As a manufacturer of variable frequency drive (VFD) air compressors, we fully understand the importance of frequency conversion technology in modern industry. VFD air compressors optimize energy efficiency and stabilize operations through frequency conversion speed control. The VFD adjusts the output voltage and frequency by switching the IGBT (Insulated Gate Bipolar Transistor) inside, supplying the appropriate voltage based on the motor’s needs, achieving energy savings and speed control. As industrial automation continues to improve, VFD air compressors are becoming mainstream products, and VFDs have been widely adopted. However, improper installation of VFDs, especially retrofitting them on compressors not originally designed for VFD use, can cause significant damage to the motor. This article will analyze the potential impact of improper VFD installation on motors, the underlying reasons, and how to carry out a proper VFD retrofit to ensure the motor’s long-term stable operation.
Improper installation of a variable frequency drive (VFD) on a compressor can cause a series of damages to the motor, including: motor overheating, insulation layer aging due to reduced cooling efficiency; bearing currents caused by harmonic currents, leading to electrical arcing and accelerated bearing wear; high-frequency pulse voltages damaging the motor’s insulation system, resulting in insulation breakdown; and increased mechanical stress due to frequent starts and stops or low-speed operation, causing wear and aging of motor components. During the VFD retrofit process, selecting a compatible VFD motor, properly setting the VFD parameters, implementing effective protective measures, and optimizing the system based on actual working conditions are key to ensuring a successful modification. Of course, if you choose MINNUO, you won’t need to worry about any of these issues. We have the most professional engineers and a highly experienced technical team to design customized gas solutions for you.
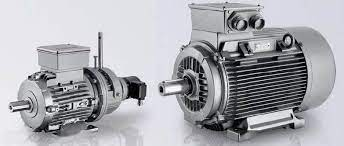
Overheating of the Motor in VFD Air Compressors
If a VFD is installed without proper calculation and configuration, it can cause the motor’s operating temperature to rise. The VFD controls the motor’s speed by adjusting the frequency, but a reduction in frequency can reduce the motor’s cooling efficiency. Traditional compressor motors are usually designed for optimal cooling at full speed, but at low speeds, the cooling airflow from the internal fan is greatly reduced, causing the motor’s temperature to increase. Extended operation at high temperatures can accelerate the aging of the motor’s insulation, ultimately shortening its lifespan.
The motor’s temperature rise is also closely related to load characteristics. During VFD retrofitting, if the load is not carefully assessed, the motor may operate at higher load levels at certain frequencies, exacerbating overheating. Additionally, low-frequency operation increases the magnetic flux density in the motor’s core, causing iron losses that contribute to overheating. To avoid motor overheating, it’s important to select a suitable VFD frequency range during the retrofit, ensuring effective cooling at all operating frequencies.
Bearing Current Damage from VFDs
The use of a VFD generates harmonic currents that can induce bearing currents in the motor. Harmonic currents are high-frequency components in the VFD’s pulse-width modulation (PWM) signal, which can affect the motor bearings through capacitive coupling, creating bearing currents. These currents can cause electrical arcing between the bearing balls and raceways, leading to pitting on the bearing surface. Over time, this wear and tear can damage the bearing and disrupt the motor’s operation, potentially causing irreversible mechanical failure. This problem is especially noticeable in motors not designed to handle harmonic currents, as they lack the necessary shielding and isolation to combat them.
The generation of bearing currents is closely related to the VFD’s output voltage characteristics. The PWM control method generates high-frequency pulses, which induce high-frequency voltages in the motor windings. These pulses are then transferred to the motor bearings through capacitive coupling, triggering bearing currents. To minimize bearing current damage, we recommend the following measures:
- Use VFD-compatible motors: These motors are designed with harmonic currents in mind, offering better shielding and insulation to reduce bearing currents.
- Install shaft current bypass devices: Bypass rings on motor bearings can effectively direct bearing currents to ground, reducing bearing damage.
- Use insulated bearings: In some applications, insulated bearings can effectively block bearing currents, protecting the bearings.
Damage to Motor Insulation Systems
The high-frequency pulse voltage generated by VFDs can place additional stress on the motor’s insulation system due to the high rise time (dv/dt) of these pulses. Traditional compressor motors are not designed to withstand such rapid pulses, which can weaken the insulation, especially under higher voltage conditions, ultimately leading to winding short circuits or insulation breakdown.
During the VFD retrofit, high-frequency pulses can cause partial discharge phenomena, which are detrimental to the motor’s insulation system. To reduce this risk, we suggest:
- Use appropriate VFD filters: Installing filters at the VFD’s output can effectively reduce high-frequency components, minimizing the impact of pulse voltage on the motor’s insulation system.
- Choose VFD-specific motors: These motors are designed with insulation systems that can handle high-frequency pulses, offering better protection against insulation breakdown.
- Optimize the VFD’s carrier frequency: The higher the carrier frequency, the more high-frequency components in the output voltage, which increases the strain on the motor insulation. Reducing the carrier frequency while maintaining control performance can lessen insulation damage.
Mechanical Stress from Frequent Starts and Low-Speed Operation
The introduction of a VFD can lead to the motor running at low frequencies for extended periods or frequent starts and stops. Compressors are typically designed for continuous stable operation, and frequent starts and stops increase mechanical stress, accelerating wear on mechanical parts. Extended low-speed operation exacerbates bearing wear and compromises the overall stability and lifespan of the compressor.
At low speeds, the motor’s internal lubrication system becomes less effective, especially when relying on an internal fan for cooling. Low-speed operation leads to insufficient fan speed, reducing cooling airflow and increasing motor temperature. Frequent starts and stops further increase the mechanical shock between components, stressing bearings, couplings, and other parts, accelerating wear.
To reduce the impact of VFD operation on the motor’s mechanical parts, we recommend:
- Set reasonable acceleration and deceleration times: Properly configuring the acceleration and deceleration times in the VFD settings can reduce mechanical shock during starts and stops, minimizing stress.
- Avoid frequent starts and stops: Optimize the system design to reduce the frequency of starts and stops, ensuring the motor operates in stable conditions.
- Install forced lubrication systems: For motors operating at low speeds for extended periods, a forced lubrication system can ensure proper lubrication, even under low-speed conditions.
Consequences of Incorrect VFD Parameter Settings
The settings of the VFD have a significant impact on the motor’s performance. If the VFD parameters are not adjusted according to the motor’s specific characteristics, it may cause instability, overloads, or faults. Common improper settings include excessively high carrier frequencies, inadequate current limits, and too-short acceleration/deceleration times.
Excessive carrier frequency increases motor losses and exacerbates insulation system damage. Setting current limits too low may prevent the motor from delivering sufficient torque, affecting compressor performance. Setting acceleration and deceleration times too short can result in excessive shock to the motor during starts and stops. Properly configuring the VFD parameters to match the motor and load characteristics is essential for a successful retrofit.
Proper VFD Retrofit Recommendations
To ensure a proper VFD retrofit and minimize motor damage, we suggest the following:
- Use VFD-compatible motors: Select motors specifically designed for variable frequency control, optimized for harmonic currents, cooling, and insulation.
- Install output filters: Use appropriate filters at the VFD’s output to reduce harmonic currents, minimizing damage to the motor bearings and insulation.
- Regular maintenance and monitoring: After the retrofit, regularly monitor the motor’s operational parameters, such as temperature, vibration, and current waveforms, to detect potential issues and perform necessary maintenance.
- Optimize control logic: In the compressor control system, optimize logic to reduce frequent starts and stops and extended low-speed operation, ensuring the motor operates under optimal conditions.
Impact of Harmonics on VFD Air Compressors
Harmonics from the VFD are a significant issue in VFD air compressor applications. Harmonics can affect various equipment, including transformers, motors, capacitor banks, switchgear, and protective devices. For example, current harmonics increase copper losses in transformers, while voltage harmonics increase iron losses, raising temperatures and reducing insulation capacity. Harmonics also induce additional heating in motors, affecting their insulation properties. Harmonic issues can destabilize equipment and lead to system resonance or faults, so we recommend considering harmonic mitigation, such as installing reactors or filtering devices, to reduce their impact on the equipment.
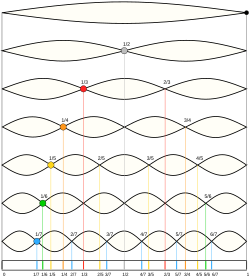
(Harmonics)
Frequently Asked Questions
What industrial applications are VFD air compressors suitable for?
VFD air compressors are ideal for various industries, including manufacturing, automotive, textiles, and food processing. Their ability to adjust output power according to demand ensures high energy efficiency.
How do I choose the right VFD and motor combination?
It is crucial to select motors designed for VFD use and ensure that the VFD’s parameters match the motor’s characteristics. Consult with technical experts if needed.
Why should I install filters?
Filters reduce the impact of harmonics on the motor and electrical system, preventing insulation damage and bearing current, ensuring long-term stable operation.
Conclusion
Improperly retrofitting a VFD onto a compressor can lead to significant motor damage. Proper VFD retrofitting not only improves energy efficiency but also ensures stable and reliable operation, preventing unnecessary damage and maintenance costs. This not only achieves energy savings but also extends the compressor’s lifespan, providing greater economic and social benefits to the business.
If you would like a customized gas solution or want to learn more, please visit the MINNUO official website.