In the process of modern industrial development, compressors are a type of general-purpose mechanical equipment with an important position. Its industry segmentation is diversified and systematic. This article covers the classification of compressors from different types to multiple dimensions based on application industries, technical characteristics and market demand. These subdivisions each have unique attributes and values, and together constitute the complex and orderly overall structure of the compressor industry.
The compressor industry covers multiple fields, such as oil and natural gas (including upstream applications like flare gas, hydrocarbon vapor recovery, and midstream applications like gas turbine fuel gas booster compressors), refining, petrochemicals (such as butadiene, ethylene production), chemicals (e.g., fluorine liquid production, pharmaceutical processes), power generation (e.g., steam recovery, landfill gas), and industrial sectors (such as industrial gas filling, automotive airbag inflation).
Compressor types
Reciprocating compressor
Working principle
The crankshaft drives the connecting rod, and the connecting rod drives the piston to move up and down in the cylinder. When the piston moves downward, the cylinder volume increases, the intake valve opens, the exhaust valve closes, and air is sucked in; when the piston moves upward, the cylinder volume decreases, the exhaust valve opens, and the intake valve closes, completing the compression process.
Structural features
It is mainly composed of cylinders, pistons, connecting rods, crankshafts, valves and other components. There are many moving parts and the structure is relatively complex.
Performance characteristics
- Advantages: high thermal efficiency, low unit power consumption; easy processing, low material requirements, low cost; simple device system; early design and production, mature manufacturing technology; wide applicable pressure range, can be used in ultra-high pressure, high pressure, medium pressure or low pressure occasions.
- Disadvantages: many moving parts, large maintenance workload, high maintenance cost; limited speed; piston rings, cylinders and other parts are easy to wear, resulting in rapid efficiency decline; high noise; relatively backward control system, not suitable for interlocking control and unattended needs.
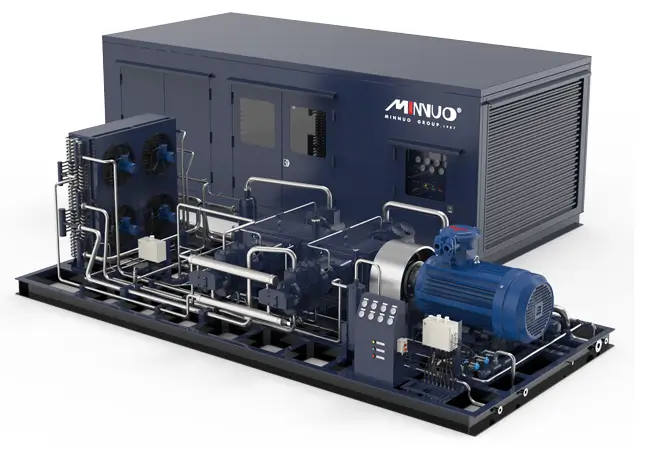
Screw compressor
Working principle
A pair of intermeshing spiral yin and yang rotors are installed in the cylinder. The main rotor is driven by the engine or electric motor, and the other rotor is driven by the oil film formed by the main rotor through oil injection or synchronous gear. The rotor groove is filled with gas when passing the suction port. When the rotor rotates, the rotor groove is closed by the casing wall to form a compression chamber. As the rotor rotates, the volume of the compression chamber decreases, and the oil-gas mixture is compressed to the exhaust port to complete the suction, compression and exhaust process.
Structural features
It is mainly composed of dual rotors, a body, a main bearing, a shaft seal, a balancing piston and an energy regulating device, and has a relatively simple structure.
Performance characteristics
- Advantages: Few parts, no wearing parts, reliable operation, and long life; convenient operation and maintenance, high degree of automation, and unattended operation can be realized; good power balance, no unbalanced inertial force, and can work smoothly at high speed, especially suitable for mobile compressors, small size, light weight, and small footprint; strong adaptability, the volume flow is almost unaffected by the exhaust pressure, and can maintain high efficiency in a wide range, suitable for a variety of working fluids; can transport liquid gas, dust-containing gas, and easily polymerized gas.
- Disadvantages: High cost, the rotor tooth surface is a spatial curved surface, which needs to be processed on expensive special equipment with special tools, and has high requirements for the processing accuracy of the cylinder; it cannot be used in high-pressure occasions, and the general exhaust pressure does not exceed 3MPa; it cannot be used in micro occasions, and the performance is usually superior when the volume flow is greater than 0.2m³/min.
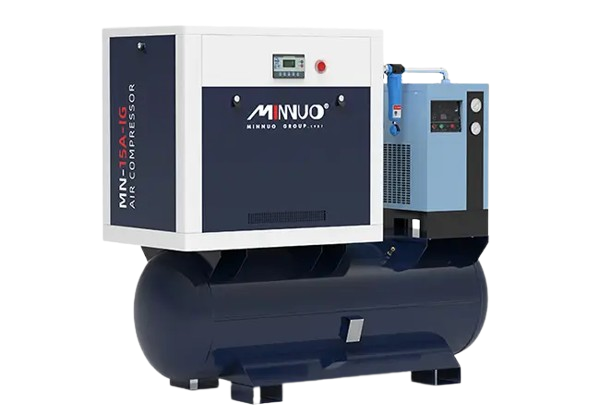
Centrifugal compressor
Working principle
The gas is accelerated by rotating the impeller, and the main airflow flows radially. When the gas flows through the impeller of the centrifugal compressor, the high-speed running impeller causes the gas to increase its pressure and speed under the action of centrifugal force. After that, when the gas flows through the diffuser channel, the flow channel cross-section gradually increases, so that most of the kinetic energy of the gas is converted into static pressure energy, which further plays a role in boosting.
Structural features
It is mainly composed of two parts: the rotor and the stator. The rotor includes the impeller and the shaft. The impeller has blades, a balance disk and a part of the shaft seal; the main body of the stator is the cylinder, and there are also diffusers, bends, return pipes, intake pipes, exhaust pipes and other devices.
Performance characteristics
- Advantages: large gas volume, simple and compact structure, light weight, small unit size, small footprint; balanced operation, reliable operation, high operating rate, few friction parts, less spare parts required, less maintenance costs and personnel; absolutely oil-free compression process for chemical media; suitable for direct dragging of industrial steam turbines or gas turbines, providing the possibility for comprehensive utilization of thermal energy1.
- Disadvantages: not suitable for occasions with too small gas volume and too high pressure ratio; narrow stable operating range, although gas volume adjustment is more convenient, but the economy is poor; efficiency is generally lower than piston compressors; more sensitive to gas properties, poor operational adaptability when load changes; high speed, may produce mechanical vibration, and surge phenomenon may occur in operating characteristics, causing damage to the machine; gearbox noise is large, high technical content, and relatively high maintenance costs.
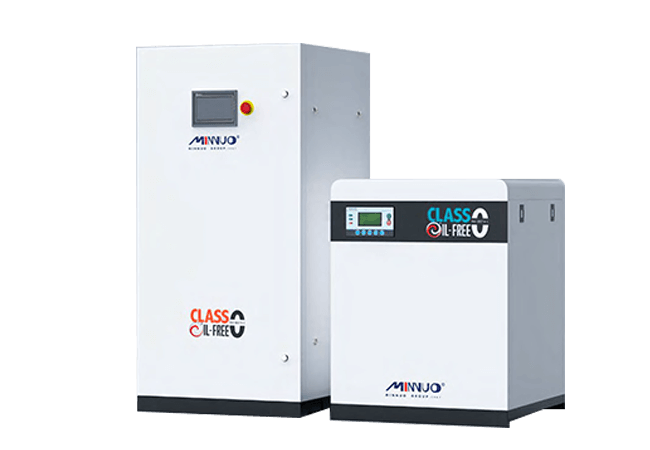
Compressor industry segmentation
The compressor industry covers multiple fields. Here we list the upstream and midstream fields of oil and gas, refining, petrochemicals, chemicals, power generation, and industry, as well as the corresponding applications of reciprocating compressors, screw compressors, and centrifugal compressors.
Trade | Subdivision of applications | piston compressor | screw compressor | centrifugal compressor | ||
AP1618 Piston type | diaphragm type | Screw type | Turbine type (monopole) | multiple-step type | ||
Oil &gas upstream | Torch gas, hydrocarbon vapor recovery, flash gas | √ | √ | |||
Unconventional gas, well gas reinjection | √ | √ | ||||
Onshore and offshore oil and gas, floating production storage and offloading units (FPSO) | √ | √ | √ | |||
Liquefied natural gas (LNG), compact natural gas to synthetic oil, sulfur recovery and gas treatment plant, gas lift, carbon dioxide recovery, enhanced oil recovery (EOR) and carbon dioxide capture | √ | √ | √ | |||
Oil &gas midstream | Gas turbine fuel gas booster, coalbed methane (CBM)/ coalbed natural gas (CSG), natural gas collection and pressurization | √ | √ | √ | √ | |
Liquefied natural gas (LNG), liquefied petroleum gas (LPG), vaporized oil gas (BOG), natural gas to synthetic oil (GTL) | √ | √ | ||||
Natural gas and carbon dioxide gas dehydration, separation, precipitation | √ | √ | ||||
Gas discharge | √ | √ | √ |
Trade | Subdivision of applications | piston compressor | screw compressor | centrifugal compressor | ||
AP1618 Piston type | diaphragm type | Screw type | Turbine type (monopole) | multiple-step type | ||
Refinery | Hydrogen (H2) process feed, hydrogenation treatment (HDT), high density polyurethane (HGU), tail gas | √ | √ | √ | √ | |
Hydrocracking, hydrogenation treatment, isomerization, catalytic reforming, alkylation | √ | √ | ||||
Sulfur recovery and sulfuric acid plant, oil-free hydrogenation desulfurization (HDS) | √ | √ | √ | |||
Torch gas recovery, propane and butane recovery | √ | √ | √ | √ | √ | |
Soda ash, acidic hydrocarbons, vinyl chloride (VCM) belt gas | √ | √ | √ | |||
Utilities, torch and venting gases, air instruments, inert gases | √ | √ | √ | √ | √ |
Trade | Subdivision of applications | piston compressor | screw compressor | centrifugal compressor | ||
AP1618 Piston type | diaphragm type | Screw type | Turbine type (monopole) | multiple-step type | ||
Petroche mical | Butadiene, ethylene, low density polyethylene (LDPE) | √ | √ | √ | √ | |
Evaporable Gas (BOG) (ethylene), process gas supplementation and recovery | √ | √ | √ | √ | √ | |
Ethylene, purified terephthalic acid (PTA), high density polyethylene (HDPE), linear low density polyethylene (LLDPE), vinyl chloride (VCM), phenol | √ | √ | √ | √ | √ | |
Utilities, torch and venting gases, air instruments, inert gases | √ | √ | √ | √ | √ | |
Caprolactam plant | √ |
Trade | Subdivision of applications | piston compressor | screw compressor | centrifugal compressor | ||
AP1618 Piston type | diaphragm type | Screw type | Turbine type (monopole) | multiple-step type | ||
Chemical | Mechanical vapor recompression | √ | √ | √ | ||
Fluorine production, chemical paint, chlorine | √ | √ | ||||
Pharmaceutical processes, research and laboratories | √ | |||||
Agricultural chemical process cooling and key gases | √ | |||||
sewage disposal | √ | |||||
polycrystalline silicon | √ | √ | ||||
Urea plant, nitric acid plant, synthetic ammonia plant, lime kiln gas plant | ||||||
Mechanical vapor recompression | √ | √ |
Trade | Subdivision of applications | piston compressor | screw compressor | centrifugal compressor | ||
AP1618 Piston type | diaphragm type | Screw type | Turbine type (monopole) | multiple-step type | ||
Power generation | Vapor recovery, landfills, biogas, synthetic gases | √ | √ | √ | ||
Nuclear fuel, compressed radioactive gas and leak recovery, pressure test | ||||||
Transportation and distribution of hydrogen and natural gas fuels, fuel cells | √ | √ | ||||
Gas turbine supply | √ | √ | √ | √ | ||
Flue gas desulfurization (FGD), circulating fluidized bed (CFB) | √ | |||||
Carbon dioxide capture and dehydration, gas desulfurization (oxidation) | √ | √ | √ |
Trade | Subdivision of applications | piston compressor | screw compressor | centrifugal compressor | ||
AP1618 Piston type | diaphragm type | Screw type | Turbine type (monopole) | multiple-step type | ||
Industrial | Industrial gas / cylinder filling, special gases, aerospace, food and beverage, blow molding and carbon dioxide recovery | √ | √ | √ | √ | |
Cars, airbag filling, fuel tank manufacturing | √ | |||||
Fluorinated gases used in tetrafluoroethylene (TFE), lubricants, reactants, refrigerants and electronic processes | √ | √ | ||||
Steel and coke application, coke oven gas, pollution gas | √ | √ | √ | √ | √ | |
fermentation industry | √ | |||||
High temperature gas, gas with different molecular weights | √ | |||||
Carbon black, fuel gas | ||||||
Mining, smelting, metal refining, sulphuric acid plants | √ | |||||
Industrial refrigeration, process cooling, mine cooling | √ | √ | √ | |||
Blast furnace, air separation unit, coke oven gas, sintering gas | √ | |||||
pneumatic transmission | ||||||
Wastewater treatment, sewage treatment | √ | √ | ||||
Vacuum vehicles and high vacuum applications | √ | √ | √ | |||
Vacuum oscillation adsorption (air separation) | √ | |||||
Vacuum (wet / dry, such as vacuum in paper machine, vacuum filter, ash conveying) | √ | √ | ||||
Dairy, food and beverage processing, mechanical vapor compression (MVC)/mechanical vapor recompression (MVR) | √ | |||||
Aeration (general) | √ | √ | ||||
ater recovery / zero liquid discharge, desalination and distillation | √ | |||||
Waste heat recovery (expander) | √ |
Conclusion
In short, the compressor industry has a rich variety of subdivisions, which are interrelated and interact with each other, driving the continuous development and progress of the industry.
MINNUO has been focusing on compressor production for more than 30 years. We have the most professional team of engineers to tailor compressed gas solutions for you. You are welcome to consult!