In modern industrial production, compressed air is widely used across various equipment and processes. However, many overlook the microbial contamination that may exist within compressed air. These invisible pollutants can seriously affect equipment, product quality, and employee health. This article provides an in-depth analysis of the risks posed by microbial contamination in compressed air, as well as detection methods and preventive measures to ensure system stability and air quality.
Microbial contamination in compressed air and its potential risks to equipment, product quality, and employee health require effective management. Measures such as controlling humidity, installing high-efficiency filters, regular cleaning, and using disinfection technologies can help reduce the risks of microbial contamination. Through proper detection and system maintenance, businesses can safeguard air quality and production safety, ultimately improving equipment efficiency, extending its lifespan, ensuring employee health, and maintaining product quality.
What is Microbial Contamination in Compressed Air?
Common microbial contaminants in compressed air include bacteria, mold, yeast, and fungi. Since compressed air systems are often exposed to warm and humid environments, they provide an ideal breeding ground for microorganisms. These microbes can easily spread through the compressed air flow, contaminating equipment and the surrounding environment.
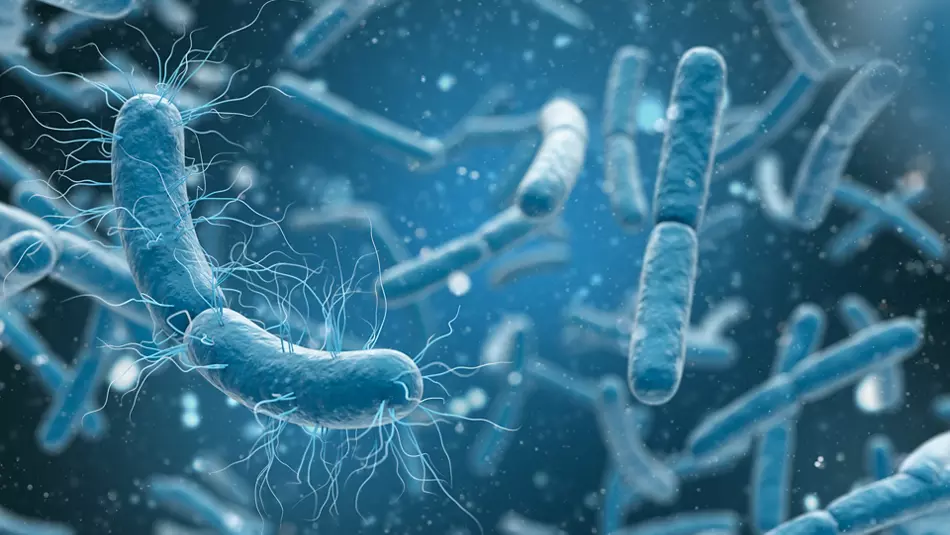
Major Risks of Microbial Contamination
Health Risks: Threats to Employees and Consumers
Microbial contamination poses a serious threat in industries such as food, healthcare, and pharmaceuticals. Bacteria (such as Legionella) and mold in compressed air can spread via airborne particles, contaminating products or causing respiratory illnesses. Legionella infection can lead to pneumonia, while mold exposure can trigger allergic reactions, adversely affecting employee health.
Equipment Damage: Accelerating Corrosion and Malfunctions
Microbes can also cause significant damage to equipment. Bacteria such as sulfate-reducing bacteria can generate corrosive substances, accelerating the corrosion of components and shortening the lifespan of equipment. Moreover, mold and fungal growth can block pipes and filters, reducing the efficiency of the system and potentially causing equipment failures.
Product Contamination: Reducing Quality and Safety
Microbial contamination directly impacts product quality, especially in industries with stringent air quality requirements. For example, in the pharmaceutical and food industries, uncontrolled microbial contamination can lead to product contamination, damaging the brand’s reputation and endangering consumer health.
How to Detect Microbial Contamination in Compressed Air?
Effective detection methods are key to preventing and controlling microbial contamination. Here are some commonly used techniques:
Microbial Culture Method
This method involves cultivating an air sample on a culture medium to determine the type and quantity of microorganisms. While this method is accurate and reliable, it typically takes several days to yield results.
ATP Bioluminescence Method
The ATP test detects the presence of ATP molecules inside microbial cells, indirectly determining the microbial concentration in the air sample. This method is quick and efficient, making it suitable for regular monitoring and onsite testing.
UV Detection Method
This method uses ultraviolet light to illuminate air samples, causing microorganisms to emit a fluorescent signal. It is particularly effective for low microbial concentrations, helping to pinpoint contamination sources quickly.
Particle Counting Method
By detecting the number of particles in the air, this method indirectly reflects microbial contamination levels. Microbes are often particles themselves, and particle counting can effectively monitor air quality changes.
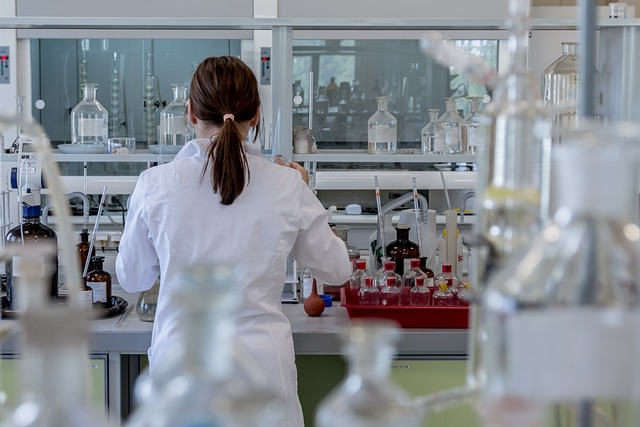
How to Prevent and Control Microbial Contamination in Compressed Air?
Control Humidity: Inhibit Microbial Growth
Moisture is a catalyst for microbial growth. If the humidity in compressed air is not effectively controlled, it becomes a breeding ground for microorganisms. Installing efficient dryers to maintain humidity within the recommended range is the first step to preventing microbial contamination.
Install Microbial Filters: Efficiently Remove Contaminants
For high-demand industries, installing microbial filters is an effective solution. High-efficiency filters can remove bacteria, mold, and other microorganisms from the air, ensuring the purity of compressed air. Choosing the appropriate filters can improve air quality and prevent the spread of contamination.
Regular Cleaning and Maintenance: Keep Equipment Clean
Regular cleaning of the compressed air system, especially storage tanks, pipes, and filters, helps prevent moisture buildup, reducing microbial growth. Keeping the system dry is essential in controlling microbial proliferation.
Disinfection Technologies: UV and Ozone Treatment
UV and ozone technologies have powerful sterilization capabilities. UV light destroys the DNA structure of bacteria and mold, eliminating microorganisms, while ozone kills airborne pathogens through oxidation. Using both methods in combination provides additional protection in environments requiring high cleanliness.
Regular Monitoring and Assessment: Ensure Air Quality
Regular monitoring of microbial levels in compressed air helps identify contamination sources early and take corrective measures. Methods such as ATP testing and microbial culturing can ensure that air quality consistently meets required standards.
How to Choose the Right Compressed Air System and Filtration Equipment?
Choosing the right compressed air system and filtration equipment is essential. Here are key factors to consider:
- System Design: The system should be designed to effectively control moisture and reduce the risk of microbial growth.
- Filter Type: Select the appropriate type of filter based on specific needs, such as high-efficiency microbial filters, particle filters, etc.
- Drying Equipment: High-efficiency dryers effectively remove moisture, minimizing the impact of humidity on microbial growth.
- Regular Maintenance: The system should allow for regular maintenance and inspections to ensure long-term stable operation.
Conclusion
With continuous advancements in technology, more effective detection and prevention methods are available to support the management of compressed air systems. Regular monitoring and scientific maintenance will help reduce the risk of microbial contamination, ensuring businesses operate in an efficient and safe environment.
If you want to know more, please follow MINNUO.