Causes and Solutions for Air Compressor Oil Leakage
Air compressors are indispensable equipment in industrial production, directly affecting production efficiency, quality, cost, and safety. Oil leakage not only wastes lubricating oil but may also lead to equipment damage, production interruptions, and safety hazards. In depth research on air compressor oil leakage is crucial for ensuring the sustainable development of industrial production. This article will provide a systematic solution from aspects such as the types of oil leakage, hazards, troubleshooting steps, and preventive measures.
The causes of air compressor oil leakage include phenomena such as oil seepage, oil dripping, and oil spraying, which are usually caused by seal failure, loose connection parts, or blockage of the oil cooler. Oil seepage usually stems from the aging of seals or loose connections. Oil dripping is mostly caused by poor sealing and pressure fluctuations, while oil spraying is related to the blockage of the oil cooler. Solutions include tightening connection parts, replacing seals, cleaning the oil cooler and oil circuit system, and checking oil pressure.
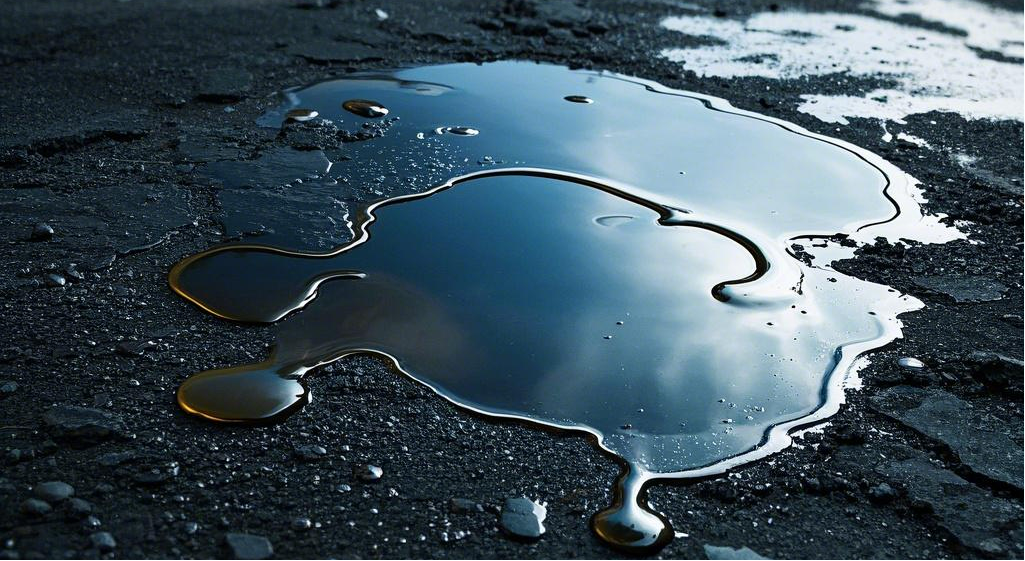
I. Types, Causes, and Solutions of Air Compressor Oil Leakage
A. Oil Seepage Phenomenon
1. Formation Mechanism
Oil seepage usually results from the failure of the sealing structure at the connection parts. During the operation of the air compressor, the internal pressure of the oil system is in a dynamic change. When the sealing gasket is affected by factors such as temperature, pressure, and chemical corrosion, it ages and deforms, or the threaded connection parts become loose due to vibration, thermal expansion, and contraction, resulting in an increase in the sealing gap. Then, under the action of the pressure difference, the lubricating oil slowly seeps out through microscopic pores. This seepage process is based on the principles of capillary action and microscopic flow driven by pressure.
2. Characteristic Manifestations
In the initial stage, oil seepage is extremely concealed. The amount of seepage is tiny, and only an extremely thin oil film forms on the equipment surface, which is difficult to detect with the naked eye. Over time, a small amount of oil droplets may accumulate. The dripping frequency is low, and the size of the oil droplets is small. The seepage area is relatively scattered, mostly distributed near multiple connection parts.
3. Treatment Methods
- For oil seepage due to loose connection parts, after ensuring the safe shutdown of the air compressor, use a high precision torque wrench to tighten the connection parts according to the specified torque value.
- For oil seepage due to the aging and damage of seals, select suitable seals according to the equipment specifications and replace them. Ensure proper installation in strict accordance with the installation process requirements.
B. Oil Dripping Phenomenon
1. Formation Mechanism
The oil dripping phenomenon is mainly caused by poor sealing at the connection parts and internal pressure fluctuations in the air compressor. When the sealing performance deteriorates and the internal pressure of the air compressor suddenly increases or fluctuates frequently due to load changes or air path blockages, the lubricating oil will intermittently drip from the weak sealing areas. This phenomenon involves the transient changes in pressure and flow in fluid dynamics and the response of the sealing structure to pressure fluctuations.
2. Characteristic Manifestations
The lubricating oil falls in the form of relatively regular droplets. The dripping frequency is more obvious than that of oil seepage, and the size of the oil droplets is larger. The dripping position is concentrated below the connection parts with poor sealing, and obvious oil droplet tracks or oil spots may form on the equipment surface.
3. Treatment Methods
- After shutdown, comprehensively check the connection parts that may have sealing problems, including the tightness of the connection parts and the integrity of the seals.
- Re tighten the loose connection parts to the specified torque and replace the damaged seals in a timely manner.
- Check the operating conditions of the air compressor and eliminate factors causing abnormal pressure fluctuations, such as cleaning the air path blockage and adjusting the load, to prevent recurrence.
C. Oil Spraying Phenomenon
1. Formation Mechanism
Oil spraying is a relatively serious oil leakage phenomenon, mainly caused by the blockage of the oil cooler. In the lubrication system of the air compressor, the oil cooler cools the high temperature lubricating oil to an appropriate temperature. If the oil cooler is blocked by dirt, impurities, metal shavings, or oil oxidation deposits, the flow of the lubricating oil is blocked, and the pressure in the oil system rises sharply. When it exceeds the bearing limit of the sealing parts, the lubricating oil will spray out from the weak parts. This process involves fluid mechanical principles such as pipeline flow, pressure accumulation, and seal failure.
2. Characteristic Manifestations
Oil spraying is manifested as a large amount of lubricating oil spraying out from specific parts of the air compressor in a short time, accompanied by obvious pressure impact and sound. The spraying area is concentrated, and the amount of sprayed lubricating oil is large, forming a large area oil stain on the surrounding equipment and the ground.
3. Treatment Methods
- Thoroughly clean and unclog the oil cooler, combining chemical and physical cleaning methods. First, soak it with a professional cleaning agent to dissolve and soften the dirt, and then use a high pressure water gun or special tools to remove impurities and deposits to ensure smooth channels.
- Comprehensively check and clean the entire oil circuit system, including components such as filters, oil pipes, and oil pumps, to prevent residual impurities from causing blockages again.
- Check and replace the sealing parts to ensure that they can withstand normal working pressure.
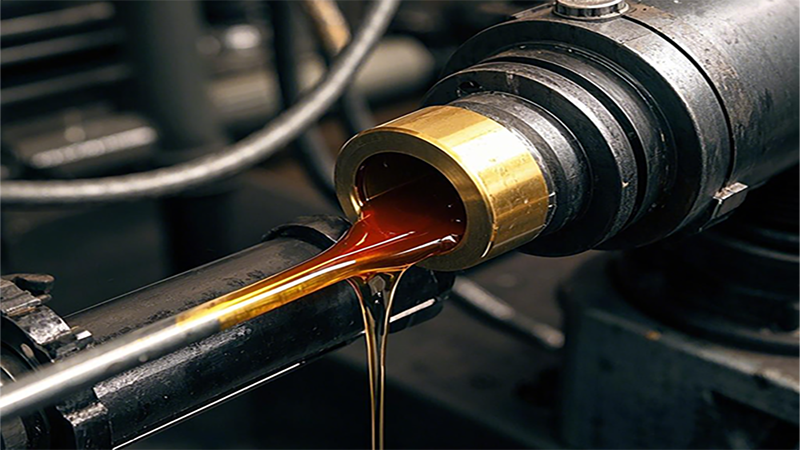
II. How to Troubleshoot Oil Leakage Points
A. Initial Visual Inspection
1. Overall Observation Process
After the air compressor is shut down and fully cooled, follow a strict inspection process to conduct a systematic visual inspection of all parts of the equipment from the top down and from front to back. Maintenance personnel need to have keen observation skills and rich experience to identify subtle oil leakage signs on the equipment surface.
2. Key Part Inspection
- Focus on inspecting key parts such as the front and rear oil seals of the crankshaft and the rear oil seal of the camshaft.
- For the front oil seal of the crankshaft, check whether it is broken, aged, or the rubber has hardened and lost elasticity, and whether the contact surface with the crankshaft pulley is worn or scratched.
- For the rear oil seal of the crankshaft, check whether it is damaged or aged, and whether the oil return hole of the rear main bearing cover is blocked due to design or other reasons, resulting in poor oil return.
- Due to the special working environment, the rear oil seal of the camshaft may also age and crack. Inspection can be carried out with the help of tools such as magnifying glasses and endoscopes.
- Check other key parts of the engine lubrication system one by one, such as the front and rear cylinder head covers, front and rear valve tappet chambers, oil filters, and oil pan gaskets, and record and analyze any subtle oil leakage traces.
B. Oil Seal Oil Leakage Troubleshooting
1. Association with the Crankcase Ventilation Device
If no obvious oil leakage points are found during the initial visual inspection, but there are signs of oil leakage at parts such as the front and rear cylinder head covers, front and rear valve tappet chambers, oil filters, and oil pan gaskets, the focus of troubleshooting should be shifted to the crankcase ventilation device. The crankcase ventilation system is crucial for maintaining the pressure balance in the crankcase. When this system malfunctions, the pressure in the crankcase rises abnormally, causing the lubricating oil to seep out from weak sealing parts, resulting in oil leakage in multiple places. This involves the relationship between pressure distribution and the sealing structure in fluid mechanics.
2. Troubleshooting Operation Points
- Thoroughly clean and unclog the crankcase ventilation pipeline, using a special cleaning agent and high pressure air to remove oil stains, impurities, and deposits to ensure smooth flow.
- Focus on checking the working condition of the PCV valve (Positive Crankcase Ventilation valve). This valve is prone to carbon deposition and jamming due to long term exposure to harsh environments.
- Use professional testing tools to check whether it can open and close normally under different working conditions and whether the opening degree meets the requirements. If there are problems, clean or replace it in a timely manner to restore normal performance and solve the oil leakage problem.
C. Oil Pressure Related Troubleshooting
1. Basis for Oil Pressure Detection
If the oil leakage phenomenon still exists after tightening the oil filter and some oil pipeline joints, attention should be paid to the oil pressure. Abnormal oil pressure is an important potential factor for oil leakage at the joints. According to the principles of fluid mechanics, too high oil pressure will subject the sealing parts to additional pressure, causing oil leakage when the bearing capacity is exceeded. Therefore, accurate measurement of oil pressure is crucial for judging the cause of oil leakage.
2. Inspection of the Oil Pressure Relief Valve
- Use a high precision oil pressure measuring instrument to accurately measure the air compressor oil pressure according to the standard process, ensuring that the measurement point can reasonably reflect the pressure of the oil system.
- Compare the measured oil pressure value with the design standard value to determine whether it exceeds the normal range. If the oil pressure is too high, conduct an in depth inspection of the oil pressure relief valve.
- The oil pressure relief valve is a pressure regulating component. When it malfunctions, such as valve core wear, impurity jamming, or insufficient spring elasticity, the oil pressure will rise out of control.
- Disassemble, clean, and test the components according to the maintenance manual. Replace parts with severe wear or insufficient elasticity in a timely manner. After assembly, test the performance to ensure that it can accurately regulate the oil pressure and solve the oil leakage problem.
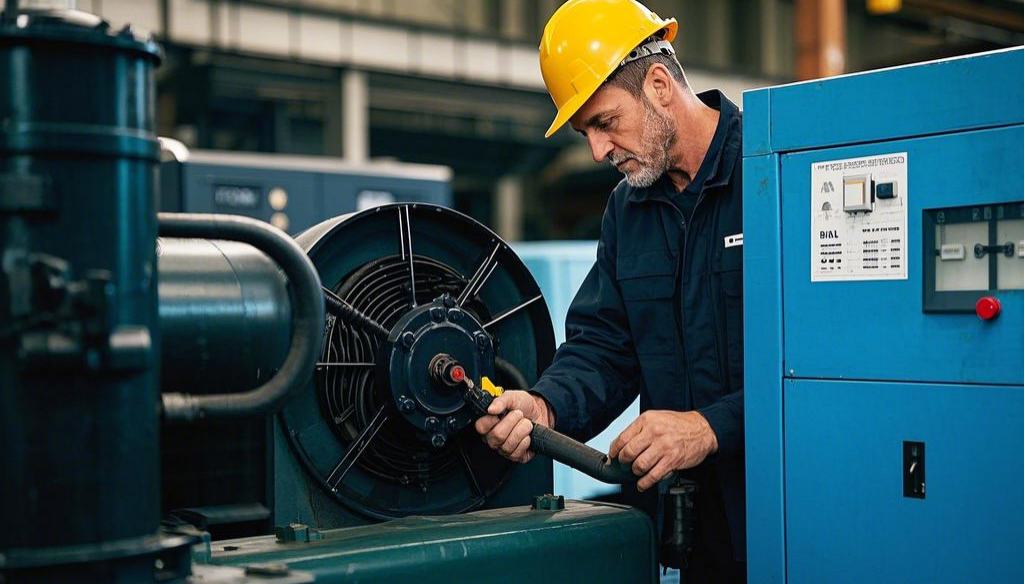
III. Hazards of Air Compressor Oil Leakage
A. Damage to Equipment Performance and Life
From the perspectives of materials science and tribology, oil leakage leads to insufficient lubrication, disrupts the lubrication state between components, and significantly increases the friction coefficient. Take a piston type air compressor as an example. The dry or semi dry friction between the piston and the cylinder wall intensifies, resulting in increased wear and generating a large amount of heat, causing thermal deformation of the components and destroying the fit accuracy. Over time, key components such as the piston and the cylinder wall will be severely worn, shortening the equipment life. At the same time, the lubrication system will experience chain failures. Insufficient oil suction by the oil pump leads to a decrease in oil pressure, affecting the lubrication of other transmission components such as bearings and gears, accelerating their wear and fatigue spalling, and even causing the failure of the lubrication system.
B. Reduction in Production Efficiency
In the modern industrial production system, air compressors are a key link. Downtime due to oil leakage faults will paralyze downstream equipment that relies on compressed air, disrupt production plans and delay progress. Moreover, troubleshooting and maintenance are time consuming and labor intensive. Not only do we need to find the oil leakage points, but the downtime may also cause abnormalities in other components, which need to be inspected and maintained together, greatly reducing production efficiency and causing economic losses.
C. Increase in Safety Hazards
1. Risk of Slipping and Falling
From the perspective of ergonomics, the lubricating oil on the ground reduces the friction between the sole and the ground, increasing the probability of people slipping and falling. This is especially serious in precision workshops or high altitude workplaces.
2. Fire and Explosion Risks
Lubricating oil is flammable and can easily cause a fire when it encounters an open flame, high temperature heat source, or electric spark. In industries such as chemical engineering and painting, due to the presence of flammable and explosive gases or dust in the environment, an explosion may occur, resulting in significant casualties and property losses.
3. Occupational Health Hazards
Long term exposure to an environment containing oil mist may damage the respiratory system of personnel, causing inflammation, lung diseases, etc. when inhaled. Contact with the skin may also cause allergic and other discomfort symptoms.
D. Environmental Pollution
1. Soil Damage
A large amount of leaked lubricating oil flowing into the soil changes the physical and chemical properties of the soil, affects the survival and reproduction of microorganisms, inhibits the growth of plant roots, and disrupts the ecological balance.
2. Water Pollution
When lubricating oil enters the water body, it forms an oil film, which hinders the exchange of oxygen, reduces the dissolved oxygen, and endangers aquatic organisms. Harmful substances will also accumulate through the food chain, affecting the ecosystem.
3. Corporate Responsibility
With the increasing strictness of environmental protection regulations, enterprises may face fines for environmental pollution caused by oil leakage, damage to their reputation, and need to invest funds in treatment and restoration, increasing operating costs.
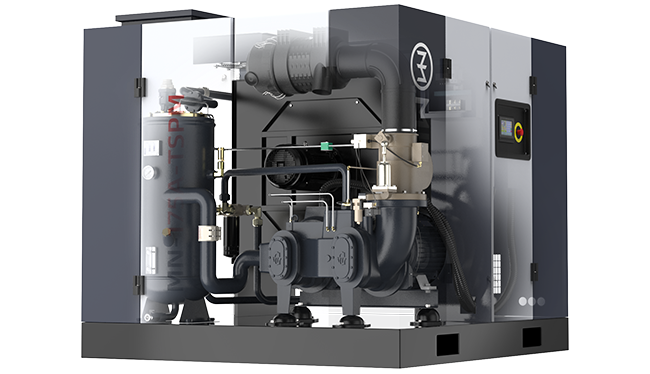
IV. Preventive Measures for Air Compressor Oil Leakage
A. Daily Maintenance
1. Regular Inspection of Sealing Parts
- Establish a scientific maintenance plan and set strict inspection cycles.
- Regularly and carefully inspect key sealing parts. Use non destructive testing techniques to detect signs of aging and wear in a timely manner.
- When problems are found, replace the sealing parts in a timely manner according to the equipment specifications to ensure good sealing performance.
2. Cleaning of the Oil System
- Regularly replace the appropriate lubricating oil as required to keep the oil system clean.
- Regularly clean the oil filter to ensure the filtering effect, prevent impurities from wearing the sealing parts, and reduce the risk of oil cooler blockage.
- It is possible to comprehensively clean the oil system regularly to remove dirt and deposits and keep the system unobstructed.
B. Standardized Operation Procedures
1. Operator Training
Provide systematic and professional training to air compressor operators, enabling them to deeply understand the working principle, operation procedures, and prevention and handling methods of common faults of air compressors.
If you need training, MINNUO will improve the professional skills and fault handling capabilities of operators through various methods such as theoretical training, practical operation demonstrations, and case analysis. We will emphasize the importance of standardized operation to avoid abnormal pressure fluctuations in the oil system and damage to the sealing parts caused by improper operation, such as starting and stopping too quickly or sudden load changes.
2. Following Operating Parameters
- Operate the air compressor strictly according to the parameters provided by the equipment manufacturer to ensure that the oil temperature, oil pressure, rotation speed, etc. are within the normal range.
- Install high precision monitoring instruments to monitor in real time and set alarm thresholds. When the parameters are abnormal, promptly remind the operators to take measures to avoid excessive pressure on the sealing parts and causing oil leakage.
C. Equipment Selection and Installation
1. Rational Selection
When purchasing an air compressor, fully consider the actual production needs and comprehensively evaluate the equipment performance, quality, and reliability. You can choose MINNUO air compressors with good sealing design and manufacturing processes. Our equipment adopts advanced sealing technologies and materials to ensure high oil leakage prevention performance at the design and manufacturing stage.
2. Correct Installation
Have the air compressor installed by a professional installation team in accordance with the requirements of the equipment installation manual. For example, during the installation process of MINNUO, we will definitely ensure that all components are tightly connected and well sealed, strictly control the installation accuracy, and have received no negative reviews in more than 30 years. For the installation of sealing parts, follow the correct installation methods and sequences to avoid seal failure due to improper installation. After installation, conduct a comprehensive commissioning and inspection to ensure that the equipment operates normally without oil leakage.
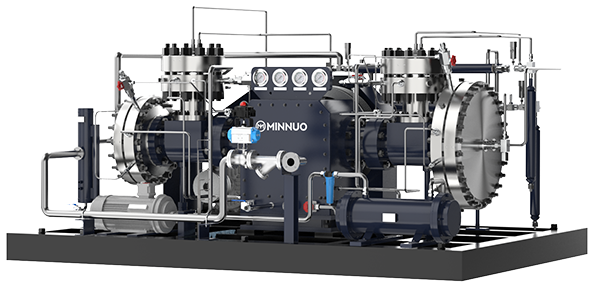
V. Conclusion
In general, solving the problem of air compressor oil leakage requires starting from multiple aspects such as equipment design and manufacturing, installation and commissioning, operation and use, and maintenance, forming a complete management system. Of course, if you have already chosen MINNUO, you don’t need to worry about the oil leakage problem, as we have the most professional engineering team!
If you have any needs, you are welcome to consult!