As global demand for clean energy rises, hydrogen is becoming an essential part of the future energy landscape. Used as a low-carbon energy source in transportation, industrial manufacturing, and energy storage, its high energy density and zero-emission properties position it as a key player in the global energy transition. Hydrogen is flammable and explosive, which makes it a huge safety risk in the production, storage and transportation process. This article will discuss in detail how to ensure the safe operation of hydrogen plants, reduce risks and avoid accidents from multiple aspects such as hydrogen plant design, safety management, equipment maintenance, leak detection, risk assessment and emergency response.
Ensuring the safety of hydrogen plants covers key areas such as hydrogen plant design, safe operation management, equipment maintenance, leak detection, risk assessment and emergency response. Through scientific safety management, advanced technical means and comprehensive risk prevention and control measures, potential risks can be effectively reduced to ensure the safe and efficient operation of hydrogen plants. With the rapid development of the hydrogen industry, the safety management of hydrogen plants will become the core guarantee for promoting the sustainable development of the industry.
Safety Risks of Hydrogen Gas
Hydrogen’s flammability and explosive potential make it a highly dangerous substance if not handled properly. As the lightest element, hydrogen can easily form explosive mixtures with air, and its colorless and odorless properties make it difficult to detect without advanced systems. Below are the primary safety risks involved in hydrogen production and storage:
Hydrogen Leaks
Hydrogen is odorless, colorless, and extremely lightweight, making it prone to rapid dispersion when a leak occurs. Due to its invisible nature, leaks are challenging to detect with the human senses, and if not promptly addressed, they can result in catastrophic fires or explosions.
High-Pressure Gas Risks
Hydrogen is often stored and transported as a high-pressure gas. If the storage tanks or pipelines fail, it can lead to violent explosions or leaks, causing severe damage to equipment and endangering personnel.
Fire and Explosion Hazards
Hydrogen has a wide explosive range (4%-75% in air), meaning that even small quantities of hydrogen can form a combustible mixture. If exposed to a spark or flame, this mixture can ignite and cause a fire or explosion.
Equipment Failures
Over time, hydrogen plant equipment such as storage tanks, pipelines, and valves may suffer from wear, corrosion, or cracking. Equipment failures increase the risk of leaks or accidents if not properly maintained.
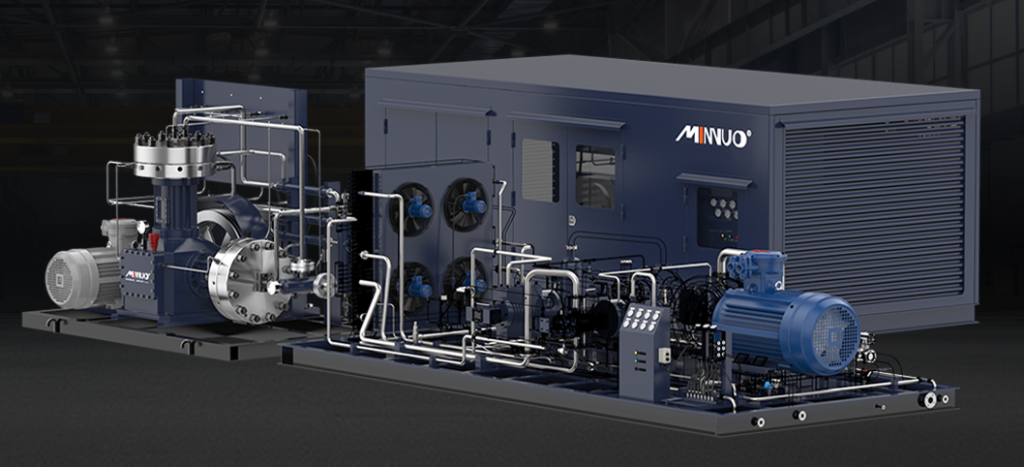
Designing a Safe Hydrogen Production System
A safe hydrogen production system begins with careful and thoughtful design. Properly designed systems can significantly reduce the chances of accidents and mitigate their severity if they do occur. Key safety design considerations include high-pressure storage and transport systems, explosion-proof equipment, and effective ventilation and leakage prevention systems.
High-Pressure Storage and Transport System Design
Hydrogen producers store it at high pressure. They must design storage tanks and pipelines to withstand this pressure, incorporating safety valves, pressure release devices, and other safety features. They should install real-time monitoring systems to track pressure, temperature, and other critical parameters to prevent over-pressurization or other unsafe conditions.
Storage facilities should be located away from high-traffic areas and be properly isolated from other equipment and personnel to prevent the spread of any potential accidents.
Explosion-Proof Design of Hydrogen Production Equipment
Design hydrogen production equipment, such as electrolysis cells and reactors, with explosion-proof measures. Rate all electrical equipment as explosion-proof and protect it against corrosion to ensure safe and reliable operation over time.
Properly designed seals and joints are essential to preventing leaks. Materials used in construction should be resistant to the corrosive effects of hydrogen over time.
Ventilation and Leak Prevention Design
Effective ventilation is critical to preventing hydrogen from accumulating in low-lying areas or poorly ventilated spaces. The facility’s design should ensure that hydrogen can quickly dissipate in the event of a leak. Hydrogen leak detection systems and alarms should be integrated into the plant, ensuring that leaks are identified and addressed immediately.
Operational Safety Management
Beyond equipment design, effective operational safety management is essential to ensuring a hydrogen plant operates safely on a day-to-day basis. Operators must adhere to strict safety protocols and remain vigilant to potential hazards during routine operations.
Safety Training for Operators
Operators are the first line of defense in ensuring safe operations. It’s crucial that employees undergo regular safety training to understand hydrogen’s unique properties and the risks associated with its production and storage. Key training areas should include:
- The chemical and physical properties of hydrogen
- Standard operating procedures for hydrogen production and storage
- Hydrogen leak detection and emergency response procedures
- Emergency evacuation and self-rescue techniques
Regular practical drills should also be conducted to ensure operators can respond effectively to emergency situations.
Standard Operating Procedures (SOPs)
Hydrogen plants must develop comprehensive standard operating procedures (SOPs) for all tasks related to hydrogen production, storage, and handling. These SOPs should be reviewed and updated regularly to ensure they align with the latest safety guidelines and industry best practices. Continuous training and periodic safety audits will help reinforce these procedures and reduce human error.
Maintenance and Inspections
Routine maintenance and inspection of equipment are critical to preventing failures and mitigating risks. Operators must regularly inspect key systems, such as hydrogen storage tanks, pipelines, and safety valves, to identify signs of wear, corrosion, or damage. This helps address potential issues before they escalate into major safety incidents.
Hydrogen Leak Detection and Monitoring Systems
Hydrogen is notoriously difficult to detect with the human senses, so reliable leak detection and monitoring systems are essential for ensuring safety in a hydrogen plant.
Gas Detection Technology
Various gas detection technologies can be employed to monitor hydrogen concentrations in real-time. Common technologies include electrochemical sensors and infrared sensors, both of which are effective at detecting hydrogen leaks and providing early warnings.
Automated Alarms and Control Systems
An automated alarm system should be in place to alert operators when hydrogen concentrations exceed safe thresholds. This system can be integrated with the plant’s ventilation systems, fire suppression systems, and other safety measures to trigger automatic responses and reduce the risk of an accident.
Real-Time Monitoring Systems
A comprehensive real-time monitoring system is essential for tracking the health and performance of critical equipment in the hydrogen plant. By continuously monitoring pressure, temperature, and hydrogen concentrations, operators can quickly identify potential hazards and take corrective action before a problem escalates.
Risk Assessment and Emergency Response
Comprehensive risk assessment and emergency response planning are fundamental to ensuring a hydrogen plant can handle unforeseen incidents effectively. Regular risk assessments and emergency drills help plant operators prepare for potential accidents and mitigate the consequences when they occur.
Regular Risk Assessments
Hydrogen plants should conduct regular risk assessments to identify potential hazards across various stages of operation, including equipment malfunctions, human errors, and environmental factors. Risk assessments should be documented and used to update safety procedures and emergency response plans.
Emergency Response Plans
A detailed emergency response plan should be in place to guide the plant’s reaction in the event of a fire, explosion, or hydrogen leak. These plans should include evacuation routes, emergency contact information, and detailed procedures for handling various types of accidents. Emergency drills should be conducted regularly to ensure all staff members are familiar with the plan and can act quickly and effectively in an emergency.
Conclusion
Ensuring safety in a hydrogen plant requires a comprehensive approach, covering plant design, equipment maintenance, daily operations, and emergency preparedness. By incorporating advanced technology, strict safety protocols, and regular training, hydrogen plants can mitigate risks and ensure safe operations. As the hydrogen industry grows, effective safety management will be key to ensuring a safe, efficient, and reliable energy future.
If you have any questions, please feel free to contact MINNUO.