In the context of the booming global aquaculture industry, dissolved oxygen (DO) has become a core factor constraining breeding efficiency and quality. As farming models shift towards high-density and intensive systems, the limitations of traditional aeration technologies are becoming increasingly apparent. How to scientifically and accurately select a suitable oxygen generator has become a critical issue for aquaculture practitioners.
When choosing an oxygen generator for aquaculture, factors such as oxygen output, purity, energy efficiency, equipment durability, and intelligence must be considered. Different farming environments (e.g., high-density ponds, RAS systems, and marine aquaculture) have varying requirements, such as stable dissolved oxygen, low energy consumption, and corrosion resistance. MINNUO PSA oxygen generators, with their advanced technology, energy-saving design, and ability to withstand extreme environments, provide efficient and stable oxygen supply solutions, helping aquaculture improve yield and reduce costs.
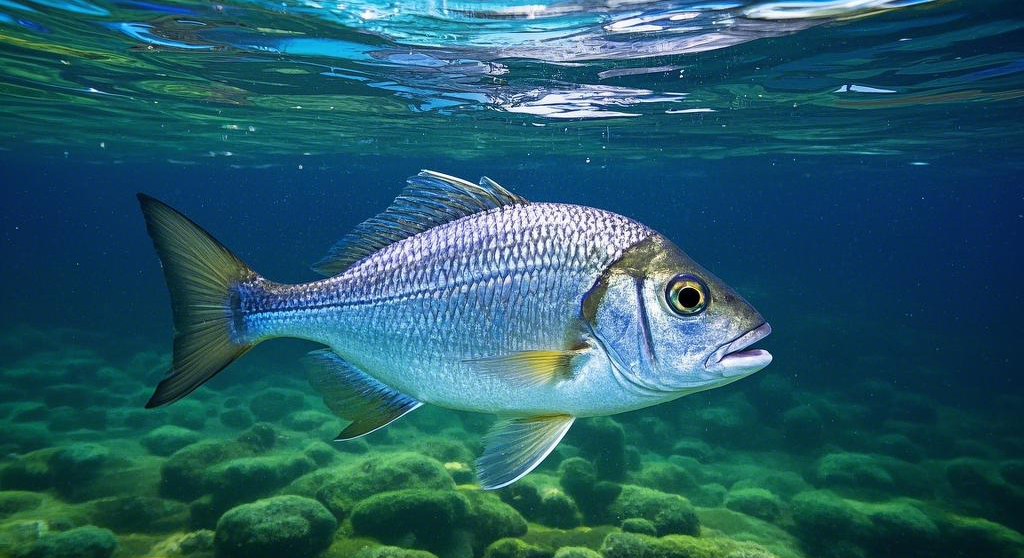
I. Oxygen Supply Challenges in Aquaculture: Challenges in Different Scenarios
(1) High-Density Pond Farming
- Pain Points: Significant diurnal temperature differences lead to thermal stratification in water bodies, causing an imbalance between algae photosynthesis and respiration at different times, resulting in drastic fluctuations in dissolved oxygen levels. Traditional paddlewheel and aerator-type machines often suffer from uneven mixing and oxygen dead zones in large ponds, with high energy consumption. During sudden weather changes, they struggle to quickly increase dissolved oxygen levels, leading to fish stress or even suffocation.
- Requirements: Equipment with adaptive adjustment capabilities is needed, capable of dynamically adjusting oxygen production and aeration strategies based on real-time changes in water parameters such as dissolved oxygen, temperature, and pH, ensuring stable oxygen supply around the clock. The equipment housing must have excellent weather resistance and anti-corrosion properties, with internal circuits and key components designed to withstand high humidity and large temperature fluctuations.
(2) Recirculating Aquaculture Systems (RAS)
- Pain Points: The biological treatment units in RAS systems require extremely precise dissolved oxygen levels. Insufficient oxygen purity can reduce the activity of beneficial microorganisms like nitrifying bacteria, leading to the accumulation of harmful substances such as ammonia and nitrite, and deteriorating water quality. Liquid oxygen storage and transportation require specialized cryogenic tanks and vehicles, which are costly and pose safety risks such as cryogenic burns and explosions.
- Requirements: Oxygen generators must have efficient gas separation technology, stably outputting high-purity oxygen with a purity of ≥90%. The equipment should be compact to fit limited workshop space, with operating noise below 50dB (A), to avoid affecting the growth of farmed organisms. It should also have comprehensive automation interfaces for seamless integration with the RAS system’s PLC control system.
(3) Nearshore Cage and Deep-Sea Farming
- Pain Points: The periodic effects of tides and waves create complex water flow patterns in farming areas. Traditional oxygen generators are prone to displacement and damage in high-flow, high-impact seawater environments. Additionally, long-term exposure to high salt spray and humidity in marine atmospheres leads to rapid corrosion of metal components. Moreover, offshore power supply is limited by the difficulty of cable laying and the stability of power generation equipment, making it hard to ensure continuous and stable operation.
- Requirements: Oxygen generators must use high-strength, corrosion-resistant alloy materials or special engineering plastics, with impact-resistant and displacement-resistant fixing devices. In terms of energy adaptation, they should support multiple energy sources such as solar, wind, and diesel generators, with intelligent energy switching and management systems to ensure low-energy, stable operation.
(4) Fry and Hatcheries
- Pain Points: Fry and fish eggs are highly sensitive to water flow and dissolved oxygen during the initial stages of hatching and cultivation. Traditional aeration methods, which produce large bubbles and strong water currents, can cause physical damage to the larvae, affecting survival rates and growth.
- Requirements: Oxygenation equipment based on micro-nano bubble technology is needed. Special microporous aeration devices release oxygen in the form of micron-sized bubbles, achieving uniform and gentle oxygenation, with bubble diameters controlled below 50 microns and operating noise below 60dB (A).
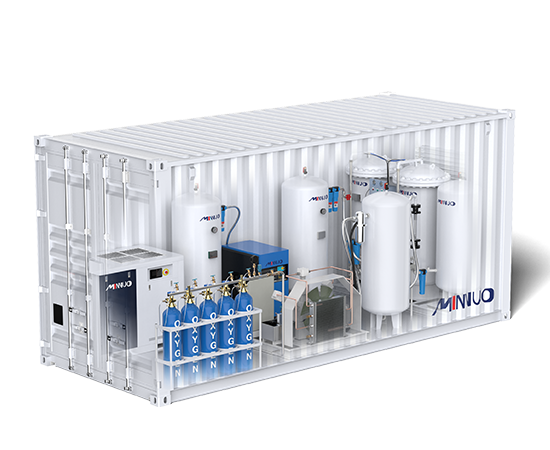
II. Five Core Indicators for Choosing an Oxygen Generator
(1) Oxygen Output Capacity and Purity
- Oxygen Demand Calculation: Based on the respiratory metabolism model of the farmed species, combined with factors such as stocking density, water volume, and temperature, use the formula:
- O₂ demand = Stocking density × Individual oxygen consumption rate × Water volume × Safety factor
- to accurately calculate the total oxygen demand. For example, at 25°C, the individual oxygen consumption rate of salmon is approximately 0.2mg/g·h. If the stocking density is 50kg/m³ and the water volume is 1000m³, with a safety factor of 1.5, the hourly oxygen demand is:
- 50 × 1000 × 0.2 × 1.5 = 15000g = 15kg
- Technology Comparison: PSA (Pressure Swing Adsorption) technology, based on the selective adsorption of different gas molecules by molecular sieves, adsorbs nitrogen and other impurities under pressure and releases them during depressurization, achieving high-purity oxygen with a purity of ≥95%. Membrane separation technology, which separates gases based on their permeation rates through polymer membranes, typically achieves purities below 90%, making it more suitable for scenarios with lower purity requirements.
(2) Energy Efficiency and Operating Costs
- Energy Consumption Indicators: The key metric for energy efficiency is the power consumption per unit of oxygen produced (kWh/Nm³). For example, a high-efficiency oxygen generator with a unit energy consumption of 0.5kWh/Nm³ can save 37.5% in electricity costs compared to traditional models with 0.8kWh/Nm³.
- Energy-Saving Technologies: Frequency conversion drive technology can adjust motor speed in real-time based on actual oxygen demand. Intelligent load adjustment systems can precisely control the working load of the oxygen generator based on dissolved oxygen feedback, achieving energy-efficient operation.
(3) Environmental Adaptability and Durability
- Protection Level: In coastal areas, oxygen generators with an IP65 or higher protection rating can effectively prevent dust and water splashes from eroding internal circuits and mechanical components. 316L stainless steel, containing molybdenum, offers excellent resistance to pitting and crevice corrosion in seawater environments.
- Special Environment Adaptation: Oxygen generators in cold regions need electric heating and anti-freeze modules to ensure gas pipelines and key components do not freeze in low temperatures. In dusty environments, efficient air pre-filters and fine filters are necessary to prevent dust from entering the oxygen generation system and affecting molecular sieve performance.
(4) Intelligence and Compatibility
- IoT Technology: IoT-enabled oxygen generators can collect real-time operating parameters (e.g., oxygen flow, purity, energy consumption) and dissolved oxygen data via sensors, transmitting them wirelessly to cloud servers. Users can monitor device status remotely via mobile apps or computers, enabling remote operation and fault warning.
- System Integration: With standard communication protocol interfaces such as RS485 and Modbus, oxygen generators can seamlessly integrate with farm management systems (e.g., water quality monitoring, feeding control systems), automatically starting and stopping based on dissolved oxygen changes to optimize farming processes.
(5) Maintenance Costs and After-Sales Service
- Consumable Lifespan: Filter replacement cycles are typically 3-6 months, while high-quality molecular sieves can last 5-8 years, effectively reducing long-term maintenance costs.
- Service Network: Choosing a brand with a global network of spare parts and after-sales service ensures that in the event of equipment failure, a response can be provided within 12 hours, with spare parts replacement and on-site repair services available within 24 hours.
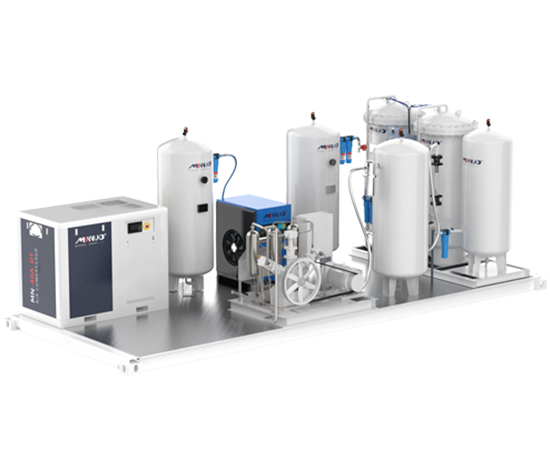
III. MINNUO PSA Oxygen Generator: A Tailored Solution for Aquaculture
(1) Precise Oxygen Supply, Stable Yield Increase
MINNUO PSA oxygen generators use advanced pressure swing adsorption technology to efficiently separate oxygen from nitrogen in the air through molecular sieves. Our oxygen generators achieve a purity of 93%±3%, with customizable purity up to 99.5%, and a flow range of 1-1000Nm³/h, meeting the needs of different farming scales. The multi-machine parallel design, coordinated by an intelligent control system, ensures stable and uniform oxygen output, providing a stable dissolved oxygen environment for farmed organisms, effectively promoting growth and increasing yield. Additionally, special aeration technology optimizes gas-liquid mixing, significantly improving oxygen dissolution efficiency, allowing oxygen to be more fully utilized by farmed organisms.
(2) Intelligent Energy Saving, Cost Reduction, and Efficiency Improvement
Equipped with advanced AI algorithms, the device can collect multi-source data such as dissolved oxygen, temperature, and stocking density in real-time, dynamically adjusting the oxygen generator’s working frequency and output to achieve precise oxygen supply control. Compared to traditional equipment, it can save over 25% in energy, effectively reducing long-term operating costs. Additionally, it can be equipped with a photovoltaic energy storage system, using solar power in areas with sufficient sunlight to store electricity and power the oxygen generator, enabling off-grid operation and further reducing energy costs and carbon emissions.
(3) Reliable Operation in Extreme Environments
With an IP66 protection rating, the device offers excellent dust and water resistance. It has undergone 1000 hours of salt spray testing, demonstrating strong resistance to salt spray corrosion. The lightning protection design complies with ISO14223 standards, effectively protecting the device from severe weather damage. With a special temperature control system and low-temperature resistant materials, it can operate stably in a wide temperature range from -30°C to 50°C, ensuring normal operation in both the high-temperature, high-humidity climates of Southeast Asia and the cold climates of Northern Europe.
(4) Quiet Operation, Eco-Friendly
Through optimized internal structural design, soundproofing materials, and shock-absorbing devices, the operating noise is ≤55dB (A), avoiding disturbance to farmed organisms and reducing stress. The oxygen generator does not require liquid oxygen, eliminating the risks associated with liquid oxygen transportation. Additionally, it reduces carbon emissions by over 60% compared to traditional oxygen generation methods, aligning with sustainable development principles and helping maintain a stable farming ecosystem.
(5) Full-Cycle Service Support
MINNUO provides professional and comprehensive full-cycle services. In the initial stages, we tailor scientific and reasonable oxygen supply solutions based on the customer’s farming scale, species, and local climate and geographical conditions, ensuring precise equipment selection that matches actual needs. During equipment use, we offer 7×24-hour technical consultation services.In addition, we will regularly revisit customers, proactively understand the operating status of the equipment, provide equipment maintenance and servicing suggestions, extend the service life of the equipment, ensure the long-term and stable operation of the equipment, and safeguard the stable production of aquaculture.
IV. Conclusion
Selecting an oxygen generator is a systematic project impacting aquaculture’s economic returns, ecological benefits, and sustainability. MINNUO PSA generators, with their advanced technology, superior performance, and comprehensive service, provide reliable, cost-effective, and eco-friendly solutions for global aquaculture.
What are you waiting for? Visit MINNUO now to get your customized gas solution!