Air compressors are widely used in industrial production, but the phenomenon of surge is like a “time bomb” that threatens equipment stability, impacts production efficiency, and affects economic benefits. It is crucial to explore the definition, hazards, and causes of surge, and to propose effective methods for preventing and eliminating it to ensure production continuity, efficiency, and reduced operational costs.
The surge phenomenon in air compressors affects equipment stability and production efficiency, leading to equipment damage and increased maintenance costs. Methods to prevent and eliminate surge include increasing intake flow, properly adjusting anti-surge systems, accurately controlling acceleration and pressure rise processes, using isentropic and safe pressure rise methods, and appropriately configuring and adjusting anti-surge valves.
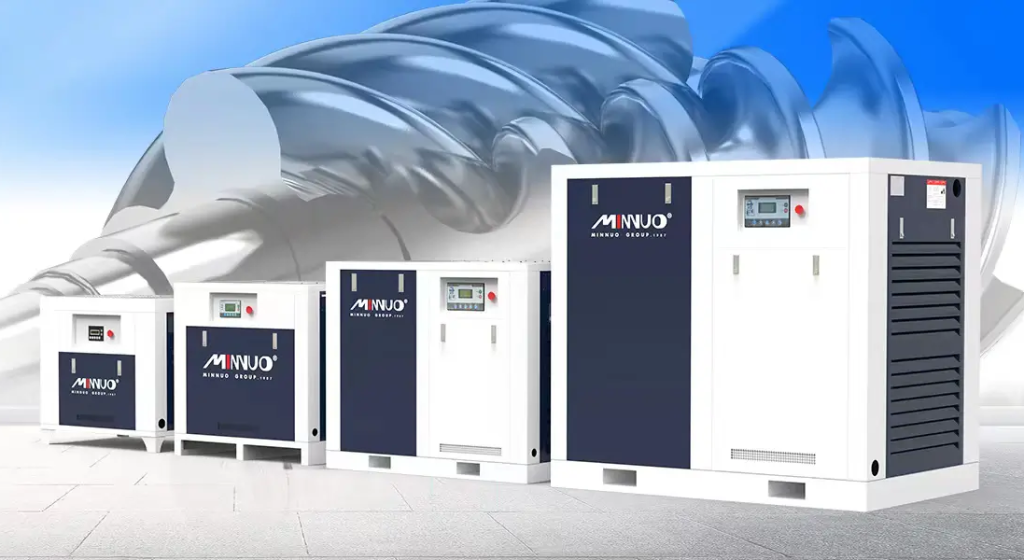
I. Definition and Hazards of Surge
(a) Definition of Surge
Surge, known in English as “Surge,” refers to the phenomenon where, during operation, an air compressor experiences severe fluctuations in intake airflow and exhaust pressure due to unstable or insufficient gas flow. These fluctuations act like an internal “storm” within the equipment, severely disrupting the normal operation of the compressor and even leading to shutdowns, which in turn causes a series of production issues.
(b) Hazards of Surge
(1) Efficiency Reduction
Once surge occurs, the compressor’s airflow and exhaust pressure can no longer be maintained in an ideal stable state. In chemical production, if a compressor experiences surge, it will lead to unstable gas flow and pressure delivered to the reactor, causing the reaction to proceed under suboptimal conditions and reducing both product quality and output. To avoid surge, operators often need to consume more energy, which further lowers the overall energy efficiency of the compressor system and increases production costs.
(2) Equipment Damage
Prolonged surge can severely damage the internal structure and components of the air compressor. For example, bearings suffer from uneven load distribution due to continuous pressure fluctuations and vibrations, accelerating wear and shortening service life. Surge can also damage seals, causing gas leakage that not only affects equipment performance but also may lead to safety incidents. The rotor, as the core component of the compressor, is subjected to unbalanced forces under surge, which can deform it and affect the normal operation of the equipment.
(3) Increased Maintenance Costs
Surge typically leads to frequent equipment failures, increasing maintenance times and costs. Each failure requires professional technicians for repairs, consuming significant human resources and time, and possibly requiring the replacement of damaged parts. Additionally, longer downtime affects the normal operation of production lines, leading to production interruptions and substantial economic losses.
(4) System Instability
Surge affects not only the performance of the air compressor but may also impact downstream equipment, causing instability in the entire production system. In gas storage devices, pressure fluctuations caused by surge can cause failures in pressure control devices, increasing equipment safety risks. In transmission pipelines, pressure fluctuations accelerate pipeline wear, shortening its service life, and may even cause pipeline rupture, leading to gas leakage.
II. Fundamental Causes of Surge in Air Compressors
(a) Insufficient Intake Flow
Insufficient intake flow is one of the fundamental causes of surge in air compressors. Like a “gas processing plant,” an air compressor needs a certain intake flow to operate efficiently. When the gas flow entering the compressor is too low, the compressor cannot maintain stable operation, leading to surge. In some industrial processes, surge is triggered by insufficient gas supply or blocked intake pipelines, which reduce the intake flow to the compressor.
(b) Excessive Backpressure
Backpressure refers to the external pressure exerted on the gas after it exits the compressor. If the system’s backpressure is too high, the compressor cannot discharge enough gas, causing an unstable operating state that leads to surge. For instance, in gas transportation, if downstream equipment’s resistance increases or the exhaust pipeline becomes blocked, backpressure rises, causing surge.
(c) Rapid Acceleration or Pressure Rise
Rapid acceleration or pressure rise is a common operational mistake. When starting the compressor or adjusting its working state, if the compressor speed or exhaust pressure increases too quickly over a short period, it can cause unstable gas flow, leading to surge. This is like a car suddenly accelerating too fast, making it hard to control. Therefore, acceleration and pressure rise must be strictly controlled to avoid rapid changes.
(d) Unreasonable System Configuration
Unreasonable configuration of the compressor system, such as improper valve settings or incorrect performance curve selections, can also lead to surge. The valve opening directly impacts gas flow and pressure, and improper valve settings can lead to abnormal gas flow and pressure, causing surge. Additionally, selecting a compressor performance curve that does not match actual working conditions can make surge more likely.
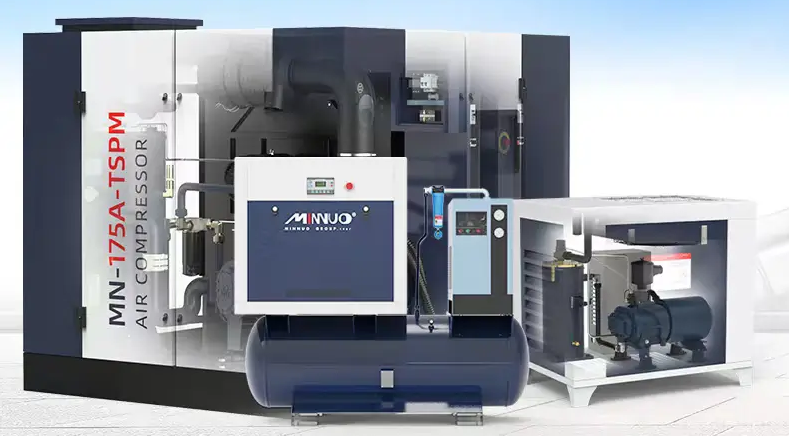
III. Measures to Prevent and Eliminate Surge
(a) Increase Intake Flow
(1) Vent Method
For gases like air and CO2, the venting method can be used to increase the intake flow. Venting operations “open up a new channel” for the gas, allowing part of it to be expelled and thereby increasing intake flow, which eliminates surge. However, while this method can effectively increase flow, it leads to a decrease in exhaust pressure, causing some power loss. In situations with strict gas emission requirements, the environmental impact of venting needs to be considered.
(2) Recycling Method
For gases like syngas, natural gas, and ammonia, the recycling method can be used to increase flow. Recycling involves redirecting the discharged gas back to the compressor’s intake, “creating a circulation channel” that increases flow and reduces surge. However, while this increases gas flow, it can also lead to reduced exhaust pressure and increased power loss. Therefore, measures like increasing speed are needed to restore exhaust pressure and maintain the system’s economic viability.
(b) Reasonably Adjust Anti-Surge Systems
The setting of anti-surge systems is crucial to preventing surge. According to the compressor’s performance curve, the anti-surge system’s safety margin should be adjusted reasonably. During normal operation, the anti-surge system should be in automatic mode, constantly monitoring the compressor’s operation. During acceleration and pressure rise, the appropriate operating point should be selected based on the performance curve and adjusted with precision according to the safety margin. If the anti-surge margin is set too large, surge will be less likely, but the pressure may be too low, resulting in reduced energy efficiency. Thus, the anti-surge valve should be adjusted according to actual needs to ensure both safe and economical operation.
(c) Pressure Rise and Speed Control
Pressure rise and speed control are crucial to preventing surge. Before increasing pressure, the compressor’s performance curve must be confirmed, and the appropriate speed must be selected. During acceleration, the pressure rise should be gradual and uniform to avoid large pressure fluctuations from rapid pressure increases. During deceleration, the operation must be conducted under the normal operation of the anti-surge valve to ensure stable system operation. The deceleration process should be gradual to avoid significant pressure fluctuations. Anti-surge valve opening and closing actions should be slow to avoid excessive vibrations that could disrupt axial thrust and seal system balance.
(d) Use of Isentropic and Safe Pressure Rise Methods
Isentropic and safe pressure rise methods are another effective way to prevent surge. By controlling the compressor’s speed and pressure ratio, surge can be prevented. Each cylinder has a specific surge flow at a given speed, and when the gas flow exceeds a certain value, surge occurs. By calculating the anti-surge margin and safe flow for different speeds, the corresponding exhaust pressure can be determined. By ensuring that the exhaust pressure does not exceed the calculated pressure during acceleration and pressure rise, surge can be avoided.
(e) Configuration and Adjustment of Anti-Surge Valves
If the compressor is equipped with multiple anti-surge valves, the valves should be configured to open and close alternately in an orderly “dance,” ensuring uniform pressure changes across all cylinders. The opening and closing actions of the valves should be smooth to avoid excessive vibration that could impact axial thrust and seal system stability. During adjustment, the anti-surge valve should be finely tuned according to the compressor’s operation state and actual working conditions to ensure optimal anti-surge performance.
IV. Conclusion
By preventing and eliminating Surge in Air Compressors, equipment efficiency and lifespan improve, energy consumption and costs decrease, and production remains stable. Operators must recognize surge hazards, follow procedures, and conduct inspections, while enterprises should adopt advanced technologies to enhance competitiveness.
MINNUO, as an excellent air compressor manufacturer, is a brand you can trust.