As we know, reciprocating compressors are widely used in various industries such as petroleum, chemical engineering, metallurgy, and more, serving as a common gas compression equipment. However, due to their structural characteristics, reciprocating compressors often encounter various faults during long-term operation. This article will explore the common faults of reciprocating compressors and their troubleshooting methods, aiming to help users improve the stability of equipment operation and extend its service life.
Common faults of reciprocating compressors include gas leakage, mechanical wear, lubrication system failure, and irregular exhaust. The main troubleshooting methods include regular inspection and replacement of seals, repairing or replacing damaged pistons and cylinders, cleaning or replacing lubricating oil, maintaining gas valves and exhaust systems, and conducting regular fault checks to ensure normal operation and prolong the service life.
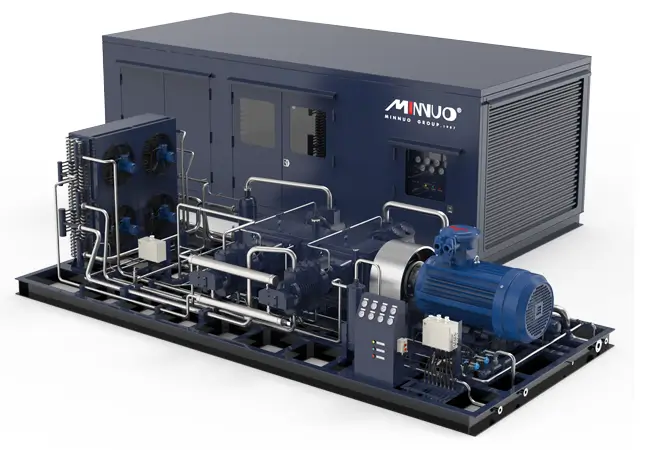
Basic Knowledge
Definition
A reciprocating compressor, also known as a piston compressor, uses the reciprocating motion of the piston in the cylinder to compress gas. Depending on the required pressure level, reciprocating compressors can be designed as single-stage or multi-stage compressors. They are especially common in applications where high gas pressure is required.
Operating Principle
When the crankshaft rotates, the connecting rod causes the piston to move reciprocally. The piston’s motion leads to continuous changes in the working volume of the cylinder.
Specifically, as the piston moves from the cylinder head side, the working volume inside the cylinder gradually increases. At this point, gas is pushed into the cylinder through the intake valve via the intake pipe until the working volume reaches its maximum. The intake valve then closes. As the piston moves in the opposite direction, the working volume decreases, causing the gas pressure to rise. When the pressure inside the cylinder is slightly higher than the exhaust pressure, the exhaust valve opens, and the gas is discharged from the cylinder until the piston reaches its limit position. The exhaust valve then closes, and when the piston starts moving in the opposite direction again, the whole process repeats.
In summary, when the crankshaft completes one full rotation, the piston completes a single reciprocating motion, and the working volume inside the cylinder continues to change accordingly.
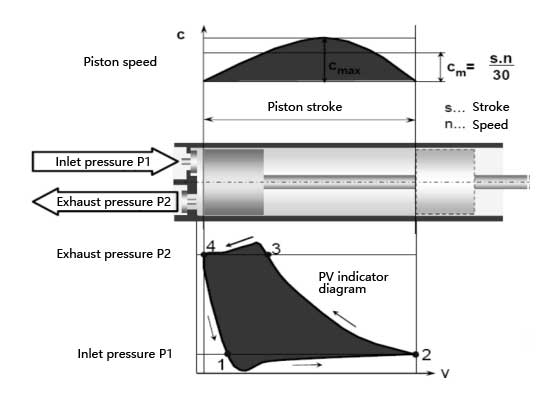
The ideal operating conditions for reciprocating compressors should meet the following criteria:
- The compressor has no dead volume.
- There is no resistance loss during the intake and exhaust processes.
- No heat exchange occurs between the system and the external environment during the intake and exhaust processes.
- There are no internal leaks in the compressor.
Pros and Cons
Main Advantages
- Wide Application Range: Piston compressors can be customized to meet requirements for ultra-high pressure, high pressure, medium pressure, or low pressure, with minimal fluctuations in exhaust volume under different exhaust pressures.
- High Compression Efficiency: Large reciprocating compressors can achieve adiabatic efficiency greater than 80%, and their isothermal efficiency can usually remain above 70%.
- Strong Adaptability: This type of compressor is suitable for a wide range of gas delivery volumes, from as low as a few liters per minute to as high as 500 m³/min of exhaust volume.
Main Disadvantages
- Gas Oil Contamination: Particularly in industries like chemicals, where the quality of gas is critical, the compressed gas may contain a significant amount of oil contamination, which increases the burden of purification.
- Speed Limitations: Due to the inertial effects of the reciprocating motion, reciprocating compressors’ rotational speed cannot be too high. This limits the maximum amount of gas it can process, meaning that in large-scale production environments, larger equipment or multiple units are often required to operate, thereby increasing both equipment investment and infrastructure costs.
- Intermittent Exhaust: As the compression process is intermittent, the discontinuity in gas discharge can cause fluctuations in exhaust pressure, which typically necessitates the installation of pressure stabilizing equipment to ensure a steady airflow.
- Frequent Maintenance: This type of compressor has many wear-prone components, resulting in high maintenance requirements. Therefore, spare units are usually kept on hand to address potential maintenance needs.
Common Fault Analysis and Troubleshooting Methods
Abnormal Noise
When equipment malfunctions, it is often accompanied by unusual sounds, which can typically be used to diagnose the faulty parts. Below, we will explore the potential causes of abnormal noise from components such as cylinders, crankcases, and intake/exhaust valves.
Abnormal Noise from the Cylinder
- Insufficient Dead Point Clearance: If the dead point clearance is too small, the piston may directly contact the cylinder body, producing a knocking sound.
- Water Hammer Phenomenon: If water accumulates in the cylinder, it can lead to a water hammer sound.
- Loose Nut: If the connection nut or cotter pin between the piston rod and the piston is loose, it may cause unusual noises.
- Loose Plug: If the plug at the piston end is loose, it may press against the cylinder head, generating noise.
- Wear Issues: Severe wear on the cylinder, piston, and piston rings, which causes increased gaps, can also lead to noise.
- Tightening Issues: If the piston rod is not securely connected to the crosshead, the piston may move upwards and collide with the cylinder head, potentially creating abnormal sounds.
- Insufficient Lubrication: A lack of lubricant or coolant may result in high-temperature dry friction, leading to the seizure of the piston rings.
- Foreign Objects Entering the Cylinder: If hard objects, such as valve plates or springs, fall into the cylinder, they will create abnormal noises.
- Alignment Issues: Misalignment between the crankshaft and the cylinder centerline may also cause noise.
Solution:
Adjust the dead-point clearance, remove water accumulation from the cylinder, tighten connections such as nuts and plugs, repair or replace worn parts, ensure a secure connection between the piston rod and the crosshead, replenish lubricants or coolants, remove foreign objects from the cylinder, and calibrate the alignment between the crankshaft and the cylinder’s centerline.
Abnormal Noise in the Crankcase
- Wear or looseness of the connecting rod big-end bearing: If the connecting rod big-end bearing is excessively worn, loose, or the gap exceeds the standard, it may cause abnormal noise.
- Severe wear of the crankshaft or crank pin: Deformation of the crankshaft, such as ovality or excessive taper, may generate abnormal noise.
- Wear of the crosshead pin and bushings: If the fit gap between the crosshead pin and the bushings increases, it can also lead to abnormal noise.
- Insufficient oil supply or excessive tightness of the crankshaft bearings: If the crankshaft bearings run out of oil or have an excessively tight fit gap, they may overheat or even burn out, producing noise.
- Looseness between the crosshead pin and the crosshead body: If the connection between the crosshead pin and the crosshead body is not tight, noise may be generated.
- Loose fasteners: Loose or damaged bolts, nuts, connecting rod bolts, or crosshead bolts inside the crankcase can also result in abnormal noise.
- Excessive gap in the crosshead slipper: If the gap between the crosshead slipper and other components is too large, or the fastening bolts are loose, it may cause noise.
- Severe bearing wear: If the bearings at both ends of the crankshaft are severely worn and the gap is too large, it can also cause noise.
Solution:
Replace the worn connecting rod big-end bearings, repair or replace the worn crankshaft and journals, adjust the clearance between the crosshead pin and the bushings, ensure proper oil supply to the crankshaft bearings, tighten the connection between the crosshead pin and the crosshead body, check and tighten all fasteners, adjust the clearance of the crosshead slide, and replace severely worn bearings.
Causes of Suction and Exhaust Valve Fracture
- Improper Load Regulator Setting: If the load regulator is not properly adjusted, it can cause the valve to fracture.
- Material Stress Issues: The valve may fracture due to stress concentration during the manufacturing process.
- Inappropriate Material Selection: If the material of the valve is not suitable for the working environment, it may lead to fracture.
- Mismatch Between Gas Force and Spring Force: If the gas force and spring force are not properly matched (too hard or too soft), it can cause damage to the valve.
- Design Flaws: Insufficient valve design may make it prone to fracture.
- Excessive Speed: Increasing the speed without consideration may result in valve damage or fracture.
Solution:
Properly set the load regulator, optimize the valve manufacturing process to reduce stress concentration, select materials suitable for the operating environment, precisely match the gas and spring forces, improve the valve design, and avoid arbitrarily increasing the speed.
Valve Knock Sound
- Improper Load Adjustment: If the load regulator is not correctly adjusted, the valve plate may collide with other components.
- Damaged Valve Plate: A broken valve plate can produce a knocking sound.
- Loose or Damaged Valve Spring: If the valve spring does not maintain sufficient tension, it may cause the valve plate to become unstable, resulting in a knocking sound.
- Collision Between Valve Seat and Piston: When the valve seat depth is incorrect, it may cause a collision between the valve seat and the piston inside the cylinder.
- Incorrect Valve Installation: Improper placement of the valve or incomplete fixing of the valve cover can also cause knocking sounds.
Solution:
Precisely adjust the load regulator, replace damaged valve plates, repair or replace loose or damaged valve springs, adjust the valve seat depth, and correctly install the valve and valve cover.

Overheating Issues
Overheating typically occurs in components with significant friction. Commonly affected areas include:
- The contact area between the crankshaft and bearing
- The contact area between the big end of the connecting rod and the crank pin, crosshead pin, or piston pin
- The contact area between the crosshead and guide rails
- The contact area between the packing and the piston rod
- The contact area between the piston ring and the cylinder wall
Bearing Overheating
- Uneven fit between the bearing and journal: If the bearing and journal contact area is too small, it can cause excessive local pressure, leading to overheating.
- Bearing misalignment or crankshaft bending: Incorrect installation of the bearing or any bending or twisting of the crankshaft itself can result in uneven wear on the bearing, increasing friction and causing overheating.
- Oil quality issues: Poor quality bearings or lubricant with low viscosity, blocked oil passages, or low oil pressure can all lead to inadequate lubrication, which results in overheating.
- Improper installation: Incorrect installation procedures may cause uneven lubrication between the bearing and journal, accelerating overheating.
Solution:
Improve the fit between the bearing shells and shaft journals, correct any bearing installation deviations, repair crankshaft bending issues, use qualified bearing shells and appropriate viscosity lubricants, clean the oil paths, ensure proper oil pressure, and follow correct installation procedures.
Piston Rod Overheating
There are several possible causes for piston rod overheating, including:
- Improper assembly of the packing gland: If the packing gland is not assembled correctly, it may cause friction and overheating.
- Excessively small gap between the piston rod and packing: A small gap can hinder normal movement and lubrication, leading to overheating.
- Contaminated or insufficient lubricant: Dirty oil or a lack of oil can lead to dry friction, causing overheating.
- Metal sealing ring adhesion: If the metal sealing ring cannot move freely, it will generate heat and friction.
- Incorrect assembly of metal plates: Improper assembly of metal plates may block the oil passages, leading to poor lubrication and overheating.
- Foreign objects in the packing box: Foreign materials in the packing box can hinder normal movement and cause overheating.
Solution:
Properly reassemble the packing box, adjust the clearance between the piston rod and the packing, clean or replenish lubricants, address any sticking metal sealing rings, correctly assemble metal plates, and remove any debris from the packing box.
Oil Pump and Injector Failures, Abnormal Oil Pressure/Temperature
Although oil pump and injector issues may seem minor, they can significantly impact the normal operation of the compressor and may lead to serious accidents. Failures usually result from insufficient oil supply and pressure drop:
- Excessive clearance: Worn parts or excessive gaps between components can lead to insufficient oil supply.
- Worn oil pressure regulator: If the regulator valve or spring weakens, oil may flow back to the oil tank, lowering the pressure.
- Clogged or contaminated filters or pipes: Blocked filters or broken pipes can obstruct normal oil circulation.
- Low oil level in the oil tank: Insufficient oil in the oil tank can cause improper lubrication and reduced pressure.
- Reduced pump speed or reverse rotation: These issues may prevent the oil pump from functioning correctly.
Solution:
Repair worn parts, adjust the clearances between components, replace the worn oil pressure regulator, clean or replace clogged or contaminated filters and pipes, replenish the oil tank to the proper level, and adjust the pump speed to normal operating conditions.
Abnormal Vibration
Vibration may originate from multiple sources within the system:
Cylinder Section
- Loose Supports: Unstable supports, loose components, or excessive loads can cause vibration.
- Poor Piping Layout: Improper piping design can increase pulsation and vibration.
Solution:
Tighten the support structure and optimize the pipe layout design.
Body Section
- Excessive Bearing or Guide Rail Clearance: Worn bearings or excessive clearance in sliding guide rails can lead to vibration.
- Installation Issues: Poor installation methods can result in mechanical instability and vibration.
- Cylinder-Induced Vibration: If vibrations from the cylinder are transmitted to the body, it may cause overall instability.
Solution:
Replace worn bearings, adjust the guide rail clearance, use the correct installation methods, and isolate vibrations coming from the cylinder.
Piping Section
- Insufficient or Poorly Positioned Piping Supports: Insufficient support or poorly positioned supports can lead to vibration at the support points.
- Weak Piping Framework: Vibration can occur if the piping support is not sufficiently sturdy.
- Flow-Induced Vibration: If the frequency of gas or fluid flow in the system matches the natural frequency of the pipes, resonance can occur, leading to noticeable vibration.
Solution:
Increase the pipe supports, adjust the support positions, reinforce the pipe frame, change the frequency of gas or fluid flow, and avoid resonance.
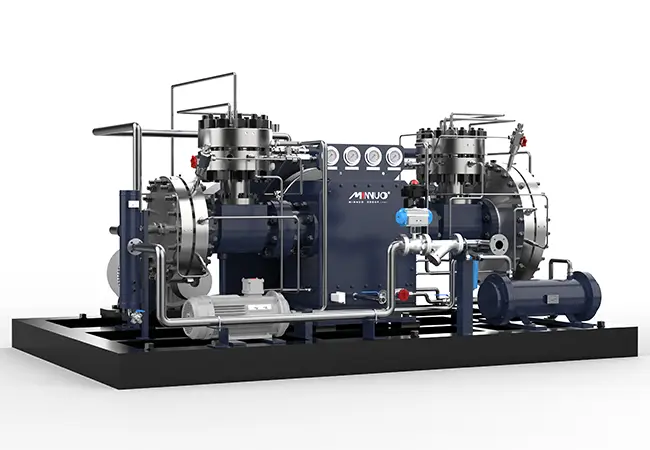
Conclusion
In summary, while reciprocating compressors play a crucial role in industrial applications, their unique structure and operating principles make them prone to a variety of faults. Regular inspections and maintenance, along with timely identification and resolution of these issues, can significantly improve the compressor’s operational efficiency and lifespan.
As a professional compressor manufacturer with over 30 years of experience, MINNUO is capable of effectively mitigating most of the issues mentioned above. For more professional knowledge, feel free to consult us!