves delivery efficiency. Variable speed drives also allow users to optimize energy use during intermittent hydrogen production cycles (e.g. electrolysis based on renewable energy availability).
Example: A Nordic electrolyzer company reduced 22% energy loss in storage transitions by switching to a screw-type hydrogen compressor with automatic unloading.
Challenge: Purity and Contamination Control
Hydrogen fuel cell systems demand >99.999% gas purity. Traditional lubricated compressors pose a contamination risk — even tiny traces of oil or moisture can poison catalysts in downstream systems.
✅ Solution:
Dry-running or diaphragm-type compressors offer contact-free compression, eliminating hydrocarbon contamination. Integrated filters and dryers tailored for hydrogen ensure compliance with stringent purity standards.
Carbon Capture: Not Just Compression — It’s About Containment
Challenge: CO₂ Compression & Transport Efficiency
Captured CO₂ often needs to be compressed to 100+ bar for pipeline injection or storage. However, compressing large volumes of CO₂ consumes significant energy and causes wear on unoptimized equipment.
✅ Solution:
Energy recovery systems, intercooling stages, and advanced rotor designs can cut electricity consumption by up to 30%. Additionally, compressors with low compression ratios per stage and high volumetric efficiency reduce maintenance costs in long-term CCS projects.
Challenge: Leakage Risks and System Reliability
CO₂ leakage is more than a nuisance — it directly affects carbon accounting, violates environmental regulations, and can result in dangerous workplace conditions.
✅ Solution:
Advanced sealing technologies like dry gas seals or tandem seals, combined with real-time pressure monitoring, can detect and prevent microleaks. Some industrial compressors even include auto-shutdown protocols when irregular pressure drops occur.
Customer Insight: A Middle East energy contractor integrated leak-proof booster compressors into their CCS pipeline network and avoided over $250,000/year in CO₂ loss penalties.
Why the Right Compressor Isn’t Just Equipment — It’s Project Insurance
Optimized Efficiency Built-In
Compressors designed with high-efficiency motors, intelligent control systems, and modular expandability help operators reduce costs and scale operations as demand grows. Whether hydrogen output varies by time-of-day or CO₂ flows fluctuate seasonally, intelligent load-matching saves real money.
Engineered for Longevity and Harsh Environments
From desert-based solar hydrogen plants to offshore CCS rigs, environmental stress can shorten equipment life. Choosing compressors with corrosion-resistant alloys, vibration-isolated bases, and low-maintenance configurations protects your CAPEX investment.
Safety and Compliance as a Standard, Not an Upgrade
Top-tier compressors come pre-certified for ATEX, PED, and ISO 8573 standards — saving months of regulatory delay. They also support SCADA or cloud integration, helping plant managers monitor pressure, vibration, and leak risks remotely in real time.
✅ Final Takeaway for Buyers
If you’re scaling into green hydrogen or CCS, don’t treat the compressor as an afterthought. It’s the heart of your gas flow — and the brain of your cost control. The right compressor partner will offer more than a machine: they’ll bring you pressure maps, material compatibility checks, purity calculators, and long-term energy audits.
“We thought we were just buying a compressor — what we got was a roadmap to optimize our whole hydrogen storage system.”
— CTO, European CleanTech Startup
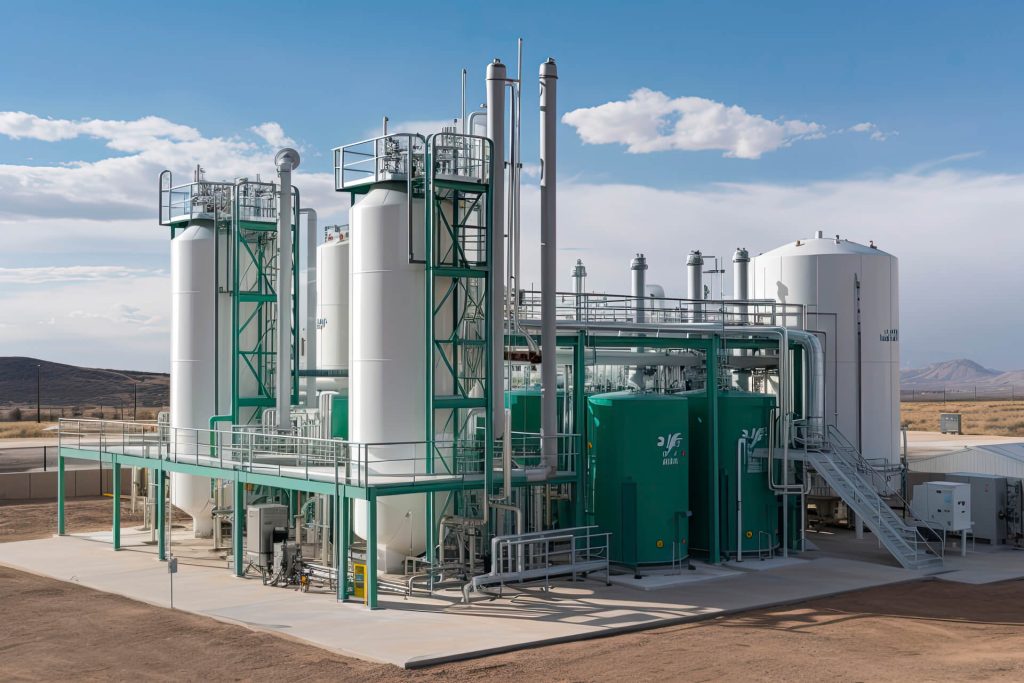
4. How to Choose the Right Compressor for Clean Energy Projects
Choosing the right compressor is not just about matching pressure ratings—it’s about securing long-term performance, safety, and efficiency tailored to the specific demands of clean energy systems. Here’s how to make a smart, informed decision:
1. Understand Your Operational Needs
Every clean energy project is unique—so your compressor should be too. Begin by assessing your actual process parameters, including:
Required pressure and flow rate: For green hydrogen production, this often involves ultra-high pressures up to 1000 bar. Choose a compressor with a proven track record in such ranges to avoid system strain or failure.
Purity and contamination sensitivity: Hydrogen fuel cell applications are extremely sensitive to impurities. Select oil-free compressors or units with integrated filtration systems to meet purity standards (typically 99.999% or higher).
Environmental and safety considerations: Hydrogen is explosive and CO₂ is corrosive. Your compressor must be compatible with ATEX or explosion-proof standards for hydrogen, and corrosion-resistant materials (e.g., stainless steel seals and valves) for CO₂ applications.
Pro Tip: Don’t assume a general-purpose compressor can adapt to clean energy needs. Ask your supplier for detailed case studies in similar applications.
2. Prioritize Energy Efficiency
In projects where margins are tight and energy costs are significant, energy efficiency isn’t a luxury—it’s a necessity.
Look for VSD (Variable Speed Drive): VSD allows compressors to adjust output based on real-time demand, minimizing wasted energy during low-load conditions.
Integrated heat recovery systems: Some high-efficiency compressors allow captured waste heat to be reused in nearby processes—ideal for facilities aiming for net-zero operations.
Energy usage transparency: Choose models with built-in energy monitoring systems. This allows you to track kWh/m³ compressed and identify cost-saving opportunities over time.
Quick Win: Opt for ISO 1217-certified performance data to ensure energy savings aren’t just theoretical.
3. Evaluate After-Sales Support & Lifecycle Planning
Many project delays and losses stem not from equipment failure—but from poor response times or lack of service support.
Global parts availability: Especially for international clean energy projects, ensure spare parts and technical expertise are available locally or with rapid logistics support.
Remote diagnostics and predictive maintenance: Modern compressors equipped with IIoT sensors can detect abnormal vibrations, wear, or overheating early, reducing unplanned downtime.
Extended service contracts: Ask if the supplier offers service agreements with periodic inspections, oil analysis, or compressor overhaul planning.
Case Insight: A hydrogen project in Germany saw a 20% reduction in downtime after switching to a supplier with cloud-based compressor diagnostics.
4. Compliance with Clean Energy Standards
Last but not least, verify whether the compressor complies with global regulatory frameworks:
For hydrogen: EC79/2009, ISO 14687, ATEX certification
For CO₂: PED 2014/68/EU, API 618 (for reciprocating), ISO 8573-1 (for air quality)
Compliance isn’t just about red tape—it’s about safe commissioning, easier permitting, and long-term trust from your stakeholders.
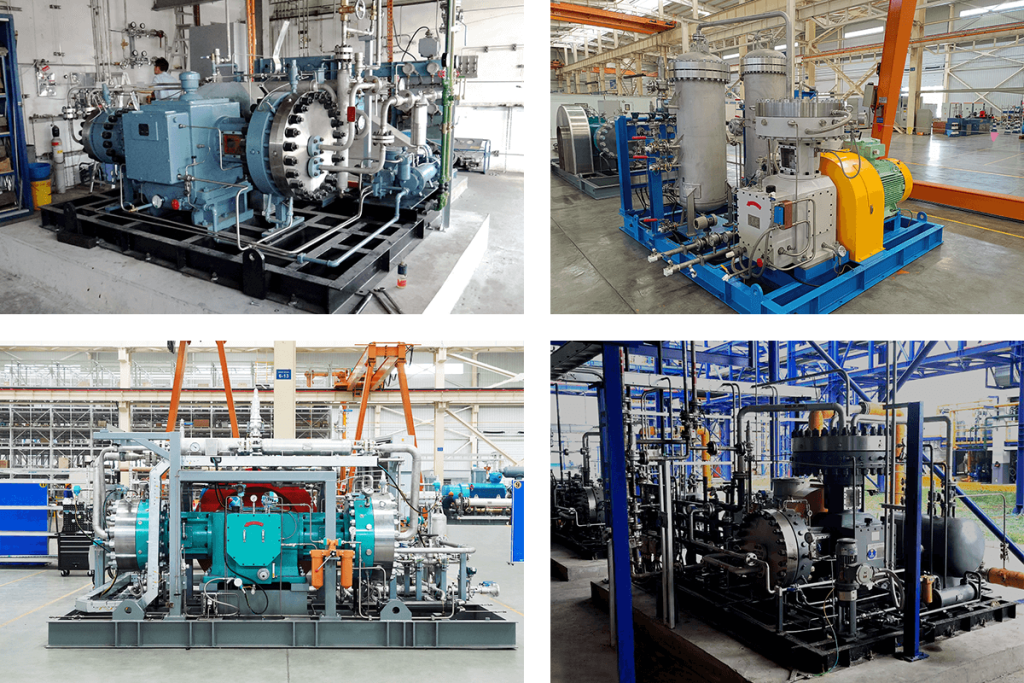
Conclusion
Green hydrogen and carbon capture are poised to play a pivotal role in the transition to sustainable energy systems. However, the success of these projects depends heavily on the right equipment, including the compressor.
At MINNUO, we specialize in providing high-quality compressors designed for green hydrogen and carbon capture projects. Our solutions are tailored to meet the specific needs of clean energy applications, ensuring efficiency, reliability, and long-term savings.
If you’re embarking on a clean energy project, contact MINNUO today for a tailored compressor solution that supports your goals for sustainability and operational success. Let us help you build the foundation for a cleaner, greener future.