In recent years, laser cutting has occupied an important position in many fields such as metal processing, automobile manufacturing, aerospace, etc. with its advantages of high precision, high speed and small heat-affected zone. Stable, pure compressed air with pressure and flow adaptation is one of the key factors to achieve high-quality laser cutting. This article will deeply explore the professional and technical points that need to be considered when selecting an air compressor in the laser cutting industry, helping practitioners to make scientific and reasonable decisions.
When selecting an air compressor in the laser cutting industry, the exhaust volume and pressure range should be determined based on the power and gas demand of the laser cutting equipment; pay attention to the quality of gas production, and select products with high-efficiency filtration systems and high cleanliness of compressed air; give priority to air compressors with mature technology and stable performance to ensure reliability and stability; energy saving should also be considered, such as variable frequency technology products that can adjust the motor speed as needed to reduce energy consumption.
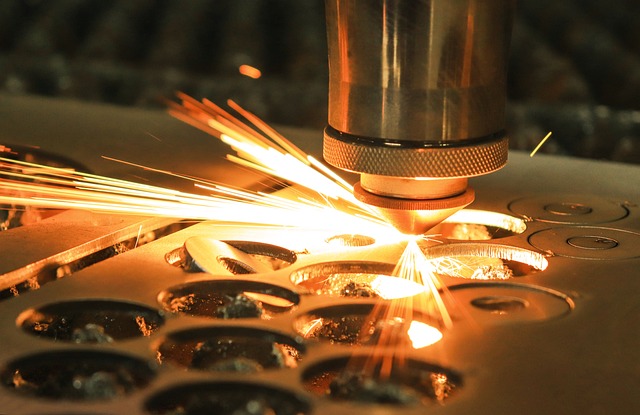
Requirements for compressed air in laser cutting process
Pressure requirements
When laser cutting different materials and thicknesses, there are fine requirements for compressed air pressure. The thicker the material, the greater the pressure required. Here you can refer to thin plate cutting:
Material Thickness (mm) | Typical Material | Compressed Air Pressure Range (MPa) | Notes |
---|---|---|---|
0.5 – 3 | Carbon/Stainless Steel | 0.8 – 1.2 | Suitable for thin plates; ensures slag removal and stable cutting |
3 – 10 | Carbon/Stainless Steel | 1.2 – 1.5 | Increased thickness requires higher pressure for energy transfer |
>10 | Carbon/Stainless Steel | 1.5 – 1.6+ | High-pressure demands to ensure smooth cutting and quality cut edges |
Flow rate requirements
The determination of flow rate is closely related to cutting speed, material thickness and cutting nozzle size. The faster the cutting speed and the thicker the material, the greater the air flow required. Take the common 2kW fiber laser cutting machine as an example:
Material Thickness (mm) | Cutting Power | Material Type | Airflow Range (m³/min) |
---|---|---|---|
3 | 2kW | Carbon Steel | 1.0 – 1.2 |
6 | 2kW | Carbon Steel | 1.5 – 1.8 |
At the same time, the aperture size of the cutting nozzle will also affect the flow demand. A nozzle with a larger aperture requires a higher air flow to maintain the cutting effect under the same cutting conditions. For example, when using a 2.0mm aperture nozzle to cut an 8mm stainless steel plate, the air flow needs to be increased by about 20% – 30% compared to a 1.5mm aperture nozzle to ensure that the slag can be blown away from the cutting area in a timely and effective manner to prevent slag and burrs on the cutting surface.
Air quality standards
The quality of compressed air has a decisive influence on the quality of laser cutting. Among them, moisture, oil and impurity content are the core indicators for measuring air quality. Excessive moisture content will cause oxidation and rust on the cutting surface, especially when cutting non-ferrous metals.
Generally, the dew point temperature of compressed air is required to be lower than -40℃. For high-precision cutting processes, the dew point temperature should reach below -70℃ to ensure that there is almost no moisture. The presence of oil will contaminate the optical lens of the cutting head and reduce the transmission efficiency and focusing accuracy of the laser. Therefore, the oil content must be strictly controlled below 0.01ppm. Impurity particles, such as dust, metal chips, etc., may block the cutting nozzle and affect the uniformity and stability of the airflow. The impurity particle size is required to be less than 0.01μm. In the titanium alloy laser cutting in the aerospace field, the quality requirements for compressed air are extremely high. Any tiny moisture, oil or impurities may cause microscopic defects on the cutting surface, affecting the performance and service life of the material.
Analysis of air compressor types
Piston air compressor
The piston air compressor is a more traditional type. Its working principle is to compress the air through the reciprocating motion of the piston. Its advantages are simple structure and relatively low price. It is suitable for some small laser cutting equipment that does not require high air source pressure and is used intermittently. However, the disadvantages of piston air compressors are also obvious, such as high noise, strong vibration, relatively low gas production efficiency, and the need for regular maintenance of pistons, cylinders and other components. In the long-term continuous operation of the laser cutting production line, its stability and reliability may not meet the needs.
Screw air compressor
Screw air compressors have been widely used in the laser cutting industry in recent years. It consists of a pair of intermeshing screw rotors that rotate and compress air, with significant advantages such as large gas production, stable pressure, low noise, and low vibration. Its high compression efficiency can meet the continuous and stable gas supply during laser cutting, and it is relatively easy to maintain. It only needs to regularly replace consumables such as lubricating oil, air filters, and oil-gas separators. However, the initial purchase cost of screw air compressors is high, but from the perspective of long-term operating costs and production benefits, it is a more ideal choice for medium and large laser cutting companies.
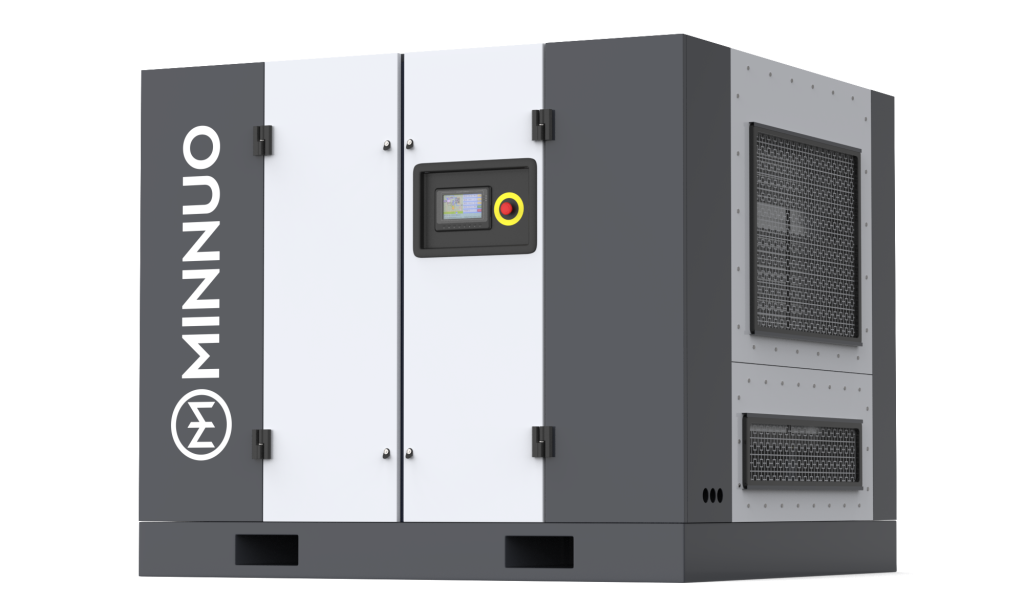
Determination of key parameters of air compressor
Pressure calculation and selection
When selecting the pressure of the air compressor for the laser cutting industry, not only the rated pressure requirements of the laser cutting equipment should be considered, but also a certain pressure margin should be reserved to cope with the pressure loss of the pipeline network, the pressure fluctuation during the peak of gas consumption, and the possible process upgrade requirements in the future. The pressure margin is generally recommended to be between 0.1 and 0.2MPa. For example, if the maximum working pressure of the laser cutting equipment is 1.3MPa, the rated pressure of the air compressor should be selected to be around 1.5MPa.
At the same time, the unloading pressure and loading pressure settings of the air compressor should also be considered. The unloading pressure is generally 0.1-0.15MPa higher than the rated pressure, and the loading pressure is 0.05-0.1MPa lower than the rated pressure. This can ensure that the air compressor operates stably within a certain pressure range and reduce energy waste and equipment wear caused by frequent start-stop. In practical applications, the pressure of the air compressor can be monitored and adjusted in real time through pressure sensors and control systems to ensure that it is always in the best working condition.
Flow calculation and selection
Accurately calculating the air flow required for laser cutting is a key step in selecting an air compressor. Flow calculation needs to comprehensively consider factors such as the type of cutting material, thickness, cutting speed, cutting nozzle size, and the number of cutting heads working simultaneously. The following formula can be used for preliminary estimation:
Q = k × A × V × n
- Q: Required airflow (m³/min)
- k: Flow coefficient (1.2-1.5, accounting for leaks and inefficiencies)
- A: Cutting area (m²)
- V: Cutting speed (m/min)
- n: Number of cutting heads
For example, a laser cutting workshop has 3 laser cutting machines. When each cutting machine cuts 5mm carbon steel, the cutting speed is 3m/min, the cutting nozzle size is 1.8mm, and the cutting area of a single cutting head is about 0.01m². According to the formula, the required air flow is about 1.35 – 1.69m³/min (take k = 1.3).
When selecting an air compressor, you should choose a product with a flow rate slightly larger than the calculated value to ensure that the gas demand for laser cutting can be met under various working conditions. At the same time, the exhaust volume adjustment range of the air compressor must also be considered. An air compressor with a wide range of exhaust volume adjustment function can better adapt to the needs of different cutting tasks and improve energy efficiency.
Air quality assurance measures
In order to meet the high quality requirements of laser cutting for compressed air, the air compressor system needs to be equipped with complete air quality assurance equipment.
Air dryer
The first is the air dryer, commonly used are refrigerated dryers and adsorption dryers. The refrigerated dryer cools the compressed air to below the dew point temperature through the refrigeration system, so that the water condenses into water droplets and is discharged. The dew point temperature of the compressed air can be reduced to 2-10℃, which is suitable for occasions where the moisture content requirement is not particularly high. The adsorption dryer uses the adsorption effect of adsorbents (such as molecular sieves, activated alumina, etc.) on water to reduce the dew point temperature to below -40℃ or even lower, which is suitable for high-precision laser cutting processes. In practical applications, a single dryer or a combination of dryers can be selected according to specific air quality requirements.
Air filter
The second is the air filter, including primary filter, medium filter and high efficiency filter. The primary filter mainly filters large particles of impurities in the air, such as dust, rust, etc., and the filtration accuracy is generally above 5μm; the medium filter further filters smaller particles of impurities, and the filtration accuracy is between 1-5μm; the high efficiency filter is used to remove tiny particles of impurities, oil mist, etc., and the filtration accuracy can reach below 0.01μm. Multi-stage filtration can ensure that the cleanliness of compressed air meets the requirements of laser cutting.
Qil-gas separator
In addition, for air compressors with oil lubrication (such as screw air compressors), it is also necessary to equip them with high-efficiency oil-gas separators to reduce the oil content in the compressed air to an extremely low level to prevent the oil from contaminating the cutting head lens and cutting surface.
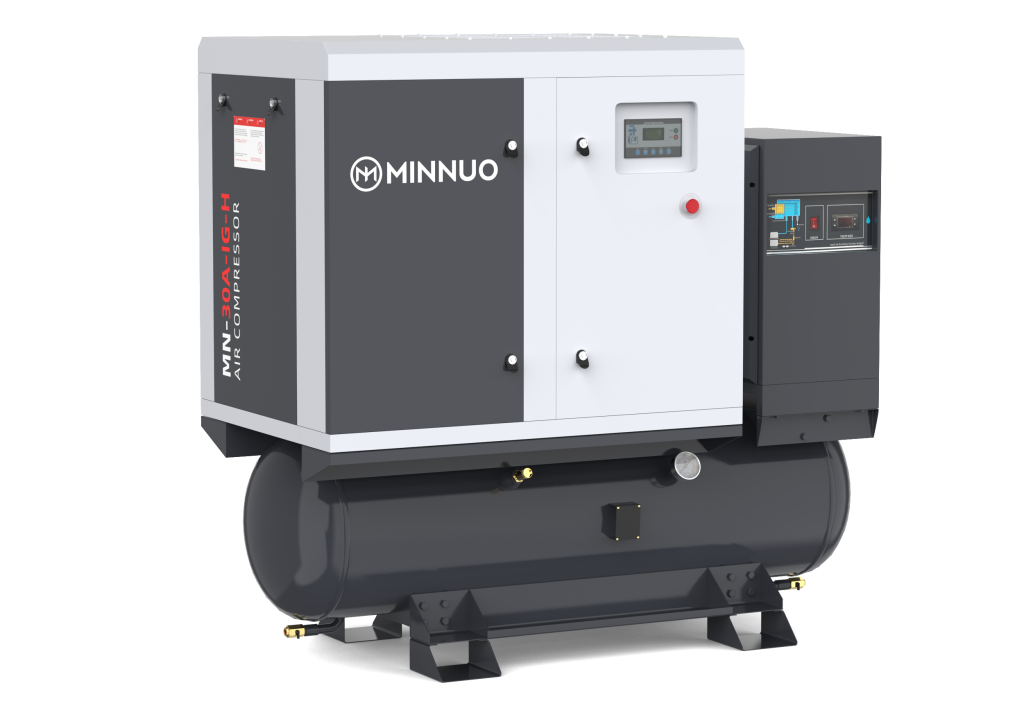
Permanent magnet variable frequency screw machine for laser cutting
If you still have doubts, you might as well take a look at the permanent magnet variable frequency screw machine for laser cutting, which is superior to traditional screw machines in all aspects.
Operation stability
Pressure stability: The permanent magnet variable frequency screw compressor utilizes the stepless speed regulation characteristics of the frequency converter. Through the controller or the regulator inside the frequency converter, it can start smoothly and can quickly adjust and respond to occasions with large fluctuations in gas consumption. The gas pressure stability is exponentially improved compared to the power frequency operation of the traditional screw compressor.
Small starting impact: The frequency converter itself contains a soft starter function, and the starting current is within 1.6 times the rated current, while the power frequency starting current of the traditional screw compressor is generally more than 6 times the rated current, which not only has a small impact on the power grid, but also greatly reduces the impact on the entire mechanical system.
Energy saving
Variable flow control: Traditional screw compressors can only work at one exhaust volume, while permanent magnet variable frequency screw compressors can adjust the motor speed in real time according to the actual gas consumption to control the exhaust volume, and can automatically sleep when the gas consumption is low, greatly reducing energy loss. The optimized control strategy can further improve the energy saving effect.
High motor efficiency: The permanent magnet variable frequency screw machine is driven by a permanent magnet synchronous motor, which can maintain extremely high motor efficiency at any speed. However, the efficiency of the traditional screw machine will drop significantly when the external inverter forces the motor to deviate from the rated speed.
Control accuracy
The variable frequency control system of the permanent magnet variable frequency screw machine has precise pressure control capabilities, which can make the air pressure output of the compressor highly match the air volume required by the user’s air system. The output air volume changes with the motor speed, and the pressure control accuracy can reach ±0.01Mpa, which effectively improves the working condition quality. The pressure adjustment speed of the traditional screw machine is slow, the fluctuation is large, and the accuracy is low.
Conclusion
In short, how to choose an air compressor in the laser cutting industry is a very challenging but crucial task. Only through comprehensive evaluation and weighing in all aspects and dimensions can we accurately lock in the most suitable air compressor model and configuration, build a solid, stable and efficient air source foundation for laser cutting operations, and effectively promote the laser cutting industry to move forward steadily on the track of high precision, high quality and sustainable development, gain better economic benefits and competitive advantages in the fierce market competition, and continue to contribute key forces to the vigorous development of related manufacturing industries.
If you want to know more, please consult MINNUO!