Piston compressors are widely used in industries such as petrochemical, power, and metallurgy. The working principle of a piston compressor relies on the reciprocating motion of the piston inside the cylinder to compress gas. They are characterized by a simple structure, ease of operation, and strong adaptability. However, due to complex working environments and varying operating conditions, piston compressors are prone to various failures during operation, which can severely impact the production process.
Piston compressors may experience a range of issues, mainly including piston ring wear, cylinder wear, piston rod fracture, valve failure, lubrication system issues, and sealing problems. Common maintenance methods include replacing or repairing worn parts, optimizing designs, improving lubrication, enhancing sealing, and regularly cleaning and maintaining components.
Working Principle of Piston Compressors
The working process of a piston compressor mainly includes four stages: intake, compression, exhaust, and expansion. During the intake stage, the piston moves from one end of the cylinder to the other, lowering the pressure inside the cylinder, allowing external gas to enter the cylinder through the intake valve. In the compression stage, the piston compresses the gas inside the cylinder, increasing the pressure. Then, in the exhaust stage, the gas is expelled through the exhaust valve. Finally, in the expansion stage, the piston moves in the opposite direction, reducing the pressure in the cylinder and preparing for the next intake.
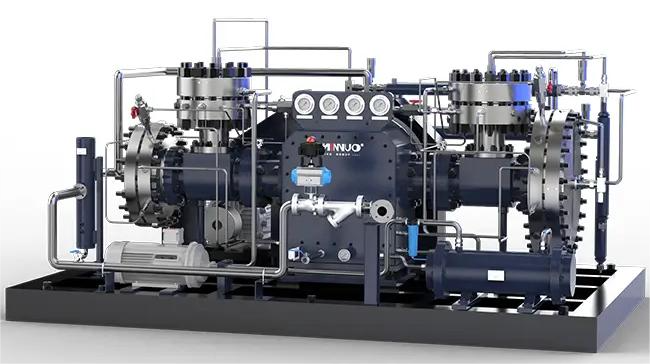
Common Failures and Maintenance of Piston Compressors
Piston Ring Wear
- Causes: Poor material quality of the piston rings, excessive friction coefficient between the piston rings and the cylinder wall, improper installation of the piston rings, prolonged operation in high-temperature environments, etc.
- Maintenance: Replace the piston rings with high-quality, wear-resistant ones; adjust the installation of the piston rings to ensure a tight fit with the cylinder wall; regularly lubricate the piston rings to reduce friction; optimize the piston ring design to improve wear resistance.
Cylinder Wear
- Causes: Excessive friction between the piston and the cylinder wall, excessive impurities in the gas inside the cylinder, excessive piston speed, poor lubrication of the cylinder, etc.
- Maintenance: Repair or replace the cylinder, selecting the appropriate repair method based on the degree of wear; improve the filtration of gas inside the cylinder to reduce damage from impurities; adjust the piston speed to avoid damage from excessive motion; enhance lubrication conditions for the cylinder to improve its wear resistance.
Piston Rod Fracture
- Causes: Poor material quality of the piston rod, excessive stress on the piston rod, improper installation of the piston rod, fatigue damage from long-term operation, etc.
- Maintenance: Replace the piston rod with one of higher quality and strength; analyze the stress on the piston rod to identify the fracture cause and take corresponding measures; reinstall the piston rod, ensuring it is securely fixed; strengthen the maintenance of the piston rod, and regularly inspect its operating condition.
Valve Failure
- Causes: Poor valve sealing, damaged valve springs, worn valve cores, corrosion of the valve during long-term operation, etc.
- Maintenance: Replace the valve, check the sealing to ensure it is tight; replace the valve spring to ensure its elasticity; repair or replace the valve core to improve valve performance; regularly maintain and clean the valve to remove impurities.
Lubrication System Failure
- Causes: Insufficient lubrication oil, poor quality of lubrication oil, blockage in lubrication system pipes, lubrication pump failure, etc.
- Solution: Replenish lubrication oil and choose the appropriate type; replace lubrication oil and ensure its quality; clean the lubrication system pipes to ensure smooth oil circulation; inspect the lubrication pump to ensure it is functioning properly.
Sealing Issues
- Causes: Aging of sealing materials, improper installation of seals, damage to sealing surfaces, corrosion of seals over extended operation, etc.
- Solution: Replace seals with high-quality, highly effective sealing components; adjust the seal installation position to ensure a tight fit between the seal and the sealing surface; repair or replace sealing surfaces to improve sealing performance; enhance maintenance and care of seals, and regularly check their working condition.
Cooling System Failure
- Causes: Cooling water pump failure, blockage in cooling pipes, low water level in the cooling tank, poor heat dissipation of the cooling system, etc.
- Solution: Inspect the cooling water pump to ensure it is working properly; clear the cooling pipes to ensure smooth flow; replenish the cooling tank to maintain an adequate water level; optimize the design of the cooling system to improve heat dissipation efficiency.
Abnormal Vibration
- Causes: Imbalanced piston movement, improper compressor installation, loose internal components, external interference during operation, etc.
- Solution: Adjust the balance of piston movement and check the gap between the piston and the cylinder; reinstall the compressor to ensure a secure installation; inspect internal components to ensure none are loose; strengthen maintenance practices and minimize external interference.
Abnormal Pressure
- Causes: Instability in intake pressure, excessively high exhaust pressure, imbalance in internal compressor pressure, external interference during operation, etc.
- Solution: Adjust intake pressure to ensure stability; reduce exhaust pressure to avoid excessive pressure; check internal pressure balance and ensure it is normal; enhance maintenance practices and reduce external interference.
Insufficient Exhaust Volume
- Causes: Blocked intake, poor sealing of intake valves, excessive piston speed, external interference during operation, etc.
- Solution: Clean the intake to ensure it is unobstructed; check the valve seals to ensure they are intact; adjust piston speed to increase exhaust volume; strengthen maintenance and reduce external interference.
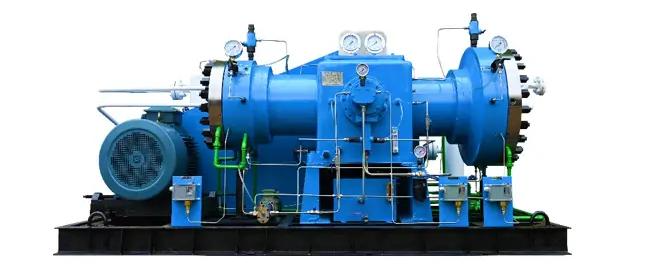
Conclusion
Piston compressors may encounter various faults during operation. By analyzing common failures and corresponding solutions, we can significantly improve the operational efficiency and reliability of piston compressors. Regular maintenance is crucial to identify and resolve issues promptly, ensuring smooth operation.
As a leader in the compressor industry, MINNUO continually optimizes the design and performance of piston compressors. Our compressors are not only of exceptional quality but also capable of withstanding extreme working environments. Feel free to contact us for consultation!