Centrifugal air compressors are essential power equipment in industrial production, widely used in industries such as petroleum, chemical, metallurgy, and textiles. However, during prolonged operation, compressors may experience various faults that affect production efficiency and equipment lifespan. This article will analyze common faults, their causes, and solutions for centrifugal air compressors, helping users improve the reliability of their equipment’s operation.
Common faults in centrifugal air compressors in industrial applications include abnormal vibration and noise, bearing failure, thrust bearing failure, oil seal ring and sealing ring failure, etc. These problems are usually caused by misalignment, rotor imbalance, poor lubrication, and poor sealing. The solutions to these issues include checking and adjusting alignment, balancing, bearing condition, ensuring proper lubrication, checking oil quality and temperature, and repairing or replacing damaged components.
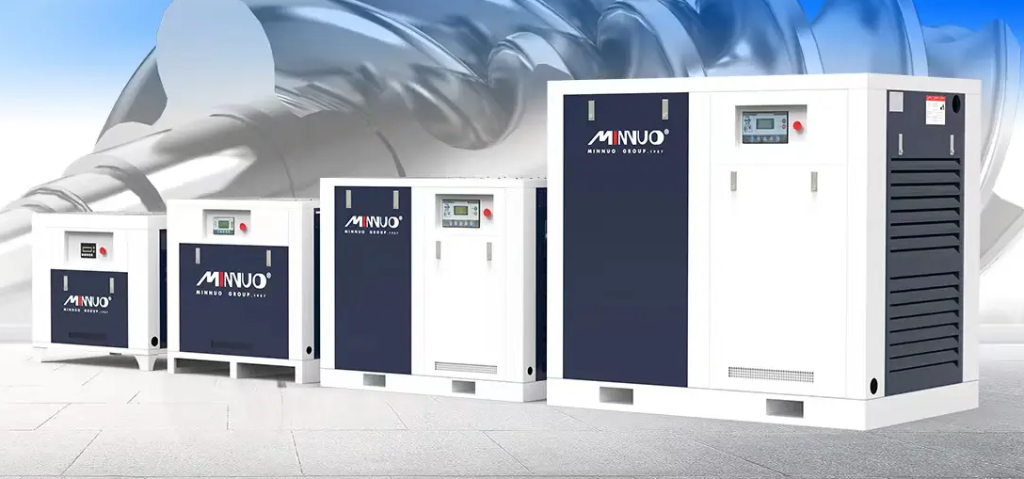
1. Abnormal Vibration and Noise
1.1 Fault Cause Analysis
Abnormal vibration and noise during the operation of centrifugal air compressors can be caused by the following factors:
- Misalignment: The coupling between the compressor and the driver is not properly aligned, causing an imbalance during operation.
- Rotor Imbalance: Uneven mass distribution in the rotor or accumulation of dirt, corrosion, etc., leading to rotor imbalance.
- Damaged Impeller: Cracks, corrosion, or wear in the impeller that affect its balance.
- Bearing Failure: Bearing wear, poor lubrication, or improper installation leading to abnormal bearing operation.
- Coupling Failure or Imbalance: Damaged or improperly installed coupling causing unstable transmission.
- Faulty Sealing Ring: Worn or improperly installed sealing rings causing gas leakage, which increases vibration.
- Abnormal Oil Pressure or Temperature: Lubrication system failure leading to abnormal oil pressure or temperature, affecting bearing operation.
- Contaminants in Oil: Impurities in lubricating oil causing bearing wear.
- Surge Phenomenon: The compressor operates in the surge zone, causing system instability.
- Stress Transfer in Gas Pipelines: Stress from the gas pipelines is transferred to the compressor casing, causing misalignment.
- Interference from Nearby Equipment: Other equipment operating near the compressor causes vibrations that affect it.
1.2 Solutions
- Check Alignment: Disconnect the coupling and let the driver rotate independently. If the driver rotates without abnormal vibration, the fault may be caused by misalignment. Check alignment according to the installation manual.
- Check Rotor Balance: Inspect the rotor for dirt or damage. If necessary, balance the rotor.
- Inspect Impeller Condition: Check the impeller and repair or replace it if necessary.
- Examine Bearing Condition: Check the bearing, adjust gaps, and repair or replace it if needed.
- Check Coupling Balance: Check the balance of the coupling and inspect the coupling bolts and nuts.
- Inspect Sealing Ring Gap: Measure and adjust the sealing ring gap, repair or replace it if necessary.
- Check Lubrication System: Check oil pressure, oil temperature, and oil system performance at various lubrication points, adjusting if anomalies are found.
- Examine Oil Quality and Filtration System: Identify the source of contaminants, check oil quality, enhance filtration, change oil regularly, check bearings, and adjust gaps.
- Avoid Surge Phenomenon: Ensure the compressor operates away from the surge point. Check surge margin and ensure surge protection devices are functioning properly.
- Check Gas Pipelines: Ensure gas pipelines are securely fixed to prevent excessive stress on the compressor casing. The pipelines should have enough flexibility to handle thermal expansion.
- Isolate Nearby Equipment: Separate their foundations and increase flexibility in connecting pipes.
2. Bearing Failure
2.1 Fault Cause Analysis
Bearings are critical components in centrifugal air compressors, and their failure can be caused by:
- Improper Lubrication: Insufficient or substandard lubricating oil leading to poor bearing lubrication.
- Misalignment: Misalignment between the compressor and the driver causes uneven force on the bearing.
- Incorrect Bearing Gap: The bearing installation gap is not according to the design specifications, affecting its normal operation.
- Imbalanced Compressor or Coupling: Imbalanced rotors or couplings cause uneven bearing force.
2.2 Solutions
- Ensure Proper Lubrication: Regularly check the lubricating oil to ensure no water or contaminants have entered it.
- Check Alignment: Inspect and adjust alignment if necessary.
- Check Bearing Gap: Check the bearing gap and adjust or replace bearings if needed.
- Inspect Rotor and Coupling: Check the compressor rotor and coupling for contaminants or damage, and rebalance the rotor if necessary.
3. Thrust Bearing Failure
3.1 Fault Cause Analysis
Thrust bearings are used to handle axial thrust in compressors, and their failure can be caused by:
- Excessive Axial Thrust: Excessive pressure difference between gas inlet and outlet, causing axial thrust to exceed design limits.
- Improper Lubrication: Insufficient or poor-quality lubricating oil causing inadequate lubrication for the thrust bearing.
3.2 Solutions
- Check Thrust Bearing Gap: Measure and adjust the thrust bearing gap if necessary.
- Check Gas Inlet/Outlet Pressure Difference: Inspect and adjust the pressure difference if necessary.
- Inspect Sealing Ring Gap: Check internal sealing ring gaps and adjust if necessary.
- Examine Oil System: Check the oil pump, filter, cooler, oil temperature, pressure, and oil quality.
4. Oil Seal Ring and Sealing Ring Failure
4.1 Fault Cause Analysis
Oil seal rings and sealing rings prevent lubricating oil leakage and gas ingress, and their failure can be caused by:
- Misalignment and Vibration: Misalignment between the compressor and driver causing uneven force on the sealing ring.
- Contaminants in Oil: Impurities in lubricating oil causing sealing ring wear.
- Incorrect Sealing Ring Gap: Incorrect installation gap affecting sealing performance.
- Insufficient Oil Pressure: Lubrication system failure causing inadequate oil pressure, impacting sealing efficiency.
- Poor Sealing Ring Precision: Low manufacturing precision affecting sealing effectiveness.
- Oil Quality and Temperature Issues: Poor quality oil or excessively high oil temperature affecting the sealing performance.
4.2 Solutions
- Refer to Vibration Solutions: Follow the solutions outlined in the abnormal vibration and noise section.
- Check Oil Filters: Replace filters with contaminants and enhance inline filtration.
- Inspect Sealing Ring Gap: Measure and adjust the gap if necessary or replace the sealing ring.
- Check Oil System: Ensure oil pressure meets requirements.
- Inspect Sealing Ring Precision: Examine the sealing ring and repair or replace it if necessary.
- Examine Oil Quality and Temperature: Check oil quality and temperature, adjusting as needed to ensure the sealing system operates normally.
5. Unstable or Abnormal Sealing System Operation
5.1 Fault Cause Analysis
The sealing system in centrifugal air compressors is crucial for stable operation and preventing gas leakage. Common fault causes include:
- Low Sealing Ring Precision: Poor manufacturing precision leading to poor sealing performance.
- Sealing Oil Quality or Temperature Issues: Low-quality sealing oil or excessive oil temperature leading to sealing failure.
- Malfunctioning Oil/Gas Pressure Differential System: A failure in the oil/gas pressure differential system leading to decreased sealing efficiency.
- Wear or Damage to Sealing Parts: Wear or damage to sealing rings, seats, etc., causing sealing failure.
- Uneven Contact Wear on Floating Ring Seat: Uneven wear on the floating ring seat leading to poor sealing.
- Chipped or Worn Sealing Surface on Floating Ring Seat: Damage to the sealing surface leading to gas leakage.
5.2 Solutions
- Check Sealing Ring: Inspect the sealing ring for precision and replace or repair if necessary.
- Inspect Sealing Oil Quality and Temperature: Check sealing oil quality and adjust the temperature to ensure compliance with requirements.
- Check Oil/Gas Pressure Differential System: Inspect components of the oil/gas pressure differential system to ensure normal operation and adjust to specified values.
- Check Sealing Parts for Wear: After disassembling the seal, adjust the gap and replace worn parts.
- Repair Floating Ring Seat: Grind the contact surface of the floating ring seat to ensure uniform contact, and replace the seat if necessary.
- Prevent Ingestion Damage: Minimize ingestion damage to prevent excessive wear during operation, and replace components as necessary.
6. Conclusion
By analyzing the common fault causes and corresponding solutions, compressors’ failures can be effectively prevented and resolved, ensuring long – term stable operation of the equipment. Additionally, users should select reliable compressor equipment suppliers and ensure that installation, operation, and maintenance comply with technical requirements. For any other issues or if further professional support is needed, feel free to contact MINNUO Compressor Manufacturer, and we will be happy to assist you.