Air compressor cylinder failures are a key factor affecting performance and lifespan. This article analyzes common causes of air compressor cylinder failures and offers targeted solutions, focusing on the technical aspects of cylinder liner repair.
Cylinder failures are primarily caused by issues such as wear, scratches, deformation, and cracks. Common causes include poor lubrication, excessive temperatures, and the intrusion of particulate matter. Solutions include regular inspections, use of high-quality lubricants, ensuring the cooling system operates properly, and maintaining cleanliness. Additionally, the cylinder liner repair process is an effective method for addressing cylinder damage, reducing repair costs, and extending equipment lifespan.
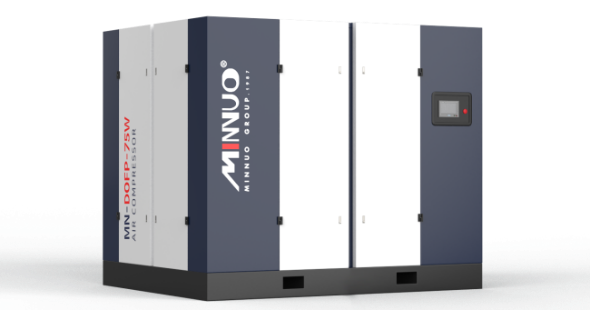
1. Common Cylinder Failures and Causes Analysis
Air compressor cylinder failures mainly manifest in the following ways:
- Cylinder Wear: Due to long-term friction between the piston ring and the inner wall of the cylinder, especially in cases of insufficient lubrication or particulate contamination, the cylinder mirror surface gradually wears, leading to reduced compression efficiency.
- Scoring (Cylinder Scuffing): Due to poor lubrication or high-temperature overload, the piston ring may cause noticeable scratches on the cylinder wall, resulting in gas leakage and reduced sealing capability.
- Cylinder Deformation: High operating temperatures, installation stresses, or prolonged use may lead to deviations in the roundness of the cylinder bore, affecting the stability of piston movement.
- Cracks and Fatigue Damage: Due to long-term stress or material defects, cracks may form in the cylinder, causing abnormal vibrations or noise in the compressor.
These failures are usually closely related to factors such as material selection, lubrication management, cooling conditions, load conditions, and maintenance methods.
2. Cylinder Liner Repair Process
When cylinder wear exceeds 5mm or when structural damages like cracks or scoring occur, the cylinder liner is an economical and effective repair option. The key technical aspects are as follows:
2.1 Cylinder Liner Design and Material Selection
Parameter | Standard Requirement |
Material | Low Pressure: HT200; Medium-High Pressure: HT250/HT300 |
Thickness | Small to Medium Diameter: 510mm; Large Diameter: 1040mm |
Interference Fit Value | (0.0001~0.0002)D (D is the cylinder diameter) |
Clearance Fit Value | (0.00005~0.0001)D (for the last section of the fit area) |
Special Conditions Processing:
- For high-pressure single-acting cylinders, use an interference fit for the first 1/3 of the cylinder liner length near the valve and a clearance fit for the rest of the section to balance sealing and thermal expansion compensation.
- Double interference fit should be applied on the positioning shoulder side to prevent lubricating oil leakage and enhance sealing performance.
2.2 Processing Process Specifications
- Step-by-Step Assembly: A segmented stepped structure (2~3 segments) is used to reduce the difficulty of press-fitting the cylinder liner.
- Reference Positioning: During boring and grinding, the original cylinder body is used as the reference positioning to ensure coaxiality ≤8-grade precision.
- Allowance Control: The boring allowance should be ≤0.5mm to prevent the loss of bonding force, affecting stability.
- Surface Treatment: After honing the inner hole of the cylinder liner, the surface roughness should reach Ra ≤ 0.4μm, and the cylindricity error should be ≤0.02mm.
2.3 Key Quality Indicators
Inspection Item | Precision Requirement |
Outer Surface Roughness | Ra ≤ 1.6μm |
Positioning Flange End Face Perpendicularity | ≥5-grade precision |
Mirror Diameter Deviation | ±0.01mm (adjusted according to cylinder diameter) |
Coaxiality | ≤8-grade precision |
3. Cylinder Maintenance Recommendations
To extend the cylinder’s lifespan and reduce the occurrence of failures, the following measures are recommended:
- Regular Inspection: Measure mirror surface wear every 500 hours, focusing on the area corresponding to the first piston ring.
- Lubrication Management: Use high-quality synthetic lubricants to avoid accelerated wear due to lubricant degradation.
- Cooling System Maintenance: Ensure the cooling system is operating properly to prevent cylinder deformation or fatigue damage caused by overheating.
- Cleaning Management: Regularly remove carbon buildup from the air valve to prevent hard particles from entering the cylinder and accelerating wear.
- Use of Quality Parts: Use MINNUO original piston rings and components to ensure precise matching, thereby improving the overall lifespan of the equipment.
4. Conclusion
Cylinder failures in air compressors are closely related to material selection, lubrication, operating environment, and maintenance management. Proper selection of repair methods, especially the cylinder liner technology, can significantly reduce repair costs and extend the equipment’s service life.
MINNUO recommends that users establish a standardized maintenance system and initiate a repair plan when the mirror surface wear reaches 3mm. For professional technical support, please contact the MINNUO engineering team to obtain customized solutions.