As industrialization accelerates, climate change has become an urgent global issue, with CO₂, the primary greenhouse gas, drawing significant attention for its reduction and management; CO₂ recovery and utilization, through Carbon Capture and Utilization (CCU) technologies, has emerged as a key solution to mitigate climate change and drive green economic transformation.
CO₂ recovery and utilization technologies mainly include amine scrubbing and cryogenic separation methods. Amine scrubbing is suited for high-concentration emission sources, where an amine solution chemically absorbs CO₂. After processes like initial filtration, adsorption, solution regeneration, and gas compression and storage, it captures CO₂ efficiently and flexibly. Cryogenic separation targets low-concentration emission sources, using low temperatures to liquefy CO₂ through a phase change, achieving high efficiency and high-purity CO₂ output.
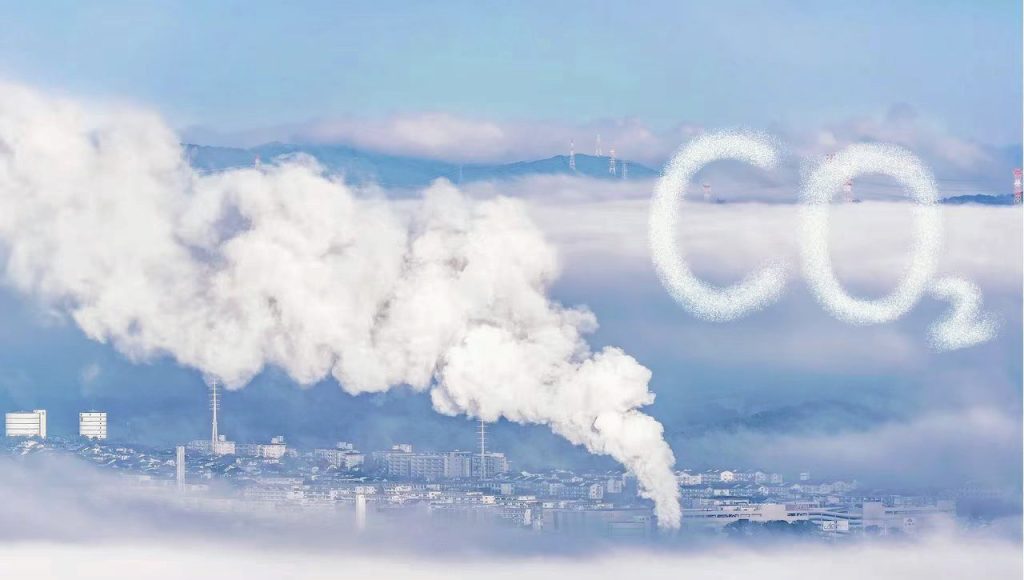
Global Carbon Emission Regulations and Industry Pressures
In the face of severe global warming, many countries and regions, especially the European Union, have gradually implemented carbon taxes and carbon market trading mechanisms, forcing businesses to adopt more stringent emission reduction measures. This has created significant economic pressure for high-carbon-emission industries such as cement, steel, fertilizers, and petrochemicals. Against this backdrop, CO₂ recovery and utilization (CCU) has not only become a key technology for mitigating climate change but also an effective means for companies to reduce carbon emissions, optimize cost structures, and enhance their competitiveness in the green economy.
The Significance of CO₂ Recovery and Utilization
From an economic perspective, CO₂ recovery and utilization can significantly reduce the economic burden of carbon emissions for businesses, avoid emission penalties, and create potential revenue. For instance, CO₂ can be used in processes like beverage production, fertilizer manufacturing, and enhanced oil recovery, turning it into a profitable byproduct for businesses. In some cases, companies may also benefit from government subsidies or rewards.
From an environmental responsibility perspective, CO₂ recovery and utilization provide sustainable emission reduction solutions for businesses. By capturing and utilizing CO₂, companies not only reduce direct emissions and alleviate environmental pollution but also provide technical support for mitigating global warming and addressing climate change. Increasingly, leading companies are integrating CO₂ capture and utilization technologies into their long-term strategies, driving the development of green industries and creating a win-win situation for both economic and environmental benefits.
Technical Challenges in CO₂ Recovery
Despite significant advancements in CO₂ recovery technologies in recent years, businesses still face substantial technical challenges in scaling up for industrial applications.
Emission Volume and CO₂ Concentration
The CO₂ concentration of emission sources is one of the key factors determining the difficulty and economic feasibility of recovery technologies. For large-emission sources in traditional industries like cement, steel, and fertilizers, the CO₂ concentration in exhaust gases is relatively high, making recovery more favorable. In high-concentration situations, existing capture technologies can efficiently separate and extract CO₂, with costs controlled within a reasonable range, making them quite feasible. However, for special emission sources such as Direct Air Capture (DAC) aimed at low-concentration CO₂ environments (with CO₂ in the atmosphere at only about 0.04%), the technical challenges are considerable. Low concentrations lead to inefficient capture and increased consumption of adsorption materials, raising recovery costs. There is an urgent need to develop more efficient, low-cost adsorption materials and innovative capture technology frameworks to overcome this bottleneck.
Production Process and Equipment Compatibility
When selecting CO₂ recovery technologies, businesses must carefully consider their compatibility with existing production processes and equipment. For example, amine scrubbing requires optimization to integrate the CO₂ capture system into existing industrial workflows. Variations in temperature, pressure, and complex chemical reactions in industrial processes can interfere with the system’s performance and even cause efficiency losses. Engineers must adopt a systems approach, balancing various physical and chemical parameters, adjusting processes, and improving equipment to ensure seamless integration of CO₂ capture systems into existing production lines, minimizing disruptions to normal operations.
Cost and Return on Investment
Even as CO₂ recovery technologies mature, the high initial investment and ongoing operational and maintenance costs remain significant barriers for businesses. For small and medium-sized enterprises (SMEs), limited financial resources and weak risk tolerance make it crucial to select the most suitable technological solution within a limited budget. This requires calculating costs for equipment procurement, installation, and commissioning, while also estimating long-term operational costs, including energy consumption, materials replenishment, and equipment maintenance. A comprehensive cost-benefit analysis, considering the anticipated revenue from CO₂ recovery and utilization, is necessary to develop the most economically viable implementation strategy.
CO₂ Recovery Technologies
Currently, two main CO₂ recovery technologies are widely used: amine scrubbing and cryogenic separation.
Amine Scrubbing
Amine scrubbing, known for its outstanding performance, currently dominates the CO₂ capture field, especially for high-concentration industrial emissions.
Basic Principle
Amine solutions (such as monoethanolamine (MEA)) utilize their unique chemical adsorption properties to react with CO₂ molecules, forming stable carbonate compounds and achieving efficient separation from the mixed gas stream. By heating the amine solution, the carbonate compounds decompose, releasing CO₂ for recovery.
Technical Process
- Initial Filtration: Prior to the adsorption step, specialized filtration devices remove impurities like sulfides and nitrides from the gas flow. These impurities could interfere with the chemical reaction between CO₂ and the amine solution and corrode subsequent equipment. Thus, pre-purification is crucial.
- CO₂ Adsorption: The purified gas comes into contact with the amine solution in a specific absorption tower, where CO₂ molecules rapidly combine with amines, forming carbonate compounds, completing the essential gas capture step.
- Solution Regeneration: The CO₂-saturated amine solution is transported to a regeneration unit, where it is heated using an external heat source, breaking the chemical bonds of the carbonate compounds and releasing high-concentration CO₂ gas. The regenerated amine solution is then ready for the next adsorption cycle.
- Gas Compression and Storage: The separated CO₂ gas is typically compressed in multiple stages to increase pressure, making it suitable for storage or direct delivery to utilization processes, effectively managing and storing CO₂ resources.
Technical Advantages
- High Efficiency: Amine scrubbing offers exceptional efficiency for high-concentration CO₂ emission sources, ensuring substantial CO₂ recovery and significantly reducing a company’s carbon emissions.
- Flexibility: With its mature process system, amine scrubbing can be optimized according to the specific emission characteristics and production process of different industries, easily integrated into existing production lines with minimal disruption to normal operations.
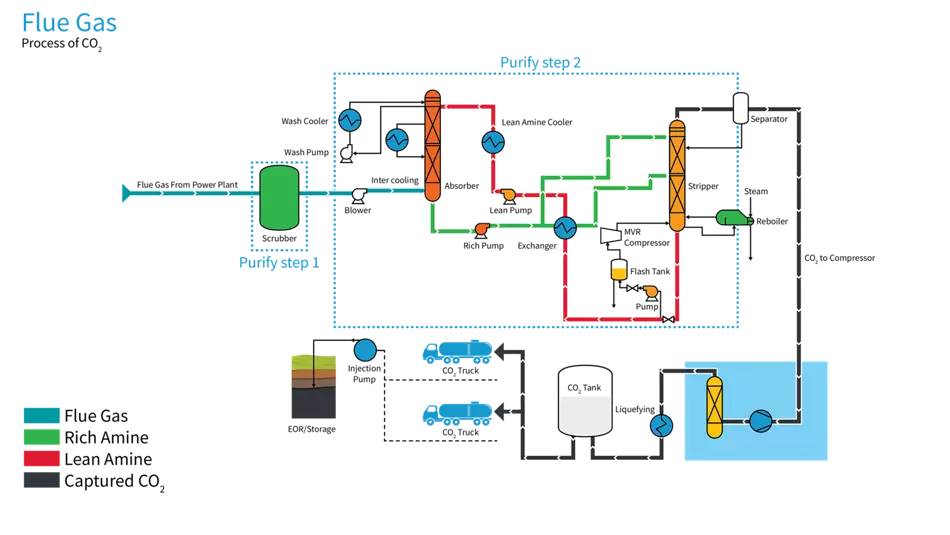
Cryogenic Separation
Cryogenic separation is a key CO₂ recovery technology, particularly effective for low-concentration CO₂ emissions.
Basic Principle
This method uses the physical properties of CO₂ at low temperatures. By deep cooling, the gas temperature is lowered to extremely low levels, causing CO₂ to liquefy by crossing the critical temperature, with separation from other mixed gases based on differences in gas-liquid density.
Technical Process
- Pre-cooling: The gas enters a pre-cooling unit, where a cooling medium (such as liquid nitrogen or refrigerant) gradually absorbs heat, preparing the gas for deeper liquefaction.
- Gas Liquefaction: The pre-cooled gas enters a cryogenic liquefaction unit, where it is subjected to conditions near or below CO₂’s critical temperature (-31.1°C, 7.38 MPa). The CO₂ molecules bond more strongly and transition to liquid form, separating from the gas phase.
- Compression and Recovery: The separated liquid CO₂ is then compressed, increasing its pressure to meet the needs for storage, transportation, or further utilization processes.
Technical Advantages
- High Efficiency: Cryogenic separation efficiently captures CO₂ from low-concentration emission sources, overcoming limitations of traditional technologies.
- High Purity: Due to the physical phase-change separation process, the liquid CO₂ produced is highly pure, with minimal impurities. This is particularly beneficial for industries requiring high-purity CO₂, such as food, electronics, and pharmaceuticals.
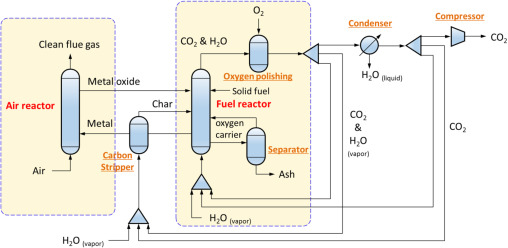
CO₂ Compression and Storage Technology
Regardless of the CO₂ recovery method used, compression and storage are crucial steps that connect the recovery process to utilization.
Compressor Technical Requirements
CO₂ compressors face several challenges during operation. The increasing pressure during compression places high mechanical demands on equipment, ensuring the ability to withstand high pressure without leakage, deformation, or rupture. Additionally, CO₂ is corrosive under certain humidity conditions, especially at high pressures, which accelerates corrosion of metal components. Thus, the selection of materials for compressors is vital, typically involving stainless steel or corrosion-resistant alloys, with optimized material structure and surface treatments to ensure long-term stable operation and high compression efficiency.
MINNUO’s Solution
MINNUO has deep expertise in CO₂ compression technology, offering advanced CO₂ compressors that combine cutting-edge technological breakthroughs. Our compressors address the challenge of balancing corrosion resistance with high efficiency, featuring unique sealing structures and anti-corrosion coatings. We optimize the fluid dynamics design of key components like the impeller and cylinder to enhance compression efficiency and reduce energy consumption. In practical applications, our compressors provide stable, continuous compression power for CO₂ recovery processes, ensuring smooth transition from low-pressure to high-pressure gas or liquid, laying a solid foundation for subsequent storage and utilization.
Conclusion
Although CO₂ recovery technologies still face challenges in research, cost control, and large-scale application, ongoing advancements in fundamental research and engineering technology, along with market demand, will gradually mature these technologies. In this process, a company’s ability to accurately identify needs, scientifically choose technological solutions, and adopt practical implementation strategies will ultimately determine success in the future CO₂ recovery and utilization market.
No matter what your compression needs are, MINNUO can provide the right solution for you. With compressors specifically designed for carbon dioxide compression, we can help you take an important step towards achieving your CO₂ recovery and utilization goals. Feel free to reach out for more information!