Hydrogen, as a vital part of future clean energy, plays a key role in reducing carbon emissions and addressing global warming. A stable and sustainable hydrogen supply depends on the right hydrogen production technology, with electrolyzers being the core equipment that generates hydrogen by decomposing water. To ensure efficient use of hydrogen, it is often compressed to high pressure and stored in tanks for conversion into clean energy through fuel cells. Due to the extremely small size of hydrogen molecules, direct storage requires large spaces, making appropriate compression and storage methods critical for system efficiency and economic viability.
Among the four main hydrogen production electrolyzer technologies: Alkaline Electrolyzers (AEC) use alkaline solutions to produce hydrogen, offering low costs but slower response; Proton Exchange Membrane (PEM) Electrolyzers work with a proton exchange membrane, providing fast startup and high-purity hydrogen but at a higher cost; Solid Oxide Electrolyzers (SOEC) utilize high temperatures to decompose water vapor, offering high efficiency but requiring heat-resistant equipment; and Anion Exchange Membrane (AEM) Electrolyzers combine the advantages of the previous two, eliminating the need for precious metals, but the technology is still immature. These electrolyzers are suitable for different industrial applications based on their characteristics.
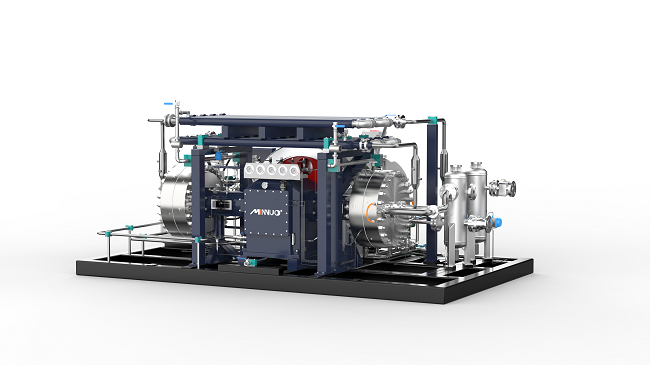
Overview of the Four Main Electrolyzer Technologies
The hydrogen production industry offers diverse technological paths, with “green hydrogen” referring to the process of obtaining hydrogen and oxygen through water electrolysis. Electrolyzers, being the core equipment, account for about 70% of the total hydrogen production system cost, making the selection of the appropriate electrolyzer crucial. Based on different technological paths, electrolyzers are mainly divided into four types: Alkaline Electrolyzers, PEM Electrolyzers, SOEC Electrolyzers, and AEM Electrolyzers.
Each electrolyzer type is suited for different application needs, from hydrogen fuel for buses to clean energy for power plants. Here are their features and differences:
Alkaline Electrolyzers (AEC)
AEC is the most established electrolyzer technology in industrial applications, generating hydrogen through the movement of hydroxide ions in an alkaline solution (e.g., potassium hydroxide). During electrolysis, water molecules are split by direct current, releasing hydrogen at the cathode and oxygen at the anode. AEC technology is mature, cost-effective, and does not require rare metals, making it suitable for large-scale industrial use. However, AEC has slower load response and longer startup times, which limits its use in applications requiring quick start-ups.
PEM Electrolyzers
PEM Electrolyzers use a proton exchange membrane as a solid electrolyte, capable of operating at high current densities and quickly responding to load changes. The proton exchange membrane only allows protons to pass, ensuring efficient electrochemical reactions. The advantages of PEM Electrolyzers include fast startup, high current density, high-purity hydrogen generation, and a compact structure, making them ideal for distributed hydrogen production systems and mobile applications. However, PEM Electrolyzers require precious metals like platinum as catalysts, making the equipment expensive. Additionally, the proton exchange membrane requires high-quality deionized water for stable operation.
SOEC Electrolyzers
SOEC Electrolyzers use solid ceramic materials (e.g., zirconium oxide) as the electrolyte, operating at high temperatures (typically 700-1000°C), utilizing heat to decompose water vapor into hydrogen and oxygen. Due to the high-temperature electrolysis, SOEC Electrolyzers have relatively low electrical energy demands and can directly use waste heat from industrial processes, leading to high overall efficiency. SOEC is particularly suited for processes that generate industrial steam, such as in the steel and chemical industries, where waste heat can be used for hydrogen production. However, SOEC technology faces challenges related to high-temperature material stability and equipment durability, which impact its large-scale industrial application.
AEM Electrolyzers
AEM Electrolyzers are an emerging technology that combines the advantages of both Alkaline and PEM Electrolyzers. AEM uses an anion exchange membrane to conduct electricity by moving hydroxide ions in the electrolyte to decompose water. Compared to traditional alkaline electrolyzers, AEM Electrolyzers do not require expensive platinum-group metals, potentially reducing system costs significantly. With solid electrolytes, AEM Electrolyzers offer higher current density and compact system designs. However, AEM technology is still in the research and development stage, with challenges regarding membrane stability and lifespan that need to be addressed for large-scale commercialization.
Advantages and Disadvantages of Each Electrolyzer
Each electrolyzer technology has unique advantages and limitations. The selection of the most suitable electrolyzer depends on the specific needs and application scenarios.
Alkaline Electrolyzers (AEC)
- Advantages: Mature technology, low manufacturing costs, does not require rare metals, suitable for large-scale industrial applications.
- Disadvantages: Slow response to load fluctuations, long startup time (about 20 minutes), limiting its use in applications requiring rapid responses.
PEM Electrolyzers
- Advantages: Fast startup, agile load response, suitable for distributed and mobile applications, operates at higher pressures, produces high-purity hydrogen.
- Disadvantages: Requires precious metal catalysts (e.g., platinum), leading to high equipment costs, especially in large-scale applications.
SOEC Electrolyzers
- Advantages: High efficiency, especially suitable for integration with high-temperature processes, can utilize industrial waste heat, promising cost reduction for large-scale applications.
- Disadvantages: Requires high-temperature environments, with challenges related to the stability of high-temperature materials, suitable for processes with industrial steam.
AEM Electrolyzers
- Advantages: Combines the benefits of Alkaline and PEM Electrolyzers, does not require rare metals, offers higher flexibility, and holds great potential for future development.
- Disadvantages: Membrane stability and lifespan need improvement, and large-scale industrial applications are not yet fully realized.
Ideal Operating Conditions and Application Scenarios
Each electrolyzer technology performs best under specific conditions. Below are their ideal application scenarios:
Alkaline Electrolyzers (AEC)
- Ideal for applications with pressure ranges of 0 to 16 bar, especially suited for medium-scale applications (10-20 MW), ideal for industrial hydrogen production.
PEM Electrolyzers
- Typically operate at pressures around 30 bar, suitable for applications in the 10-40 MW range. Due to their rapid startup and flexibility, they are particularly suited for intermittent renewable energy-driven hydrogen production, such as solar and wind.
SOEC Electrolyzers
- Suitable for applications that require process steam, typically with inlet pressures close to atmospheric pressure, especially for 5-20 MW scenarios. Their high efficiency makes them ideal for energy-intensive industries like chemicals, especially where waste heat is available for utilization.
AEM Electrolyzers
- Similar to PEM in terms of operating pressure (usually 30 bar), suitable for applications in the 10-40 MW range. Due to the lack of rare metals, AEM Electrolyzers offer significant cost advantages for large-scale applications in the future.
Importance of Hydrogen Compressors in Hydrogen Production
Regardless of the electrolyzer technology chosen, compressors are an indispensable part of the hydrogen production system. While compressors account for only about 10% of the total hydrogen production system cost, they play a crucial role in ensuring efficient storage and safe transport of hydrogen. Hydrogen tends to heat up significantly during compression, so multi-stage compression is necessary to prevent excessive temperature rise and maintain a safe operating range (usually below 130°C).
MINNUO has developed a series of high-performance hydrogen compressors tailored for hydrogen compression, equipped with advanced components and technologies to meet the demands for efficient and safe compression. Our targeted technologies and designs include:
- High-Precision Sealing Technology: To address the issue of hydrogen leakage due to the small size of hydrogen molecules, we use multi-layer sealing structures and high-precision sealing materials to ensure the compressor’s sealing performance, effectively preventing hydrogen leaks and ensuring safe system operation.
- Multi-Stage Compression and Intermediate Cooling: Our hydrogen compressors employ multi-stage compression, with intermediate coolers after each stage to lower gas temperature, reduce heat accumulation during compression, improve compression efficiency, and extend the equipment’s lifespan.
- Explosion-Proof Design: Given the flammability and explosiveness of hydrogen, safety is paramount. Our compressors are designed with explosion-proof motors and control systems that comply with ATEX and IECEx standards, ensuring the highest safety standards during operation.
- Intelligent Control System: MINNUO hydrogen compressors are equipped with advanced intelligent control systems that use sensors to monitor the compressor’s operating status in real-time, automatically adjusting operational parameters to optimize performance, reduce energy consumption, and ensure system stability.
In practical applications, using multi-stage compression with intermediate cooling effectively reduces the compression ratio at each stage, preventing excessive temperature rise. In typical multi-stage compression systems, each compression stage is followed by an intermediate cooler to lower the gas temperature, improve compression efficiency, and reduce thermal load on the compressor itself.
Hybrid Electrolyzer Solutions
The advantage of hybrid electrolyzer solutions lies in combining the benefits of different electrolyzer technologies to achieve higher overall efficiency.
For instance, in an industrial park project, MINNUO used a hybrid configuration of Alkaline and PEM electrolyzers: Alkaline electrolyzers handle base load hydrogen production to meet the basic hydrogen demand of the industrial park, while PEM electrolyzers address peak load and fluctuations. This combination optimizes system costs and ensures fast response during fluctuations in hydrogen demand.
Our Mastery and Research Progress in Hydrogen Electrolyzer Technology
MINNUO has long been committed to the research and innovation of hydrogen electrolyzer technology, achieving significant progress in Alkaline Electrolyzers (AEC) and PEM Electrolyzers. We have successfully designed and produced multiple commercial-grade electrolyzers, with a focus on improving production efficiency, reducing energy consumption, and increasing hydrogen production output. Our expertise enables us to provide tailored solutions for different industries, from energy storage to chemical processes, and our electrolyzers have been widely applied in various national and international projects.
Our ongoing research focuses on increasing the energy efficiency of the electrolyzers, optimizing system integration, and further developing AEM electrolyzers for future commercialization. With our commitment to clean energy and advanced technology, we continue to play a pivotal role in shaping the future of hydrogen energy production.