Oil-free air compressors are widely used in industries such as pharmaceuticals, food production, and electronics, where high-quality air compression is crucial. However, water leakage in the sealing components of an oil-free air compressor not only reduces the performance of the equipment but can also lead to a series of severe secondary faults, affecting production. This article will provide an in-depth analysis of the causes of water leakage in oil-free air compressor sealing components and offer specific solutions and preventive measures from a professional perspective.
The main causes of water leakage in oil-free air compressor sealing components include seal aging, poor sealing, improper assembly, or damage. Leakage is typically manifested as water marks on the exterior of the seal housing or as coolant water leaking through the tie rods. Solutions include regular inspection and replacement of aged components, ensuring accurate assembly, selecting suitable sealing materials, and enhancing maintenance to prevent leakage due to overloads or improper operation.
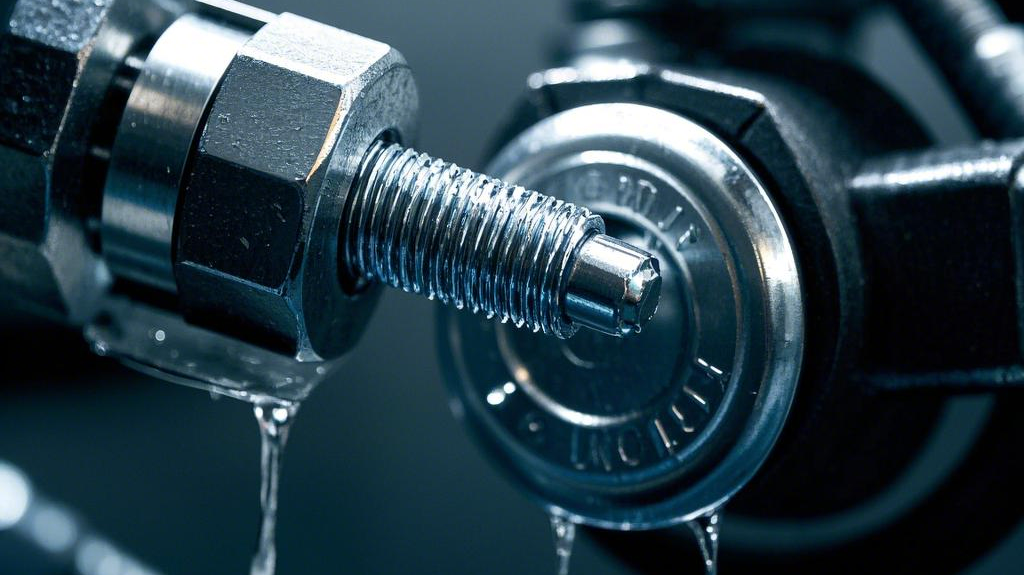
I.Water Leakage Phenomena
Water leakage in the gas seal assembly of the oil-free air compressor typically manifests in two forms. First, water stains or slight leakage traces can appear around the bolts fixing the gas seal on the outside of the gas seal housing. This type of leakage is more apparent and easy for inspection personnel to detect. Initially, there may only be a small amount of water near the bolts, but over time, the leakage may worsen. Second, cooling water may leak or drip slowly along the pull rod inside the gas seal. Since this type of leakage occurs inside the equipment, it is less noticeable and often requires monitoring indirect phenomena, such as increased exhaust temperature or emulsification of lubricating oil, to detect.
II.Causes of Water Leakage
(A) Causes of Water Leakage on the Outer Side of the Gas Seal Assembly
1.O-Ring Aging
The O-ring, which is a key sealing component at the lower end of the gas seal assembly, operates in a complex environment of high temperature, high pressure, and mechanical vibration. Under high temperatures, the rubber material of the O-ring undergoes molecular chain fracture and cross-linking, which increases its hardness and decreases its elasticity. High-pressure environments subject the O-ring to greater extrusion pressure, accelerating wear. Mechanical vibrations cause relative displacement between the O-ring and the sealing surface, further compromising its sealing ability. Additionally, chemical substances in cooling water may react with the O-ring, causing corrosion and aging. These combined factors gradually degrade the sealing performance of the O-ring, ultimately leading to leakage.
2.Casting Defects in the Cylinder Body
During the casting process of the cylinder body, improper control of parameters such as pouring temperature, cooling rate, and material impurities can lead to defects like shrinkage cavities, porosity, and cracks. These defects, under the repeated action of mechanical and thermal stresses, may expand and connect, forming a leakage pathway that results in cooling water leakage.
(B) Causes of Internal Water Leakage in the Gas Seal Assembly
1.Sealing Gasket Issues
The sealing gasket at the connection between the gas seal housing and the cylinder body relies on its elasticity and fit with the sealing surface. When the gasket ages, its modulus of elasticity increases, losing its ability to effectively fill microscopic irregularities in the sealing surface, leading to sealing failure. Additionally, insufficient gasket thickness results in inadequate sealing pressure, also causing leaks. During the piston’s downward movement, the internal pressure in the cylinder rises sharply, and the piston’s high-speed movement generates impact loads, which exacerbate the deformation and wear of the gasket, allowing cooling water to enter the cylinder more easily.
2.Cylinder Bed Issues
The cylinder bed, a crucial sealing component connecting the cylinder body and the cylinder head, prevents leakage of gases and cooling water from inside the cylinder. Over time, the cylinder bed may become damaged due to prolonged exposure to high-temperature, high-pressure gases and mechanical vibrations, or if cylinder head bolts are not tightened according to specified torque and sequence. When this happens, high-pressure gases and cooling water may leak through the sealing gap and enter the gas seal, causing leakage. Severe leakage in the cylinder bed may worsen lubrication conditions between the piston and cylinder wall, increasing wear and potentially leading to serious accidents like piston seizure or cylinder damage.
3.Gas Seal Assembly Housing Issues
The gas seal assembly housing is constantly in contact with cooling water. During operation, frequent temperature changes cause the housing to experience alternating thermal stresses. According to the principle of thermal expansion and contraction, the housing expands when the temperature rises and contracts when it lowers, generating fatigue stress inside the housing. Moreover, dissolved oxygen, acidic or alkaline substances in the cooling water may cause electrochemical corrosion on the housing surface, forming corrosion pits and cracks. Over time, these pits and cracks can expand, and when they connect, a leakage pathway is formed. Gas seal components with casting defects, such as sand holes or pores, are more susceptible to breakage, cracking, or perforation due to the combined effect of thermal stress and corrosion, leading to water leakage.
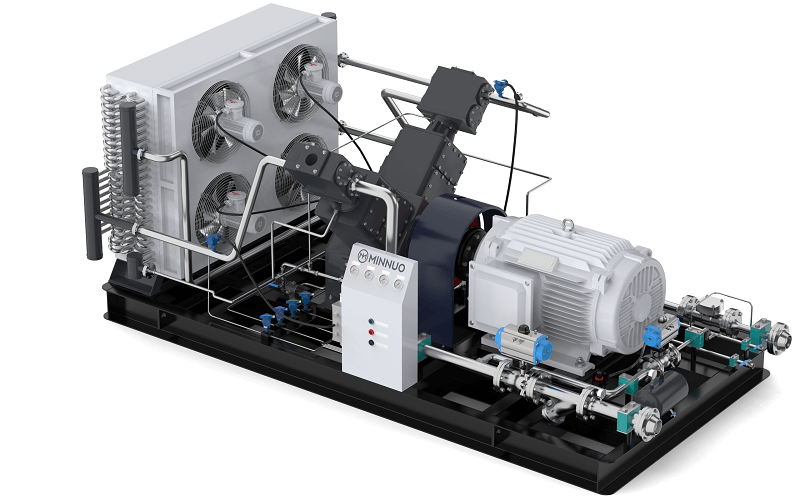
III.Solutions
(A) Handling External Water Leakage in the Gas Seal Assembly
1.O-Ring Replacement
When replacing the O-ring, it is essential to select one that meets the equipment’s specifications, considering factors such as model, working pressure, and temperature. The O-ring material should typically be fluorocarbon rubber (FKM) or silicone rubber (VMQ), as these materials are resistant to oil, chemical corrosion, and high temperatures. During installation, ensure the sealing groove is clean, free of contaminants, and not scratched. Use specialized tools and follow correct installation procedures to ensure the O-ring is positioned accurately and free of distortion or deformation.
2.Cylinder Body Repair or Replacement
For minor defects in the cylinder body, such as small shrinkage cavities or porosity, argon arc welding can be used for repairs. Prior to welding, thoroughly clean the defect area to remove impurities like oil and rust, and select an appropriate bevel for the weld. Control welding parameters such as current, voltage, and speed to avoid deformation due to excessive heat input. After welding, grind and polish the welded area to ensure a smooth surface.
For more serious defects like cracks, a crack-stopping hole and repair welding can be applied if the cracks are short and not through the entire cylinder body. For longer or through cracks, cylinder replacement should be considered. When replacing the cylinder body, select one that matches the original equipment model and install it according to the assembly procedure. After repair or replacement, perform a hydrostatic test at 1.25 to 1.5 times the working pressure for at least 30 minutes to ensure the cylinder’s sealing and structural integrity.
(B) Handling Internal Water Leakage in the Gas Seal Assembly
1.Sealing Gasket Handling
Select a new gasket based on the equipment’s design and technical specifications. Measure the dimensions of the cylinder body and gas seal housing precisely using calipers and depth gauges to determine the required thickness of the gasket. Gaskets should be made from asbestos-free rubber, PTFE, or other high-performance materials. Clean and polish the sealing surfaces to remove dirt, rust, and projections, ensuring a smooth, clean surface. Apply a layer of high-performance polymer sealant like anaerobic or silicone sealant to enhance sealing performance. Install the gasket carefully, ensuring proper positioning without misalignment or wrinkles.
2.Cylinder Bed Handling
Replace the damaged cylinder bed with a new one according to the equipment’s repair manual. Before installation, check that the sealing surfaces of the cylinder body and cylinder head are flat, and if necessary, repair minor scratches or deformations by grinding. Tighten the cylinder head bolts with a calibrated torque wrench, following the specified torque values and tightening sequence, typically using a cross-tightening method. Tighten gradually in multiple stages, ensuring uniform pressure on the cylinder bed to maintain its sealing ability.
3.Gas Seal Assembly Housing Handling
Minor defects like cracks or sand holes in the gas seal assembly housing can be repaired with welding or sealing methods. For welding, choose materials and techniques suitable for the housing material, such as cast iron electrodes for cast iron housings or argon arc welding for aluminum alloy housings. Pre-treat the defect area to remove oxidation and impurities before welding. After welding, grind and perform anti-corrosion treatments. For severe defects, like large cracks or perforations, the gas seal assembly housing may need to be replaced. When replacing, select high-quality original parts or compliant substitutes and install them according to the assembly guidelines. After repair or replacement, conduct thorough quality checks, including visual inspections, dimensional measurements, and sealing tests.
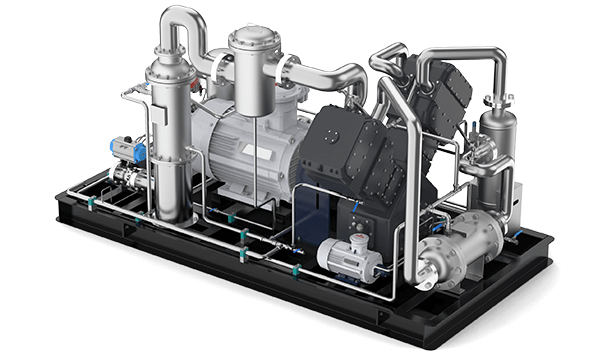
IV.Preventive Measures
(A) Establish a Comprehensive Inspection System
Develop a detailed inspection plan that defines inspection content, frequency, and responsibility. Inspections should cover equipment appearance (looking for water, oil, or air leaks), monitoring of operational parameters (e.g., exhaust pressure, temperature, flow, motor current), and checks of vibration and noise levels. The frequency of inspections should be based on the equipment’s operating conditions and age, with daily checks for continuous operations and weekly comprehensive inspections. Ensure that inspection personnel are well-trained and experienced, and can use various tools such as thermometers, pressure gauges, and vibration testers to detect abnormalities.
(B) Optimize Equipment Maintenance
Develop a reasonable maintenance plan based on the equipment manual and actual operational conditions. Regularly replace consumable parts like O-rings, gaskets, cylinder beds, and piston rings. Generally, O-rings and gaskets should be replaced every 1-2 years, while cylinder beds and piston rings should be replaced every 3-5 years, depending on wear. Also, perform regular cleaning, lubrication, and cooling system maintenance to remove contaminants and scale from the cooling water. Ensure that moving parts, like crankshafts, connecting rods, and pistons, are lubricated to reduce wear.
(C) Enhance Operator Skills
Provide comprehensive training on the equipment’s structure, working principles, operation procedures, and troubleshooting methods. Conduct skills assessments to ensure operators fully understand the equipment and can perform necessary maintenance. Strengthen operators’ sense of responsibility and safety awareness by implementing strict operational and maintenance management systems.
(D) Use Advanced Monitoring Technologies
Use advanced monitoring technologies like vibration, temperature, and leakage monitoring to track the operation of the oil-free air compressor. Install sensors at critical points to collect data and analyze it through monitoring software. When abnormal data is detected, operators can take action before serious problems occur, such as adjusting operating parameters, shutting down equipment, or initiating maintenance.
V.Our Advantages
(A) Advanced Sealing Design
MINNUO’s oil-free compressors feature a unique sealing structure design, employing multi-layer composite sealing technology. For example, the sealing component not only uses conventional O-rings and sealing gaskets but also adds a special sealing sleeve. This sleeve is made from high-strength, wear-resistant, and highly sealed materials, effectively dispersing pressure and reducing the strain on O-rings and gaskets, thereby extending their lifespan. Furthermore, this multi-layer composite sealing structure is better suited to complex operational environments and effectively prevents coolant leakage.
(B) Premium Material Selection
For critical components, our O-rings are made from imported high-performance rubber materials. These materials offer excellent resistance to high temperatures, chemical corrosion, and wear. Compared to standard rubber materials, they maintain superior sealing performance even in harsh environments, significantly reducing the risk of leakage due to O-ring aging. Sealing gaskets are made from new asbestos-free polymer materials, which not only offer excellent sealing performance but also have excellent anti-aging and anti-deformation properties, ensuring long-term stable sealing effects. For the sealing component housing and cylinder, MINNUO uses high-strength, corrosion-resistant alloy materials, which improve the component’s resistance to corrosion and structural strength, reducing water leakage caused by casting defects and corrosion.
(D) Precision Manufacturing Process
MINNUO boasts advanced manufacturing processes and strict quality control systems. During the casting process of the oil-free compressor cylinders and other key components, we utilize advanced lost-wax casting techniques and CNC machining technology, allowing for precise control of the casting parameters to ensure the dimensional accuracy and internal quality of the components. This effectively reduces casting defects such as shrinkage cavities, porosity, and cracks. Additionally, during the assembly process, we strictly adhere to high-precision assembly standards, ensuring the flatness and fitting of all sealing surfaces, further enhancing the equipment’s sealing performance.
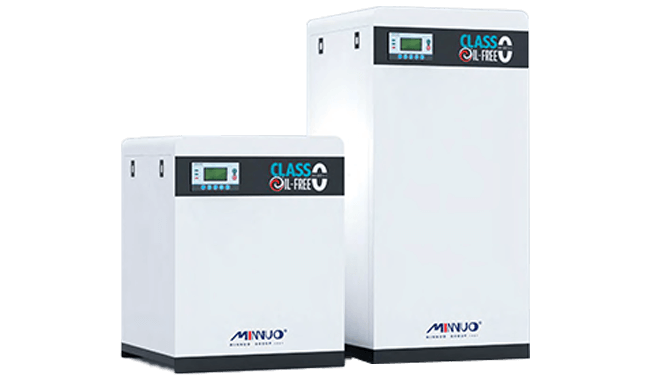
VI.Conclusion
Although the occurrence of water leakage in oil-free air compressor sealing components is relatively rare, when it does happen, it can significantly affect equipment safety and production. Especially for older equipment with insufficient maintenance, sealing components are more prone to leakage. Therefore, a scientifically reasonable periodic inspection system should be established, using advanced testing technologies for comprehensive maintenance to detect and address potential faults promptly.
If you’d like to learn more about MINNUO compressors, feel free to contact us!