Scroll compressors and reciprocating compressors represent two major mainstream technological approaches, with significant differences in performance, applicable scenarios, and future development trends. This article conducts an in-depth analysis from five key dimensions—mechanical principles, energy efficiency characteristics, environmental compatibility, cost-effectiveness, and industrial applications. Combining experimental data and industry case studies, it provides a scientific basis for enterprise product selection and technological upgrades.
Scroll compressors operate through a non-reciprocating rotary mechanism, delivering smooth, low-pulsation, and energy-efficient performance. They are ideal for residential air conditioning and heat pumps, offering higher energy efficiency and lower maintenance costs. However, their efficiency drops under high pressure ratios and low-temperature environments. Reciprocating compressors excel in high-pressure, low-temperature, and multi-stage compression applications, making them suitable for oil and gas transportation and ultra-low temperature refrigeration systems.
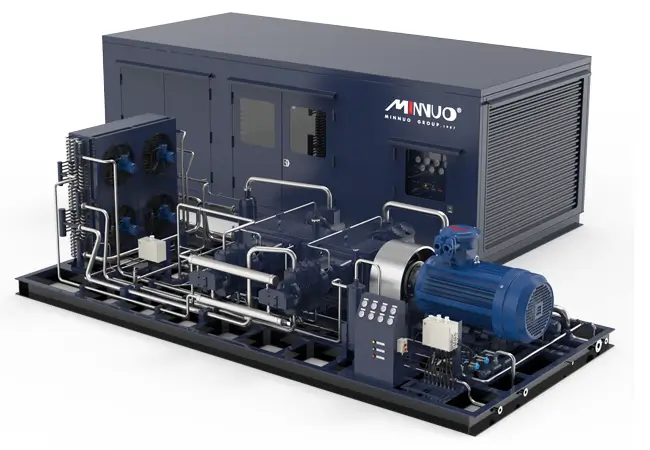
I. Mechanical Structure and Working Principle Comparison
1.1 Core Operating Mechanism Differences
Scroll Compressor:
Its core structure consists of a pair of meshing orbiting and stationary scroll plates. The orbiting scroll revolves eccentrically around the stationary scroll, forming multiple continuous and sealed crescent-shaped compression chambers. As the scroll rotates, gas is gradually pushed from the outer edge toward the center, completing the suction, compression, and discharge processes. With no reciprocating components, the mechanical inertial force is minimal, greatly enhancing operational stability.
Reciprocating Compressor:
Based on a piston-cylinder design, it uses a crankshaft and connecting rod to convert the motor’s rotary motion into linear reciprocating motion of the piston. During downward movement, the piston creates negative pressure to intake gas; during upward movement, it compresses the gas and discharges it through valves. Its working principle inherently involves mechanical vibration and airflow pulsation, which are especially pronounced under high pressure ratio conditions.
Key Differences:
- Motion Type: Scroll compressors use pure rotary motion; reciprocating compressors use linear reciprocating motion.
- Number of Compression Chambers: Scroll compressors require only one set of compression units, whereas reciprocating compressors often require 2–6 cylinders to balance pulsations.
- Cycle Continuity: Scroll compressors achieve uninterrupted compression; reciprocating compressors have “dead time” due to piston reversal.
1.2 Rotational Characteristics and Airflow Pulsation
According to MINNUO laboratory data, a scroll compressor requires 2–2.5 crankshaft rotations per compression cycle, while a reciprocating compressor completes one suction stroke in half a rotation and one discharge in a quarter. Although multi-cylinder designs reduce pulsation amplitude (e.g., 6-cylinder models with pulsation frequency six times the base frequency), instantaneous flow fluctuations remain significantly higher than in scroll compressors.
Scroll Compressor Pulsation Suppression Mechanisms:
- Continuous rotary motion eliminates mechanical inertia shocks.
- Gradual compression chamber volume changes prevent abrupt gas flow variations.
- No valve opening/closing action (only dynamic discharge valves in some high-pressure-ratio models).
Measured Data:
At the same power (10kW), scroll compressor outlet pulsation amplitude is 0.2 bar, while reciprocating compressors can reach 2.5 bar. This translates to over 10× higher pipeline vibration intensity (ISO 10816 standard).
II. Energy Efficiency Characteristics and Thermodynamic Analysis
2.1 Isentropic Efficiency Comparison
Scroll Compressor Advantages at rated conditions (e.g., 7°C evaporating/54°C condensing in air conditioning):
- No Clearance Volume Loss: Fully sealed chambers eliminate residual gas expansion that lowers volumetric efficiency.
- Low Throttling Loss: No valve resistance during suction; dynamic discharge valves engage only under high-pressure differentials.
- Low Mechanical Friction Loss: Contact area of moving parts is only 1/5 that of reciprocating (scroll speed ≤3 m/s, piston avg. speed ≥8 m/s).
Experimental Data:
Scroll compressors can reach 85%-92% isentropic efficiency, while reciprocating types range from 70%-80%. In one commercial AC system case, scroll compressors reduced annual power consumption by 18%.
2.2 Efficiency Reversal Under High Pressure Ratios
When the pressure ratio (discharge/inlet) exceeds 4:1 (e.g., low-temp refrigeration or CO₂ systems), scroll efficiency may drop:
- Non-Valve Design Limitation: Fixed compression ratio may lead to “over-compression” or “under-compression” losses. At -40°C evaporating temp, scroll efficiency can be 5%-8% lower than reciprocating.
- Reciprocating Adaptability: Adjustable clearance volume (e.g., via variable valve timing) and multi-stage compression maintain high efficiency across wide pressure ranges.
Case Study:
In an industrial freezing system (-45°C evaporating temp, 8:1 pressure ratio), the reciprocating compressor achieved a COP of 2.1, compared to the scroll’s 1.8.
III. Environmental Refrigerant Compatibility Challenges
3.1 Technical Bottlenecks with CO₂ (R744) Systems
Although CO₂ has zero ODP and low GWP (GWP=1), its low critical temp (31.1°C) and high critical pressure (7.38 MPa) pose challenges:
Scroll Compressor Difficulties:
- High-Pressure Sealing: Scroll end-face seals must withstand >70 bar; common fluororubber materials often fail.
- Lubrication System Redesign: CO₂ is incompatible with mineral oils, requiring POE or PAG, which increases wear rate 3×.
- Intermediate Injection Challenge: Enhancing low-temp performance requires mid-chamber injection, demanding extremely precise scroll geometry.
Reciprocating Compressor Advantages:
- Oil film lubrication between piston rings and cylinder walls reduces leakage by 40% compared to scrolls.
- Multi-stage structures are more compatible with CO₂ transcritical cycles.
3.2 Adaptability to Alternative Refrigerants
For R290 (propane), R32, and other low-GWP refrigerants, scroll compressors dominate due to:
- Enclosed design minimizes flammable refrigerant leakage.
- Variable speed control precisely regulates discharge temperature, avoiding R290 ignition limits (2.1%-9.5% by volume).
Market Data:
As of 2024, 90% of household R290 air conditioners use scroll compressors, with leakage rates <1g/year, meeting IEC 60335-2-40 safety standards.
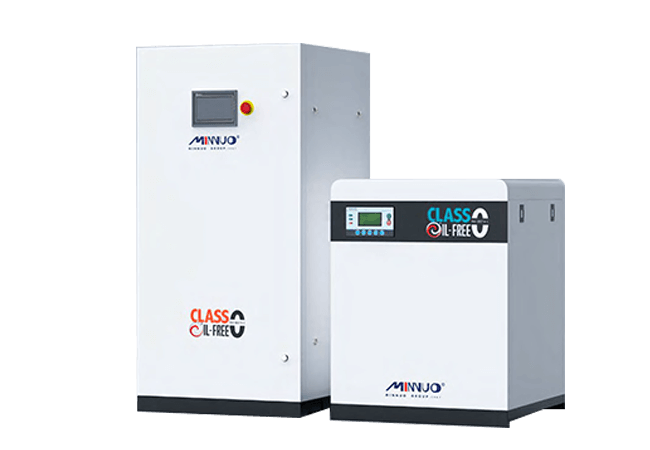
IV. Full Life Cycle Cost Analysis
4.1 Initial Purchase Cost
- Scroll Compressor: Higher precision (≤5μm scroll profile tolerance) and complex assembly make unit price 20%-30% higher than reciprocating.
- Reciprocating Compressor: Standardized piston-cylinder modules support mass production, offering cost advantages.
4.2 Operating and Maintenance Costs
Scroll Compressor Advantages:
- Fewer Components: 150–200 parts vs. 300–400 in reciprocating.
- Longer Maintenance Intervals: No fragile valves or piston rings; first overhaul after 50,000 hours (reciprocating: 20,000 hours).
- Lower Energy Bills: For a 100kW commercial system, annual electricity savings reach $12,000 (at $0.10/kWh).
Economic Estimate:
Over a 10-year life, scroll compressors’ total cost of ownership (TCO) is 15%-25% lower, especially in continuous-use scenarios.
V. Industry Application Scenarios and Selection Guide
5.1 Scroll Compressor Dominant Fields
- Residential & Commercial AC: Over 75% demand share due to high efficiency, low noise, and variable speed control.
- Heat Pump Water Heaters: Enhanced vapor injection scrolls maintain COP ≥2.0 at -25°C.
- Data Center Cooling: 24/7 uptime required—scroll compressors offer MTBF up to 100,000 hours.
5.2 Irreplaceable Reciprocating Compressor Applications
- Oil & Gas Transport: Under ultra-high pressure (>100 bar), efficiency is 12%-15% higher than scrolls.
- Industrial Refrigeration: Multi-stage compression and inter-cooling meet sub -60°C ultra-low temp needs.
- Mobile Compressors: Better tolerance to engine RPM fluctuations in diesel-powered scenarios.
VI. Technological Evolution and Future Trends
6.1 Scroll Compressor Innovation Directions
- Smart Integration: Embedded pressure/temp sensors enable AI fault prediction (e.g., Copeland SmartFlow™).
- Material Upgrades: Silicon carbide coatings extend wear life to 200,000 hours.
- CO₂ Cross-Critical Systems: Danfoss TWH series boosts COP to 3.1 via mid-injection.
6.2 Reciprocating Compressor Breakthroughs
- Oil-Free Designs: Use self-lubricating materials (e.g., PTFE rings) for food/pharma-grade cleanliness.
- Modular Architecture: Bitzer’s FOCUS series allows fast cylinder swaps for varying pressures.
- Hybrid Drive Systems: Combine linear motors with digital valves to increase efficiency by 30%.
VII. User Selection Decision Matrix
Evaluation Criteria | Weight | Scroll Compressor Score | Reciprocating Compressor Score |
Energy Efficiency (COP) | 30% | 9/10 | 7/10 |
Initial Investment Cost | 20% | 6/10 | 8/10 |
Maintenance Convenience | 15% | 9/10 | 5/10 |
High-Pressure/Low-Temp | 20% | 6/10 | 9/10 |
Environmental Compatibility | 15% | 8/10 | 7/10 |
Comprehensive Recommendation:
- Total score >80: Choose scroll compressors (for AC, heat pumps, conventional refrigeration).
- Total score <70: Choose reciprocating compressors (for petrochemicals, ultra-low temp freezing).
VIII. Conclusion
The technical competition between scroll and reciprocating compressors essentially reflects a trade-off between “efficiency and adaptability.” As breakthroughs in material science, control algorithms, and refrigerant technologies emerge, the performance boundaries between the two are gradually blurring.
MINNUO recommends that users build a multi-dimensional evaluation model based on actual operating conditions (pressure ratio, displacement needs, ambient temperature), cost constraints, and environmental regulations to select the optimal life-cycle solution.
Of course, MINNUO has the best engineering team, and we will tailor a custom solution specifically for you.