In the field of industrial production, air compressors, as a kind of crucial power equipment, play a vital role in ensuring the continuity and efficiency of the entire production process. And the lubricating oil for air compressors is the “blood” that guarantees the normal operation of air compressors. Selecting the right lubricating oil for air compressors is an important part of equipment maintenance and management. This article will deeply explore various technical points and considerations for selecting lubricating oil for air compressors, providing you with comprehensive and in-depth guidance.
The selection of air compressor lubricating oil depends on the compressor type. Piston compressors need oil with strong lubricity and anti-wear, screw compressors require oil with good antioxidant, anti-emulsification and heat dissipation, and centrifugal compressors need high-cleanliness and stable oil. Also consider the operating environment. For high-temperature, choose oil with good high-temperature stability; for low-temperature, focus on low-temperature fluidity; in high-humidity, select oil with strong anti-emulsification; in dusty environments, need oil with good detergency and dispersancy. Pay attention to core performance indicators like viscosity-temperature, flash point and carbon deposition tendency. The base oil should have good quality, narrow fraction and appropriate viscosity. Consider the oil quality certification system and conduct on-site tests to verify the selection.
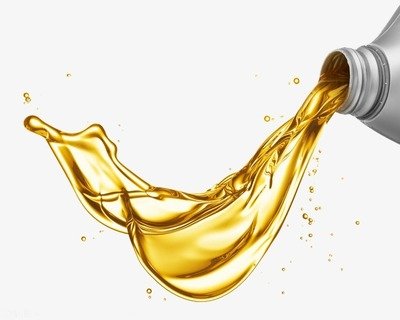
Precise Adaptation Based on the Type of Air Compressor
Different types of air compressors have completely different performance requirements for lubricating oil due to differences in their working principles and structural characteristics.
Piston Air Compressors
Piston air compressors achieve gas compression through the reciprocating motion of pistons in cylinders. This motion mode leads to relatively large friction resistance and mechanical load between the pistons and cylinder walls. Therefore, the selected lubricating oil must have excellent lubricity and anti-wear properties to effectively reduce the friction and wear of components and extend the service life of the equipment. In terms of the type of lubricating oil, mineral oil or semi-synthetic oil is commonly used, with typical viscosity grades such as ISO VG100, VG150, etc. The lubricating oil of these viscosity grades can form a sufficiently thick and stable oil film between the pistons and cylinder walls, ensuring a good lubrication effect under high-load working conditions.
Screw Air Compressors
The core of the operation of screw air compressors is a pair of meshing helical rotors. They operate at a relatively high speed and generate a lot of heat during the compression process. This requires the lubricating oil to have excellent antioxidant properties to resist the oxidation and deterioration of the oil in a high-temperature environment and prevent the formation of sludge and paint films. It should also have good anti-emulsification properties to ensure that the lubricating oil will not emulsify when it may come into contact with water, thus always maintaining stable lubrication performance. And it needs to have excellent heat dissipation properties to timely take away the heat generated during the operation of the equipment and maintain the normal working temperature of the equipment. Synthetic oils, such as polyalphaolefin (PAO) or ester oils, have become the first choice for lubricating oil of screw air compressors due to their excellent comprehensive performance. Their commonly used viscosity grades are mostly ISO VG32, VG46, etc., which can meet the lubrication needs while taking into account heat dissipation and fluidity performance.
Centrifugal Air Compressors
Centrifugal air compressors compress gas by relying on high-speed rotating impellers. Their working speeds are extremely high, putting extremely strict requirements on the cleanliness and stability of the lubricating oil. Any tiny impurities or fluctuations in the performance of the oil may cause serious damage to the high-speed rotating impellers and related precision components. Therefore, high-quality synthetic oils, such as perfluoropolyether (PFPE), are usually selected. Such synthetic oils have excellent chemical stability, extremely low volatility and excellent lubrication performance, ensuring the reliable operation of the equipment under extreme working conditions. Their viscosity grades are relatively low, generally ISO VG22, VG32, etc., to meet the low-resistance lubrication needs of high-speed rotating components, reduce energy consumption and the increase in oil temperature.
Comprehensive Consideration in Combination with the Operating Environment
The operating environment of air compressors is another key factor affecting the selection of lubricating oil. Environmental conditions such as temperature, humidity and dust content all need to be included in the comprehensive evaluation system for the selection of lubricating oil.
Temperature Factor
Countermeasures for High-Temperature Environments
When air compressors operate for a long time in high-temperature environments, the lubricating oil faces severe challenges in thermal stability. High temperatures can easily accelerate the oxidation process of the oil, resulting in a decrease in viscosity and an increase in acid value, which will then affect the lubrication performance and shorten the service life. Therefore, it is necessary to choose lubricating oil with excellent high-temperature stability and antioxidant properties. Synthetic oils perform outstandingly in this regard. Their special chemical structures enable them to maintain relatively stable molecular structures under high-temperature conditions, effectively resisting the occurrence of oxidation reactions and ensuring continuous and reliable lubrication protection for the equipment under high-temperature working conditions.
Starting Requirements in Low-Temperature Environments
When starting air compressors in low-temperature environments, the low-temperature fluidity of the lubricating oil becomes the primary consideration factor. If the pour point of the lubricating oil is too high or its low-temperature fluidity is poor, it may not be able to reach the parts that need lubrication in time at the moment of starting, resulting in dry friction of components, increasing the risk of equipment wear and even damage. In this case, low-viscosity synthetic oils or mineral oils with low-temperature flow improvers added can be selected. These oils can maintain a relatively low viscosity under low-temperature conditions, ensuring that they can quickly circulate throughout the lubrication system when starting and form an effective oil film protection.
Humidity Factor
In a working environment with high humidity, air compressors are extremely vulnerable to the intrusion of water, which is a huge test for the anti-emulsification performance of the lubricating oil. Once the lubricating oil emulsifies with water, its lubrication performance will drop significantly, unable to form a stable oil film on the surface of components, and the heat dissipation effect will also be significantly reduced. More seriously, the emulsified lubricating oil will accelerate the rusting and corrosion process of components, causing irreversible damage to the equipment. Therefore, for air compressors operating in high-humidity environments, lubricating oil with strong anti-emulsification properties should be preferentially selected, such as synthetic oils or high-quality mineral oils with special formula designs and added with efficient anti-emulsification additives. Such lubricating oil can quickly separate water after contact with water, maintain its own lubrication performance and stability, and ensure the reliable operation of air compressors in humid environments.
Dust Factor
If air compressors work in harsh environments with a lot of dust, dust particles in the air will inevitably enter the lubrication system. At this time, the lubricating oil needs to have good detergency and dispersancy, which can effectively disperse and suspend the dust particles mixed in the oil, preventing them from aggregating and depositing on the surfaces of components or in the pipelines, filters and other parts of the lubrication system. Otherwise, the accumulation of dust will lead to increased wear of components and blockage of the lubrication system, seriously affecting the normal operation of air compressors. Lubricating oil with good detergency and dispersancy can continuously carry dust particles during the operation of the equipment and filter them out through filters, thus maintaining the cleanliness of the lubrication system and the stable operation of the equipment. This performance is particularly important in the application of some industries with relatively serious dust pollution, such as mining and building materials processing.

Focus on the Core Performance Indicators of the Oil
Viscosity-Temperature Performance
The oil-injected, internally cooled rotary air compressors will repeatedly experience heating and cooling cycles during operation. Therefore, the viscosity of the lubricating oil should not fluctuate too much due to temperature changes and must have good viscosity-temperature performance. The viscosity indexes of our refined compressor oils are all above 90, which can maintain relatively stable viscosities under different temperature conditions, ensuring reliable lubrication effects for air compressors under various working conditions, effectively reducing lubrication problems caused by viscosity changes and improving the stability and reliability of equipment operation.
Flash Point Requirements
The flash point is a temperature index that measures the temperature at which the vapor pressure formed by heating the oil under atmospheric pressure reaches the lower limit concentration that can be ignited by an open flame. It should be noted that the higher the flash point is not necessarily the better. If the flash point is too high, the oil fraction will be heavier, the viscosity will increase accordingly, and the content of asphaltenes and other substances will also increase, which is prone to carbon deposition during use. And blindly pursuing air compressor oil with a high flash point may instead bring potential safety hazards. Therefore, we emphasize that the flash point of air compressor oil should be appropriate. Generally speaking, the flash point of our produced air compressor oil is controlled above 200 °C. This can not only meet the requirements for safe use but also avoid problems such as carbon deposition caused by too high a flash point, ensuring the safe and stable operation of air compressors.
Carbon Deposition Tendency
The anti-carbon deposition tendency of air compressor oil is crucial for the reliable operation of compressor oils.During actual industrial operations, accidents related to fire and explosion of large and medium-sized air compressors due to carbon deposition issues occur frequently. Among lubricating oils, the combinations of asphaltenes, resins and polycyclic aromatic hydrocarbons are the principal substances with a high tendency to generate residual carbon. When handling lubricating oil materials, a profound refining process is employed, which is capable of efficiently eliminating a significant portion of these substances. Generally speaking, lubricating oils with low viscosity and after deep refining have lower residual carbon values and are not prone to carbon deposition during use. Therefore, our high-quality air compressor oils all choose narrow-fraction base oils that are deeply refined and free of residues (bright stocks), and try to choose ashless additives as much as possible, thus significantly reducing the carbon deposition tendency, improving the safety and reliability of air compressor operation, and reducing equipment failures and maintenance costs caused by carbon deposition.
Quality of Base Oil
The base oil of air compressor oil accounts for more than 95% in the finished oil. It can be seen that the quality of the base oil directly determines the quality level of the finished compressor oil. And the quality of the base oil is closely related to its refining depth. Base oils with deep refining depths have less content of heavy aromatics and resins, low residual carbon, and good responsiveness to antioxidants. Such base oils are of high quality, have a small carbon deposition tendency in the compressor system, good oil-water separation performance and a relatively long service life. The synthetic oil-based base oils we use are organic liquid base oils obtained by chemical synthesis methods, and then carefully blended and added with a variety of high-quality additives to make lubricating oils. Most of the base oils are polymers or high-molecular organic compounds. Among the many types of synthetic oils, the five main types of synthetic oils used as air compressor oils are synthetic hydrocarbons (polyalphaolefin), organic esters (diesters), polyalkylene glycols, fluorosilicone oils and phosphate esters. Although the price of synthetic oil-based compressor oils is higher than that of mineral oil-based compressor oils, their comprehensive economic benefits far exceed those of ordinary mineral oils. They have excellent oxidation stability, extremely small carbon deposition tendency, can effectively lubricate in a temperature range beyond that of ordinary mineral oils, significantly extend the service life, and can meet special usage requirements that ordinary mineral oil-based compressor oils cannot withstand, providing strong support for the high-performance operation of air compressors.
Base Oil Fraction
We have conducted in-depth research on the working conditions of air compressor oils and found that improving the composition of base oils is the key to enhancing the quality of air compressor oils. When we inject the compressor oil composed of light and heavy components into the cylinder of the air compressor, the light components will leave the working parts in advance due to their excessive volatility, thus affecting the lubrication effect. While the heavy components, due to their poor volatility, cannot leave the working parts quickly after completing the work tasks. Over time, they are prone to generate carbon deposits under the action of heat and oxygen. Based on this, our lubricating oils all choose component oils with narrow fractions and firmly abandon component oils with mixed multiple fractions. For example, the traditional No. 19 air compressor oil is prepared by using wide-fraction oil containing a large amount of residue components. During the use process, it was found that the amount of carbon deposition in the air compressor was relatively large. Therefore, in order to improve the quality of air compressor oil, we removed the residue components in the No. 19 compressor oil and selected narrow-fraction base oils, thus effectively reducing carbon deposition, improving the lubrication effect and ensuring the stable operation and service life of air compressors.
Appropriate Viscosity
Under dynamic lubrication conditions, the thickness of the oil film will increase with the increase in the viscosity of the oil, but at the same time, the friction force will also increase with the increase in the viscosity of the oil. If the viscosity of the lubricating oil is too low, it will be difficult to form an oil film with sufficient strength, which will accelerate the wear of components and significantly shorten the service life of components. On the contrary, if the viscosity of the lubricating oil is too high, it will increase the internal friction, resulting in an increase in the specific power of the air compressor, thereby increasing power consumption and fuel consumption, and also forming deposits in parts such as piston ring grooves, valves and exhaust passages. Therefore, choosing the appropriate viscosity is the primary issue in correctly selecting air compressor oil. According to the test results of Xi’an Jiaotong University: Under the same test conditions on the same type of air compressor, using oil with a lower viscosity grade can reduce the specific power of the air compressor by about 10% at most compared with using oil with a high viscosity grade, while there is no significant difference in the wear amount of components. Therefore, on the premise of ensuring the lubrication effect, choosing oil with an appropriate viscosity grade is of great significance for realizing the energy-saving operation and reliable work of air compressors. In the design and production process of air compressors, we have fully considered this factor and provided users with accurate recommendations for the viscosity of lubricating oil to help users find the best balance between energy conservation and equipment reliability.
Importance of the Lubricating Oil Quality Certification System
The market for lubricating oil for air compressors is complex, with uneven quality and performance. Considering the quality and certification of the oil is crucial.
Key Points of Quality Evaluation
Well-known brands have strict production processes, procurement and quality control systems, ensuring quality. Check the quality inspection reports, which should include key indicators such as viscosity and acid value and meet the standards. Referring to user feedback can further verify the reliability of the quality.
Analysis of the Certification System
High-quality oils usually pass international certifications. ISO 9001 certification indicates that an enterprise has good quality management, and ISO 14001 reflects environmental awareness and level. Air compressors in specific industries need to meet industry standards such as API and DIN. These standards determine the performance requirements of lubricating oil according to working conditions to ensure the reliable operation of equipment under complex working conditions. Comprehensively considering the certification system can screen out excellent oils and stabilize the operation of air compressors.
Necessity of On-Site Test Verification for Selection
Although the lubricating oil can be initially determined through multiple considerations, on-site test verification is still indispensable. It can observe the performance of the oil in the real environment and working conditions, discover problems and optimize the selection.
During the test, we select a small amount of oil and add it to the lubrication system. We start the air compressor according to the procedures and closely monitor the performance indicators of the oil and the operating parameters of the equipment, such as oil temperature, noise, vibration and oil sample analysis. We evaluate whether the oil meets the requirements according to the test data. If there are problems, we stop the test immediately, analyze the deviation, adjust the oil parameters and repeat the test until we select suitable oil. This link can avoid risks and losses caused by improper oil selection and ensure the stable operation and high output of air compressors.
Conclusion
Selecting lubricating oil for air compressors is a complex and rigorous job involving various professional technical knowledge and comprehensive considerations. But don’t worry. As a professional air compressor manufacturer, MINNUO will equip you with the most suitable lubricating oil. Welcome to consult!