As a core component of compressed air systems, the operational condition of air receivers directly impacts the stability of the entire system and the operational costs of enterprises. Once corrosion affects the air receiver, it not only shortens the equipment’s service life but may also lead to safety hazards, causing production interruptions. This article will delve into the causes, mechanisms, and practical prevention strategies for air receiver corrosion.
Corrosion in air receivers is primarily caused by metal oxidation and electrochemical reactions. Common types of corrosion include dry atmospheric corrosion, wet atmospheric corrosion, and visible liquid film corrosion. Factors influencing corrosion include humidity, pollutants, temperature fluctuations, microorganisms, and design flaws. Protective measures include selecting corrosion-resistant materials, applying multi-layer protective coatings, controlling environmental humidity and pollutants, implementing cathodic protection, intelligent monitoring of corrosion rates, and regular maintenance.
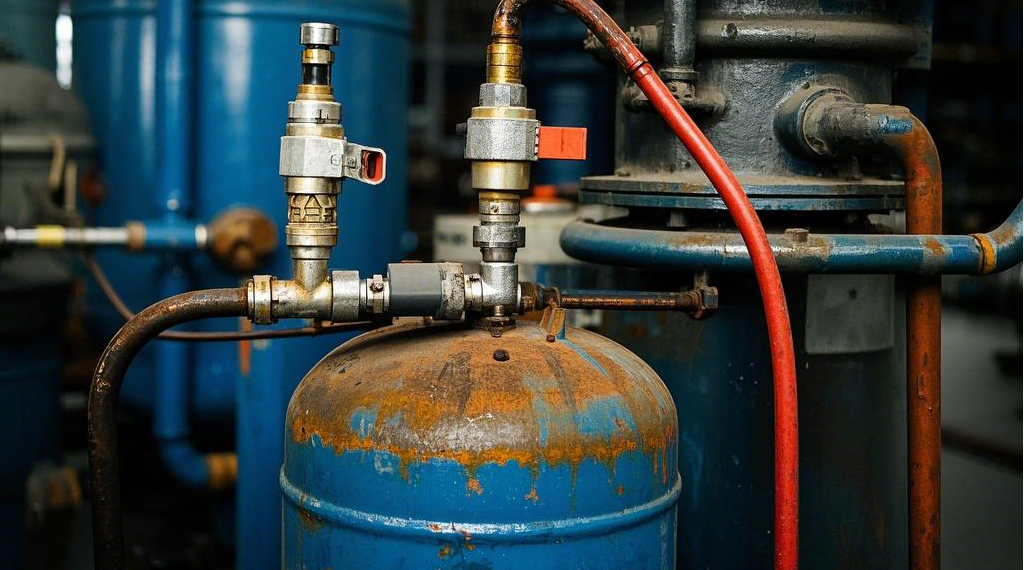
1. Nature of Air Receiver Corrosion: Coupling of Metal Oxidation and Electrochemical Reactions
Air receivers are typically made of metal materials such as carbon steel or stainless steel. The essence of corrosion is the oxidation reaction of metals under specific environmental conditions. Taking a common carbon steel air receiver as an example, the corrosion process can be simplified as the following chemical reaction:
4Fe + 3O₂ + 6H₂O → 4Fe(OH)₃ → 2Fe₂O₃・H₂O (rust)
From this reaction, it is clear that water (H₂O) and oxygen (O₂) are necessary conditions for corrosion. When acidic pollutants such as sulfur dioxide (SO₂) and chloride ions (Cl⁻) are present in the environment, they significantly accelerate the reaction rate, speeding up the corrosion process of the air receiver. According to ISO 12944 “Paints and varnishes — Corrosion protection of steel structures by protective paint systems,” the corrosion category of air receivers is classified from C1 (low corrosion) to C5 (very high corrosion) based on environmental conditions. Different corrosion categories correspond to different protection requirements and maintenance strategies, and enterprises need to accurately assess and take appropriate measures based on actual conditions.
2. Three Types of Air Receiver Corrosion and Their Mechanisms
(1) Dry Atmospheric Corrosion: Limited Protection of Passive Films
In environments with relative humidity (RH) below 60%, a nanoscale oxide film, such as Fe₃O₄, naturally forms on the metal surface, typically 2 to 4 nanometers thick. This oxide film can temporarily protect the metal and delay corrosion. However, when dust or industrial particles (PM2.5 and above) are present in the air, these impurities can disrupt the integrity of the oxide film, leading to the formation of local microcells and increasing the risk of pitting corrosion. According to ASTM G50 “Standard Practice for Conducting Atmospheric Corrosion Tests on Metals,” in such dry atmospheric environments, the annual corrosion rate of air receivers is generally less than 0.1 mm. Although the corrosion rate is relatively low, long-term accumulation can still have a significant impact on the performance of air receivers.
(2) Wet Atmospheric Corrosion: Electrochemical Corrosion Under Thin Liquid Films
When the environmental relative humidity (RH) exceeds 65%, a thin electrolyte film, approximately 10 to 100 μm thick, gradually forms on the metal surface. At this point, the corrosion process follows typical electrochemical principles:
Anode reaction: Fe → Fe²⁺ + 2e⁻
Cathode reaction: O₂ + 2H₂O + 4e⁻ → 4OH⁻
If sulfur dioxide (SO₂) is present in the environment, it quickly dissolves in water to form sulfurous acid (H₂SO₃), lowering the pH of the solution and accelerating the anode dissolution process. The specific reaction is:
SO₂ + H₂O → H⁺ + HSO₃⁻.
Experimental data show that when the SO₂ concentration increases from 10 ppm to 50 ppm, the corrosion rate of carbon steel can increase by 3 to 5 times. This type of wet atmospheric corrosion is common in industrial environments and poses a significant threat to air receivers, requiring close attention.
(3) Visible Liquid Film Corrosion: Synergistic Effects of Erosion and Local Acidification
In cases of rainwater or condensate accumulation, when the liquid film thickness exceeds 1 mm, the corrosion of air receivers exhibits two significant characteristics:
- Erosion Corrosion: The scouring action of high-speed water flow gradually strips away the protective layer on the metal surface, exposing fresh metal to the corrosive environment and causing continuous oxidation. For example, in some outdoor air receivers, heavy rain can accelerate corrosion due to rapid water flow.
- Acidic Deposition: Industrial pollutants such as nitrogen oxides (NOx) and sulfur dioxide (SO₂) dissolve in water to form nitric acid (HNO₃) and sulfuric acid (H₂SO₄), lowering the local pH to below 4 and causing severe corrosion. In such cases, the annual corrosion rate of air receivers can reach 0.5 to 1 mm, causing significant damage to the equipment. For example, air receivers near chemical plants often face corrosion issues due to acidic deposition from industrial emissions.
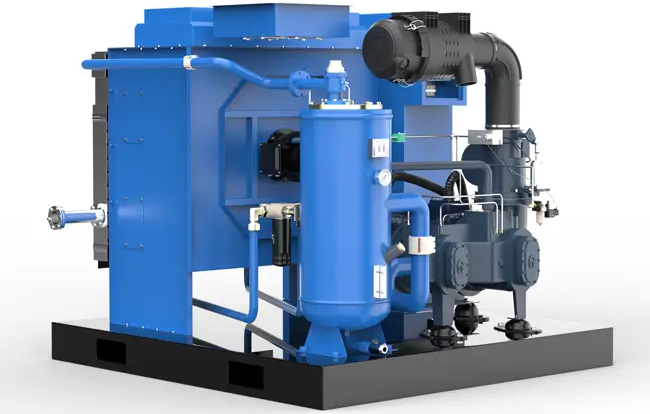
3. Six Environmental Factors Affecting Air Receiver Corrosion
(1) Humidity and Dew Point Temperature: Critical Thresholds for Corrosion
According to NACE SP0169 “Control of External Corrosion on Underground or Submerged Metallic Piping Systems,” maintaining the environmental temperature at least 3°C above the dew point can effectively prevent condensate formation, thereby reducing the risk of air receiver corrosion. MINNUO recommends that enterprises control environmental humidity below 60% and use dew point sensors for real-time monitoring to promptly detect and address humidity anomalies. For example, in some humid coastal areas, enterprises have successfully reduced air receiver corrosion rates by installing dehumidifiers and dew point sensors.
(2) Synergistic Effects of Industrial Pollutants (SO₂, NOx, H₂S)
- SO₂: Sulfur dioxide reacts with iron (Fe) to form FeSO₄・7H₂O (green rust), which causes coating delamination due to volume expansion, thereby compromising the protective effect of the coating. For example, near coal-fired power plants, the coatings on air receivers are often damaged due to high SO₂ emissions.
- Cl⁻ (Marine Environment): In marine environments, high chloride ion (Cl⁻) content can disrupt the passive film on the metal surface, leading to pitting and stress corrosion cracking (SCC). For example, air receivers on offshore oil platforms are often subject to pitting and cracking due to chloride ion erosion from seawater mist.
- H₂S: Under anaerobic conditions, hydrogen sulfide (H₂S) reacts with iron to form FeS, which not only roughens the metal surface but also increases the risk of hydrogen embrittlement. In some oil and gas extraction and processing enterprises, the presence of H₂S poses a serious threat to the safe operation of air receivers.
(3) Temperature Fluctuations and Condensation Cycles
When the daily temperature fluctuation exceeds 10°C, the inner walls of air receivers undergo repeated condensation-evaporation cycles, creating alternating wet-dry conditions. This frequent change accelerates corrosion, as metals are prone to electrochemical corrosion in wet conditions, and corrosion products accumulate during the drying process, further damaging the protective layer on the metal surface. For example, in some inland areas with large daily temperature fluctuations, air receiver corrosion is more severe.
(4) Microbiologically Influenced Corrosion (MIC): A Hidden Threat
In specific industries such as oil, gas, and wastewater treatment, sulfate-reducing bacteria (SRB) can reduce sulfate ions (SO₄²⁻) to hydrogen sulfide (H₂S), lowering the local pH and causing hydrogen-induced cracking. This type of microbiologically influenced corrosion is often hidden and not easily detected in its early stages, but once it occurs, it can be highly destructive. For example, in some wastewater treatment plants, severe corrosion perforations have occurred in air receivers due to microbial growth.
(5) Design Flaws: Breeding Grounds for Crevice Corrosion
Poor welding quality and insufficient sealing at flange connections can create oxygen concentration cells inside air receivers, leading to crevice corrosion. The depth of crevice corrosion can be up to 5 times that of uniform corrosion, causing significant damage to the structural strength of air receivers. For example, some small enterprises have experienced frequent crevice corrosion in air receivers due to neglect of welding and sealing processes during manufacturing.
(6) Improper Operation and Maintenance: Human-Accelerated Corrosion
- Failure to Regularly Drain Condensate: Condensate accumulated in air receivers typically has a pH below 5 and is acidic. Long-term failure to drain it can cause severe corrosion to the tank. For example, some enterprises, due to a lack of regular maintenance awareness, have experienced severe bottom corrosion in air receivers due to long-term water accumulation.
- Use of Chlorinated Cleaners or Unneutralized Acidic Solutions: Using chlorinated cleaners or unneutralized acidic solutions during cleaning or maintenance can directly corrode the metal surface, accelerating the corrosion process. For example, one enterprise used undiluted and unneutralized acidic cleaner to wash an air receiver, resulting in widespread surface corrosion.
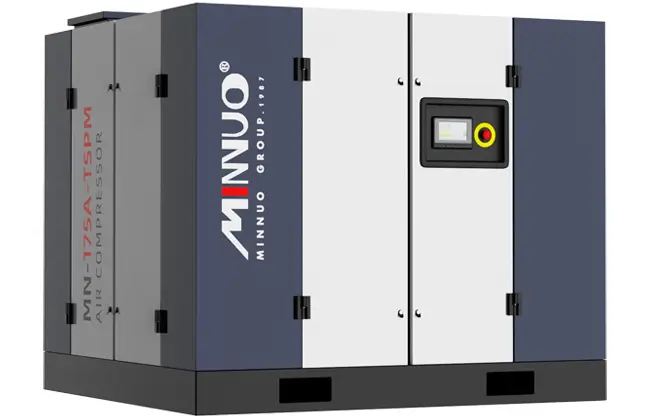
4. Air Receiver Corrosion Protection Measures — Six-Level Protection System
(1) Material Selection: Enhancing Corrosion Resistance from the Source
- Carbon Steel Tanks: For general applications, Q345R low-alloy steel (compliant with GB/T 713 standards) is recommended, as it offers 30% better corrosion resistance in atmospheric environments compared to Q235B. This makes Q345R low-alloy steel air receivers more effective in resisting corrosion and extending service life under the same conditions.
- High-End Applications: For high-end applications with stringent anti-corrosion requirements, S31603 stainless steel (containing 16% Cr, 10% Ni, 2% Mo) is a suitable choice due to its excellent corrosion resistance. Additionally, MINNUO’s patented coating steel, using nano-ceramic composite coating technology, offers over 2000 hours of salt spray corrosion resistance, providing a superior material choice for high-end air receivers.
(2) Surface Engineering: Multi-Layer Protective Coating System
- Primer: Use zinc-rich epoxy primer with over 80% zinc content, providing the first layer of protection through cathodic protection principles. Even if the coating is locally damaged, zinc will corrode preferentially, protecting the underlying metal.
- Intermediate Coating: Choose epoxy mica iron red paint, which fills the pores in the primer, enhances inter-coating adhesion, and further blocks the intrusion of corrosive media.
- Topcoat: Use polyurethane or fluorocarbon paint, which offers excellent resistance to UV and chemical erosion, effectively protecting the underlying coatings and extending the service life of the entire coating system. For air receivers in ISO 12944 C4 and above corrosion environments, the total coating thickness should exceed 200 μm to ensure adequate protection.
(3) Environmental Control: Active Management of Humidity and Pollutants
- Install Smart Dehumidifiers: By installing smart dehumidifiers, maintain environmental relative humidity below 50%, effectively reducing humidity-induced corrosion risks. Smart dehumidifiers can automatically adjust their operation based on environmental humidity, ensuring it remains within an optimal range.
- Add Activated Carbon + HEPA Filters at Air Inlets: Installing activated carbon and high-efficiency particulate air (HEPA) filters at air inlets can effectively remove pollutants such as sulfur dioxide (SO₂) and chloride ions (Cl⁻) from the air, with removal efficiency exceeding 95%. This significantly reduces the entry of corrosive substances into the air receiver, protecting the tank from erosion.
(4) Cathodic Protection: The Ultimate Electrochemical Barrier
- Sacrificial Anodes: Install magnesium alloy anodes at the bottom of the air receiver, configured at 0.5 kg per cubic meter of volume. Magnesium alloy anodes have a more negative potential than the air receiver metal, so they corrode preferentially during electrochemical corrosion, protecting the air receiver body.
- Impressed Current: For large air receivers, impressed current cathodic protection is more suitable. Using a potentiostat, maintain the tank potential between -0.85 to -1.05 V (relative to a Cu/CuSO₄ electrode), ensuring the tank remains under cathodic protection during electrochemical corrosion.
(5) Intelligent Monitoring: Real-Time Corrosion Rate Alarms
- Online Corrosion Probes: Utilize online corrosion probes using electrical resistance (ER) or linear polarization resistance (LPR) technology to collect real-time corrosion data from air receivers and transmit it to a monitoring system. If the corrosion rate exceeds a set threshold, the system immediately alerts staff to take action.
- Ultrasonic Thickness Measurement: Conduct quarterly ultrasonic thickness scans on high-risk areas of air receivers, such as welds and bottoms, with measurement accuracy up to ±0.1 mm. Regular monitoring of tank thickness changes helps identify potential corrosion issues early, providing accurate data for maintenance decisions.
(6) Lifecycle Maintenance: MINNUO “5S” Service Standards
- Cleaning: Annually clean the internal surfaces of air receivers with high-pressure water to remove accumulated dirt, impurities, and corrosion products, maintaining internal cleanliness and reducing corrosion risks.
- Inspection: Use endoscopes to conduct comprehensive internal inspections of air receivers, promptly identifying potential corrosion, cracks, and other defects to ensure safe operation.
- Sealing: Fill local corrosion pits with epoxy resin to prevent further corrosion and restore tank integrity.
- Coating: Recoat the protective layer of air receivers every 5 to 8 years based on actual usage, ensuring the coating’s protective performance remains in good condition.
- Summary: Annually generate detailed corrosion assessment reports, comprehensively analyzing and summarizing the corrosion status of air receivers, and optimizing prevention strategies based on assessment results to continuously improve protection effectiveness.
5. Conclusion
At MINNUO, we firmly believe that technological innovation and attention to detail are the core of long-term product value. We remain committed to providing global customers with efficient, safe, and durable compressor systems and anti-corrosion solutions, continuously promoting the sustainable development of industrial equipment.
What are you waiting for? Come to MINNUO to experience high-quality products and professional services!