In modern industrial production, air compressors are widely used in various production processes. However, during their operation, about 80% of the electrical energy is converted into heat, most of which is lost through the cooling system, resulting in significant energy waste and thermal pollution. This article will explore in depth the conventional heat recovery methods and applications of air compressors to help enterprises achieve efficient energy utilization and maximize economic benefits.
Conventional heat recovery methods for air compressors include heat exchanger technology, waste heat power generation, heat pump technology, and intelligent system integration solutions, which are suitable for different types of air compressors and industrial scenarios. These technologies not only improve energy use efficiency but also help enterprises reduce carbon emissions and achieve green transformation. Through reasonable design and optimization of recovery systems, enterprises can gain significant economic and environmental benefits in various areas such as domestic hot water supply, process preheating, and building heating.
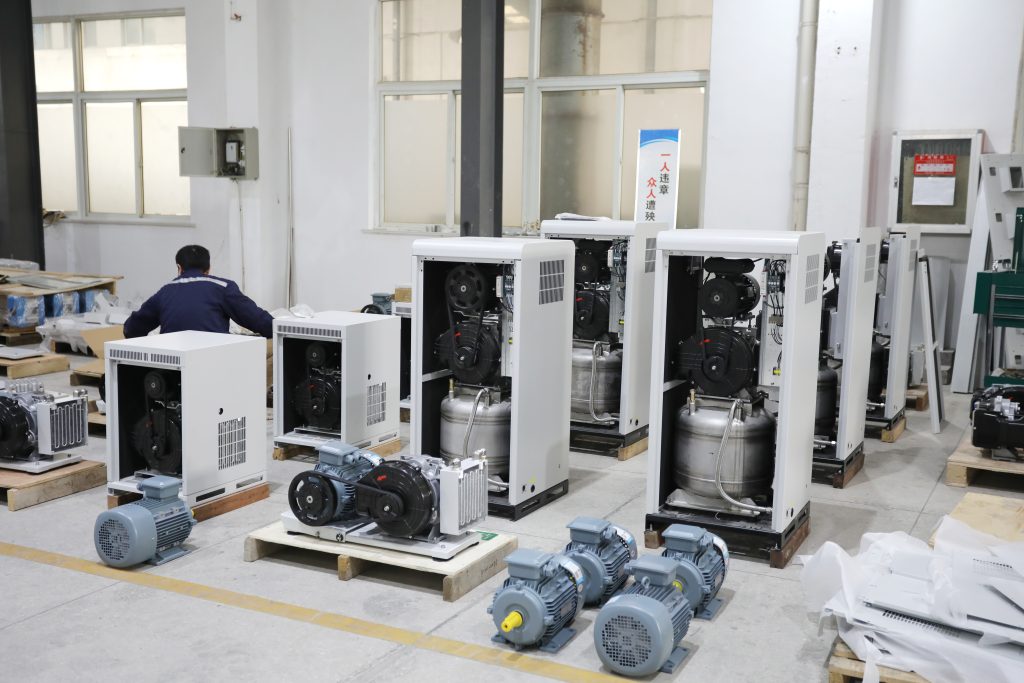
1. Heat Exchanger Technology
Heat exchangers are one of the most widely used heat recovery technologies. They transfer the waste heat generated by air compressors to media such as water or heat transfer oil for production or domestic use. This technology effectively converts otherwise wasted heat into reusable energy, improving energy use efficiency and reducing energy costs for enterprises.
(1) Plate Heat Exchanger
The plate heat exchanger is composed of corrugated metal sheets stacked together, offering highly efficient heat transfer performance, especially suitable for oil-free air compressor systems. During operation, cold water absorbs the waste heat generated by the air compressor through the heat exchanger, raising the water temperature. The heated water can be used in various scenarios, such as heating and domestic water supply. For example, a PVC pipe manufacturing enterprise saved about $90,000 annually in electricity bills and met the hot water needs of 420 employees by recovering air compressor heat through plate heat exchangers.
(2) Shell and Tube Heat Exchanger
Shell and tube heat exchangers are suitable for air compressor systems with high exhaust temperatures (80–100°C), effectively transferring high-temperature heat to the cooling medium. The heat loss is minimal—only about 2%. This type of exchanger is widely used in applications such as industrial water heating or sludge drying. For scenarios with high exhaust temperatures, shell and tube heat exchangers perform particularly well.
(3) Direct Heating Exchange
Direct heating exchange technology directly mixes cold water with high-temperature oil and gas, raising the water temperature to over 40°C in just 20 seconds. This technology is particularly suitable for scenarios requiring instant hot water, such as factory workshops and office areas.
2. Waste Heat Power Generation Technology
Waste heat power generation technology converts the high-temperature compressed air or oil circuit heat into electricity, offering an efficient energy utilization method for large-scale industrial scenarios. Especially in high exhaust temperature environments, waste heat power generation significantly enhances energy self-sufficiency and reduces dependence on the power grid.
(1) Organic Rankine Cycle (ORC)
Organic Rankine Cycle (ORC) technology uses low-boiling-point working fluids (e.g., Freon) to absorb waste heat and evaporate, thereby driving a turbine to generate electricity. This technology is suitable for recovering low-temperature waste heat and significantly improves energy efficiency. The application of ORC technology not only reduces production costs but also helps enterprises reduce carbon emissions, aligning with the green development trend of modern industry.
(2) Steam Power Generation
Steam power generation uses waste heat boilers to produce steam, which drives a generator. This technology can recover 15–25% of the input power of the air compressor and is suitable for high exhaust temperature scenarios (>100°C). Steam power generation has important applications in high-energy-consuming industries such as petrochemicals and metallurgy, helping reduce dependence on the power grid and enhancing energy self-sufficiency.
3. Heat Pump Technology
Heat pump technology elevates low-grade heat (such as 60–80°C waste heat) to high-grade heat (such as above 90°C) through compression and expansion processes. It is suitable for district heating and industrial processes, significantly improving energy efficiency and reducing energy consumption of traditional heating systems.
(1) Absorption Heat Pump
Absorption heat pumps use external heat sources to drive the refrigerant cycle and are suitable for winter heating in northern regions. In winter, the low-grade waste heat generated by air compressors is converted into high-temperature heat through absorption heat pumps for workshop or office heating. This method not only saves coal consumption but also effectively reduces CO₂ emissions.
(2) Compression Heat Pump
Compression heat pumps are driven by electricity and have relatively high efficiency, although they require additional power. Despite this, due to their efficient heat conversion, compression heat pumps are widely used in most industrial and commercial settings, especially where there is a high demand for hot water.
Application Case
A chemical plant used heat pump technology to recover air compressor waste heat for workshop heating. The project saves about 855 tons of coal annually and reduces CO₂ emissions by approximately 2,200 tons, demonstrating the vital role of heat pump technology in energy conservation and emission reduction.
4. Integrated Waste Heat Recovery Solutions
Different types of air compressors (such as oil-injected screw, oil-free screw, and centrifugal compressors) have different operating principles and characteristics, so their waste heat recovery systems also require customized design based on actual conditions.
(1) Oil-Injected Screw Compressors
These compressors extract high-temperature oil circuit heat through an oil-gas separator and regulate oil temperature with a thermostatic valve to prevent oil degradation. This type of system can achieve up to 85% heat recovery efficiency and is widely used in scenarios that demand high heat recovery performance.
(2) Centrifugal Compressors
Centrifugal compressors typically adopt multi-stage heat recovery systems combined with heat-of-compression regenerative dryers, achieving over 90% heat recovery efficiency. These systems are particularly suited for large-scale industrial applications, enabling efficient recovery of large amounts of waste heat.
(3) Intelligent Control Systems
With the development of IoT and automation technology, intelligent control systems have become an essential component of air compressor heat recovery. These systems integrate PLC (Programmable Logic Controllers) and IoT technologies, allowing real-time monitoring of water temperature and flow, and automatically switching between cooling and heat recovery modes based on actual needs, ensuring the safe operation of the compressor.
5. Application Scenarios and Economic Benefits
Heat recovery from air compressors is not limited to industrial production processes but can also be widely used in domestic hot water, process preheating, and building heating.
(1) Domestic Hot Water
By recovering air compressor waste heat and heating water to 50–60°C, hot water can be provided for employees, replacing electric or gas boilers. The investment payback period is typically 6–24 months. This solution is especially suitable for large enterprises or factories, offering convenient hot water for employees while reducing operating costs.
(2) Process Preheating
Air compressor waste heat can be used for preheating processes such as reverse osmosis water purification, boiler feedwater heating, or industrial cleaning, reducing fuel consumption and saving energy. Data shows that using heat recovery technology for process preheating can reduce fuel consumption by more than 30%, achieving energy savings and emission reductions.
(3) Building Heating
In cold regions, air compressor heat recovery can replace traditional heating systems, particularly in northern areas. Using waste heat for building heating can reduce standard coal consumption, with each air compressor saving up to 170 tons of standard coal annually.
Application Case
A coal enterprise implemented a heat recovery retrofit on three 250 kW air compressors, recovering heat equivalent to 3,600 tons of steam annually and saving approximately $70,000 in costs. This case demonstrates the great potential of heat recovery technology in cost savings and improving energy efficiency.
6. Conclusion
When selecting a heat recovery solution, enterprises should opt for customized designs based on actual needs and equipment types, and combine them with policy support (such as carbon reduction subsidies) to accelerate green transformation. For detailed technical parameters or customized solutions, feel free to consult the MINNUO technical team—we will ensure the successful implementation of your project and the realization of expected benefits.