We use natural gas compressors to transport and store natural gas and to recover light hydrocarbons. Selecting the best-fit compressor type for your application is critical.The initial and target pressure of the gas determines the different characteristics of natural gas compressors. Different types of natural gas compressors differ in production power and energy consumption.
In the following, we will present the main types of natural gas compressors used in the industry. At the same time, we will explain the advantages and disadvantages of the different compressors.
Why do we compress natural gas?
CNG(Compressed Natural Gas) is often confused with LNG (Liquefied Natural Gas). Both are forms of natural gas storage. The main difference is that CNG is stored at room temperature and high pressure, while LNG is kept at low temperatures and near atmospheric pressure.
In the industry, we usually compress natural gas in these situations.
- In the oil well sector, we use compression technology to collect and purify exhaust gases to reduce energy waste and help dispose of fugitive emissions
- We compress the natural gas to be transported through miles of pipelines to its destination.
- CNG fueling stations use compressors to remove water from the gas and store it.
In the natural gas production industry, we usually use two fundamental types, reciprocating and centrifugal. Screw compressors are not commonly used because of their limited output pressure and low efficiency in high-rate applications.
Each type of compressor has its characteristics, and the right style is chosen for different production stages to reach a better gas delivery power.
Reciprocating Natural Gas Compressor
The active part of a reciprocating compressor is the reciprocating piston, which moves back and forth in the cylinder, continuously drawing in gas and discharging it, thus increasing the pressure of the natural gas.
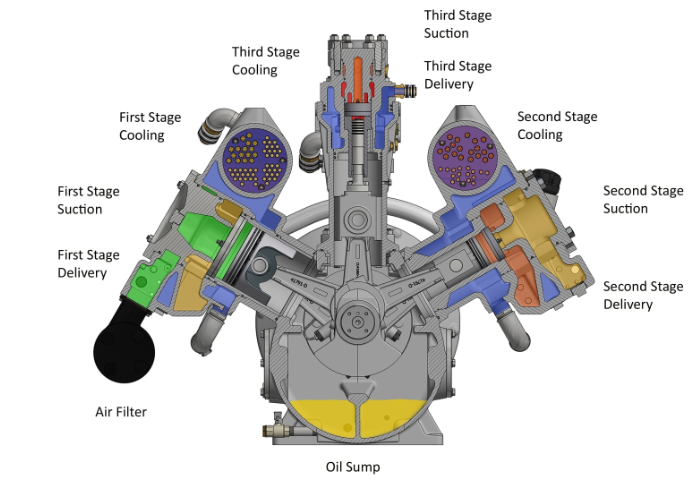
Advantages
- Wide range of applied pressures. Because it works according to the principle of volume change, the working pressure is high. Industrial ultra-high pressure compressors can operate at pressures up to 350 MPa.
- The equipment is cheaper, easy to operate, and has a long service life.
- Since the compression process is closed, the thermal efficiency will be higher.
- Wide range of exhaust volume, less affected by changes in exhaust pressure
Disadvantages
- The inertial force is large, the speed is low, and the machine is relatively bulky.
- The structure is more complex, with more wearable parts and higher maintenance costs.
- The structure is more complex, with more wearable parts and higher maintenance costs.
- Vibration and noise during operation, severe difficulty in equipment installation. And because the piston machine can get only intermittent intake and exhaust, the cylinder volume is small, and the speed can not be too fast. Hence, the piston machine exhaust volume and power output are somewhat limited.
Applications
Reciprocating compressor flow range mainly applies to small and medium displacement and high-pressure occasions. Therefore, the reciprocating compressor development direction is primarily to the large capacity, high pressure, low noise, high efficiency, and high-reliability movement.
Centrifugal Natural Gas Compressors
A centrifugal compressor’s construction and working principle are very similar to that of a centrifugal blower. But its working code is fundamentally different from the piston compressor; it does not use the cylinder volume reduction to improve the gas pressure but relies on the kinetic energy change to improve the gas pressure. The centrifugal compressor has a working wheel with blades; when the wheel rotates, the edges drive the gas movement or make the gas get kinetic energy and then make part of the kinetic energy into pressure energy to increase the pressure of the gas.
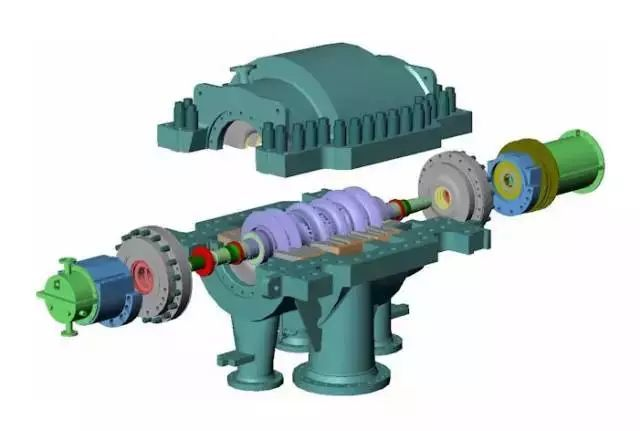
Advantages
- High flow rate and high power contribute to energy saving.
- Compact structure, good sealing effect, small size, so the floor space is much smaller than the piston compressor of the same gas volume.
- Stable and reliable operation, high operation rate, good performance, and relatively low maintenance cost.
- The compression process of centrifugal compressors can be truly oil-free, and there is no need for lubrication inside the machine.
- Few wearing parts, long operation cycle, few moving parts, and low manufacturing accuracy, so the manufacturing cost and reliability are low. It is easy to automate and expand the scale.
Disadvantages
- Difficult to withstand too small air volume and too high a pressure ratio.
- More uneconomical, with high frictional losses of the components in the runners.
- The efficiency is still usually lower than that of piston compressors.
A screw compressor is capable of up to 20 ratios of compression.A reciprocating compressor stage can have 3.5 ratios (typical), but steps can be added to the same reciprocating frame.A single vane is capable of 5 ratios (standard). A 2-stage rotary vane requires an entirely new compressor frame rather than a simple cylinder addition.
- The high speed of the centrifugal compressor has the probability of causing mechanical Vibration, which is more harmful to the machine.
- The operation is more complicated and noisy, and the maintenance cost is higher.
Applications
Some basic chemical raw materials are processed into plastics, fibers, rubber, and other essential chemical products. In addition, centrifugal compressors are also vital equipment for industries such as petroleum refining and refrigeration.
Screw compressors
A screw-type air compressor consists of two rotors with helical gears meshing with each other to compress and expel gas.
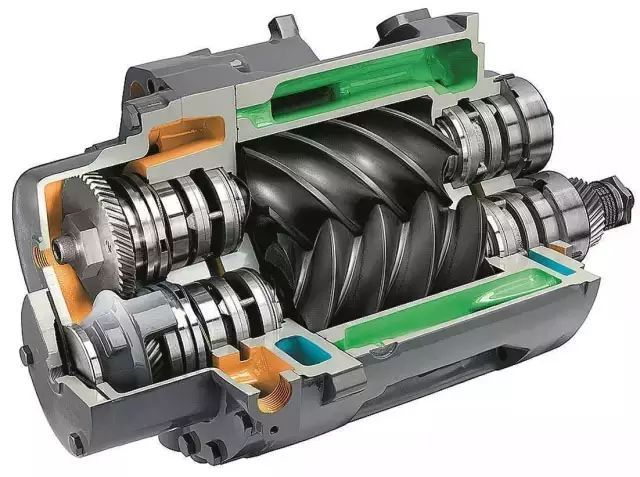
Advantages
- High reliability: fewer parts, fewer wearing parts, long service life.
- Simple and easy to operate and maintain: you can supply air according to the required exhaust volume.
- Good power balance: screw air compressor has no unbalanced inertia force, and the machine runs smoothly at high speed. Especially suitable for use as a mobile compressor, with a smaller size and lighter weight.
- High adaptability: Screw air compressor has the feature of forced air delivery. The exhaust volume is not affected by the exhaust pressure, smooth operation, slight Vibration, and smooth exhaust.
- Multi-phase mixed transmission: The rotor of a screw air compressor has a gap between the rotors, which can withstand the impact of liquid, and can also be pressurized to send out gas containing liquid, the gas containing dust, polymerized gas, etc.
Disadvantages
- Noisy, usually to install noise reduction equipment.
- For strong balance and high-speed operation, the power consumption is higher.
- After a long operation, the screw clearance will become more prominent, and regular maintenance or replacement costs will be high.
Selecting the size of the compressor
Small natural gas compressors are typically used to collect fugitive gas and send it to a burner or flare. Producers often use them to reduce gas emissions.
Medium-sized compressors are usually found where power is provided to pipelines. Producers determine the size and number of compressors by the volume of gas and the pipeline’s diameter.
The largest compressors are usually found only at compressor stations, where they are used to power the pipeline centrally. You will find the largest compressors at compressor stations. These are the “engines” that power the channel. The size and number of compressors are again determined by the amount of gas to be delivered and the pipeline’s diameter.
To conclude
You should find a suitable and economical solution based on the application and the compressor’s process. It would help if you focused on calculating gas usage, reserves, and room for future expansion. Both pressure and flow rate are decisive factors and significantly impact energy consumption. The situation may differ for the same compressor’s pressure ranges and flow rates.