The air compressor is the core equipment in industrial production, known as the “lungs” of the enterprise, providing a steady stream of power for the production line. However, cooling system failure is one of the common problems in the operation of the air compressor. If the air compressor cooling system fails, the equipment temperature will rise rapidly, affecting production efficiency, and may even cause frequent failures or equipment damage. This article will analyze the common causes of air compressor cooling failure in detail and provide effective solutions to help companies ensure the stable operation of air compressors.
Failures in the air compressor cooling system are common in insufficient cooling water, fan failure, blockage, fan shortage and other problems, which will cause the equipment temperature to rise and affect clean production efficiency. Solutions include ensuring cooling water supply, regular maintenance of cooling fans, and maintenance of cooling fans. Through daily maintenance, companies can effectively prevent cooling failures, extend the service life of air compressors and ensure the stable operation of production lines.
Ⅰ.Main causes of air compressor cooling failure
Cooling failures in the air compressor cooling system may be caused by a variety of reasons, including insufficient cooling water, fan failure, blockage, insufficient refrigeration, temperature control valve failure, cooling pipe blockage and cooler damage. In-depth analysis of the causes.
1.Insufficient cooling water or poor water quality
In water-cooled air compressors, cooling water is essential and flows through various parts of the system to take away the remaining heat. However, when the amount of cooling water is insufficient, the cooling effect of the equipment is greatly reduced, resulting in a rise in temperature. In addition, cooling water with poor moisture may have supplements and accidents, which will deposit in the cooling pipe to form scale blockages, affecting the circulation and efficiency of the cooling system.
2.Fan failure
For air-cooled air compressors, the cooling fan is a key fan component. The fan takes away the heat generated by the equipment by accelerating air circulation. When the cooling fan fails (such as motor damage, fan fan or bearing aging), the air volume will be significantly reduced, and the expected final effect cannot be achieved, resulting in an increase in the temperature of the air compressor.
3.Dust accumulation on the radiator
The radiator is one of the core components of the air compressor cooling system. It reduces the heat generated by the equipment by cooling the air flowing through it. However, as the equipment runs for a long time, dust, dirty oil, etc. are easily accumulated on the surface of the radiator. Fatally, these substances hinder the air circulation, resulting in a decrease in cooling effect and an increase in equipment temperature.
4.Insufficient coolant or lubricating oil
Coolant and lubricant play a dual role of cooling and lubrication in the air compressor. When the coolant or lubricant is insufficient, the temperature of the equipment will rise rapidly, causing the cooling system to fail. In addition, the quality and viscosity of the lubricant. Poor-quality lubricants affect the cooling effect, and poor-quality lubricants may cause cooling failures and high-temperature problems in the booster equipment.
5.Temperature control valve failure
The temperature control valve is used to automatically adjust the temperature of the coolant or lubricant to ensure that the air compressor temperature operates within a reasonable range. If the temperature control valve fails (such as stuck or malfunctions), the flow of coolant or lubricant is blocked, resulting in reduced cooling effect and increased equipment temperature.
6.Pipeline blockage or damage
The pipeline is a cooling channel for the flow of coolant. If the pipeline is blocked, the unsmooth flow of coolant will directly affect the cooling effect. In addition, aging and corrosion of the cooling pipeline may cause water leakage or seepage, causing the coolant to lose and reduce the cooling effect of the equipment.
7.Cooler damage
The cooler is the core component of the air compressor cooling system. Cooler failure, seal failure or surface corrosion will cause a sharp drop in cooling efficiency. Damage to the cooler may cause coolant leakage, resulting in the air compressor temperature out of control.
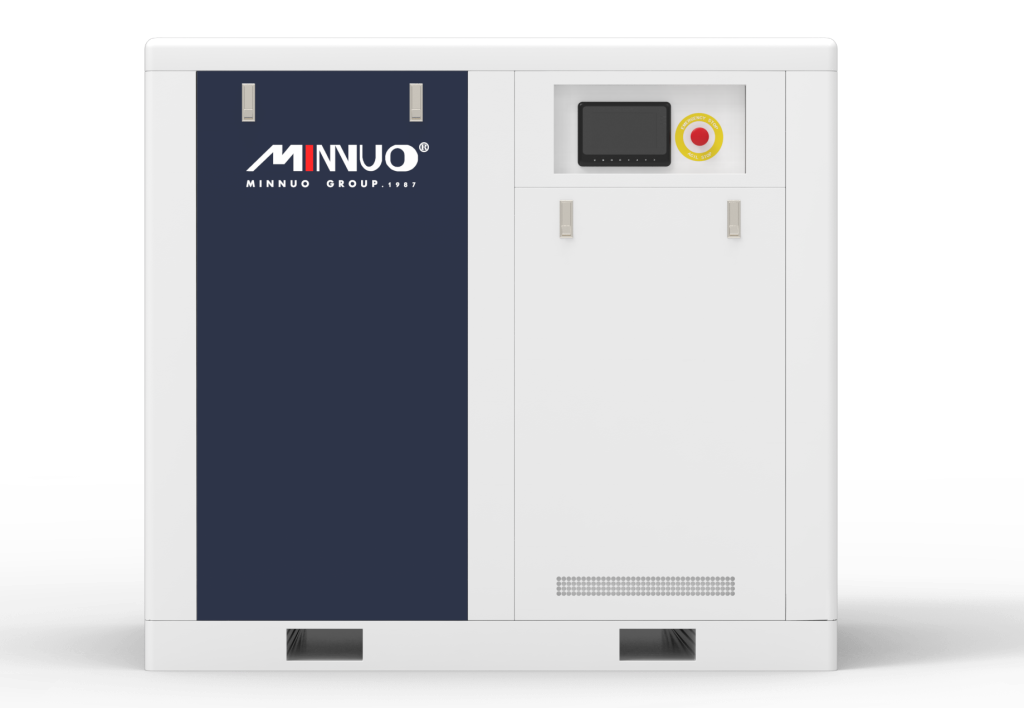
Ⅱ.Solutions to air compressor cooling failures
Depending on the different causes of the failure, the following are effective solutions that will help companies improve the efficiency of the cooling system and ensure the stable operation of the air compressor.
1.Ensure adequate cooling water supply and improved water quality
For water-cooled air compressors, the supply and quality of cooling water directly affect the cooling effect of the equipment.
- Check the water volume:Ensure the supply of cooling water, especially in hot weather or high-load operation, the water volume should be kept stable.
- Improve water quality:Poor water quality can easily lead to scaling in the pipeline. You can purify the water quality by installing filters or softening water equipment, reduce scale deposition, and ensure the cooling effect.
- Regularly replace cooling water:Long-term use of cooling water will drop sharply, affecting the smoothness of the cooling system. It is recommended to replace cooling water regularly to keep the cooling system clean.
2.Regular maintenance
In air-cooled air compressors, cooling fans play an important role. Regular maintenance of fans can ensure their normal operation.
- Check the motor and blades:The motor and blades of the cooling fan are prone to damage or wear during long-term use. The motor status needs to be checked regularly to ensure normal operation.
- Clean the blades:Dust accumulation on the blades will cause a decrease in air volume. Cleaning the blades will help maintain the air volume and improve the cooling effect.
- Replace aging parts:For aging or fatigued fan bearings, fans and other parts, it is recommended to replace them regularly, and the fan will fail.
3.Clean the blockage regularly to ensure good ventilation
Blockage is a common cause of cooling failure. Regular cleaning of blockage helps to improve the blocking effect.
- Clean the surface:Use compressed air or a soft brush to clean the regrets and hazards on the surface to ensure air circulation and improve fundamental work efficiency.
- Check the static state:If aging, corrosion, etc. are recommended, replace the static state in time to ensure the stability of the effect.
- Avoid bleaching detergents:During the cleaning process, avoid using detergents containing bleach to avoid damage to the material.
4.Replenish coolant and lubricating oil to keep the liquid level stable
Liquid and lubricating oil are essential for the cooling and lubrication of air compressor coolers, and their sufficient supply should be guaranteed.
- Check the oil level regularly:Ensure that the lubricating oil and coolant levels are within the normal range. When the oil is insufficient, it should be replenished in time.
- Use high-quality lubricating oil:High-quality lubricating oil has better cooling and lubricating effects. It is recommended to choose lubricating oil that meets the requirements of the equipment. The cooling effect of the area is reduced.
- Select viscosity according to the environment:In high or low temperature environments, select suitable viscosity to ensure that the lubricating oil can effectively play a cooling effect at various temperatures.
5.Detect the working status of the temperature control valve
The temperature control valve plays an important regulating role in the air compressor cooling system. Regularly checking the status of the temperature control valve helps to maintain the stability of the cooling system.
- Check whether the temperature control valve is stuck:A stuck temperature control valve will affect the flow of coolant or lubricating oil. It is recommended to clean or replace the temperature control valve regularly to ensure normal temperature regulation of the equipment.
- Replace aging temperature control valve:The next temperature control valve may fail and should be replaced in time to ensure the cooling effect.
6.Clean the cooling pipe and keep it unobstructed
The unobstructed cooling of the pipe directly affects the flow of coolant. Regular cleaning of the pipe can ensure the normal operation of the system.
- Clean the pipes regularly:Use professional cleaning or high-pressure water to clean the cooling system to ensure that there are no faults in the pipes and that the coolant flows smoothly.
- Check the sealed pipes:If water leakage or seepage is found in the pipes, they should be repaired or replaced in time to prevent the loss of coolant.
- Anti-corrosion treatment:Adding preservatives to the pipe cooling can prevent the coolant from corroding the pipes and extend the service life of the pipes.
7.Regularly check and maintain the cooling device
The cooler is an important component of the air compressor cooling system. Its damage will cause the cooling system to fail. The cooler needs to be checked and maintained regularly.
- Clean the surface of the cooler:Grease and oil stains are easily accumulated on the surface of the cooler. It should be cleaned regularly to maintain a good cooling effect.
- Repair or replace damaged cooling devices:If there are gaps or leaks in the cooling device, it should be repaired or replaced immediately to ensure the normal operation of the cooling system.
- Check the sealing:The sealing of the cooler is related to the leakage of the coolant. Check the sealing condition regularly to prevent the leakage of the coolant.
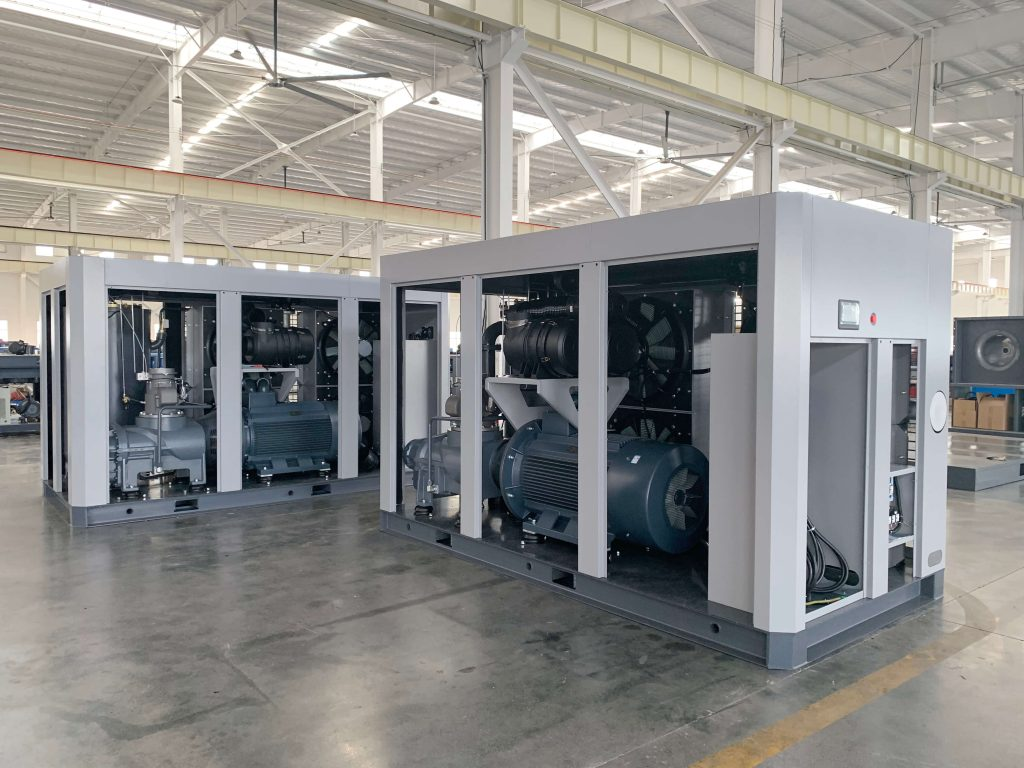
Ⅲ.Daily maintenance suggestions for the air compressor cooling system
In order to prevent the occurrence of cooling failures, enterprises need to strengthen the daily maintenance of the air compressor cooling system. Here are some practical maintenance suggestions:
1.Regularly inspect the cooling system
inspect key components such as cooling water, fans, and fans every week or every month to ensure that the equipment is in good condition.
2.Establish a maintenance log
record the operation time of each replacement of coolant, lubricating oil, cleaning cooler, etc. in detail, and establish equipment maintenance files for subsequent analysis.
3.Keep the system clean
regularly clean the cooling stop, cooling pipes and cooling fans to ensure that the cooling system is unobstructed and avoid syrup effects.
4.Regularly replace key components
regularly replace key components such as thermostats and coolers according to usage and equipment load valves to avoid cooling system failures due to aging or failure.
Ⅳ.Conclusion
Air compressor cooling failure is a key factor in the operating efficiency and continuous operation of cooling equipment. By strengthening water supply and moisture management, regularly cleaning the impact, maintaining cooling fans, checking the lubricating oil level, and keeping the cooling pipes unobstructed, enterprises can effectively prevent the occurrence of cooling system failures and ensure long-term and stable operation of air compressors. If you still have unclear questions, please leave a message on our MINNUO official website. We are always ready to serve you.