As the weather gradually turns colder, is your air compressor ready for the winter? Air compressors typically operate in an ideal temperature range of 5°C to 30°C (40°F to 90°F). When temperatures fall below this range, the efficiency, reliability, and lifespan of the entire compressed air system can be affected. This article will delve into the impact of cold weather on compressed air systems and provide solutions to mitigate the risks associated with low temperatures.
Cold weather can cause issues such as difficulty starting the compressor, thickening of lubricants, freezing of pipes, and icing of refrigerant dryers. Solutions include low-temperature startup protection, optimizing oil viscosity, antifreeze designs, refrigerant dryer optimization, the use of corrosion-resistant materials, and regular maintenance with smart monitoring to ensure stable system operation.
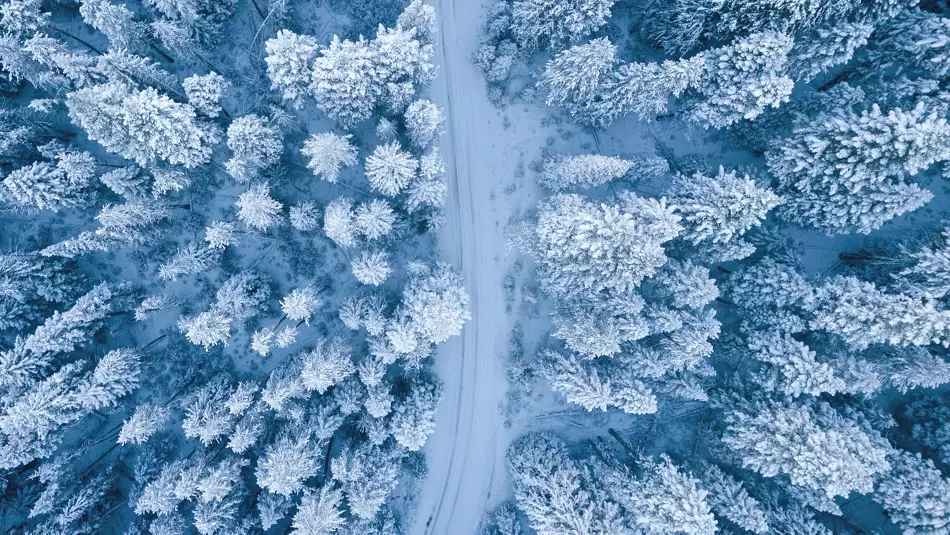
The Impact of Cold Weather on Compressed Air Systems
Cold weather can lead to a variety of short-term and long-term issues that not only affect the performance of compressed air systems but may also shorten their lifespan. Below are the primary problems that can occur in low temperatures:
Condensation and Freezing
Cold temperatures cause water vapor in compressed air to condense. As the air cools, moisture accumulates and settles in various system components, such as pipes, filters, and storage tanks. If the temperature drops further, this condensed water may freeze, leading to blockages and damage to key components.
- Impact: Frozen moisture can block filters, valves, and other critical parts, obstructing airflow, and potentially causing system failure and expensive repairs.
Compressor Startup Failure
In cold weather, the viscosity of compressor oil increases, making it thicker and reducing its lubrication efficiency. Some compressors are equipped with low-temperature startup protection switches, which automatically prevent startup when the ambient temperature is too low.
- Impact: A compressor failure to start will halt production, and the downtime can result in significant financial losses. Additionally, increased oil viscosity raises internal friction, leading to accelerated wear of components.
Thickening of Lubricants
Cold temperatures cause compressor oil to thicken, which reduces its lubricating properties. Poor lubrication increases friction, requiring the compressor to consume more energy to operate.
- Impact: Increased energy consumption, heightened friction, and accelerated component wear result in reduced equipment efficiency and potentially premature failure.
Freezing of Refrigerant Dryers
Refrigerant dryers, a common component in compressed air systems, are used to remove moisture from the air. However, in cold weather, the moisture inside the dryer may freeze, impeding airflow and even damaging the equipment.
- Impact: Ice formation in the refrigerant dryer reduces its efficiency, eventually preventing moisture from being removed from the air, which affects the normal operation of downstream equipment and increases repair costs.
Increased Risk of Corrosion
Due to the reduced efficiency of the dryer in cold weather, the accumulation of condensate increases, and prolonged exposure to moisture leads to corrosion.
- Impact: Long-term moisture exposure can cause internal rusting, leading to a decrease in component strength and sealing, increasing the risk of leaks, and potentially causing complete system failure.
Preparing Compressed Air Systems for Cold Weather
To protect compressed air systems from the harm caused by low temperatures, a series of preventive measures can be taken. These measures help maintain system efficiency, reduce downtime risks, and extend the equipment’s lifespan.
Keep the Compressor Room Warm
The ideal operating temperature for compressors should remain between 5°C and 30°C. In cold regions, it is critical to ensure the compressor room stays within this range to prevent damage to the equipment.
- Solution: Install heating equipment or use local space heaters to maintain the temperature of the compressor room above 5°C (40°F). This will prevent the equipment from freezing and ensure the compressor operates efficiently even in cold weather.
Insulate Pipes and Components
Cold weather can cause exposed pipes and other system components to freeze, obstructing airflow and potentially causing physical damage. Proper insulation can significantly reduce this risk.
- Solution: Use pipe insulation materials or heating tapes on exposed pipes to maintain a stable temperature and prevent freezing. This helps avoid damage caused by ice blockages.
Regularly Drain Condensate
Compressors naturally generate condensate during operation. In winter, if condensate is not drained in time, it will freeze, leading to pipe bursts or other damage.
- Solution: Ensure the system is equipped with automatic condensate drainage devices to regularly discharge accumulated moisture. If the system lacks such devices, it is advisable to manually drain the condensate weekly to prevent damage from freezing.
Monitor and Adjust Oil Viscosity
As mentioned earlier, cold temperatures cause compressor oil to thicken, reducing lubrication. Poor lubrication leads to decreased compressor efficiency and may accelerate component wear.
- Solution: Use synthetic oils suitable for low temperatures, as these maintain fluidity even in cold conditions. Regularly check and replace compressor oil to ensure proper lubrication and reduce internal friction.
Ensure Proper Dew Point Control
The dew point is the temperature at which water vapor condenses. In cold weather, the dew point of compressed air can rise, leading to more moisture in the system. Proper drying is crucial to prevent freezing.
- Solution: Regularly monitor and adjust the drying system to handle the increased moisture load in cold weather. Consider using more efficient desiccants or adjusting dryer settings to maintain a low dew point.
Regular Maintenance
Routine maintenance is essential for ensuring that the compressed air system operates smoothly in cold weather. Proper maintenance helps the equipment be more resilient in harsh environments and reduces the likelihood of malfunctions.
- Solution: Implement a winter maintenance checklist, including checking for leaks, replacing filters, inspecting oil levels and quality, and ensuring proper operation of condensate drainage devices. Regular maintenance will ensure the compressor operates efficiently during the cold season.
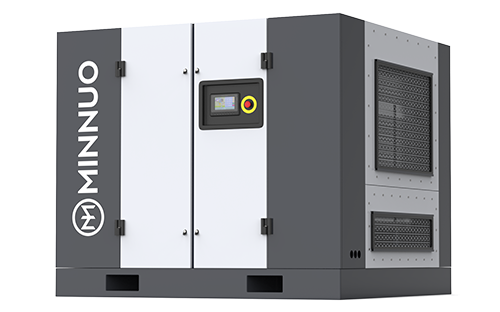
MINNUO Compressors: Ready for the Cold
Of course, customers who choose MINNUO compressors don’t have to worry about these issues. Our range of compressors is designed to withstand extreme environments.
We are equipped with low-temperature startup protection systems, use high-quality insulating materials, and feature intelligent control systems to ensure that pipes and components remain unaffected by cold weather, reducing the risk of freezing. In terms of energy efficiency, customers equipped with MINNUO inverters need not worry, as our compressors still perform excellently in terms of energy saving even in low temperatures. Additionally, we consistently use corrosion-resistant and wear-resistant materials, ensuring that the compressor can operate continuously in cold weather while minimizing failures due to corrosion and wear.
Conclusion
Preparing compressed air systems for winter protection is crucial to ensure stable operation in cold weather, ultimately saving on maintenance and production downtime costs.
If you choose MINNUO compressors, your compressed air system will operate reliably and efficiently in any extreme environment. Feel free to consult with us!