As a core power equipment in industrial production, the operational stability of air compressors directly affects production efficiency and equipment lifespan. Overheating is one of the most common faults in air compressors, and if not addressed in time, it may lead to equipment shutdowns, component damage, or even safety accidents. This article will analyze the causes and solutions for high compressor temperatures from multiple dimensions, helping enterprises achieve full lifecycle management of their equipment.
The main causes of high compressor temperatures include environmental factors, failure of the cooling system, lubrication system faults, mechanical system abnormalities, and improper load management. Specific causes include poor external ventilation, blocked heat exchangers, lubricant failure, obstructed oil circulation, failure of power transmission components, and overload operations. Solutions include optimizing spatial layout, regularly cleaning the heat exchanger, selecting the appropriate lubricant, strengthening oil line management, regularly inspecting belts and couplings, intelligently controlling load, and accurately diagnosing temperature monitoring errors.
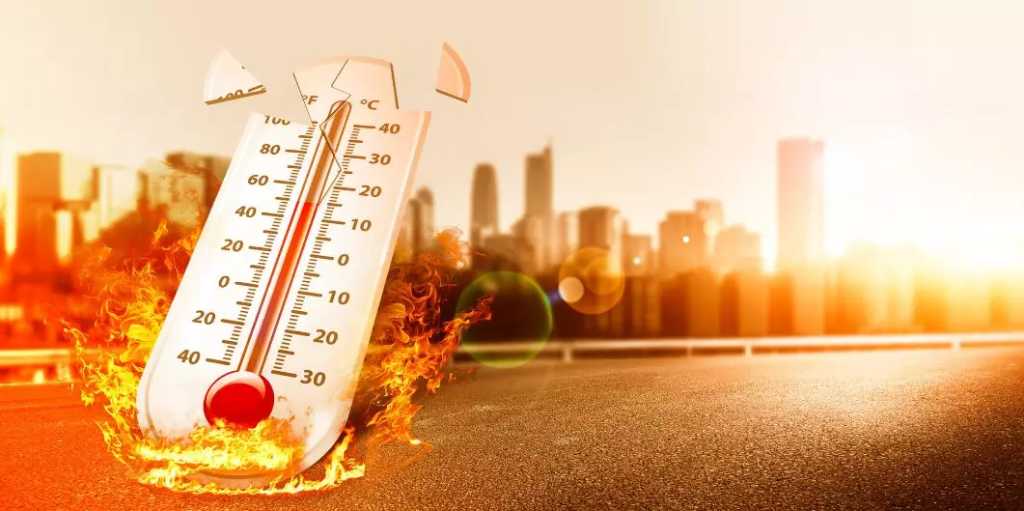
1. Environmental Factors and Cooling System Failures
1.1 Poor External Ventilation
Air compressors require a continuous heat dissipation system during operation. If the equipment is installed near walls, heat sources, or in confined spaces, or if the front/side doors are open during operation, causing airflow turbulence, it can hinder the cooling efficiency. Studies show that for every 5°C increase in environmental temperature, the compressor operating temperature will increase by 8 – 10%.
Solution:
- Space Layout Optimization: Ensure the equipment is at least 1.2 meters away from obstacles to avoid interference from heat sources. Install deflector shields if necessary to enhance directional cooling.
- Environmental Temperature Control: Install industrial fans or water curtain systems in high – temperature workshops to maintain an ambient temperature ≤38°C.
1.2 Deterioration of Heat Exchanger Performance
Blockage of the heat exchanger is a typical issue leading to overheating. Oil and dust form an insulating layer on the fins, and copper pipes inside may experience scaling or oil carbonization, reducing the flow channel area by more than 50%, which drastically lowers heat exchange efficiency.
Deep Cleaning Process:
- Physical Cleaning: Use a high – pressure air gun (0.6 – 0.8MPa) to blow out 80% of surface dirt from the inside of the heat exchanger.
- Chemical Cleaning: Use a neutral cleaning agent (pH 6.5 – 7.5) to flush stubborn oil sludge for 30 minutes to avoid acid – base corrosion.
- Periodic Maintenance: Clean every 200 hours in dusty environments and every 500 hours in regular environments, checking the heat exchanger pressure difference (standard value ≤15kPa).
2. Lubrication System Failures and Chain Reactions
2.1 Three Major Causes of Lubricant Failure
Incorrect Oil Selection
Poor – quality lubricants with inadequate viscosity index (VI) reduce oil film strength at high temperatures, causing direct contact between friction surfaces. Experimental data shows that using non – standard oils can increase bearing temperature by 20 – 25°C.
Oil Selection Criteria:
- Synthetic oil ISO VG32/46 grade (preferably VG46 when the ambient temperature is >30°C)
- Flash point ≥220°C, pour point ≤ – 15°C
Obstructed Oil Circulation
Oil filter clogging (pressure difference >0.18MPa) or a stuck oil cut – off valve can interrupt oil supply, causing “dry friction.” In typical cases, failure of the oil cut – off valve spring can raise the main unit temperature to 120°C within 90 seconds, triggering a shutdown.
Emergency Handling Steps:
- Disassemble and inspect the oil cut – off valve stem, using 800 mesh sandpaper to polish it to Ra ≤0.4μm.
- Measure the spring’s elastic modulus. If deformation exceeds 5%, replace the spring.
- After reassembly, manually test the valve’s opening and closing stroke (standard value: 8 – 10mm).
Improper Oil Level Management
If the oil level is below the lower limit of the sight glass, the circulating oil volume decreases by over 40%, preventing effective cooling. Note: During shutdown, the oil level may appear falsely high; ensure the oil level covers two – thirds of the sight glass during load operation.
2.2 Faults in Oil Line Auxiliary Components
- Thermal Control Valve Failure: A bypass valve that remains open causes hot oil not to pass through the heat exchanger, resulting in abnormal temperature gradients (replace the valve core if the oil temperature difference is <10°C).
- Oil – Gas Separator Blockage: When the pressure difference exceeds 0.1MPa, oil circulation resistance increases by three times. Replace the filter and check the sensitivity of the pressure difference switch.
3. Mechanical System Abnormalities and Load Management
3.1 Failure of Power Transmission Components
- Belt Drive System: A loose V – belt (deflection >15mm) or broken belt can reduce fan speed by 30 – 50%. It is recommended to check belt tension monthly (standard value: 10kg pressure under deflection of 10±2mm).
- Coupling Misalignment: Axial deviation >0.05mm or angular deviation >0.1° can cause additional friction heat, requiring laser alignment calibration.
3.2 Overload Operation Risks
If the exhaust pressure exceeds the rated value by 10%, specific power (kW/m³/min) increases by 18%, significantly raising thermal energy conversion rates. In a typical case, a 0.8MPa model operating at 0.88MPa for an extended period saw a temperature rise of 12 – 15°C.
Load Control Measures:
- Install an intelligent pressure controller to set pressure bands (e.g., ±0.05MPa) for precise adjustments.
- Use a master – backup rotation strategy for parallel units, controlling single – machine load rates between 70 – 85%.
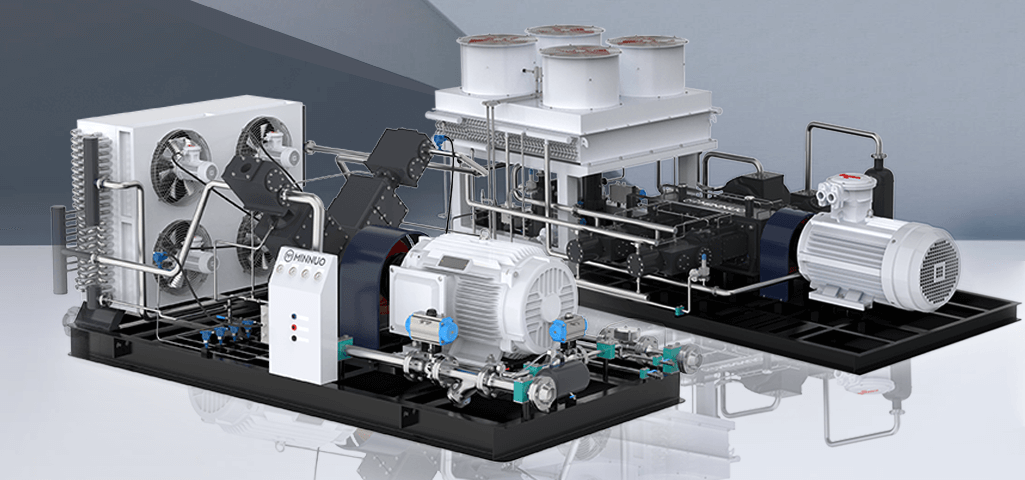
4. Precise Diagnosis through Control Systems and Sensors
4.1 Temperature Monitoring Error Analysis
- PT100 Sensor Drift: If the annual drift exceeds 1°C, recalibration is required, using a mixture of ice water (0°C) and boiling water (100°C) for two – point calibration.
- PLC Module Faults: Abnormal input impedance (normal value: 1 – 10kΩ) can lead to incorrect temperature readings. An oscilloscope should be used to check the signal waveform.
4.2 Building an Intelligent Early Warning System
Integrating IoT sensors for real – time monitoring:
- Vibration spectrum analysis (detects early bearing wear)
- Infrared thermography (identifies localized hotspots)
- Oil particle counting (predicts filter lifespan)
Achieve threshold alerts and fault root cause analysis through a cloud platform.
5. Systematic Maintenance Strategy and MINNUO Solutions
5.1 Preventive Maintenance Schedule
Component Name | Maintenance Content | Cycle (Hours) | Inspection Standard |
Air Filter | Cleaning / Replacement | 500 | Pressure difference >5kPa |
Oil Filter | Filter Replacement | 2000 | Pressure difference >0.18MPa |
Lubricant | Full Replacement | 4000 | Acid value >1.5mgKOH/g |
Heat Exchanger | Deep Cleaning | 1000 | Air inlet – outlet temperature difference <15°C |
5.2 MINNUO Professional Technical Support
- Genuine Spare Parts Guarantee: Provide DN50 grade precision filters, high – temperature resistant seals, and other custom components to extend lifespan by over 30%.
- On – site Diagnostic Services: Equipped with vibration analyzers, oil quality rapid testing instruments, etc., to locate fault sources within 2 hours.
- Energy Efficiency Optimization Plan: Based on thermodynamic simulation models, redesign cooling airflow and oil line layouts to reduce temperature by 5 – 8°C.
6. Conclusion
High – temperature failures in air compressors are the result of interactions among mechanical, fluid, and control systems. A full “monitoring – analysis – intervention” process management system should be established. MINNUO recommends enterprises replace traditional fault repair with predictive maintenance to reduce unplanned downtime through data – driven decision – making. For customized maintenance plans or technical training, please contact our 24 – hour engineering team.