In modern industrial production, air compressors are essential pieces of equipment. They compress air into high-pressure gas to power various industrial devices. Choosing the right air compressor not only boosts production efficiency but also saves significant costs over the long term. Among the different types of air compressors, single-stage and two-stage compressors each have their own pros and cons. Understanding their working principles and suitable applications can help you make the best choice. This article will delve into the differences between single-stage and two-stage compressors and provide selection advice to help you choose the most suitable compressor for your production system.
The key difference between single-stage and two-stage compressors lies in the pressure of the compressed air. A single-stage compressor compresses air to 7-13 bar in one stage, with a simple structure and lower initial investment. However, it consumes more energy under high pressure, generates high temperatures, and struggles to effectively remove moisture and oil from the air. Two-stage compression occurs in two stages, with an intermediate cooling process that further compresses the air to 15-40 bar, effectively controlling temperature, improving energy efficiency, and providing higher purity compressed air. Single-stage compression is suitable for small industrial applications with low-pressure and low-cost demands, while two-stage compression is ideal for high-pressure, large-flow, and air quality-sensitive scenarios, such as petrochemicals, metalworking, and food processing.
Now, let’s explore the working principles of both types of compressors and analyze their unique characteristics.
Single-Stage Compression vs. Two-Stage Compression: Working Principles
Single-Stage Compression
Single-stage compression refers to compressing air in a single compression chamber within the compressor. The air is compressed to the target pressure in a single compression process. The working principle is as follows:
- Intake Stage: Air enters the compression chamber through the intake valve. As the piston or screw rotates, the volume of the compression chamber increases, drawing in external air.
- Compression Stage: As the piston or screw moves, the volume of the compression chamber decreases, compressing the air and increasing pressure. During this process, the temperature of the air rises rapidly.
- Exhaust Stage: Once the air reaches the desired pressure, the outlet valve of the compression chamber opens, and the compressed high-pressure air is discharged into a storage tank or directly to the equipment requiring air.
Since single-stage compression occurs in one chamber, the higher the compression ratio, the higher the air temperature, resulting in increased energy loss and reduced compression efficiency.
Two-Stage Compression
Two-stage compression refers to compressing air in two separate compression chambers, with an intermediate cooling process between the two stages to lower the temperature of the air and improve compression efficiency. The working principle is as follows:
First Stage Compression (Low-Pressure Stage)
- Intake Stage: Air enters the first compression chamber (low-pressure chamber) through the intake valve.
- Low-Pressure Compression Stage: Air is compressed to a medium pressure in the first compression chamber. During this stage, the volume of air decreases, pressure increases, and the temperature rises.
- Intermediate Cooling Stage: The air, now at medium pressure, passes through a cooler (usually water-cooled or air-cooled) to reduce its temperature, which helps minimize energy loss in the next compression stage.
Second Stage Compression (High-Pressure Stage)
- High-Pressure Compression Stage: The cooled medium-pressure air enters the second compression chamber (high-pressure chamber) for further compression to the target high pressure. By lowering the air temperature, the power required for the second compression stage is reduced, improving overall system compression efficiency.
- Exhaust Stage: Once the air reaches the desired final pressure, it is discharged through the outlet valve into a storage tank or to the equipment requiring air.
The key feature of two-stage compression is that it compresses air in two stages, with cooling between stages to reduce temperature rise, enhance compression efficiency, and reduce energy consumption.
Key Differences in Working Principles
Compression Process Frequency
- Single-Stage Compression: The entire compression process occurs in one chamber, compressing air to the target pressure in a single step.
- Two-Stage Compression: The compression process is split into two stages, with air compressed step-by-step in two chambers, with cooling in between.
Cooling Process
- Single-Stage Compression: There is no intermediate cooling, and the air temperature rises significantly as the compression ratio increases.
- Two-Stage Compression: An intermediate cooler is used to lower the air temperature between stages, reducing energy consumption and improving efficiency.
Efficiency and Temperature Control
- Single-Stage Compression: With difficulty in temperature control, efficiency is lower in high-pressure applications, and the compressor tends to overheat, affecting stability.
- Two-Stage Compression: By using staged compression and intermediate cooling, temperature rise is controlled, reducing energy loss, and providing a significant advantage in high-pressure applications.
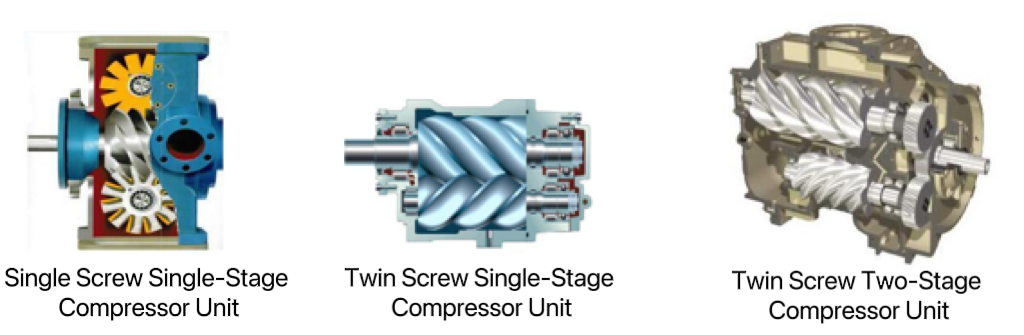
Key Differences Between Single-Stage and Two-Stage Compression
Having understood the working principles of single-stage and two-stage compression, let’s now delve into their differences across several key aspects:
Compression Pressure: Meeting Diverse Industrial Needs
- Single-Stage Compression: Single-stage compressors are typically used for low to medium pressure applications, with the compressed air pressure generally ranging from 7-13 bar. This pressure is sufficient for pneumatic tools, small machinery, or everyday workshop applications.
- Two-Stage Compression: Two-stage compressors can provide higher compression pressures, usually between 15-40 bar, which are required for high-pressure gas-powered equipment. In industries like petrochemicals, chemicals, and large-scale production lines, two-stage compression is the more suitable choice.
Temperature Control: Improving Equipment Efficiency
- Single-Stage Compression: Due to its direct compression process, air is compressed to high pressure in a single step, generating a considerable amount of heat. Without a cooling stage, the temperature of the gas rises rapidly. This high temperature not only increases energy consumption but may also cause moisture and oil in the air to evaporate, affecting air quality and accelerating wear on equipment, thereby reducing the lifespan of components.
- Two-Stage Compression: Two-stage compressors feature an intermediate cooling stage between the two compression stages, effectively lowering the temperature of the air before the second compression. This cooling process helps control the gas temperature, reducing equipment wear, enhancing overall compression efficiency, improving reliability, and avoiding air quality issues associated with high temperatures. Proper temperature control in two-stage compression equipment ensures more stable long-term operation, making it especially suitable for applications requiring continuous high-pressure air supply.
Air Quality: Ensuring Purity of Compressed Air
- Single-Stage Compression: Due to the higher temperatures, single-stage compression often results in air containing more water vapor. The compressed air must undergo additional cooling and drying treatments to reduce humidity. Additionally, because the equipment has a simpler structure, the oil content in the air tends to be higher, requiring extra oil separation and filtration. For industries with high air quality demands, the compressed air from a single-stage compressor may not meet the necessary standards.
- Two-Stage Compression: Two-stage compressors are better equipped to remove moisture and oil from the air. Because the temperature is better controlled, moisture is more effectively removed, resulting in higher-quality compressed air. This makes two-stage compressors ideal for applications requiring high-quality air, particularly when supplying air to sensitive equipment or systems. The air treatment system in two-stage compressors is generally more sophisticated, yielding compressed air with lower humidity and oil content, meeting the requirements of more stringent industrial applications.
4. Energy Efficiency and Operating Costs: Reducing Power Consumption and Saving Costs
Power Consumption Formula

- P: Power consumption (kW)
- Q: Volume flow (m³/s)
- p2/p1: Compression ratio
- k: Specific heat ratio of air (typically k=1.4)
- η: Isentropic efficiency (0.7-0.9)
- T1: Initial temperature (K)
Operating Cost Formula
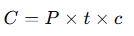
- C: Operating cost (currency)
- t: Operating time (hours)
- c: Electricity rate (currency/kWh)
Assumptions
- Volume flow Q = 1.5 m³/s
- Initial pressure p1 = 1 bar (atmospheric pressure)
- Single-stage compressor output pressure p2 = 8 bar
- Two-stage compressor output pressure p2 = 16 bar (compressed in two stages, each stage compressing to about 4 bar)
- Specific heat ratio k = 1.4
- Initial temperature T1 = 298 K (25°C)
- Isentropic efficiency η = 0.75
- Electricity rate c = 0.12 USD/kWh
- Operating time t = 8 hours/day
Results
- Single-Stage Compression Power Consumption:

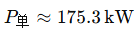
- Two-Stage Compression Power Consumption:

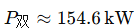
- Single-Stage Compression Operating Cost:

- Two-Stage Compression Operating Cost:

From the calculations, it’s clear that although single-stage compressors require a lower initial investment, their higher temperatures during compression result in greater energy consumption, leading to higher operational costs, especially in high-pressure applications. On the other hand, two-stage compressors optimize temperature control during the compression process, significantly reducing energy loss. Although the initial investment for a two-stage compressor is higher, over the long term, it reduces energy consumption and operational costs, making it more cost-effective, particularly for large-scale industrial applications.
How to Choose the Right Air Compressor for You
Choosing the right air compressor requires consideration not only of the initial investment but also of long-term energy efficiency, operating costs, and production requirements. Here are some suggestions to help you select the most appropriate air compressor:
Low-Pressure Requirements
If your production process demands low-pressure compressed air and air quality requirements are not too stringent, a single-stage air compressor is a cost-effective and easy-to-use choice.
High-Pressure Requirements
For industrial applications requiring high-pressure air, such as petrochemicals, large-scale manufacturing, or mining, a two-stage air compressor can provide higher pressure along with better energy efficiency and air quality.
Long-Term Operation and Energy Saving
If your production system needs to operate at high loads for long periods, a two-stage air compressor will be more energy-efficient and require less frequent maintenance.
High Air Quality Requirements
For industries such as electronics manufacturing, food processing, and pharmaceuticals, which have strict air quality standards, two-stage compressors can supply cleaner and purer compressed air, ensuring stable production and product quality.
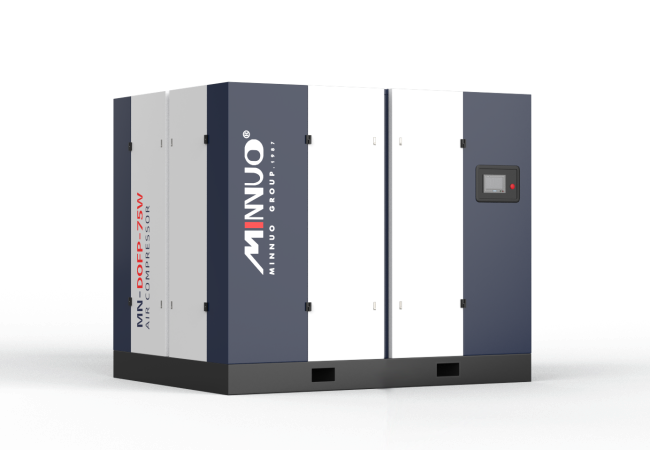
Conclusion
Whether it’s a single-stage or two-stage air compressor, selecting the right model is crucial for ensuring production efficiency, reducing operational costs, and improving equipment stability. As a professional air compressor manufacturer, MINNUO offers customized compressed air solutions to help you choose the most suitable compressor for your business needs.
If you have any questions or need assistance, feel free to contact us. MINNUO is ready to provide expert consulting services and the best equipment recommendations tailored to your needs.