Hydrogen compressors play a central role in high-pressure hydrogen gas transportation, ammonia synthesis, methanol production, and other processes, directly affecting production efficiency and safety. However, due to the complex structure and harsh operating conditions of hydrogen compressors, the risk of failure is high. This article systematically reviews common failures and their solutions, providing practical and feasible guidance for businesses.
Common failures of hydrogen compressors include low lubricating oil system pressure, gas valve and valve failure, cylinder and piston assembly damage, crosshead and connecting rod wear, and insufficient exhaust volume. Solutions to these problems include regular inspection of the lubricating oil system, optimization of the filtration system, timely replacement of worn components, and enhanced cooling system maintenance.
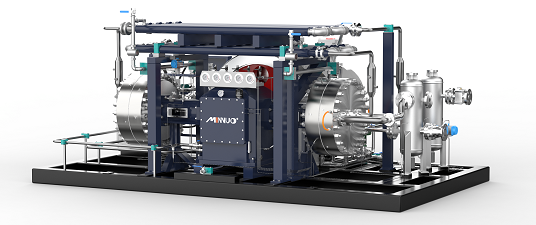
1. Lubricating Oil System Failures
1.1 Low Lubricating Oil Pressure
The lubricating oil system is one of the most critical components of a hydrogen compressor. Lubricating oil not only reduces friction and wear but also helps dissipate heat and prevents gas contamination. However, low lubricating oil pressure is one of the most common failures, typically caused by the following factors:
Fault Causes:
- Oil Leak: Static seal points in the oil circuit (such as flanges and joints) may leak due to aging or loosening, causing a reduction in oil volume and leading to low pressure.
- Oil Degradation: Over time, lubricating oil undergoes oxidation, especially when it contains excess moisture and metal ions, which reduces its viscosity and lubrication performance.
- Condensation and Foam Formation: If air or undissolved gas enters the lubricating oil system, foam will form, leading to reduced oil pressure and affecting the normal operation of the equipment.
Solutions:
- Seal Point Inspection: Regularly inspect the oil circuit system for leaks, tighten loose parts or replace aged seals to prevent oil leakage.
- Oil Management: Use low-viscosity lubricating oils with high anti-coking performance, ensure stable oil quality, and regularly check indicators such as carbon residue and moisture content. It is recommended to replace the lubricating oil every 3 months.
- Return Oil Pipe Optimization: Design the return oil pipe exit to be located at the far end of the filter inlet, effectively reducing bubble accumulation and ensuring stable oil flow.
2. Gas Valve and Valve Failures (Over 40%)
The gas valves and valves of a hydrogen compressor control gas flow and pressure. If failures occur, it may lead to gas leakage, reduced compression efficiency, and other issues. Among gas valve failures, carbon buildup on valve discs and spring fractures are the most common types of failure.
2.1 Carbon Buildup on Valve Discs and Spring Fractures
Fault Causes:
- Excessive Lubrication: Over-lubrication can cause carbon buildup on the valve disc surface, preventing normal opening and closing of the gas valve, leading to sluggish or ineffective valve operation.
- Gas Contamination: If hydrogen gas contains rust, sand particles, or other foreign materials, it will accelerate valve disc wear, reducing sealing performance and affecting compressor performance.
- Spring Failure: Fatigue or improper design of spring force (either too strong or too weak) affects the valve’s response speed, leading to instability.
Solutions:
- Lubrication Control: Adjust the lubrication amount by observing the carbon buildup in the cylinder, aiming to maintain the minimum lubrication while ensuring sufficient lubrication of the valve disc to prevent carbonization.
- Filtration System Upgrade: Install a high-efficiency gas-solid separator at the inlet line, regularly clean the filter mesh, and prevent particles from entering the compressor, thus extending the life of the valve disc.
- Valve Maintenance Standards: It is recommended to dismantle the gas valve every 3-6 months, clean the carbon buildup on the valve disc, check the spring’s elasticity, and perform nitrogen leakage tests before reassembly.
3. Cylinder and Piston Assembly Damage
3.1 Cylinder Wall Scuffing
The cylinder and piston are the core components of a hydrogen compressor. Damage to the cylinder wall directly reduces gas compression efficiency and, in severe cases, may cause equipment shutdown.
Fault Causes:
- Hydrogen Containing Particles: If hydrogen gas contains dust, carbon buildup, or other particles, it can exacerbate friction between the cylinder and piston, leading to cylinder wall scuffing.
- Insufficient Lubrication or Oil Film Rupture: If the lubrication system malfunctions and the oil film fails to cover the cylinder surface adequately, dry friction will occur, increasing cylinder wear.
Solutions:
- Minor Damage Treatment: Polish the cylinder wall and use a semi-circular oilstone to smooth the surface, restoring the cylinder’s smoothness and reducing friction.
- Severe Damage Boring: If cylinder damage is severe (the scuffing length exceeds 1/4 of the cylinder circumference or the depth exceeds 0.4mm), boring should be performed, and the appropriate piston rings should be replaced.
3.2 Piston Ring Leakage
Piston ring leakage is a common failure type that directly affects the sealing effect between the cylinder and piston, leading to gas leakage and reduced working pressure.
Fault Causes:
- Excessive Piston Ring Wear: Wear of the piston ring increases the gap between it and the cylinder, reducing sealing effectiveness and causing leakage.
- Improper Installation: If the piston ring is misaligned or stuck during installation, it will result in poor sealing, leading to leakage.
Solutions:
- Regular Piston Ring Replacement: Replace the piston ring according to service hours or wear detection results (typically every 2000-3000 hours) to ensure good sealing performance.
- Gap Adjustment: Select the appropriate mating gap based on materials (cast iron, aluminum alloy, steel, etc.) to ensure good sealing performance and avoid leakage.
4. Crosshead and Connecting Rod Wear
4.1 Crosshead Cracks and Slideway Wear
The crosshead and connecting rod are crucial transmission components in a hydrogen compressor. If failure occurs, it directly affects the operating efficiency of the cylinder.
Fault Causes:
- Long-Term High-Load Operation: Operating under high-load conditions for extended periods can cause metal fatigue, resulting in cracks in the crosshead or wear on the slideways.
- Poor Lubrication: Insufficient lubrication or contaminants entering the slideways will exacerbate friction, causing wear and crack formation.
Solutions:
- Crosshead Replacement: During maintenance, dismantle the crosshead via the middle body measurement hole or window, ensuring that the slideway working surface is not damaged and that the mating gap meets design requirements.
- Enhanced Lubrication Monitoring: Ensure the cleanliness of the lubricating oil, regularly check oil pressure and temperature, and maintain the oil temperature in the range of 40-50°C to prevent poor lubrication.
4.2 Connecting Rod Bearing Failure
The failure of the connecting rod bearing can also cause unstable operation of the cylinder and may even lead to severe damage to the equipment.
Solutions:
- Pair Replacement of Bearings: The connecting rod bearings should be replaced in pairs to ensure that the gap is 0.8‰-1.2‰ of the crankshaft neck diameter, avoiding excessive wear.
- Non-Destructive Testing: Conduct magnetic particle or ultrasonic testing on connecting rod bolts to avoid the risks posed by bolt fractures.
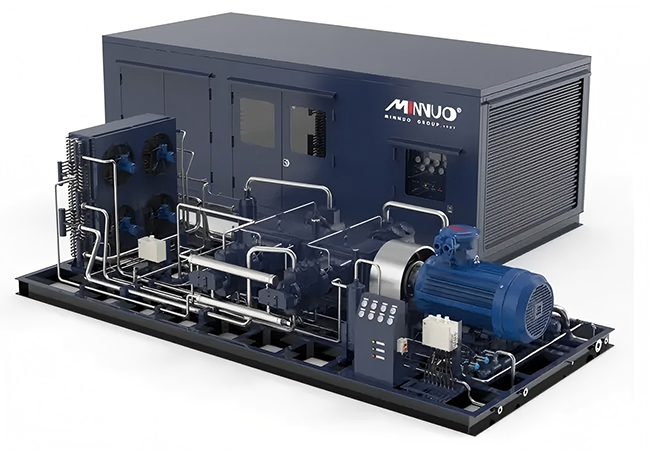
5. Process Operation-Related Issues
5.1 Insufficient Exhaust Volume
The exhaust volume of a hydrogen compressor directly affects the production process. Insufficient exhaust volume may prevent the product output from reaching the required levels.
Fault Causes:
- Inlet Filter Blockage: A clogged inlet filter restricts gas flow, resulting in insufficient exhaust volume from the compressor.
- Gas Valve Leakage: If the gas valve seals poorly or the packing box seal fails, it can also lead to insufficient exhaust volume.
Solutions:
- Regular Cleaning of the Filter: Clean the inlet filter every 500 hours to ensure smooth gas entry into the system.
- Packing Box Maintenance: Lubricate the packing box and ensure proper alignment of the piston rod to prevent gas leakage.
5.2 High Exhaust Temperature
High exhaust temperatures can affect the operating efficiency of hydrogen compressors and even lead to equipment damage.
Fault Causes:
- Low Efficiency of Intermediate Cooler: If the cooler’s heat dissipation efficiency is low or scale builds up, exhaust temperature will rise.
- Excessive Compression Ratio: If the compression ratio is too high, it will lead to an increase in exhaust temperature.
Solutions:
- Optimize Cooling System: Regularly acid wash the cooler and monitor the flow and temperature of the cooling water to ensure good heat dissipation.
- Adjust Interstage Pressure: Control the compression ratio of each stage through valve adjustments to avoid overloading in any stage and reduce exhaust temperature.
6. Maintenance and Prevention Strategies
6.1 Scientific Maintenance Cycle
- Daily Inspection: Regularly record parameters such as oil pressure, temperature, and vibration to detect abnormalities and ensure optimal equipment performance.
- Planned Major Overhaul: Perform a full inspection every 12-18 months, checking key components and replacing wear-prone parts (such as gas valves and piston rings).
6.2 Spare Parts Quality Control
- Material Certification: Key components such as crossheads and crankshafts should be made of high-quality forged steel with an inspection report to ensure component strength and durability.
- Dimensional Precision: All parts should meet the strict dimensional tolerances in the drawings to ensure good fit and sealing performance.
6.3 Operator Training
- Standardized Operation: Develop detailed operating manuals to ensure that operators follow procedures for startup and shutdown to prevent liquid hammer and other issues.
- Emergency Drills: Regularly conduct emergency drills, especially for hydrogen leaks and fires, ensuring operators are familiar with emergency response procedures.
7.Conclusion
By systematically addressing common hydrogen compressors’ failures, MINNUO can significantly extend the lifespan of their equipment, enhance production efficiency, and ensure the safety of their operations. Through regular maintenance, proper lubrication, and timely repairs, the risk of unexpected downtime can be minimized.