When designing medical oxygen systems, many purchasers often focus solely on the oxygen generator itself, neglecting the compressor—the unsung hero behind the scenes. In reality, the compressor is not merely a supporting component that supplies gas to the system; it directly impacts the stability, operational efficiency, and maintenance costs of the entire oxygen system.
A suitable compressor can optimize gas source quality, enhance molecular sieve efficiency, and reduce overall energy consumption and equipment failure rates. Conversely, improper selection may lead to frequent shutdowns, oxygen purity failing to meet standards, or even accelerated molecular sieve aging, severely impacting the continuity and safety of medical oxygen supply.
This article will focus on the role of compressors in PSA and VPSA oxygen systems, helping you clarify key issues such as equipment types, selection criteria, and energy consumption pitfalls, and avoid common misconceptions that focus solely on “supply pressure” and “rated power.” Continue reading to gain a comprehensive understanding of how to achieve long-term energy efficiency, safety, and high-performance operation of medical oxygen systems through compressor configuration.
1.PSA vs VPSA Oxygen Systems: Where Compressors Fit In
When choosing a gas compressor for oxygen generation, it’s essential to understand how it integrates into the overall system—especially within PSA (Pressure Swing Adsorption) and VPSA (Vacuum Pressure Swing Adsorption) technologies.
Quick Comparison: PSA vs VPSA Core Logic
PSA Systems operate under positive pressure. They use compressed air to drive atmospheric air through molecular sieves for oxygen separation.
VPSA Systems operate under vacuum pressure, utilizing a blower and vacuum pump to draw air and then desorb nitrogen with minimal energy.
Understanding this difference is critical when selecting a compressor. The pressure level, duty cycle, and load behavior of your compressor must match the system’s working principle.
What Role Do Compressors Play?
In PSA systems: The air compressor initiates the entire separation process. It must deliver a steady, oil-free stream of air at the correct pressure (often 6–10 bar) to feed the adsorption columns.
In VPSA systems: Although the main pressure component is vacuum-based, compressors may still be needed for oxygen backflushing, storage compression, or hybrid systems.
Without the right compressor, oxygen purity and flow stability can fluctuate, leading to inefficiencies or even plant shutdowns.
What Buyers Should Focus On: 3 Key Compressor Indicators
From the buyer’s perspective, evaluating a compressor goes beyond brand names. Here are three performance criteria that directly impact oxygen plant efficiency:
1. Flow Rate Stability (Nm³/h)
Your compressor should maintain a consistent volumetric output, even under fluctuating environmental conditions. In PSA, unstable airflow leads to incomplete adsorption. In VPSA, it can disrupt timing with vacuum desorption.
✅ Solution: Choose compressors with intelligent control systems (like VSD or PID feedback) that auto-adjust flow based on downstream pressure needs.
2. Discharge Pressure (Bar)
For PSA, the pressure should precisely match the molecular sieve requirements (usually 7–10 bar). Over-pressurizing wastes energy and under-pressurizing affects oxygen purity.
✅ Tip: Look for energy-optimized compressor systems with integrated aftercoolers and pressure regulators.
3. Load Profile and Duty Cycle
In oxygen production, compressors often work 24/7. Frequent startups or wide load variations will reduce compressor life.
✅ Recommendation: Ask your supplier whether the compressor is rated for continuous duty and designed for oxygen-compatible service—especially if paired with sensitive molecular sieves.
Pro Tip: Don’t Treat PSA and VPSA as Compressor Twins
Many buyers assume PSA and VPSA use interchangeable compressors. In reality, VPSA often needs vacuum-tolerant auxiliary blowers and may not benefit from high-pressure air at all. Misjudging this can double your operational costs.
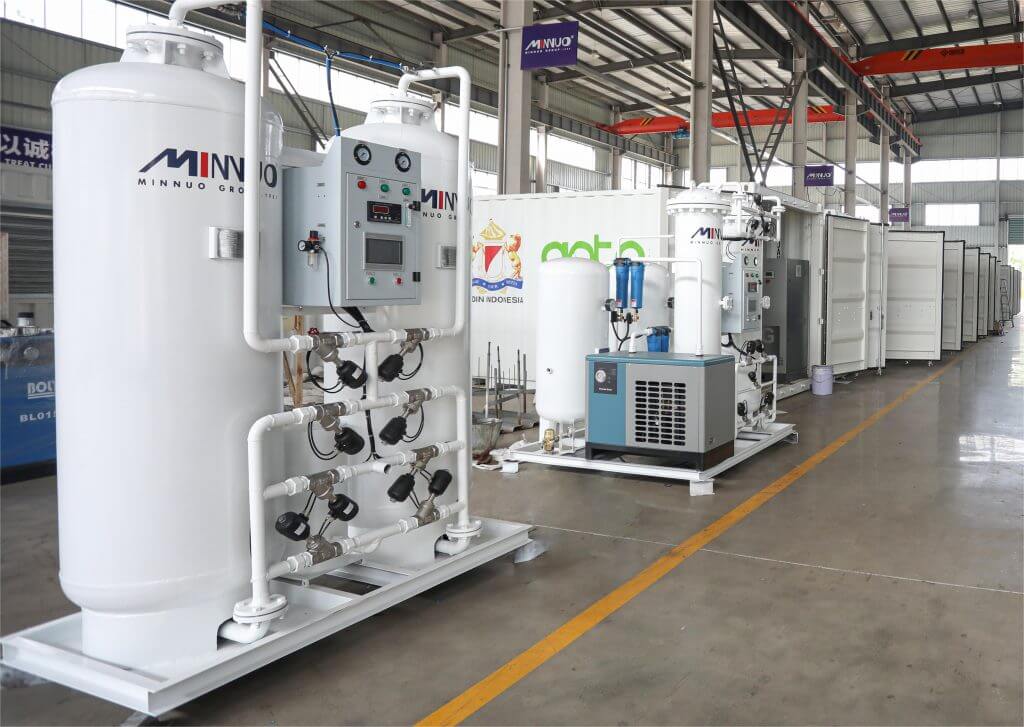
2.Buyer’s Checklist: 5 Questions to Ask Before Choosing a Compressor
Selecting the appropriate fan not only affects the operational stability of the oxygen system but also impacts long-term operational cost control and scalability. The following five questions are critical considerations that every buyer should carefully evaluate before making a decision:
2.1 Do you know how much airflow (in cubic meters) is required to meet your target oxygen output?
Under different operating conditions, the required compressed air flow rate can vary significantly. Whether using PSA or VPSA technology, compressor selection should be closely aligned with oxygen production targets rather than providing generic specifications. Customers should clearly specify:
The required air intake volume (Nm³/h);
Actual operating duration (hours per day);
Whether there are peak demand and standby requirements.
✅Solution Tip: MINNUO offers gas production configuration matching calculation services, supporting multi-scenario simulations.
2.2 How to determine if your operating conditions require an oil-free compressor?
Some applications (e.g., medical, electronic, food) have extremely high requirements for gas purity and require oil-free purifiers. Evaluation criteria include:
Whether the final use of oxygen involves human contact or high-purity processes;
Whether an internal filtration system can partially replace cleanliness requirements;
Whether national/regional industry standards require oil-free (e.g., ISO 8573-1 Class 0).
✅Solution Tip: MINNUO offers multiple solution options, including oil-free screw compressors, moisture-lubricated compressors, and dry oil-free compressors.
2.3 Do the working environment and temperature affect server efficiency?
Environmental magnetic fields and temperature directly affect the air intake density and suction efficiency of the heat sink. For example:
In high-altitude environments (>1,500m), servers require special design for air intake compensation;
In high-temperature regions (>40°C), attention must be paid to heat dissipation and lubrication system configurations.
✅Solution Tip: MINNUO offers territory/temperature control parameter correction selection schemes and has experience in deploying systems in extreme environments.
2.4 How long is the continuous runtime? Is it necessary to rotate multiple units?
Equipment does not guarantee 100% continuous operation; reasonable rotation + optimal backup are key to equipment lifespan:
Does daily runtime exceed 8 hours?
Is there a 365-day period with no demand?
Are backup routers or bypass air sources available?
✅Solution tip: MINNUO can configure intelligent solutions such as report parallelization, automatic switching, and automatic alarms.
2.5 Are there future expansion plans? Can the system support expansion?
Microprocessor selection should include: If future expansion to a larger system is required, does the current microprocessor support:
Flow rate (approximately 20%);
Control logic for a multi-tower system;
Does the electrical control panel have secondary expansion wiring terminals?
✅Solution tip: MINNUO offers a “custom design” solution supporting expansion, followed by equipment upgrades and pipeline system upgrades.
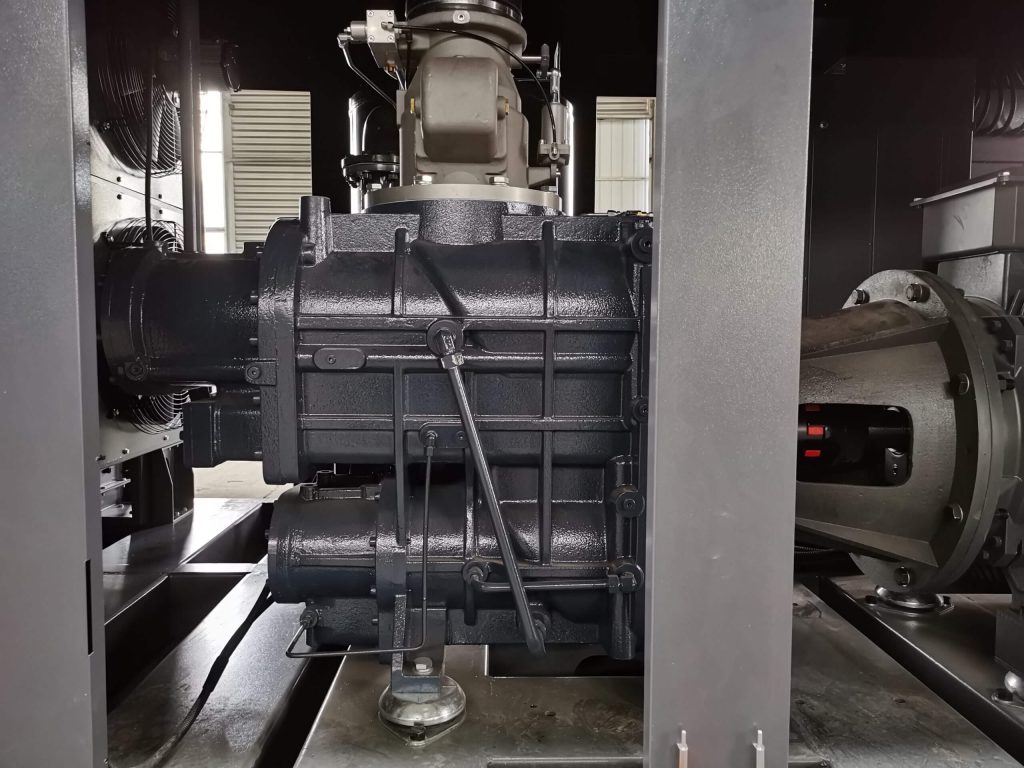
3. Common Mistakes in Air Compressor Selection and How to Avoid Them
When selecting an air compressor, some seemingly minor details can often be the key factors determining the stability of the system. The following are common misconceptions and solutions to help purchasers avoid costly hidden costs early on.
Ignoring Inlet Air Filtration and Post-Treatment Systems
Many users focus solely on the compressor’s power and price, neglecting the importance of inlet air quality and post-treatment. Without efficient filters and drying systems, compressed air may contain high levels of oil and moisture, damaging downstream equipment—a critical issue in medical and laboratory settings.
Solution: When selecting a compressor, it is essential to include pre-filters, dryers, and precision filtration components to ensure clean, dry output air and achieve system-level reliability.
Mismatch between municipal voltage and compressor motor, resulting in inability to start or frequent tripping
In some regions (such as the Middle East or Africa), voltage instability or frequency deviations may occur. If equipment is selected without considering local power parameters, it can easily lead to issues such as inability to start, frequent alarms, or motor burnout, ultimately causing project delays.
Solution Recommendations: Clearly define the on-site voltage and frequency (e.g., 220V/380V, 50Hz/60Hz). If necessary, opt for a wide-voltage-compatible compressor to ensure plug-and-play functionality.
Ignoring long-term operational noise and vibration risks
Hospitals, food factories, and research laboratories have strict noise control requirements. If the compressor is excessively noisy or vibrates severely, it not only affects operational comfort but may also cause adjacent instruments to malfunction or even lead to complaints.
Solution recommendation: Choose equipment with a low-noise design, prioritizing models with soundproof enclosures; also ensure the equipment has rubber vibration-damping bases or vibration-isolation structures to ensure stable operation.
Failure to adequately assess actual usage and lack of system architecture integrity
Common misconceptions include relying on a single compressor to handle all loads without considering backup or multi-module parallel configurations; or failing to reserve expansion interfaces, leading to frequent air supply interruptions during use and severely impacting efficiency.
Solution recommendation: When purchasing, do not just buy a single piece of equipment, but design a “compressed air solution.” It is recommended to choose a complete system that is modularly expandable and equipped with remote monitoring and backup protection.
✅ Systemized solution:
Select a compressed air system with complete supporting facilities, optimized structure, stable and quiet operation, and support for remote control and expansion. Especially for users in hospitals, laboratories, and high-end manufacturing industries, it is recommended to choose medical-grade dedicated air systems or customized intelligent compressed air stations.
4. Case Spotlight: How Southeast Asia Clinics Solved High-Temperature Operation Challenges
Country & Background
A large clinic group located in Thailand’s southern region, known for its year-round tropical climate, encountered operational instability in their oxygen generation system due to high ambient temperatures reaching 40°C.
Problem Identified
The PSA oxygen generation system frequently triggered overheat alarms during the daytime peak, causing unexpected shutdowns and interruptions in oxygen supply for critical wards.
Targeted Solution
To address the overheating issue, the clinic introduced a mid-pressure compressor with low power consumption and specialized thermal design. The compressor was selected for its ability to maintain optimal output even under extreme ambient temperatures.
Key technical improvements included:
Enhanced radiator fins with large surface area for improved heat dissipation
Integration of a temperature-controlled ventilation system
Motor insulation class upgraded to Class F for higher thermal tolerance
Continuous monitoring of inlet air temperature and discharge temperature
✅ Results After 12 Months of Operation
After system commissioning and one year of continuous use, the following results were achieved:
Oxygen purity remained consistently above 92%, ensuring patient safety
Noise level reduced by approximately 25%, improving comfort in clinical environments
Energy-related operational costs decreased by 13%, through reduced compressor load and downtime
No further overheating shutdowns occurred during the peak summer months
Insight
This case highlights the importance of adapting compressor selection to local climate conditions. Standard models may fail under stress, while climate-specific solutions can significantly extend system life, stabilize oxygen delivery, and reduce lifecycle costs. In high-temperature regions like Southeast Asia, clinics should prioritize thermal efficiency and derating considerations when sourcing compressors for PSA systems.
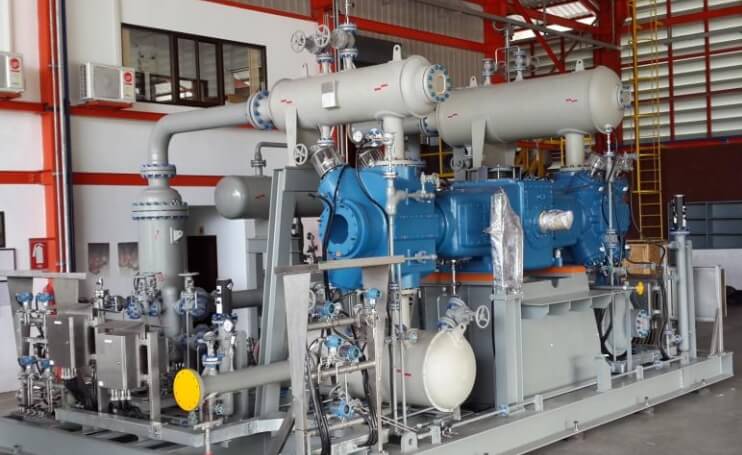
5.Smart Investment: How the Right Compressor Saves You Money Long-Term
Upfront Cost ≠ Expensive System
Choosing a high-quality compressor may seem like a bigger investment at first glance—but in practice, it’s the smarter choice for facilities aiming for long-term cost control and operational stability.
Compared with low-cost alternatives, a reliable system brings:
Lower maintenance costs
Quality components and precise engineering reduce the frequency and cost of repairs. For example, compressors with wear-resistant rotors and extended-life bearings can cut annual maintenance visits in half.
Lower energy consumption
High-efficiency motor designs, inverter control systems, and intelligent load management help reduce electricity bills by 10–25%, especially in oxygen production systems that run 24/7.
Longer service life
Industrial-grade machines typically have 1.5–2× the lifespan of budget compressors, saving replacement costs and avoiding the hassle of mid-life failure. This is particularly critical for medical and industrial oxygen systems that demand reliability.
A Case for TCO (Total Cost of Ownership)
Too often, customers are lured by low purchase prices, only to face hidden costs such as:
Frequent motor or valve failure
Excessive oil carryover leading to oxygen contamination risks
Lack of replacement parts and extended downtimes
Higher noise and heat output, compromising working conditions
By evaluating Total Cost of Ownership rather than just initial cost, you avoid these pitfalls and gain:
Predictable maintenance budgeting
More uptime, fewer breakdowns
Long-term performance stability
The Cost of Chasing “Cheap”
Instead of pursuing “cheap air compressors,” it is better to choose the right one once and enjoy long-term peace of mind.
Investing in the right machine the first time avoids recurring headaches, unexpected repair bills, and operational downtime. This is especially relevant for oxygen concentrator systems used in hospitals or remote industrial sites, where every failure may directly impact safety or production.
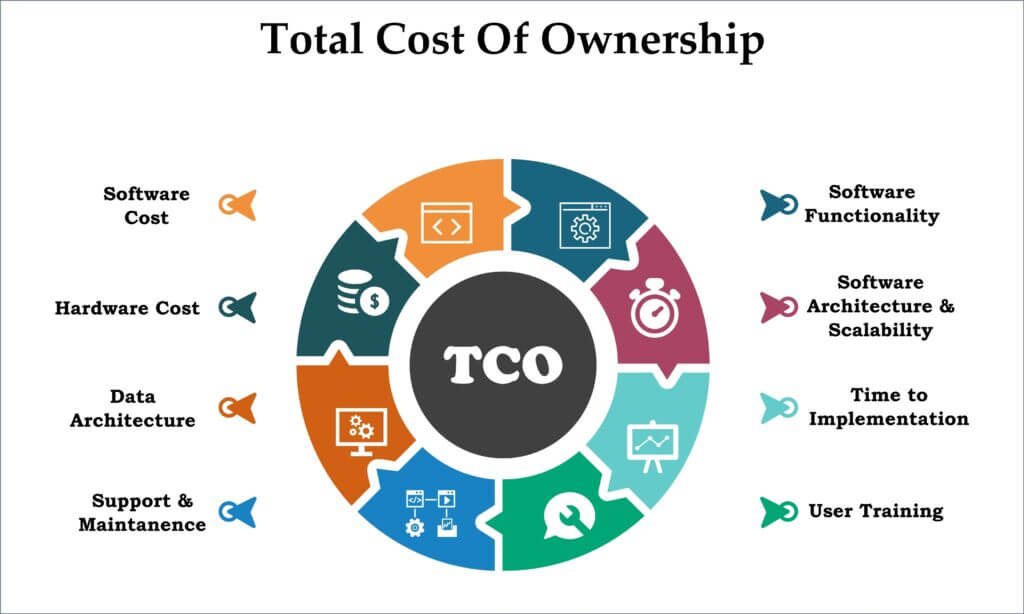
Conclusion
Compressors are not merely front-end air treatment equipment; they play a critical role in medical oxygen systems by ensuring a stable gas supply, maintaining continuous oxygen delivery, and safeguarding system safety. From efficiency to energy consumption, from service life to compatibility, compressors determine the long-term performance and return on investment of your project.
Therefore, when selecting a compressor, one should not merely focus on label specifications but instead consider the entire oxygen system comprehensively. What you need is a compressor solution tailored to your oxygen production process, not just a “cheap piece of equipment.”
If you are planning to build a PSA or VPSA oxygen production system, MINNUO can provide you with a customized integrated air compression solution, covering equipment selection, technical support, and after-sales service, helping you avoid the trap of low-cost options and achieve true long-term savings.