As a core component in many industrial systems, the stable operation of an air compressor is crucial. However, in daily use, compressors often encounter several issues that can affect production efficiency. Understanding the common causes of these failures, along with how to prevent and address them, can effectively extend the equipment’s lifespan and reduce maintenance costs. This article introduces the five most common air compressor failures and their solutions, helping you improve the reliability of your equipment’s operation.
The five common air compressor failures include insufficient air output, abnormal pressure, abnormal temperature, abnormal noise, and overheating. The corresponding solutions include checking air filters, adjusting speed, and optimizing cooling systems. Additionally, preventive measures and equipment upgrades are necessary, such as regular maintenance, adding intake mufflers, and using air quality testers.
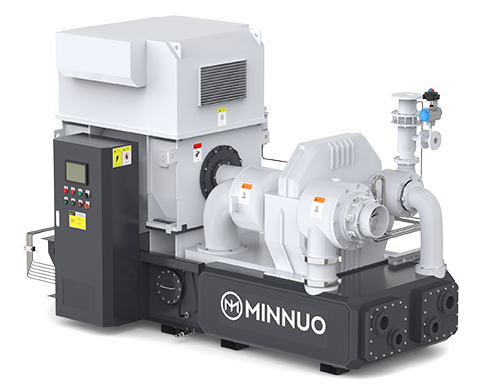
1. Insufficient Air Output
1.1Symptom:
The actual air output is lower than the rated value, leading to reduced production efficiency.
1.2Cause Analysis and Solutions:
1.2.1Air Filter Blockage
Detection Method:
Observe the differential pressure gauge (normal differential pressure < 10kPa), or use an infrared thermometer to check the filter surface temperature (temperature difference > 5°C indicates cleaning is needed).
Maintenance Steps:
Remove the filter element and blow it clean with compressed air from the inside out (pressure ≤ 0.3MPa).
If the filter element is paper, replace it every 2000 hours; metal mesh filters can be soaked in neutral detergent and air-dried.
Install a pre-filter (e.g., cyclone separator) to extend the life of the main filter.
1.2.2Abnormal Speed
Check Points:
Use a tachometer to measure the motor speed, ensuring it matches the nameplate parameters (tolerance ±5%).
Check the belt tension of the belt-driven compressor (deflection should be 15-20mm/100mm center distance); replace if necessary.
For variable frequency compressors, verify the inverter settings (e.g., acceleration time, overload protection threshold).
1.2.3Mechanical Wear
Piston Ring Replacement Standards:
End gap exceeds 1.5 times the original design value (e.g., cast iron ring end gap > 3mm).
Side gap > 0.15mm (aluminum ring) or > 0.10mm (cast iron ring).
If the cylinder ovality exceeds 0.05mm, re-bore the cylinder.
Packing Box Maintenance:
If the piston rod linearity error exceeds 0.05mm/m, straighten it.
Use special tools to align the packing box, ensuring radial runout ≤ 0.03mm.
When packing graphite packing, install with staggered joints (adjacent layers staggered ≥ 90°).
1.2.4Valve Failure
Maintenance Process:
The contact area between the valve plate and the valve seat should be 1.5-2mm. Use red lead powder to check the sealing.
Replace springs if the free height deviation exceeds ±2%, and test the spring’s compression elasticity after compression to the working length (tolerance ±5%).
Tighten the valve bolts using a torque wrench (e.g., M12 bolts with a torque of 60-80N·m) and add anti-loosening glue.
Preventive Measures:
Establish a regular maintenance schedule: check filters every 500 hours, inspect valves every 2000 hours, and replace piston rings every 4000 hours.
Install intake mufflers to reduce the impact of pulsations on valves.
Use air quality testers to ensure that intake dust levels are <1mg/m³ and humidity is <60% RH.
2. Abnormal Pressure
2.1Symptom:
The system pressure cannot remain stable at the set value, or pressure fluctuates significantly.
2.2Diagnosis and Solutions:
2.2.1Valve Leakage Detection
In shutdown mode, introduce 0.5MPa compressed air into the cylinder and check for bubbles at the valve chamber interface with soapy water.
During operation, use an infrared thermograph to check the temperature of the valve. Leakage areas will show an abnormal temperature rise (temperature difference > 15°C).
2.2.2Piston Ring Failure Determination
Measure the cylinder compression ratio: Theoretical compression ratio = (discharge pressure + 0.1MPa) / (intake pressure + 0.1MPa).
If the actual compression ratio decreases by more than 10%, it indicates piston ring seal failure.
2.2.3Pressure Control System Failure
Check the accuracy of the pressure sensor (tolerance should be <±0.5% FS) and calibrate zero drift.
Clean or replace the unloading valve core, ensuring it operates smoothly without sticking (action pressure deviation ≤ ±0.02MPa).
2.3Upgrade Suggestions:
When the existing compressor cannot meet pressure requirements, consider:
- Series Boosting: Add a secondary booster cylinder to raise the pressure by 1.5-2 times the original design.
- Switching to a Screw Compressor: At the same power, screw compressors offer 30% more stable discharge pressure than piston compressors.
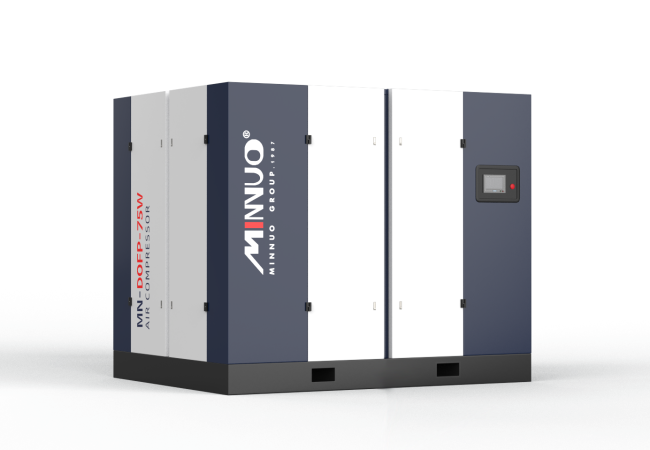
3. Abnormal Temperature
3.1Symptom:
Discharge temperature >180°C (oil-injected screw compressor) or >200°C (oil-free compressor), or bearing temperature >90°C.
3.2Solutions:
3.2.1Cooling System Optimization
Water-cooled Models:
Clean the cooler of scale (use a 5% citric acid solution for circulation cleaning, stop when pH rises to 4.5).
Check the water pump head (should meet system resistance + 0.1MPa), and replace the impeller if flow is insufficient.
Air-cooled Models:
Clean the radiator fins of dust (use a high-pressure water gun to wash with pressure ≤ 0.5MPa).
Check the fan belt tension (deflection should be 10-15mm/100mm center distance) to ensure proper air volume.
3.2.2Lubrication System Maintenance
Regularly check lubrication oil quality:
If viscosity changes by more than ±10%, replace it.
If the acid value exceeds 0.5mgKOH/g, filter or change the oil.
Clean the oil circuit: use a special oil sludge cleaning agent for circulation for 4-6 hours, then thoroughly drain.
3.2.3Compression Efficiency Improvement
Check intake valve opening (resistance loss <0.03MPa when fully open).
Adjust cylinder clearance volume (the optimal clearance volume is 4-8% of the cylinder’s working volume).
4. Abnormal Noise
4.1Symptom:
Metal knocking, friction sounds, or vibration noises.
4.2Fault Location and Solutions:
4.2.1Piston and Cylinder Head Collision
Measure the piston stroke clearance (should be 3-5mm) and adjust the piston rod nut accordingly.
Check if the cylinder head cushion pad is aging (hardness > 70A on the Shore scale indicates replacement).
4.2.2Looseness in the Connecting Rod Mechanism
Use a dial indicator to measure the radial clearance of the connecting rod big end bearing (normal ≤ 0.05mm).
Use a hydraulic stretcher to tighten the connecting rod bolts (control the elongation as per manufacturer specifications, e.g., M20 bolts elongation 0.15-0.18mm).
4.2.3Foreign Objects Entering the Cylinder
Shutdown, disassemble the cylinder, and check if the intake filter is damaged or the check valve is detached.
For water-cooled models, check for leaks in the cylinder water jacket (apply pressure of 0.6MPa and hold for 30 minutes with pressure drop <0.05MPa).
5. Overheating Failure
5.1Symptom:
Bearing temperature >80°C or piston rod surface temperature >120°C.
5.2Solutions:
5.2.1Bearing Failure Treatment
Use a vibration analyzer to check the bearing condition (if acceleration effective value >10m/s², replace the bearing).
During installation, use the heating method to assemble the bearing (heating temperature ≤120°C) to ensure an interference fit of 0.02-0.04mm.
5.2.2Lubrication System Improvement
Check for wear on the oil pump gears (if gear tip clearance >0.15mm, repair it).
Add a magnetic oil filter to filter ferromagnetic particles (accuracy ≤ 10μm).
5.2.3Installation Precision Adjustment
Use a laser alignment tool to calibrate the motor and main shaft (parallelism error <0.05mm/m, angular error <0.05°).
Adjust the pre-tightening force of anchor bolts (torque values as per equipment manual, e.g., M16 bolts with torque 200-250N·m).
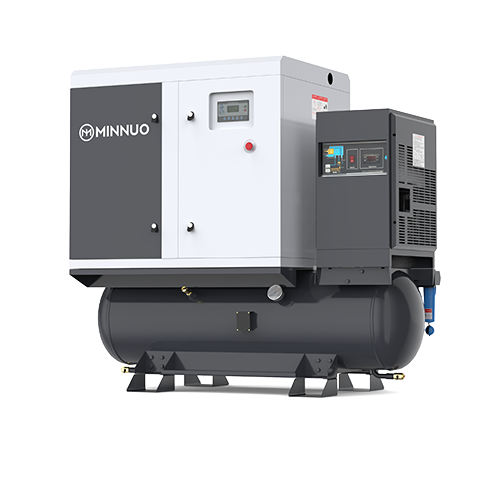
6.MINNUO Air Compressor Professional Solutions
As an industry-leading brand, MINNUO effectively reduces failure rates through the following technological innovations:
6.1Intelligent Diagnostics System
Integrates pressure, temperature, and vibration multi-parameter sensors, using AI algorithms to predict failures (e.g., air valve leak prediction accuracy >95%).
The remote monitoring platform can generate maintenance work orders in real time and support preventive maintenance planning.
6.2Modular Design
Uses quick-disconnect valve components (replacement time <30 minutes), reducing downtime.
Cylinders and piston rings use nano-coating technology (e.g., DLC coating), doubling wear resistance.
6.3High-Efficiency Cooling Technology
Patent cross-flow cooler design lowers discharge temperature by 15-20°C compared to traditional models.
Intelligent temperature control fan system automatically adjusts air volume based on load, saving over 15% energy.
6.4Precision Lubrication Management
Oil-gas separation system uses three-stage filtration (accuracy 0.1μm), ensuring oil cleanliness above NAS grade 8.
The circulating oil circuit is equipped with a thermostat valve to maintain the oil temperature in the optimal working range of 45-55°C.
7.Conclusion
By following a systematic fault diagnosis process and implementing preventive maintenance measures, compressor failure rates can be reduced by over 70%. It is recommended that enterprises establish equipment health records, document each maintenance session, and combine intelligent monitoring systems for precise operation and maintenance.
MINNUO provides customized solutions to help clients optimize the total lifecycle cost of air compressors. For technical support, please contact our professional service team.