Frequency inverter control technology has become a core method for energy saving and performance optimization in modern air compressors. By adjusting the motor speed, compressors can operate efficiently according to actual demand, resulting in significant energy savings and extended equipment lifespan. This article provides a brief analysis of the basic principles and formula breakdown of frequency inverter control in air compressors.
The frequency inverter control technology for air compressors enables stepless speed regulation by adjusting the power supply frequency, maintaining constant magnetic flux for stable motor torque. The inverter system consists of rectification, filtering, and inversion units to optimize energy conversion, reduce energy consumption, and minimize equipment wear. Frequency inverter control improves energy efficiency, reduces waste, and extends equipment lifespan under varying loads.
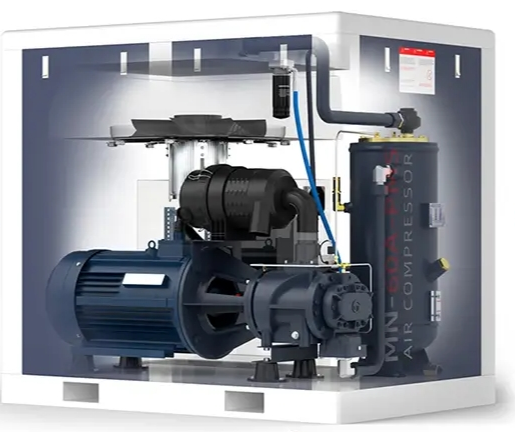
1. Core Principles of Frequency Inverter Control
The core of frequency inverter control technology for air compressors lies in adjusting the motor speed by changing the frequency of the power supply. The speed of an asynchronous motor is determined by the following formula:
n = n1 (1 – s) = (60f(1 – s)) / p
Where:
- n = Actual motor speed (r/min);
- n1 = Synchronous speed (r/min);
- s = Slip (s = (n1 – n) / n1);
- f = Power supply frequency (Hz);
- p = Number of pole pairs of the motor.
From this formula, it can be seen that the speed can be adjusted by changing p, slip s, or frequency f. Frequency inverter control achieves stepless speed adjustment by changing f, avoiding the complexity of traditional mechanical speed regulation. This has become the mainstream method for energy-saving transformation of air compressors.
2. Electromagnetic Fundamentals and Voltage-Frequency Coordination Control
The electromagnetic characteristics of the asynchronous motor are governed by the voltage formula:
E = 4.44 * kw * N * f * Φ
Where E is the induced electromotive force (EMF) of the stator and Φ is the magnetic flux. If the frequency f is changed, the magnetic flux Φ will also change:
- At low frequency: If the voltage U remains constant, Φ increases, leading to magnetic saturation, a surge in magnetizing current, and increased iron losses.
- At high frequency: Φ decreases, which reduces the motor torque and overload capacity.
Therefore, frequency inverter control must follow the U/f constant rule (i.e., constant magnetic flux control). The voltage and frequency must be adjusted in coordination (VVVF control) to maintain a constant Φ, ensuring stable motor torque. This principle is called Voltage Variable Frequency Control (VVVF), which is the core control strategy of modern inverters.
3. AC-DC-AC Inverter System Structure and Working Process
The air compressor frequency inverter system typically uses AC-DC-AC (alternating current-direct current-alternating current) inverters, which consist of three main parts:
3.1 Rectifier Unit (AC-DC Conversion)
Function: Converts three-phase AC power to DC power.
Technical Solution: Uses a diode or thyristor full-bridge rectifier circuit, with efficiency reaching above 98%.
3.2 Filtering Unit (DC Bus Voltage Stabilization)
Function: Smooths out the pulsed DC voltage from the rectifier and suppresses harmonics.
Key Technology: A combination of large-capacity electrolytic capacitors and DC reactors reduces voltage ripple.
3.3 Inverter Unit (DC-AC Conversion)
Function: Converts DC power into adjustable frequency and voltage AC power.
Control Mode:
- SPWM modulation: Generates a sine wave with pulse width modulation;
- Vector Control: Decouples the motor’s magnetic field and torque current for enhanced dynamic response accuracy.
Working Process: AC power → Rectification & Filtering → DC Bus → Inversion & Frequency Adjustment → Motor Drive. This process is controlled in real-time by microprocessors, with a response time of milliseconds.
4. Energy Saving Benefits and Engineering Applications of Frequency Inverter Control
4.1 Energy Saving Principle
Unload Loss Elimination: Traditional air compressors still have 40%-60% of idle energy loss when unloaded. Frequency inverter systems reduce this to zero-power standby by lowering the frequency.
Optimized Constant Pressure Supply: PID closed-loop control keeps network pressure fluctuations within ±0.02MPa, avoiding energy waste due to frequent loading and unloading.
4.2 Measured Energy Savings
For a 75kW air compressor:
Operation Mode | Loaded Current (A) | Unloaded Current (A) | Daily Power Consumption (kWh) |
Power Supply | 220 | 90 | 1200 |
Inverter | 130 | 50 (low-frequency standby) | 720 |
Annual Energy Saving:
(1200 – 720) × 300 = 144000 kWh
Energy saving rate exceeds 40%.
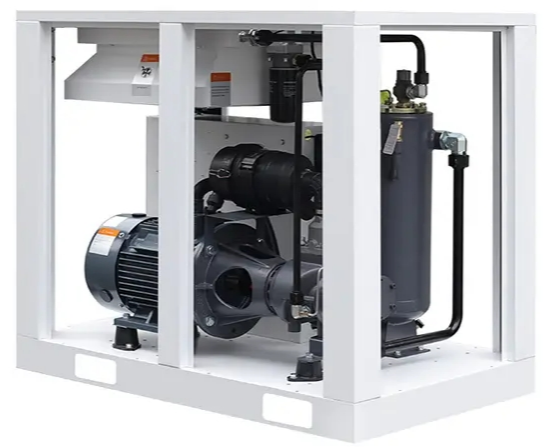
5. Key Technical Challenges and Solutions in Frequency Inverter Control
5.1 Low Frequency Operation Stability
Problem: At frequencies below 25Hz, poor lubrication can lead to increased bearing wear.
Solution: Set a minimum frequency limit (≥25Hz) and use vector control algorithms to enhance torque output.
5.2 Harmonic Suppression and EMC Compatibility
Problem: IGBT high-frequency switching generates 5%-15% harmonic current, causing interference with the power grid.
Solution:
- Add AC reactors or active filters on the input side;
- Install sine wave filters on the output side to meet IEC 61800-3 electromagnetic compatibility standards.
5.3 Motor Heating and Insulation Protection
Problem: High-frequency operation increases stator winding temperature rise.
Solution: Use F-class insulation materials and include PT100 temperature sensors for real-time monitoring.
6. Inverter Selection and System Design Considerations
6.1 Inverter Capacity Calculation
P_inverter ≥ 1.2 × P_motor rated
Consider motor starting torque (150%-200% rated torque) and overload capacity.
6.2 Control Mode Selection
- V/F Control: Suitable for general air compressors, cost-effective;
- Vector Control: Suitable for high-precision tension control, with quick dynamic response.
6.3 System Redundancy Design
Equip with dual power supply (inverter/power supply) for quick recovery in case of failure.
7. Future Development Trends
7.1 Permanent Magnet Synchronous Motors (PMSM) Application
Efficiency improves by 5%-10% compared to asynchronous motors, with a speed range extended to 1:100.
7.2 Integration with Smart Technology and IoT
By using Modbus/TCP protocols to connect to cloud platforms, real-time monitoring and energy analysis are achievable.
7.3 Silicon Carbide (SiC) Power Devices
Switching loss reduced by 50%, with inverter efficiency exceeding 98%, ideal for high-voltage and high-power applications.
8.Conclusion
Frequency inverter control technology for air compressors achieves energy efficiency improvement, noise reduction, and extended equipment lifespan through precise frequency and voltage control. MINNUO compressors use advanced vector control inverters and permanent magnet synchronous motors to provide customers with efficient, stable, and smart compressed air solutions.