In modern industrial production, air compressors have become critical air supply equipment. As the core component of the air compressor, the main unit, once worn or damaged, will significantly impact the performance of the entire compression system. Therefore, in-depth research on how to handle wear or damage to the compressor main unit holds substantial practical significance.
When dealing with wear or damage to the compressor main unit, precise maintenance or refurbishment measures should be employed to restore its performance. Traditional maintenance faces limitations such as reverse engineering risks, coating regeneration challenges, and system compatibility pitfalls. In contrast, professional refurbishment technologies like digital mapping, plasma remelting, and dynamic balance correction can effectively repair worn components and even enhance performance.
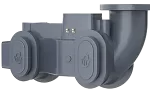
1.The Core Position and Technical Characteristics of the Compressor Main Unit
1.1 Working Principles and Classification
As the core component of the compressor, the main unit is often referred to as the “heart” of the compressor, where the actual compression process takes place. From a technical and physical perspective, compression principles are mainly divided into positive displacement compression and dynamic compression. Positive displacement compression achieves compression by reducing the volume of air, employing technologies such as piston, screw, rotary tooth, or screw rotor compressors. Dynamic compression, on the other hand, uses centrifugal or turbo technology to compress air or gas by altering speed. In practical applications, different compression principles and technologies can be selected based on the required air volume (FAD), pressure (bar), and air quality for the production process. Among these, screw compressors are widely used in industrial applications due to their efficiency and stability, and can be further divided into oil-injected and oil-free types.
1.2 Technical Characteristics
Whether it is oil-lubricated or oil-free precision coating design, the core value of the main unit is reflected in the following three points:
1.2.1 Precision Tolerance Control
Micron-level clearance between rotors directly affects compression efficiency, and even minor tolerance changes can lead to significant performance fluctuations. In screw compressors, the machining precision of the rotors is extremely high, typically with clearances controlled within a few microns to tens of microns. Improper tolerance control can increase gas leakage, reducing compression efficiency. For example, when rotor clearance increases by 10 microns due to wear, the compressor’s energy consumption may increase by 5% – 8%, and air production capacity may drop by 10% – 15%.
1.2.2 Coating Technology Barriers
The Teflon coating on oil-free models requires special processing techniques, and its integrity is crucial for the compressor’s performance and lifespan. Teflon coatings offer excellent wear resistance, corrosion resistance, and low friction coefficients, effectively protecting rotor surfaces and reducing wear and friction. However, the preparation of Teflon coatings requires advanced vacuum plasma spraying technology, demanding high standards for equipment and processes. Once the coating peels or is damaged, the rotor surface is directly exposed, accelerating wear and reducing the compressor’s performance and lifespan.
1.2.3 Dynamic Balance System
Mechanical stability during high-speed rotation determines the equipment’s lifespan, and unbalanced operation can accelerate component wear and increase failure risks. During operation, the rotor speed of the compressor main unit can reach several thousand revolutions per minute or higher. If the rotor’s dynamic balance is poor, severe vibration can occur during high-speed rotation, causing additional impact and wear on bearings, seals, and other components, and potentially leading to damage to the overall structure of the equipment. For example, a compressor experiencing rotor dynamic balance issues saw vibration levels three times higher than normal during operation, leading to premature bearing failure and significantly increased repair costs.
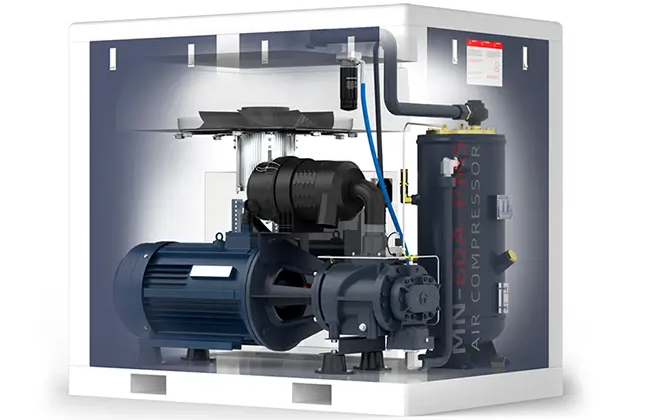
2.Deep Mechanisms of Main Unit Performance Degradation
Under conditions of dust, high temperature, or overload, main unit wear exhibits progressive characteristics:
2.1 Rotor Coating Peeling
Leading to increased friction coefficients, studies show this can reduce energy efficiency by 12 – 18%. In environments with high dust levels, such as mining and construction, dust particles continuously erode the rotor surface coating. Over time, the coating gradually peels off. For instance, in a cement plant’s air compressor operating in a high-dust environment, after three years, 30% of the rotor coating had peeled off, reducing energy efficiency by 15% and significantly increasing energy consumption per unit of air produced.
2.2 Tolerance Expansion
Causing gas backflow, reducing volumetric efficiency by over 20%, severely impacting the compressor’s air production capacity. With prolonged operation, the fit tolerances between components gradually expand. In screw compressors, increased clearance between the screw and the housing exacerbates gas backflow during compression, reducing the actual amount of gas discharged. A chemical plant’s screw compressor experienced a 25% reduction in volumetric efficiency due to tolerance expansion, gradually failing to provide sufficient compressed air for production needs.
2.3 Geometric Deformation
Disrupting dynamic balance, increasing vibration by 30dB, affecting not only the equipment’s lifespan but also potentially impacting surrounding equipment. High temperatures and high loads can cause geometric deformation of main unit components, such as screw bending or distortion. This disrupts the rotor’s dynamic balance during high-speed rotation, causing severe vibration. For example, a steel plant’s compressor main unit operating in high temperatures experienced slight screw bending, increasing vibration from 60dB to 90dB, severely damaging the compressor’s bearings and seals, and causing resonance effects on surrounding pipes and valves, shortening their lifespan.
At this stage, although the equipment can still operate, energy consumption per unit of air produced can surge by 40%, becoming a hidden cost black hole for enterprises, severely affecting production efficiency and competitiveness.
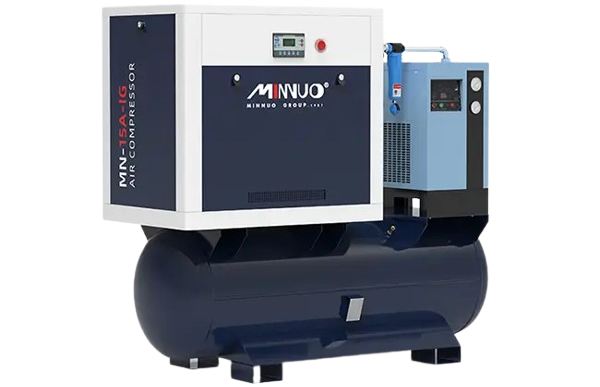
3.Limitations of Traditional Maintenance and Feasibility of Refurbishment
3.1 Misconceptions in Traditional Maintenance
Common maintenance attempts often fall into three major misconceptions:
3.1.1 Reverse Engineering Risks
Non-original disassembly leads to tolerance mismatches, making it difficult to restore the main unit’s original high-precision performance. The compressor main unit is a highly precise device, with internal component fit tolerances strictly designed and calibrated. Non-original maintenance personnel, lacking professional tools and techniques, often fail to restore original tolerance precision during reassembly. For example, a company choosing a non-professional repair service to save costs found post-repair that the compressor’s energy consumption significantly increased and air production capacity decreased, due to tolerance mismatches from improper disassembly.
3.1.2 Coating Regeneration Challenges
Teflon recoating requires vacuum plasma technology, which general maintenance cannot achieve. As mentioned, Teflon coating preparation requires advanced vacuum plasma spraying technology, demanding specialized equipment and technicians. General maintenance firms lack these capabilities, and even attempts at recoating often fail to meet original coating quality and performance standards. A repair shop attempting Teflon recoating on an oil-free screw compressor rotor, due to technical and equipment limitations, resulted in uneven coating thickness and poor wear resistance, leading to rapid reoccurrence of faults.
3.1.3 System Compatibility Pitfalls
Modified parts disrupt the compressor’s thermodynamic balance, affecting overall performance and stability. During maintenance, using incompatible modified parts can alter the compressor’s thermodynamic parameters, disrupting overall balance. For example, replacing seals with unsuitable ones can increase gas leakage; using non-specification lubricants can affect lubrication and cooling performance. A company using cheaper non-original seals during maintenance experienced significant gas leakage and unstable pressure, severely impacting production.
3.2 Feasibility of Refurbishment
MINNUO’s refurbishment technology achieves regeneration through three core breakthroughs:
3.2.1 Digital Mapping System
Laser measurement reconstructs the rotor’s 3D model with ±3μm precision, providing a data foundation for precise repair. Professional refurbishment centers use advanced laser measurement technology to comprehensively scan and measure worn rotors, quickly and accurately obtaining geometric shape and size data. This data rebuilds the rotor’s 3D model, precisely analyzing wear locations and extent, providing a scientific basis for subsequent repairs. For example, a refurbishment center using digital mapping on a worn screw rotor identified a minor wear area, allowing precise data measurement and targeted repair, ensuring restored rotor precision and performance.
3.2.2 Plasma Remelting Process
Restores coating to the initial 0.25mm standard thickness, reinstating the coating’s protective and performance-enhancing functions. For coating peeling issues, professional refurbishment uses plasma remelting to reapply Teflon and other coating materials to the rotor surface without damaging the base, ensuring 0.25mm thickness. This process ensures excellent adhesion, wear resistance, and corrosion resistance. Rotors repaired with plasma remelting can achieve or exceed new rotor performance and lifespan in actual operation.
3.2.3 Dynamic Balance Correction
Controls vibration within ISO 1940 G2.5 standards, ensuring stable operation and extended lifespan. During refurbishment, high-precision dynamic balance testing equipment corrects the rotor’s dynamic balance. According to ISO 1940 G2.5 standards, rotor imbalance is strictly controlled, reducing vibration to specified levels. For example, a refurbished compressor main unit saw vibration drop from 80dB to 40dB post-correction, operating more smoothly with significantly reduced wear on bearings and seals, greatly extending lifespan.
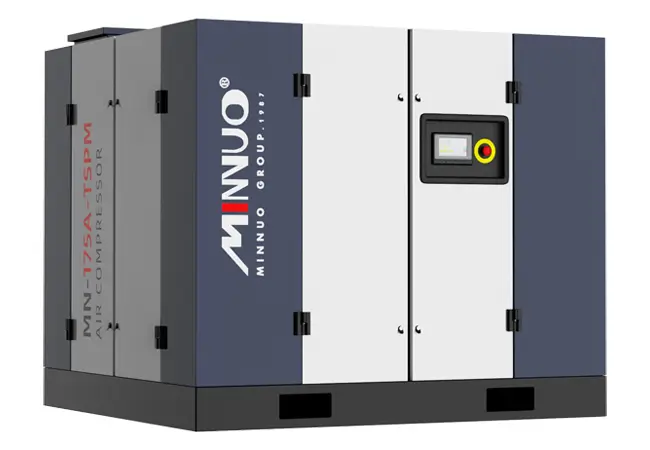
4.Engineering Value of MINNUO Replacement Plan
Our solution creatively constructs a circular technical-economic model:
4.1 Performance Upgrade Path
New model rotor sets improve FAD by 5 – 8%, restoring and enhancing equipment performance. The MINNUO replacement plan uses new model rotor sets with advanced design and manufacturing technologies and materials, effectively enhancing compressor performance. For example, a company participating in the MINNUO replacement plan saw a 6% increase in free air delivery (FAD) after replacing rotor sets, meeting growing air demand and improving production efficiency.
4.2 Carbon Neutral Benefits
Refurbishment energy consumption is only 15% of new unit manufacturing, aligning with current environmental and sustainable development requirements. In the global context of environmental and sustainable development advocacy, the MINNUO replacement plan offers significant carbon neutral benefits. Refurbishment mainly repairs and upgrades key components of the original main unit, significantly reducing energy consumption compared to manufacturing new compressor main units. Statistics show refurbishing a compressor main unit consumes only 15% of the energy required for a new unit, greatly reducing carbon emissions and contributing to corporate carbon neutral goals.
4.3 TCO Optimization Model
Saves 45% cost compared to new unit procurement, extends MTBF to 50,000 hours, reducing total cost of ownership and improving equipment reliability. From a long-term operational cost perspective, the MINNUO replacement plan offers clear advantages. Compared to purchasing new compressor main units, the replacement plan saves 45% in costs, a significant saving for enterprises. Additionally, refurbishment and upgrades extend mean time between failures (MTBF) to 50,000 hours, greatly improving reliability and reducing downtime and repair costs due to equipment failure.
5.Conclusion
In summary, when the compressor main unit experiences wear or damage, selecting appropriate replacement, refurbishment, or maintenance solutions can rejuvenate the compressor, meeting production needs. Professional refurbishment is not only an economical choice but also a crucial pivot for the green transformation of manufacturing.
If you wish to enjoy MINNUO‘s premium services, please feel free to inquire!