Ashley – a buyer for a large Australian hydrogen production and storage company. The company is involved in various areas, including fuel cell vehicles, industrial manufacturing, and power generation.
Customer Demand:
Ashley sent an email needing a hydrogen compressor for hydrogen charging. She provided specifications and requested a quote.
- l Inlet pressure: 0.4~0.6MPa(G)
- l Exhaust pressure: 25~40MPa(G)
- l Inlet air temperature: ≤30℃
- l Exhaust temperature: ≤45℃(after cooling)
- l Volume flow: 3Nm 3/h
Demand Analysis:After exchanging WhatsApp, we analyzed Ashley’s desire for a piston compressor capable of handling hydrogen. It could meet a hydrogen product on the system’s specific compression requirements. We made the following analysis for her.
- Fully enclosed diaphragm compressor, safer than piston type with no significant downtime requirements.
- A Diaphragm compressor is more suitable for handling flammable and explosive hydrogen gas.
- Water’s cooling effect is better than wind’s cooling effect, improving productivity.
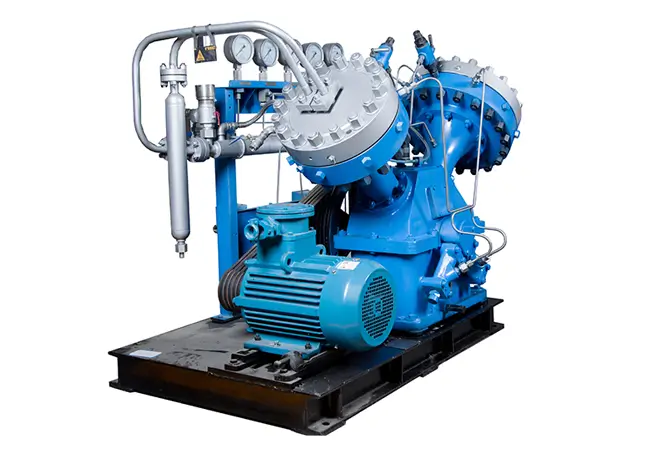
The customer finally chose the model G2V-3/5-350 diaphragm compressor with the following parameters:
- l Type: V-type, double-cylinder, two compressions, water-cooled
- l Drive mode: belt
- l Compression medium: hydrogen
- l Inlet pressure: 0.5MPa(G)
- l Exhaust pressure: 35MPa (G)
- l Inlet gas temperature: ≤ 30 ℃
- l Exhaust temperature: ≤45℃ (after cooling)
- l Volume flow: 3Nm 3/h
- Crankshaft speed: 400 r/min
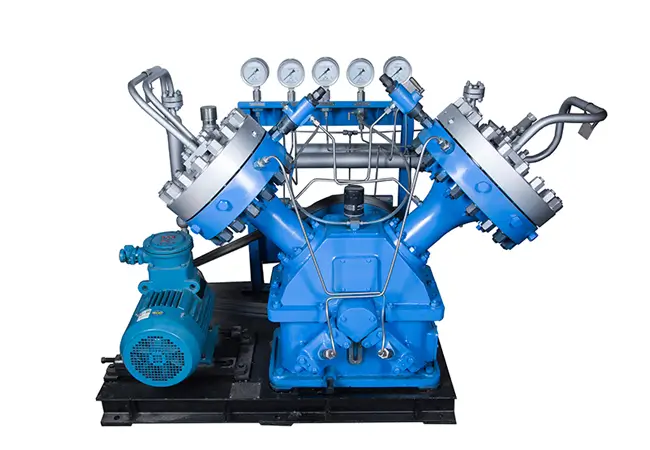
Excellent Service:
- lEfficient demand feedback and 24h online response
- lCustomized and reliable solutions, customer first
- lSend videos and photos during production to ensure customers keep track of production progress
- lProvide test run videos after production is completed to confirm the required specifications
- larrange the most efficient shipping company to ensure timely delivery
- lprovides complete training and support services
On-site service and training
- Installation: Customers will install by themselves according to the requirements provided by Minuo.
- Commissioning: After the installation, an experienced after-sales team will go to the site for free commissioning. The team will ensure that the equipment can be used generally on schedule.
- Training: During commissioning, the after-sales service personnel will provide free on-site training. The team will ensure that the operators know the relevant knowledge and skills.
- Acceptance: After the above work, we will approve. Both parties sign on the after-sales service sheet to confirm that the equipment is accepted and the commissioning work has been completed.
- Technical support: If there are technical problems during the use process, customers can contact us anytime. We will provide free technical support.
- Response time: If equipment fails, customers promptly contact us, and we promise to reply within 16 hours.
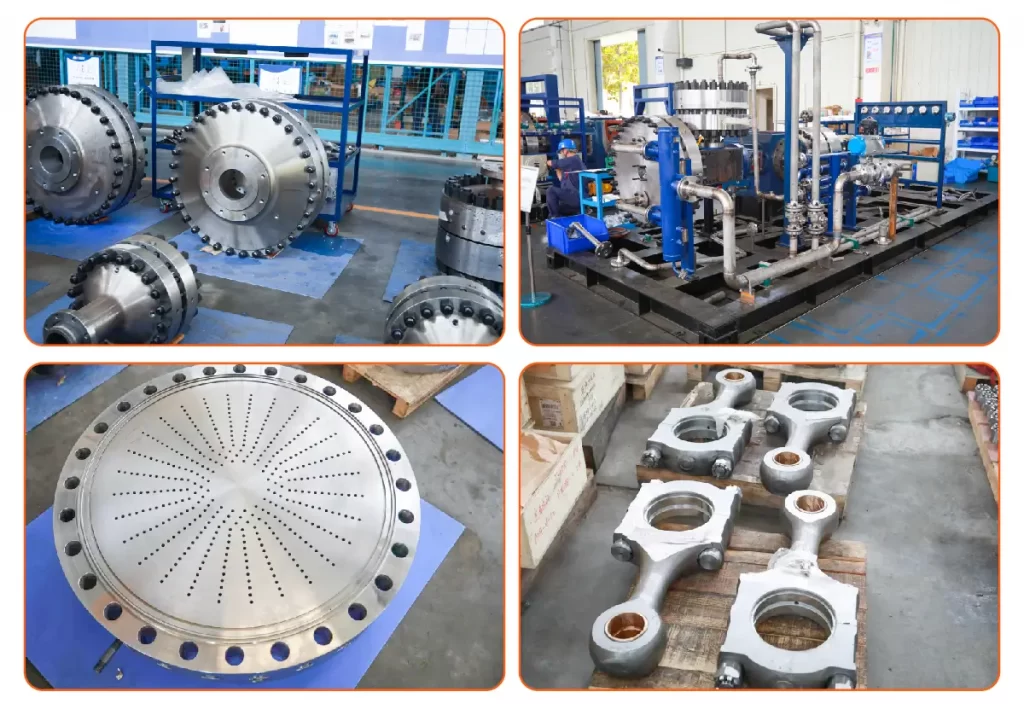