As an indispensable core equipment in modern industrial production, the compressor undertakes many key tasks. However, with long-term high-load operation, wear or damage of the compressor host is almost inevitable. At this time, enterprises often face the decision of whether to refurbish the compressor host. Can refurbishment restore the performance of the equipment? Can it save costs and extend the service life for enterprises? This article will explore the feasibility of refurbishing the compressor host in depth and provide enterprises with a practical guide on how to judge whether to refurbish.
Whether the refurbishment of the compressor host is feasible depends on the degree of damage, the availability of parts and the quality of refurbishment. The advantages of refurbishment are cost savings, extended equipment life, and compliance with environmental protection requirements. However, the performance after refurbishment may not be comparable to that of new equipment, and the quality depends on the technical level of the repairer. Enterprises should comprehensively consider factors such as economic evaluation, equipment age, and downtime tolerance, and choose the right time and repairer for refurbishment to ensure that the equipment restores optimal performance.
Common causes of damage to the compressor host
To determine whether to refurbish the compressor host, you first need to understand the cause of the damage to the host. The compressor operates in harsh environments for a long time, which is prone to various problems.
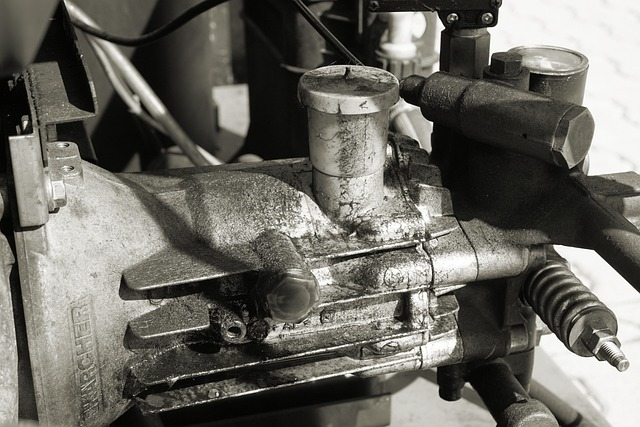
Mechanical wear
The piston, cylinder, valve and other parts of the compressor will wear out under long-term high-speed operation. Although this wear is usually slow, it may lead to problems such as reduced compression efficiency and increased operating noise over time, and even affect the overall performance of the equipment.
Overload operation
Overload operation is one of the common causes of damage to the compressor host. Long-term overload operation of the equipment will not only aggravate the wear of the parts, but also cause the oil temperature to rise, the sealing performance to decline, and even cause equipment failure. For those equipment that are frequently used and have a large load, the overload phenomenon is particularly serious.
Poor lubrication
Lubricating oil is the “blood” of the normal operation of the compressor. It can effectively reduce the friction between parts and take away heat. If the lubricating oil is insufficient or the quality is not up to standard, the internal parts of the compressor will accelerate wear due to excessive friction, and eventually cause equipment damage.
Contaminant entry
In some cases, external contaminants, such as moisture, dust, etc., may enter the compressor, causing corrosion or clogging of key components. In particular, moisture can cause metal parts to rust, seriously affecting the working efficiency and life of the equipment.
High temperature and humidity
Excessive temperature or humidity may cause damage to the compressor. High temperature can easily lead to aging of lubricating oil, while moisture can cause metal parts to rust, thus affecting the normal operation of the compressor.
Feasibility analysis of compressor host refurbishment
After the compressor host is damaged, the company often needs to determine whether to refurbish it. Can refurbishment restore the performance of the compressor and is it a cost-effective solution? This needs to be considered from multiple angles.
Extent of damage
Whether refurbishment is feasible depends first on the extent of damage to the compressor. If only some small parts are damaged, such as air valves, seals, bearings, etc., refurbishment is completely feasible. These parts are easy to replace, and the refurbished compressor can usually restore its original performance. However, if core parts, such as the compressor crankshaft, cylinder block, connecting rod, etc., are severely damaged or cracked, refurbishment may become unrealistic, or even impossible to restore the basic function of the compressor.
Availability of parts
If the compressor host has been discontinued for many years, parts may be difficult to find. In this case, refurbishment will face great challenges. Companies may need to rely on custom parts, which significantly increases costs and may bring risks to compatibility and quality.
Technical Support
Refurbishment is not as simple as replacing parts. It requires a professional technical team to conduct comprehensive inspections, repairs and precision adjustments. Therefore, it is critical to choose an experienced and technically competent maintenance company to ensure that the refurbished compressor is restored to its ideal state.
Advantages of compressor host refurbishment
Although refurbishment is not suitable for all situations, its advantages cannot be ignored, especially for companies that want to save costs and extend the service life of equipment.
Cost Savings
Compared to buying new equipment, the cost of refurbishing a compressor is obviously much lower. Companies do not need to bear the high purchase costs, transportation costs, and installation and commissioning costs of new equipment. The refurbished equipment can basically be restored to its original working performance, thereby significantly reducing the company’s capital expenditure.
Extended Service Life
After refurbishment, the key components of the compressor are repaired and replaced, and its performance is usually restored. In many cases, refurbished equipment works more stably and is even more reliable than equipment that has not been used for a long time. Through refurbishment, companies can not only extend the service life of equipment, but also avoid high maintenance costs caused by equipment failure.
Environmental protection and energy saving
An important advantage of refurbishing compressors is that it is an environmentally friendly choice. Through refurbishment, companies can reduce the generation of waste, save resources, and reduce the impact on the environment. Compared with scrapping old equipment, refurbishment is undoubtedly a greener alternative.
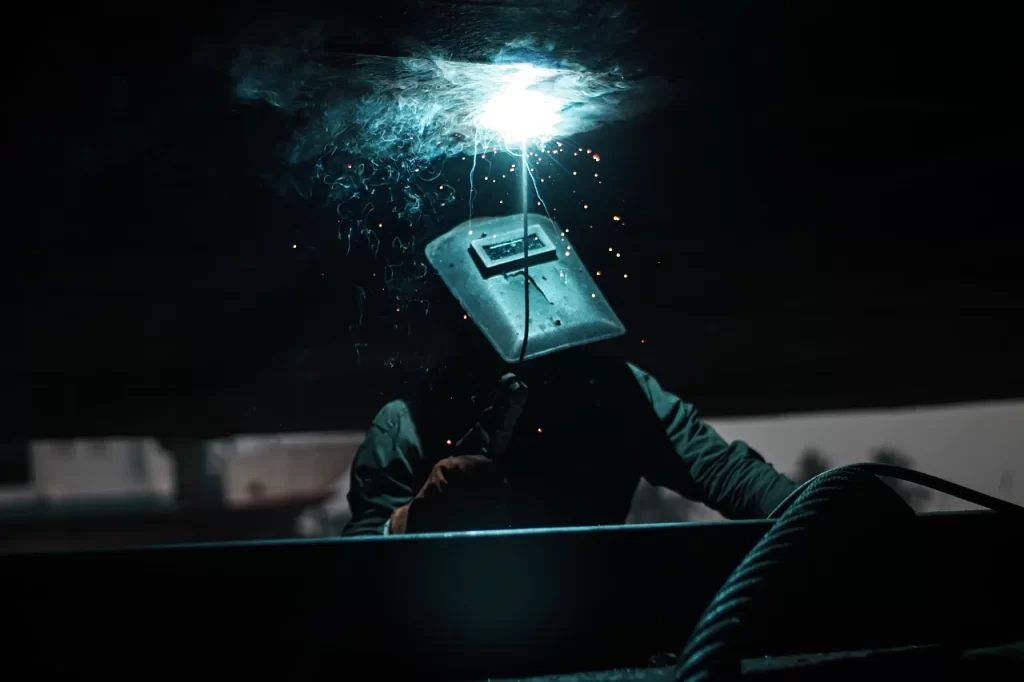
Limitations of compressor host refurbishment
Although refurbishment has many advantages, it also has certain limitations. Companies need to consider carefully when deciding whether to refurbish.
Limited refurbishment performance
Refurbished compressors are usually not restored to a brand new state. Even after precise repairs and adjustments, the performance and efficiency of old equipment may still be different from new equipment. For production lines that need to operate efficiently and stably, refurbishment may not meet high requirements.
Uncertain refurbishment quality
The quality of refurbishment is directly affected by the technical level of the repair shop. Choosing a repairer who is unprofessional or lacks experience in equipment repair may result in unsatisfactory refurbishment results and even affect the safety and long-term reliability of the equipment.
Long refurbishment cycle
Compared to buying new equipment, compressor refurbishment usually takes a longer period of time. Disassembly, inspection, repair and commissioning may take weeks or even longer. If the production line urgently needs the equipment to be put into use, the downtime required for refurbishment may affect the overall production efficiency.
How to decide whether to refurbish the compressor host?
When facing the decision of whether to refurbish the compressor host, enterprises can consider the following aspects:
Economic evaluation
First, enterprises need to evaluate the cost of refurbishment and the cost of purchasing new equipment. If refurbishment can significantly save expenses and the equipment can meet production needs after refurbishment, then refurbishment is obviously a more attractive option.
Equipment age and technology update
If the compressor equipment has been used for many years and the technology is outdated, refurbishment may not restore its original performance. At this time, the company may need to consider replacing new equipment. For those compressors that still have advanced technology, refurbishment may be a more appropriate choice.
Production line requirements
If the production line is highly dependent on the equipment and the downtime is limited, then refurbishment may not be suitable. At this time, the company can choose to replace the equipment or find a temporary alternative to avoid long-term shutdown of the production line.
Choose a professional renovation service
Choosing a maintenance company with professional qualifications and experience for renovation can effectively ensure the quality of renovation. The company should fully communicate with the maintenance company to ensure that all details in the renovation process are handled professionally.
Conclusion
In general, when the compressor main unit is worn or damaged, renovation as a solution has both advantages and limitations. On the premise of ensuring the quality of renovation, renovation can help companies save costs, extend the service life of equipment, and contribute to environmental protection. However, if the equipment is severely damaged and the renovation effect is uncertain, upgrading may be a wiser choice. Of course, if you are familiar with MINNUO‘s services, you don’t have to worry about this problem. Whether it is renovation or replacement of the machine, we have the most professional technicians to evaluate you and provide you with the most scientific and reasonable solutions.