Valves, as core components in industrial equipment controlling fluid flow, play a crucial role in system safety and efficiency. In this article, we will analyze the common causes of valve leakage and provide targeted solutions to help users quickly identify and fix these issues.
Valve leakage is usually caused by factors such as casting defects, low-temperature freezing cracks, welding flaws, external damage, unsuitable packing, valve stem wear, and sealing surface issues. Solutions include optimizing casting processes, anti-freezing protection, standardized welding procedures, preventing mechanical damage, correct selection, regular maintenance, precision grinding, and repairing seal ring connections.
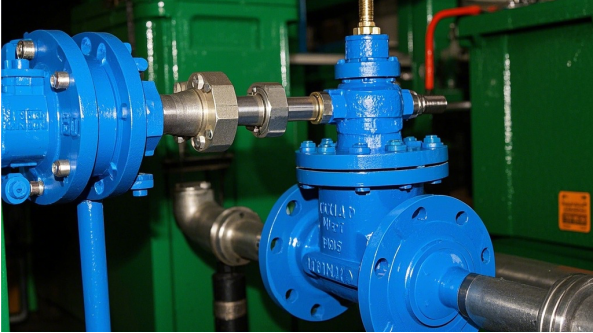
1. Causes and Solutions for Leakage Between Valve Body and Valve Cover
Common Causes:
- Casting Defects: Improper control during the casting of the valve body or cover can result in sand holes, loose structure, or slag inclusion. Sand holes form when gas trapped in molten metal fails to escape during cooling; loose structure occurs when metal grains grow unevenly during solidification, causing local areas of porosity; slag inclusion is the result of impurities mixing into the cast during manufacturing, weakening the structure.
- Low-Temperature Freezing Cracks: In cold environments, if the valve is not protected, residual water inside may freeze and expand. If the expansion exceeds the valve body or cover’s tolerance, it will crack the valve.
- Welding Flaws: When welding the valve body and cover, poor techniques may result in slag inclusion, incomplete fusion, or stress cracks. Slag inclusion is when residual slag remains in the weld, incomplete fusion occurs when the base material does not fully melt, and stress cracks arise due to residual thermal and structural stresses in the weld or heat-affected zone.
- External Damage: Impact during transportation, installation, or usage can damage the valve’s structural integrity. Large-diameter valves are more fragile and prone to cracking if struck by heavy equipment during installation.
Solutions:
- Optimize Casting Process: Selecting high-quality castings is key to valve quality. Conduct strength tests before installation using hydraulic and air pressure tests. The hydraulic test fills the valve with liquid under pressure to check for leakage and structural deformation, while the air pressure test uses compressed air to evaluate sealing performance and strength.
- Anti-Freezing Protection: In environments below 0°C, the valve should be insulated or heated using materials like rock wool or polyurethane foam. If the valve is out of service, residual water should be drained using a drain valve or disassembled parts.
- Standardize Welding Procedures: Welding should follow established standards, with professional certification required for welders. Post-weld testing such as radiographic inspection can identify porosity, slag inclusion, and cracks, while ultrasonic testing uses sound waves to detect weld defects.
- Prevent Mechanical Damage: For large-diameter valves, install dedicated supports based on the valve’s weight, size, and installation environment. Avoid placing heavy objects around the valve.
Emergency Repair Techniques:
- Low-Pressure Minor Leakage: Fast-setting adhesives can be used to seal minor leaks. Clean the surface, remove impurities, and apply the adhesive evenly before allowing it to cure. Alternatively, use a nut and drainage welding method to direct fluid away from the leak and then weld it shut, removing the nut after completion.
- High-Pressure Major Leakage: Use drainage welding or isolation valve + pipeline welding combinations. Drain the high-pressure fluid to a safe location before welding, or isolate the valve with a shut-off valve, bypassing it with temporary piping while repairing the leak. Apply rubber gaskets to sealing surfaces for enhanced sealing.
2. Handling Leakage at the Valve Packing
Leakage Causes:
- Inappropriate Packing Material: Different industrial media have varying chemical properties, temperatures, and pressures. If the packing material is incompatible, it may corrode, soften, or harden. For example, ordinary rubber packing used for corrosive media will quickly deteriorate, and packing that can’t withstand high temperatures or pressures will lose elasticity.
- Improper Installation: If the packing is not tightly installed or the number of rings is insufficient, sealing will be ineffective. The joints should be tightly connected, and the number of packing rings should match the valve specifications and working conditions.
- Valve Stem Wear: Over time, friction between the valve stem and packing, combined with media corrosion, can lead to wear. A rough stem surface will not form a tight seal with the packing. Damage to the pressure bonnet or excessive force during valve operation can also deform the packing and compromise its sealing ability.
Professional Solutions:
- Correct Material Selection: Choose corrosion-resistant and temperature-resistant packing based on the medium’s characteristics. For high-temperature and high-pressure corrosive media, graphite packing is suitable; for chemically stable media, PTFE packing is recommended.
- Standardized Installation: Tighten the packing ring progressively, ensuring a 30° – 45° angled joint to minimize leakage risks. The pre-tightening gap of the bonnet should be ≥5mm for easy adjustment during operation.
- Regular Maintenance: Replace aging packing promptly, inspect for valve stem wear, and polish lightly if the wear is slight; replace it if severe. Damaged bonnet bolts should also be replaced in a timely manner.
- Operator Training: Train valve operators to turn the handwheel smoothly, avoid excessive force, and emphasize proper operational procedures to prevent mechanical deformation that affects sealing.
3. Sealing Surface Leakage: Repair and Prevention
Problem Diagnosis:
- Sealing Surface Quality Issues: If the sealing surface is not finely ground during manufacturing, it may be uneven and fail to form a complete seal. The material may also fail to withstand corrosion, wear, and pressure impacts, leading to leakage.
- Valve Stem Assembly Issues: Incorrect assembly of the valve stem and closure part may cause misalignment, leading to uneven stress on the sealing surface, resulting in localized leakage.
- Gasket Issues: Over time, gaskets can degrade due to corrosion, temperature fluctuations, and pressure changes, losing elasticity and sealing ability. Improper alignment during installation also reduces their sealing effect.
Solutions:
- Precision Grinding: Regrind the sealing surface using professional tools and grinding agents, and check the fit using a dye to ensure continuous sealing lines for optimal sealing performance.
- Component Alignment: Adjust the valve stem and closure part connection, ensuring that the components are securely fitted and that the closure part aligns accurately with the sealing surface.
- Gasket Management: Choose appropriate gaskets based on the valve’s operating conditions, ensuring proper alignment with the sealing surface and evenly tightening bolts. Never use double gaskets, as this can lead to uneven sealing pressure and reduce performance.
4. Sealing Ring Connection Leakage Solutions
Common Failures:
- Installation and Connection Issues: Sealing rings may not be tightly pressed during installation, or connections may not align properly. Poor welding quality, including holes, incomplete fusion, or defects, can weaken the connection and sealing. Loose threads at connection points can affect the sealing ring’s performance.
- Medium Corrosion: Long-term exposure to media can cause corrosion of connection surfaces, particularly with highly corrosive substances that quickly degrade surface structures, leading to pits or holes and causing leaks.
Repair Methods:
- Welding and Bonding: For defective welds, clean the surface of impurities and oil before selecting appropriate welding materials and techniques. Small defects can be repaired with sealant, which forms a tight seal once cured. Loose screws should be replaced and tightened according to the specified torque.
- Anti-Corrosion Treatment: If the connection surface is corroded, grind away the damaged layer and impurities to restore smoothness. If the corrosion is severe and grinding is not possible, replace the sealing ring and apply corrosion protection treatments to the connection surface, such as anti-corrosion coatings or corrosion-resistant linings, to extend the sealing ring’s lifespan and enhance sealing performance.
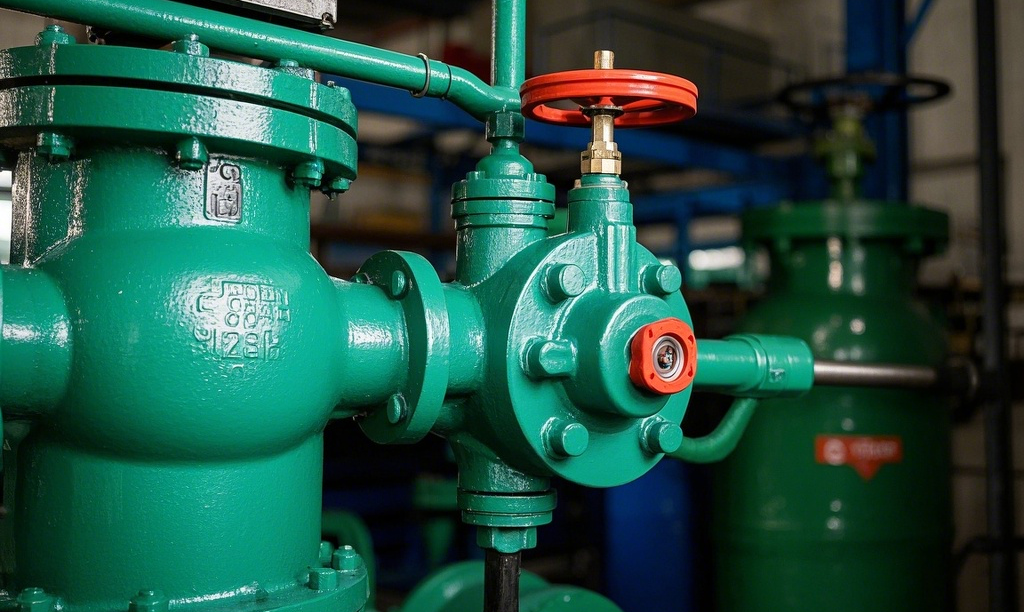
5. Emergency Response to Closure Part Detachment Leading to Leakage
Cause Analysis:
- Excessive Operation: Over-tightening the valve closure can place excessive pressure on the closure part, leading to damage and detachment. Opening the valve beyond the upper dead point can cause excessive displacement of the closure part, leading to detachment and leakage.
- Connection Part Issues: Connection parts may wear out from frequent use, weakening the joint and leading to detachment due to material wear or corrosion.
Countermeasures:
- Standardize Operations: Operators should follow proper procedures, operate valves smoothly, and slightly reverse the handwheel when fully open to avoid detaching the closure part from excessive opening.
- Strengthen Connections: Add anti-reversal components, such as stop pins or anti-reversal nuts, to enhance connection stability. Use high-strength, corrosion-resistant fasteners to improve wear and corrosion resistance.
6. MINNUO’s Professional Recommendations
Key Maintenance Points:
- Regular Inspections: Develop a regular inspection schedule to check the valve body, packing, and sealing surfaces. Ensure timely detection of cracks, leaks, wear, and other issues, and address them promptly.
- Adapt to Working Conditions: Choose materials based on valve pressure, temperature, and medium properties. Use high-temperature, high-pressure, and oxidation-resistant materials for steam environments; for corrosive media, select special corrosion-resistant materials to ensure stable valve operation in complex conditions.
- Operator Training: Train operators on valve structure, operation methods, maintenance procedures, and common failure handling. This will improve operational skills and safety awareness, avoiding mechanical damage and prolonging the valve’s lifespan.
Why Choose MINNUO?
MINNUO, as a leading brand in compressor and fluid control solutions, uses high-precision casting techniques to reduce defects and employs aerospace-grade sealing technology to enhance sealing performance. Customized valves are available based on customer needs to meet specific working conditions. MINNUO also provides full lifecycle technical support, offering guidance from selection to installation, use, and maintenance, helping customers address potential leakage risks.
7. Conclusion
To effectively address valve leakage issues, companies must enhance daily inspections and maintenance to ensure operators understand best practices for proper handling.
Click on MINNUO to get your personalized solution!