As a critical piece of equipment in industrial production, air compressors are involved in nearly every industry, such as automotive manufacturing, electronics processing, medical equipment, chemicals, metallurgy, and more. The core function of an air compressor is to provide stable compressed air to drive various devices and processes. However, compressor shutdown issues are a common problem that troubles many users. This not only leads to frequent equipment failures but can also cause production interruptions, increase maintenance costs, and even impact the final product quality. This article will delve into the causes of compressor shutdowns and provide systematic solutions to help enterprises reduce downtime risks.
The issue of air compressor shutdowns is typically caused by power abnormalities, cooling system failures, clogged filters, poor lubrication, unstable pressure, or environmental factors. These problems can be effectively addressed through scientific maintenance and technological optimization, such as installing voltage stabilizers, optimizing the cooling system, regularly replacing filters and lubricants, precise pressure control, and improving the operating environment. MINNUO compressors, equipped with intelligent electrical control, all-aluminum radiators, high-efficiency filtration, and dynamic pressure regulation technology, provide users with stable and efficient compressed air solutions, significantly reducing the risk of shutdowns and ensuring long-term equipment reliability.
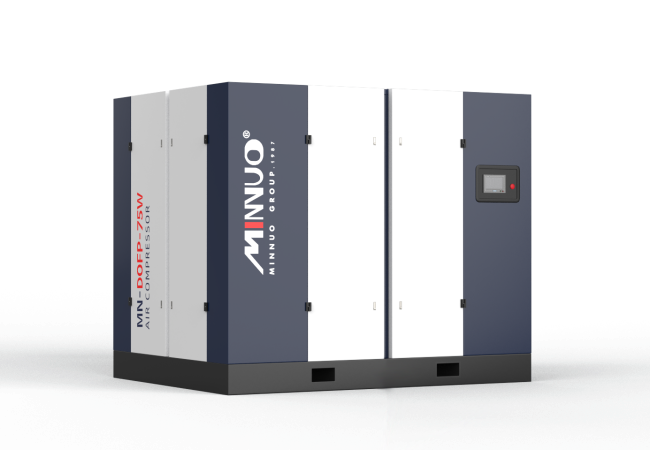
Common Causes and Analysis of Compressor Shutdowns
The phenomenon of compressor shutdown refers to the automatic stopping of the compressor during operation due to the activation of its protection mechanism. As a common fault, compressor shutdown issues are often triggered by various factors. Understanding these causes not only helps in promptly resolving the issue but also prevents production interruptions and potential economic losses caused by equipment failure. Below are the main factors that lead to compressor shutdown issues:
Power Issues
- Voltage instability: Large fluctuations in industrial power supply voltage or excessively high/low voltage may cause the compressor’s motor and control system to malfunction.
- Insufficient power supply: Inadequate power distribution equipment or aging wiring can cause abnormal current fluctuations, triggering a shutdown.
- Short circuits or poor connections: This can activate the electrical protection mechanism, forcing a shutdown to protect the equipment.
Cooling System Failures
- Inadequate cooling: Dust buildup on the radiator or failure of the cooling fan can prevent heat from being dissipated efficiently.
- Insufficient or poor-quality coolant: The cooling efficiency decreases, making it impossible to cool key components.
- Excessively high ambient temperature: If the compressor operates in an environment with temperatures above its tolerance range, the internal temperature rises quickly, triggering a temperature protection shutdown.
Clogged Filters
- Air filter blockage: This reduces the intake volume, lowering equipment efficiency and increasing workload.
- Oil filter blockage: This affects the circulation efficiency of the lubricating oil, increasing mechanical friction and temperature, and triggering the protection mechanism.
Lubrication System Issues
- Insufficient or degraded lubricating oil: Key components cannot be properly lubricated, leading to excessive temperature rise or increased friction.
- Delayed oil changes: Long-term use of aged lubricating oil may cause deposits, affecting system performance.
Pressure System Abnormalities
- Overpressure or underpressure: Faulty or improperly set pressure sensors, or operating pressures outside the normal range, can trigger safety protection.
- Pipeline leakage: Unstable system pressure can lead to frequent compressor starts and shutdowns.
Environmental Factors
- High humidity or excessive dust: This can increase wear and tear on internal components or cause blockages, putting additional strain on the equipment.
- Insufficient installation space: Poor ventilation or inadequate space for heat dissipation can cause the equipment’s temperature to rise, increasing the risk of shutdowns.
Many mid- to low-end compressors experience frequent shutdowns due to imperfect design, insufficient materials, or improper maintenance. These issues not only affect production efficiency but can also result in significant economic losses. To ensure long-term stable operation, selecting high-quality compressors and adhering to regular maintenance practices are key to preventing shutdown issues.
Solutions: How to Effectively Address Compressor shutdown issues?
Solving compressor shutdown issues requires more than just maintenance and operation; it also demands systematic support in terms of equipment selection, configuration, and technology application. Below are specific solutions for various problems, along with innovative optimization measures based on the technical features of MINNUO compressors.
Power Issues Solutions
- Install Voltage Stabilizer: An industrial-grade voltage stabilizer can ensure stable power supply, preventing shutdowns due to voltage fluctuations.
- MINNUO Solution: Our compressors come standard with a high-performance protection and electrical control system, supporting a wide voltage range (±15% fluctuation) and built-in overload protection, which monitors current changes in real time and adjusts automatically.
- Optimize Power Supply Lines: Ensure that the distribution equipment is adequate and regularly check electrical wiring to eliminate potential risks.
- MINNUO Technical Support: Our smart diagnostic electrical control system monitors voltage and current parameters in real time, issuing alerts for any abnormalities, and supports remote monitoring and adjustments.
Cooling System Optimization
- Enhance Cooling Capacity: Regularly clean radiators, check cooling fans, and use high-quality coolants.
- MINNUO Cooling Technology: Our compressors feature an all-aluminum high-efficiency radiator and intelligent fan speed control technology, adjusting cooling efficiency according to load changes. They operate reliably in extreme temperature ranges from -20°C to 50°C.
- Environmental Improvement: Ensure proper ventilation in the operating environment and install air conditioning systems to reduce ambient temperature.
- MINNUO Product Design: Our equipment uses modular compact designs for enhanced ventilation efficiency, with optional corrosion-resistant and heat-resistant materials to suit harsh environments.
Filter Management
- Clean and Replace: Regularly inspect air and oil filters and replace them with high-efficiency models as needed.
- MINNUO Filtration System: Equipped with a high-efficiency two-stage filtration system, our air filters use high-dust-resistance nanomaterials to ensure 99.9% particle isolation efficiency, extending maintenance intervals to over 2,000 hours.
Lubrication System Assurance
- Lubricating Oil Management: Use OEM lubricating oil to ensure consistent oil quality and change it on schedule.
- MINNUO Lubrication System: Our compressors feature an intelligent lubrication monitoring module that detects oil levels and quality in real time and provides alerts for oil replacement.
- Lubrication Optimization: Increase oil cooling capacity under high-load conditions to reduce mechanical wear.
- MINNUO Configuration Features: Equipped with an efficient oil cooler and precise flow control valves to ensure even oil distribution and temperature control.
Pressure Control System Improvement
- Precise Pressure Control: Calibrate pressure sensors and set reasonable operating ranges to avoid frequent overpressure or underpressure.
- MINNUO Technical Standards: MINNUO compressors use high-precision pressure sensors (±0.1% accuracy) combined with dynamic pressure adjustment systems that respond to load changes in less than one second, maintaining stable system pressure.
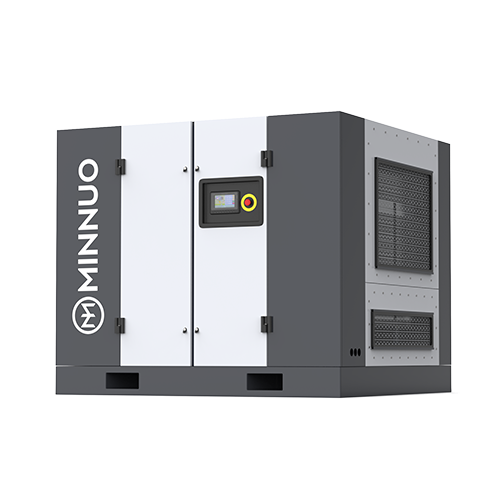
How to Avoid Shutdowns and Similar Issues from the Source?
Choosing a high-end brand like MINNUO helps to avoid shutdowns and similar issues right from the source. When selecting industrial equipment, users often compare multiple brands to ensure equipment performance, reliability, and cost-effectiveness to meet long-term needs. We will now compare MINNUO compressors with ordinary brands in terms of technology, configuration, parameters, and services.
Technical Differences: Leading in Intelligence and Energy Efficiency
Comparison Item | MINNUO Compressor | Ordinary Brand Compressor |
---|---|---|
Control System | Equipped with high-end PLC intelligent controller, remote monitoring, and fault diagnosis, user-friendly interface. | Most use traditional electrical control with limited remote management and delayed diagnostics. |
Energy Efficiency | Equipped with an IE4 ultra-high-efficiency motor and advanced variable frequency technology, energy savings of over 30%. | Some brands still use IE3 motors, with average energy efficiency. |
Operational Efficiency | German-imported technology for the main unit, improving overall efficiency by 15%, reducing airflow losses. | Most use domestic units, efficiency is not up to international standards. |
Pressure Adjustment | Dynamic pressure adjustment technology, response time < 1 second, pressure control accuracy ±0.1%. | Typically use traditional mechanical pressure regulation, slow response, and large control error. |
Core Configuration Comparison: Significant Improvements in Performance and Lifespan
Comparison Item | MINNUO Compressor | Ordinary Brand Compressor |
---|---|---|
Core Components (Main Unit) | Imported aerospace-grade rotor material, lifespan over 100,000 hours, excellent thermal stability. | Ordinary rotor material, lifespan around 60,000-80,000 hours, low reliability. |
Filtration System | Dual-stage high-efficiency filters, 99.9% particle isolation efficiency, maintenance interval extended to 2,000 hours. | Single-stage filtration, insufficient isolation efficiency, high maintenance frequency. |
Cooling System | High-efficiency radiator with intelligent fan speed control, adaptable to ambient temperatures between -20°C and 50°C. | Traditional radiator design, poor adaptability to extreme conditions, frequent failures in harsh environments. |
Lubrication System | Automatic lubrication monitoring system, real-time oil quality and level detection, ensuring long-lasting lubrication. | No oil quality monitoring, oil replacement depends on manual judgment, prone to issues. |
Parameters and Standards Comparison: Excellent Performance for High-Demand Applications
Comparison Item | MINNUO Compressor | Ordinary Brand Compressor |
---|---|---|
Compressed Air Quality | Meets ISO 8573-1:2010 standards, oil content controlled below 0.01ppm. | Higher oil content, some devices fail to meet industry standards in electronics, medical, etc. |
Environmental Adaptability | Customizable anti-corrosion coatings and dust-resistant structures for high humidity and high-dust environments. | General-purpose design, poor performance in harsh environments. |
Noise Control | Operating noise ≤68dB, optimized soundproofing structure and vibration isolation. | Noise typically ranges from 70-75dB, impacting operational comfort. |
Maintenance Cycle | Extended maintenance cycle by 30%, with equipment lifespan reaching up to 20 years after key parts are replaced. | Shorter maintenance cycles, higher long-term operational costs, and shorter lifespan. |
Service System Comparison: Comprehensive Support to Ensure Customer Interests
Comparison Item | MINNUO Compressor | Ordinary Brand Compressor |
---|---|---|
After-Sales Service Network | Global after-sales network, 24-hour response, remote technical support. | After-sales service focused on local or regional areas, slower response. |
Custom Solutions | Provides one-on-one tailored solutions, covering selection, installation, and optimization. | Primarily offers standardized products, limited customization. |
Training Support | Free operation and maintenance training with detailed technical materials and video guides. | Limited training services, documentation is brief. |
Through this comprehensive comparison, MINNUO compressors not only offer significant advantages in performance and configuration but also provide more stable, efficient, and cost-effective compressed air solutions with high manufacturing standards and a complete service system. Choosing MINNUO compressors means opting for longer service life, lower operational costs, and more reliable technical support.
Conclusion
While compressor shutdown issues are complex, they can be effectively solved through scientific maintenance, advanced equipment selection, and professional support. With exceptional quality, intelligent technology, and efficient service, MINNUO compressors have become the trusted choice for many industrial users. If you seek high-performance, low-failure-rate compressor equipment, contact MINNUO now, and we will provide you with comprehensive solutions.